Model and Die Materials
Objectives
After reading this chapter, the student should be able to:
1. Define the terms study model, cast, and die as they relate to model and die materials.
< ?mpslid E1?>< ?mpslid S2?>
< ?mpslid E2?>< ?mpslid S3?>
< ?mpslid E3?>< ?mpslid S4?>
< ?mpslid E4?>< ?mpslid S5?>
5. Describe the setting reaction of gypsum materials and the effect of excess water on the set mass.
< ?mpslid E5?>< ?mpslid S6?>
6. Name accelerators and retarders that affect the gypsum setting reaction.
< ?mpslid E6?>< ?mpslid S7?>
< ?mpslid E7?>< ?mpslid S8?>
< ?mpslid E8?>< ?mpslid S9?>
9. Describe the factors that influence the ability of gypsum to reproduce detail in an impression.
< ?mpslid E9?>< ?mpslid S10?>
10. Explain the concept of wetting and why it is important to gypsum materials.
< ?mpslid E10?>< ?mpslid S11?>
< ?mpslid E11?>< ?mpslid S12?>
< ?mpslid E12?>< ?mpslid S13?>
13. Describe the various methods of spatulation of gypsum materials.
< ?mpslid E13?>< ?mpslid S14?>
< ?mpslid E14?>< ?mpslid S15?>
15. Describe the general setting reaction of epoxy model materials.
< ?mpslid E15?>< ?mpslid S16?>
16. Describe the general manipulation properties of epoxy model materials.
< ?mpslid E16?>
Key Terms
Abrasion resistance
Cast
Die
Dihydrate
Epoxy
Gypsum
Hemihydrate
Hygroscopic
Hygroscopic expansion
Model
Model plaster
Porosity
Setting time
Spatulation
Stereolithography
Water–powder ratio
Wetting
In dentistry, replicas of the hard and soft tissues are used for diagnosis and treatment of oral disease. These replicas are called study models, casts, or dies. Each of these replicas has a specific purpose in dental practice. Study models are used to observe the patient’s oral structures. For example, orthodontists use study models to evaluate the crowding of the teeth or progress in correction of that crowding. A cast is a working model. Casts of teeth are used to make orthodontic retainers, and casts of the remaining ridges in the edentulous patient are used to make dentures. Dies are highly accurate replicas of a single tooth and generally are used to make metal crowns or inlays.
Models, casts, and dies always are made from an impression of the soft and hard oral tissues. The accuracy of the model therefore depends on the accuracy of the impression, and any flaws present in the impression are reproduced in the model (see Chapter 8). However, the accuracy of a model also depends on the materials used to pour the impression. The ability of the material to flow into details of the impression and its expansion or contraction during setting are two properties that influence the accuracy of the model. The relationship between the impression and model can be confusing (see Figures 8-1 and 9-1) because the impression is an inverse negative of the mouth. The right side of the impression becomes the left side of the model, and low points in the impression become high points in the model. Models and dies can also be prepared from digital impressions.
Desirable Qualities and Types of Products
A number of qualities are required of materials to be used for making models, casts, or dies. These qualities are accuracy, dimensional stability, reproduction of fine detail, strength and resistance to abrasion, ease of adaptation to the impression, color, and safety, among others. To a large extent, the desired qualities depend on the application. For example, dentists do not require the same dimensional accuracy for a study model as for a die. Because a die is used to make a precision crown or inlay, it must be dimensionally accurate.
Of the desirable properties mentioned previously, accuracy and dimensional stability are paramount because models, casts, and dies must reproduce an intraoral structure accurately and must remain the same size, or they are of little use to the dental team. Strength and abrasion resistance are necessary for applications such as dies, in which a wax pattern of the restoration is made on the die, and the die must not wear away, even though instruments rub against it. The color of the material may be important to provide contrast when pouring impressions. The most appropriate material varies with each application; the practitioner must therefore select the material with properties that are most desirable for the application at hand.
Two common materials are used to pour impressions: gypsum materials and epoxy materials. This chapter focuses primarily on the gypsum materials because they are by far the most common. However, epoxy materials are discussed briefly. Electroplated metal dies are used rarely and are not discussed. Information about these materials is presented in the seventh edition of this textbook. Not all materials can be poured into all impression materials. The problem of model material–impression compatibility can be significant, but it is primarily a problem for the epoxy materials. As Table 9-1 shows, gypsum products can be poured into almost all impression materials used in practice today. Epoxy materials are compatible with most of the elastomeric impression materials, but they cannot be used with the alginates or agar impression materials.
TABLE 9-1
Compatibility of Die Materials with Impression Materials
< ?comst?>
MATERIAL | COMPATIBLE WITH |
Gypsum Products | Agar |
Alginate† | |
Condensation silicones | |
Addition silicones (PVS)† | |
Polysulfides | |
Polyethers† | |
Epoxy Resin Products | Condensation silicones (some require separator)∗ |
Addition silicones (PVS) (some require separator)∗† | |
Polyethers† | |
Polysulfides (with separator) |
< ?comen?>< ?comst1?>
< ?comst1?>
< ?comen1?>
< ?comst1?>< ?comen1?>∗< ?comst1?>< ?comen1?>A separator is a material that is applied to the impression material before pouring with the die material. It prevents the die material from bonding or otherwise reacting with the impression material.
< ?comst1?>< ?comen1?>†< ?comst1?>< ?comen1?>Most commonly used impression materials.
Table 9-2 shows the major advantages and disadvantages of each model material. For most applications, the gypsum materials are easy to use with excellent impression material compatibility. However, they are abraded easily during manipulation. Epoxy materials have fair compatibility with impression materials and have good abrasion resistance, but most set slowly. Thus, each type of material has advantages and disadvantages, and the proper material must be selected for each application.
TABLE 9-2
Comparison of Gypsum and Epoxy Materials
PROPERTY | GYPSUM | EPOXY |
Abrasion resistance | Poor | Good |
Ease of use | Easy | Moderately difficult |
Time required | Minimal | Several hours |
Equipment required | Minimal | Minimal |
Harmful chemicals | None | Some (allergy) |
Compatibility with impression materials | Excellent (see Table 9-1) | Limited (see Table 9-1) |
Dimensional change | Slight expansion | Slight contraction |
Accuracy | Good | Good |
Modified from Sakaguchi RL, Powers JM, editors: Craig’s Restorative Dental Materials, ed 13, St Louis, 2012, Mosby.
Gypsum Products
Of all model materials, gypsum materials are the most common. Five types of gypsum products are available in dentistry: impression plaster, model plaster, dental stone, high-strength/low-expansion dental stone (also called die stone), and high-strength/high-expansion dental stone. Model plaster is used for study models that do not require abrasion resistance. Model plaster should not be confused with orthodontic plaster, which is a mixture of model plaster and dental stone. Impression plaster is used primarily to mount casts on an articulator. It differs from model plaster in that the setting time has been shortened to 3 to 5 minutes and the dimensional change on setting reduced to 0.06%. Dental stone (also called simply stone) is stronger and more resistant to abrasion than plaster and is used for casts that need abrasion resistance. Casts made of dental stone are durable enough to be used for forming mouth protectors. Dies require the highest abrasion resistance and strength and usually are made of high-strength dental stone.
Chemical and Physical Nature
Physical Form
The physical forms of model plaster, dental stone, and high-strength dental stone are different, but they are made of the same chemical: calcium sulfate hemihydrate (CaSO4 ·½ H2O). All of these forms are manufactured from the mineral gypsum, which is calcium sulfate dihydrate (CaSO4 · 2H2O). The only difference between the model materials and gypsum is the amount of water in the crystal. During the manufacture of model materials, water is driven out of the dihydrate gypsum to form the hemihydrate. The differences between plaster, stone, and high-strength stone are the physical forms of the hemihydrate formed when the water is driven out, not its chemical makeup.
Plaster is produced by heating the gypsum (dihydrate) in an open kettle at about 115 °C (Figure 9-2). The hemihydrate produced is a porous powder called β-calcium sulfate hemihydrate. This hemihydrate has relatively small, irregular crystals. Dental stone is produced by heating the gypsum under pressure in the presence of steam at 125 °C. The hemihydrate produced under these conditions is called α-calcium sulfate hemihydrate (see Figure 9-2). This hydrate has larger, denser, more regular crystals than the β-calcium sulfate hemihydrate of plaster. Boiling gypsum in a 30% solution of calcium chloride produces high-strength dental stone. The hemihydrate crystals produced in this case are the least porous, most regular, and largest of all of the hemihydrates.
Chemical Reaction and Excess Water
All forms of calcium sulfate hemihydrate react with water to form the dihydrate (gypsum) as shown in the following reaction:
< ?xml:namespace prefix = "mml" ns = "http://www.w3.org/1998/Math/MathML" />

Thus, model plaster, dental stone, and high-strength stone revert to the gypsum dihydrate when combined with water. It is this setting reaction that occurs when the model material sets into a hard mass. This reaction gives off heat and is therefore exothermic. Theoretically, if 100 g of any hemihydrate were combined with 19 mL of water, all of the hemihydrate would be converted to the dihydrate; that is, sufficient water would exist for all of the hemihydrate to react. However, in practice, this amount of water does not produce a mass that can be manipulated and poured into an impression. If mixed, this mass would be dry and crumbly. Therefore, in practice, excess water must be added when mixing to produce a workable mass that can be poured into an impression.
Because of their different crystal sizes and porosity, the hemihydrates of plaster, stone, and high-strength stone require different amounts of excess water to produce a workable mass. High-strength stone, with its large, dense crystals, requires the least excess water. Dental stone requires somewhat more water, and plaster requires the most excess water. In general, the larger and more dense the crystal size of the hemihydrate, the less excess water is required to get a workable mass. With any of these materials, the excess water does not react but simply is trapped in the mass when it sets. Thus, plaster has the most excess water in the mass, and high-strength stone has the least (Table 9-3). The presence of excess water has significant consequences on the physical properties of gypsum, as discussed later. After the material sets completely, any excess water eventually evaporates and leaves voids in the mass. These voids reduce the overall density of the material. Therefore, set plaster has the lowest density (most porosity) because it had the most excess water and the most voids in the mass. Set high-strength dental stone has the highest density.
TABLE 9-3
Amount of Water Needed to Mix Gypsum Materials∗
GYPSUM | MIXING WATER (mL/100 g OF POWDER) | EXCESS WATER† (mL/100 g OF POWDER) |
Model plaster | 37–50 | 18–31 |
Dental stone | 28–32 | 9–13 |
High-strength dental stone (Types IV, V) | 19–24 | 0–5 |
Accelerators and Retarders
The rate of the gypsum reaction can be altered by chemicals that the manufacturer adds to the hemihydrate powder. Accelerators are chemicals that increase the rate of setting, and retarders have the opposite effect. Some accelerators and retarders work by changing the solubility of the hemihydrate and dihydrate forms of the calcium sulfate. Accelerators make the dihydrate less soluble than the hemihydrate, so the reaction is moved toward the dihydrate because the dihydrate assumes its solid form rapidly. Potassium sulfate is an effective accelerator acting by this mechanism. A 2% water solution of potassium sulfate substituted for pure water reduces the setting time of model plaster from 10 minutes to 4 minutes. Retarders make the hemihydrate only slightly less soluble than the dihydrate. Therefore, the reaction proceeds more slowly toward the dihydrate. Borax, a chemical with the formula Na2B4O7 · 10H2O, will extend the setting time of some gypsum products to several hours if added to the powder at a concentration of 2%.
Other chemicals act as accelerators or retarders by different mechanisms. Set gypsum particles (dihydrate) accelerate the reaction by acting as nucleation sites on which new dihydrate particles can form. These particles also are called terra alba, and concentrations of 0.5% to 1.0% added to the water are effective. A practical way of using terra alba is to use the slurry water (water containing particles of dihydrate) from the model trimmer to mix the gypsum. However, the user should be warned that the setting time using this method is extremely short. Colloidal particles, such as blood, saliva, agar, or unset alginate, retard the setting reaction of gypsum. Colloids are fine particles of protein or other chemicals suspended in a liquid. These colloids bind to the hemihydrate and interfere with the addition of water to form the dihydrate. The result is a soft, easily abraded surface on the gypsum cast. To avoid this problem, impressions should be rinsed thoroughly in cold water to remove traces of blood and saliva before the impression is poured.
Water–Powder Ratio
The water–powder ratio for a material is defined as the amount of water in milliliters added to 100 g of powder. By convention, the water–powder ratio generally is expressed as a fraction, such as 45⁄100 or 0.45. This fraction means that 45 mL of water is added to 100 g of powder. For a given type of stone, the higher the water–powder ratio is, the more soupy the consistency of the mix. Table 9-3 shows the water–powder ratios for model plaster, dental stone, and high-strength dental stone. Some variation occurs, depending on the manufacturer; therefore, ranges are given in the table. However, model plaster generally has the highest water–powder ratio, and high-strength stone will have the lowest. Because all model materials require about 19 mL of water for every 100 g of powder for the conversion of the hemihydrate to the dihydrate, any water over 19 mL is excess. This fact also is demonstrated in Table 9-3. Therefore, model plaster has the most excess water (18 to 31 mL). The excess water required for mixing is a function of the particle size of the hemihydrate as described previously.
The water–powder ratio influences the physical properties of set gypsum materials. The use of excessive water lengthens the setting time and reduces the strength (Table 9-4). The reduced strength is a result of the excess water used in the mix that leaves voids on evaporation. Increased water also reduces the setting expansion of set gypsum materials. Although it is tempting to increase setting time by using more water, it is not advisable because the strength of the material will be reduced and the expansion of the material will not be appropriate. Therefore, following the recommendations of the manufacturer is important in a decision regarding the water–powder ratio. Manufacturers/>
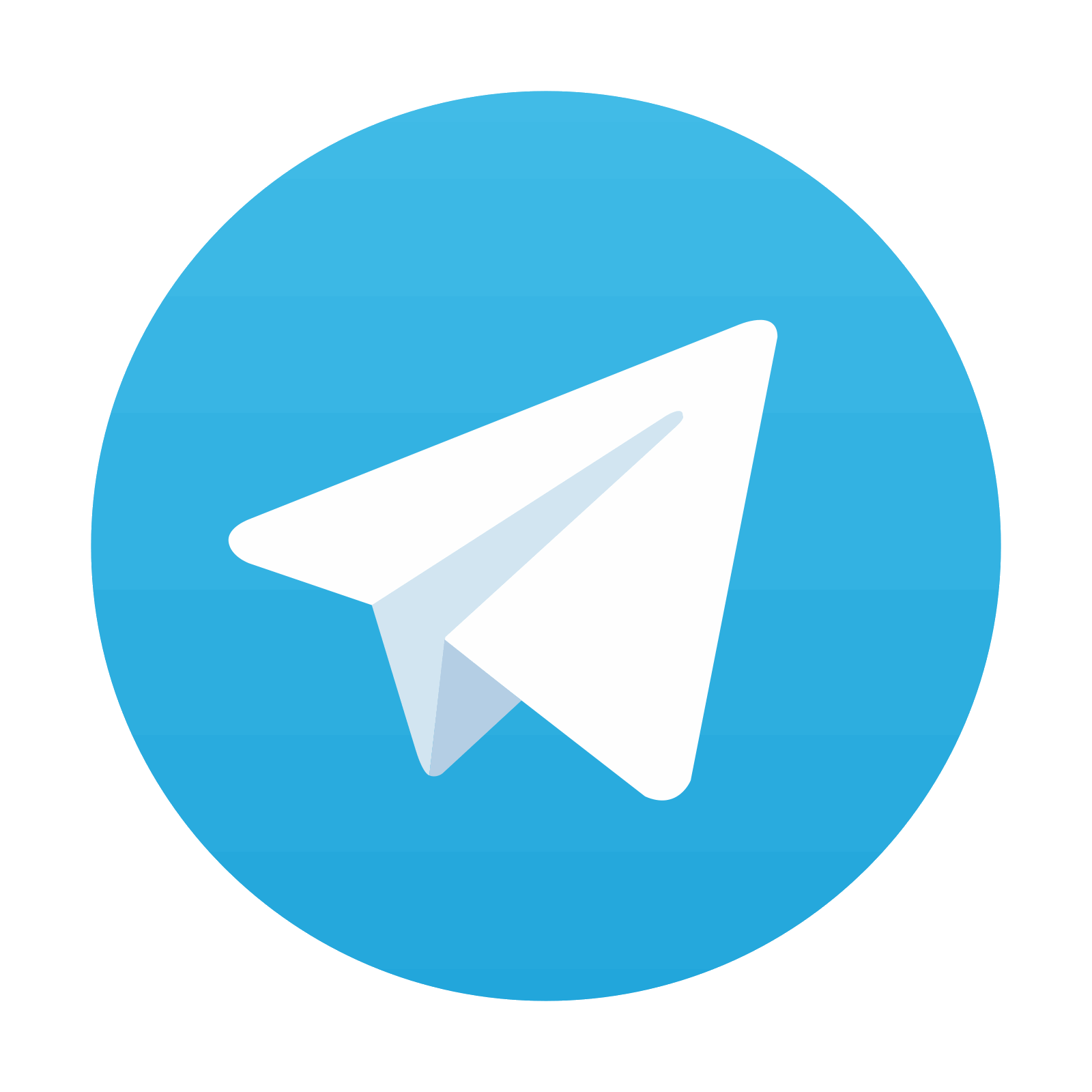
Stay updated, free dental videos. Join our Telegram channel

VIDEdental - Online dental courses
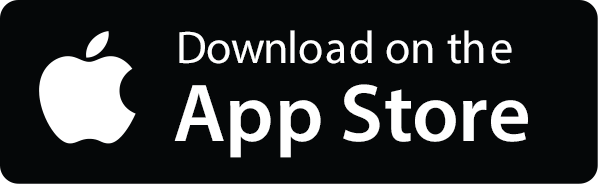
