All-ceramic restorations
High-strength core ceramics
Introduction
The work by Land in the early 1900s and others since then showed that one of the problems with the all-ceramic anterior crown was that the porcelain would fracture from the fit surface outwards. Some improvements in the strength of porcelain were achieved by the introduction of vacuum firing furnaces, which helps to minimize porosity, and raised the flexural strength of the porcelain from 20–30 MPa to approximately 50–60 MPa. However, this proved not to be adequate to produce reliable ceramic restorations and thus the search was on for a core material that would provide the necessary strength and toughness to prevent fractures arising from cracks propagating from the fit surface of the crown.
Since ceramics tend to fail at the same critical strain of ~0.1%, one means of achieving an increase in fracture strength is to increase the elastic modulus of the material. If, at the same time, the propagation of cracks is made more difficult such that a greater strain can be supported, a higher strength ceramic will result (Figure 3.6.1). The flexural strengths of a number of ceramics are shown in Table 3.6.1. As the tensile strength is a difficult property to measure (giving rise to a wide degree of scatter in the data), it is common practice to determine the flexural strength. Although the silicon nitrides and carbides are attractive from the viewpoint of strength, they are not suitable because of the difficulties associated with the manufacture of individual crowns: the colour differences and the mismatch in the coefficient of thermal expansion.
Table 3.6.1
Typical strength values for high-strength ceramics
Type of ceramic | Flexural strength (MPa) |
Hot-pressed silicon nitride | 800–900 |
Hot-pressed silicon carbide | 400–750 |
Partially stabilized zirconia | 640 |
Alumina 98% pure | 420–520 |
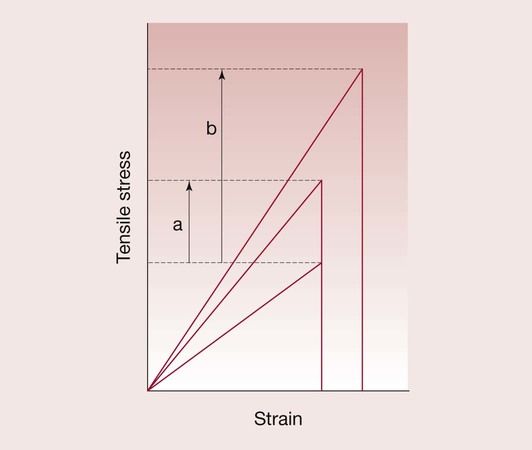
In the mid-1960s, McLean and Hughes developed a core material based on the reinforcement of a feldspathic glass with alumina, commonly referred to as the alumina-reinforced porcelain jacket crown (PJC). Since then, other systems have been developed. In the 1980s, the glass-infiltrated, high-strength ceramic cores were developed (In-Ceram, Vita) and, in the 1990s, the all-alumina core made its first appearance (Techceram, Techceram Ltd: Procera AllCeram, Nobel Biocare). Recent work has seen the introduction of ytrria-stabilized zirconia for the fabrication of cores for crown and bridge frameworks.
Alumina-reinforced porcelain jacket crowns
The alumina-reinforced feldspathic core was introduced in the early 1960s by Hughes and McLean. The material consists of a feldspathic glass containing 40–50% alumina (Figure 3.6.2). The alumina particles are far stronger than the glass, and are more effective at preventing crack propagation than quartz, acting as crack stoppers (Figure 3.6.3). Whereas the flexural strength of feldspathic porcelain is, at best, some 60 MPa, this is raised to 120–150 MPa for the aluminous core porcelains.
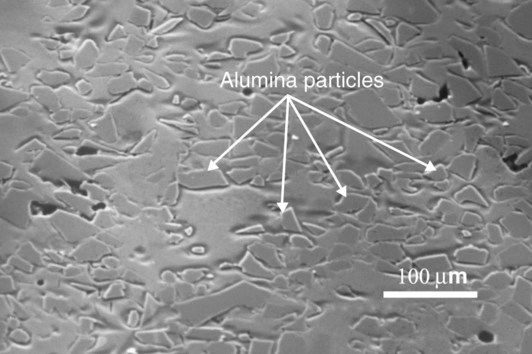
In the construction of a crown, the opaque shade shown in Figure 3.4.3 is made with an aluminous core porcelain. It is still necessary to use the weaker dentine and enamel shades of the feldspathic porcelains because it is not possible to produce aluminous porcelains with the required translucency; the alumina causes the porcelain to appear dull and opaque.
The main application of the alumina-reinforced PJC is for the restoration of anterior teeth. Although the improvement in strength is considerable, it is still insufficient to allow its use posteriorly and the construction of even a three-unit bridge is out of the question.
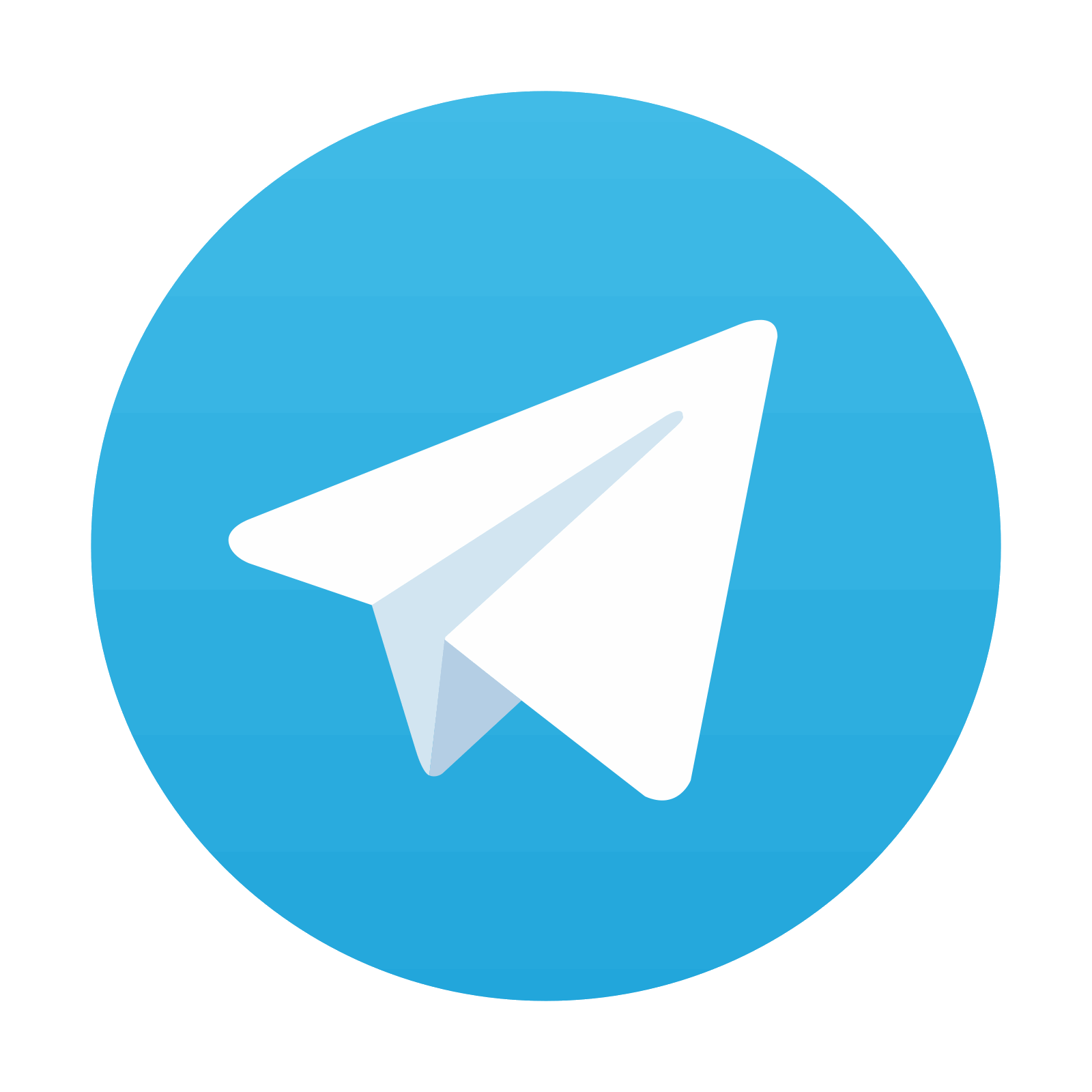
Stay updated, free dental videos. Join our Telegram channel

VIDEdental - Online dental courses
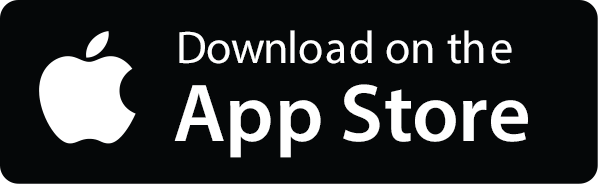
