Materials and Processes for Cutting, Grinding, Finishing, and Polishing
Principles of Cutting, Grinding, Finishing, and Polishing
Subtle differences distinguish the cutting, grinding, and polishing processes. A cutting operation usually involves the use of a bladed instrument or any other instrument in a bladelike fashion. Substrates may be divided into large separate segments, or they may sustain deep notches and grooves by the cutting operation. High-speed tungsten carbide burs have numerous regularly arranged blades that remove small pieces or segments of the substrate as the bur rotates. As shown in Figure 11-1, A, the unidirectional cutting pattern reflects the action of the regularly arranged blades on a tungsten carbide bur. The pattern produced by a diamond bur is shown in Figure 11-1, B. The surface of a coarse diamond bur is shown in Figure 11-1, C. When 30-fluted finishing burs have been used on a surface, the regular pattern of the cutting blades is discernible only if the surface is magnified for inspection. On the other hand, a separating wheel is an example of an instrument that can be used in a bladelike fashion. A separating wheel does not contain individual blades, but its thin blade design allows it to be used in a rotating fashion to grind through cast metal sprues and die stone materials.
A grinding operation removes small particles of a substrate through the action of bonded or coated abrasive instruments. Grinding instruments contain many randomly arranged abrasive particles. Each particle may contain several sharp points that run along the substrate surface and remove particles of material. For example, a diamond-coated rotary instrument may contain many sharp diamond particles (see Figure 11-1, C) that pass over a tooth during each revolution of the instrument. Because these particles are randomly arranged, many unidirectional scratches are produced within the material surface, as illustrated in Figure 11-1, B, which shows a tooth surface ground by a diamond bur. Cutting and grinding are both considered predominantly unidirectional in their action. This means that a cut or ground surface exhibits cuts and scratches oriented in one predominant direction.
Different types of burs have unique effects on surfaces. In general, a carbide bur with more blades will produce a smoother surface than a carbide bur containing fewer blades. For example, a 16-fluted carbide bur produces a smoother finish than an 8-fluted carbide bur, but the latter removes material more rapidly. Similarly, the coarsest diamond bur removes material more quickly but leaves a rougher surface. (See Figure 11-2 for scanning electron microscopy [SEM] images of carbide and diamond burs.)
Bulk-Reduction Process
Bulk reduction can be achieved through the use of instruments such as diamond burs, tungsten carbide burs, steel burs, abrasive wheels, and separating discs. Whereas diamond burs and abrasive wheels provide this action by grinding, steel and carbide burs remove materials through a cutting action of the hard blades. Abrasive-coated discs are popular instruments for bulk reduction of resin-based composite restorations. For bulk reduction of composites, the clinician should choose 8- to 12-fluted carbide burs or abrasives with a particle size of 100 µm or larger and sufficient hardness (9 to 10 Mohs hardness). SEM images of the surface finishes produced on a resin-based composite by a coarse diamond, a 12-fluted carbide bur, a 16-fluted carbide bur, and two types of finishing or polishing systems are shown in Figure 11-3. For bulk reduction of ceramics and metals, the user should follow the manufacturers’ instructions to minimize the time required. In some cases, instruments used in the dental lab may be different from those used chairside, so the abrasiveness of an unknown instrument should be tested on a scrap piece of the material that will be used for a specific task.
Polishing
Polishing is considered multidirectional, which means that the final surface scratches are oriented in many directions. Some examples of ground and polished surfaces are shown in Figure 11-3. Note that the differences in surface appearance are subtle because of the transitional nature of the grinding and polishing processes. If there were larger differences in the size of particles removed, the surface change would be more easily detected.
Abrasion and Erosion
Abrasion
Wear is a material removal process that can occur whenever surfaces slide against each other. The process of finishing a restoration involves abrasive wear through the use of hard particles. In dentistry, the outermost particles or surface material of an abrading instrument is referred to as the abrasive. The material being finished is called the substrate. In the case of a diamond bur abrading a tooth surface, as illustrated in Figure 11-4, the diamond particles bonded to the bur represent the abrasive, and the tooth is the substrate. Also, note that the bur in the high-speed handpiece rotates in a clockwise direction as observed from the head of the handpiece.
Erosion
Erosive wear is caused by hard particles impacting a substrate surface, carried by either a stream of liquid or a stream of air, as occurs in sandblasting a surface. Figure 11-5 illustrates schematically the processes of two-body abrasion, three-body abrasion, and hard-particle erosion. Most dental laboratories have air-driven grit-blasting units that employ hard-particle erosion to remove surface material. A distinction must be made between this type of erosion and chemical erosion, which involves chemicals such as acids and alkalis instead of hard particles to remove substrate material. Chemical erosion, more commonly called acid etching in dentistry, is not used as a method of finishing dental materials. It is used primarily to prepare tooth surfaces to enhance bonding or coating.
Hardness of Abrasives
Knoop and Vickers hardness tests are based on indentation methods that quantify the hardness of materials. The tip of a Knoop diamond indenter has an elongated pyramidal shape, whereas the Vickers diamond indenter has an equilateral pyramidal design. Both tests involve the application of the indenter to a test surface under a known load (usually 100 Newtons, or 100 N). The depth of surface penetration is reported as hardness in units of force per unit area. Although a number of other factors affect a material’s abrasiveness, the farther apart a substrate and an abrasive are in hardness, the more efficient is the abrasion process. On the basis of a comparison of hardness values for several dental materials listed in Table 11-1, it is expected that silicon carbide and diamond abrasives will abrade dental porcelain more readily compared with garnet, even though the abrasive particles for all three materials have very sharp edge characteristics.
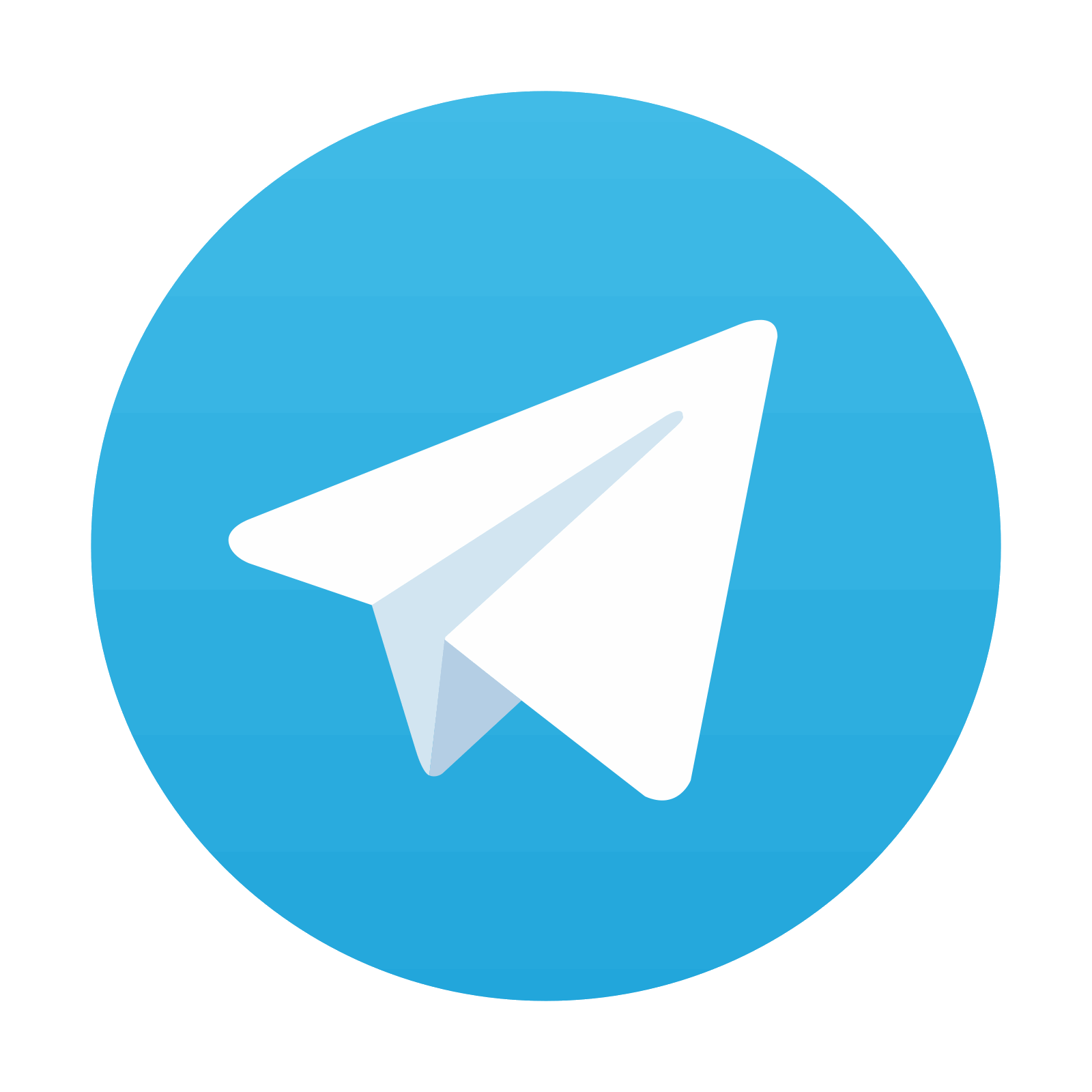
Stay updated, free dental videos. Join our Telegram channel

VIDEdental - Online dental courses
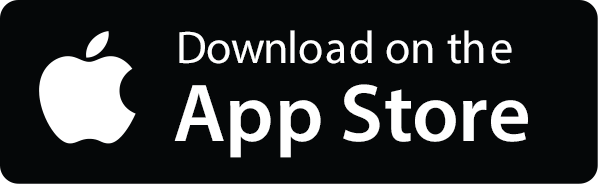
