Computer-aided design (CAD) and computer-aided manufacturing (CAM) have become an increasingly popular part of dentistry over the past 25 years. The technology, which is used in both the dental laboratory and the dental office, can be applied to inlays, onlays, veneers, crowns, fixed partial dentures, implant abutments, and even full-mouth reconstruction. This article discusses the history of CAD/CAM in dentistry and gives an overview of how it works. It also provides information on the advantages and disadvantages, describes the main products available, discusses how to incorporate the new technology into your practice, and addresses future applications.
Computer-aided design (CAD) and computer-aided manufacturing (CAM) have become an increasingly popular part of dentistry over the past 25 years. The technology, which is used in both the dental laboratory and the dental office, can be applied to inlays, onlays, veneers, crowns, fixed partial dentures, implant abutments, and even full-mouth reconstruction. CAD/CAM is also being used in orthodontics.
CAD/CAM technology was developed to solve 3 challenges. The first challenge was to ensure adequate strength of the restoration, especially for posterior teeth. The second challenge was to create restorations with a natural appearance. The third challenge was to make tooth restoration easier, faster, and more accurate. In some cases, CAD/CAM technology provides patients with same-day restorations.
Dentists and laboratories have a wide variety of ways in which they can work with the new technology. For example, dentists can take a digital impression and send it to a laboratory for fabrication of the restorations or they can do their own computer-aided design and milling in-house.
When laboratories receive a digital impression, they can create a stone model from the data and either continue with traditional fabrication or rescan the model for milling. Alternatively, the laboratory can do all of the design work directly on the computer based on the images received.
This article discusses the history of CAD/CAM in dentistry and gives an overview of how it works. It also provides information on the advantages and disadvantages, describes the main products available, discusses how to incorporate the new technology into your practice, and addresses future applications.
History of dental CAD/CAM
Computer-aided design and manufacturing were developed in the 1960s for use in the aircraft and automotive industries, and were first applied to dentistry a decade later.
Some of the most important figures in dental CAD/CAM development are Drs François Duret of France, Werner Mörmann of Switzerland, Dianne Rekow of the United States, and Matts Andersson of Sweden.
Dr Duret was the first person to develop a dental CAD/CAM device, making crowns based on an optical impression of the abutment tooth and using a numerically controlled milling machine as early as 1971. He produced the first dental CAD/CAM restoration in 1983 and demonstrated his system at the French Dental Association’s international congress in November 1985 by creating a posterior crown restoration for his wife in less than an hour. Dr Duret later developed the Sopha system.
Dr Mörmann was the developer of the first commercial CAD/CAM system. He consulted with Dr Marco Brandestini, an electrical engineer, who came up with the idea of using optics to scan the teeth. By 1985, the team had performed the first chairside inlay using a combination of their optical scanner and milling device. They called the device CEREC, an acronym for computer-assisted ceramic reconstruction.
Dr Rekow worked on a dental CAD/CAM system in the mid-1980s with colleagues at the University of Minnesota. This system was designed to acquire data using photographs and a high-resolution scanner, and to mill restorations using a 5-axis machine.
Dr Andersson developed the Procera (now known as NobelProcera, Nobel Biocare, Zurich, Switzerland) method of manufacturing high-precision dental crowns in 1983. He was also the first person to use CAD/CAM for composite veneered restorations.
Early technology permitted the creation of inlays, onlays, veneers, and crowns. More recently, CAD/CAM systems have been able to provide fixed partial dentures and implant abutments.
Another use of CAD/CAM is in orthodontics. One example of this is Invisalign (Align Technology, Inc, Santa Clara, CA, USA), a treatment that uses multiple clear, removable appliances designed and manufactured via CAD/CAM to straighten teeth.
CAD/CAM systems are becoming increasingly popular in dental offices. More than 30,000 dentists around the world own scanning and milling machines; 10,000 of these are in the United States and Canada. Worldwide, more than 15 million CEREC restorations alone have been completed.
Overview of CAD/CAM
In brief, in-office dental CAD/CAM systems consist of a handheld scanner, a cart that houses a personal computer together with a monitor, and a milling machine.
The scanner head is placed intraorally above the tooth preparation and the resulting data appear on the monitor as 2-dimensional (2-D) or 3-dimensional (3-D) images. Design work is done on the monitor and the instructions are sent to a computer-assisted processing machine for milling.
Restorations are milled from prefabricated blocks of porcelain. Options include feldspathic, leucite, or lithium disilicate materials as well as blocks of composite. After the restoration is examined and approved, it is polished and inserted using conventional bonding techniques.
Results with in-office milling machines appear to be as good as those from laboratory milling machines. A systematic review of 16 articles that comprised 1957 restorations found no significant differences in 5-year survival rates between chairside CEREC restorations (90.2% to 93.8%) and Celay laboratory restorations (82.1%).
Overview of CAD/CAM
In brief, in-office dental CAD/CAM systems consist of a handheld scanner, a cart that houses a personal computer together with a monitor, and a milling machine.
The scanner head is placed intraorally above the tooth preparation and the resulting data appear on the monitor as 2-dimensional (2-D) or 3-dimensional (3-D) images. Design work is done on the monitor and the instructions are sent to a computer-assisted processing machine for milling.
Restorations are milled from prefabricated blocks of porcelain. Options include feldspathic, leucite, or lithium disilicate materials as well as blocks of composite. After the restoration is examined and approved, it is polished and inserted using conventional bonding techniques.
Results with in-office milling machines appear to be as good as those from laboratory milling machines. A systematic review of 16 articles that comprised 1957 restorations found no significant differences in 5-year survival rates between chairside CEREC restorations (90.2% to 93.8%) and Celay laboratory restorations (82.1%).
Advantages and disadvantages of CAD/CAM
The use of CAD/CAM technology for dental restorations has numerous advantages over traditional techniques. These advantages include speed, ease of use, and quality.
Digital scans have the potential to be faster and easier than conventional impressions because casts, wax-ups, investing, casting, and firing are eliminated. According to Sirona, half-arch impressions with the most recent version of CEREC take 40 seconds and full-arch impressions take 2 minutes. CAD/CAM also makes design and fabrication faster; a full-contour crown takes just 6 minutes to mill.
Having a milling machine on site means that patients can receive their permanent restoration the same day they come in, without making a second appointment. Patients no longer need to have provisional restorations, which take time to fabricate and fit. If anesthetics are needed, they only need to be administered once.
The quality of CAD/CAM restorations is extremely high because measurements and fabrication are so precise. In a study of 117 subjects by Henkel, each subject had 2 crowns made. One crown was made based on physical impressions using standard trays and impression material and another was made based on electronic impressions. Without knowing which one was which, dentists chose the crown based on the electronic impression 68% of the time.
Perhaps this difference in the finished product should not be surprising, given the wide variation in quality of traditional impressions. Writing in a 2005 article, Christensen stated that he had seen impressions sent to laboratories in which more than 50% of the preparation margins were not discernible. Traditional impressions suffer from problems, such as bubbles and tears in the impression material, cords or other debris embedded in the impression material, and missing teeth.
CAD/CAM restorations have a natural appearance because the ceramic blocks have a translucent quality that emulates enamel, and they are available in a wide range of shades. Ceramic wears well in the mouth, even when used for posterior teeth; because it is no more abrasive than conventional and hybrid posterior composite resins, it causes minimal wear to the opposing teeth.
Finally, quality is consistent because prefabricated ceramic blocks are free from internal defects and the computer program is designed to produce shapes that will stand up to wear.
Savings in time and labor have the potential to reduce costs, and the promise of faster, high-quality restorations should appeal to patients and patients are also happy to avoid the need for gag-inducing impressions.
Another benefit is that all the scans can be stored on the computer; whereas, standard stone models take up space and can chip or break if stored improperly.
Still, CAD/CAM systems have disadvantages. The initial cost of the equipment and software is high, and the practitioner needs to spend time and money on training. Dentists without a large enough volume of restorations will have a difficult time making their investment pay off.
Just as with conventional impressions, in taking an optical scan the dentist needs to obtain an accurate recording of the tooth in need of restoration. The scan needs to emphasize the finish line and precisely duplicate the surrounding and occlusive teeth. Digital scanning requires the same type of soft-tissue management, retraction, moisture control, and hemostasis that is so important for conventional impressions.
Digital impression systems may not save time as they are currently used because of the need for multiple steps. For example, dentists who use certain scanners must first send the images for a cleanup process, which is followed by setting of the margins by a dental technician. The images next go to the clinician’s dental laboratory for review and then back for model milling. Finally, the models and dies are then sent to the clinician’s dental laboratory for fabrication of the restoration.
Office-based devices
Four products are presently available for digital impressions in the dental office: CEREC AC (Sirona, Charlotte, NC, USA), E4D Dentist (D4D Technologies, Richardson, TX, USA), iTero (Cadent, Carlstadt, NJ, USA), and Lava COS (3M ESPE, St Paul, MN, USA). Taking digital impressions allows dentists to do away with selecting trays, mixing materials and waiting for them to set, cleaning up the mess from the impressions, disinfecting the impressions, and shipping the impressions to a laboratory.
The CEREC and E4D devices can be combined with in-office design and milling; whereas, the iTero and Lava COS devices are reserved for image acquisition only. In-office milling allows same-day restorations.
The CEREC System
CEREC, introduced in 1987, was the first dental system to combine digital scanning with a milling unit. The system allows dentists to provide restorations made from commercially available ceramic blocks in a single visit.
The earliest models produced inlays and onlays only. The newest model, known as CEREC AC powered by BlueCam (Sirona, Charlotte, NC, USA) and introduced in 2009, also has the ability to take half-arch or full-arch impressions and create crowns, veneers, and bridges.
The current acquisition system employs intense blue light from blue light-emitting diodes (LEDs). The camera projects blue light onto the teeth, which reflects it back at a slightly different angle. This method of visualization is referred to as active triangulation .
To use the system, the entire tooth preparation to be scanned is coated with a layer of special titanium dioxide powder, which makes translucent areas of the teeth opaque and permits the camera to register all of the tissues. Several optical impressions are then taken from an occlusal orientation, being sure to obtain images of the tooth to be restored as well as the adjacent and opposing teeth. The scanner is able to focus automatically.
After the impression is complete, a 3-D rendering of the tooth to be restored appears on the monitor. The dentist is able to mark where the die should begin and end based on this image. The software program then generates a proposed restoration based on comparisons to the surrounding teeth, which can then be altered or fine tuned as needed.
After the design is approved, the milling process can begin. A block of ceramic or composite material in the correct color is simply inserted into the milling unit.
Alternatively, the dentist can obtain a digital impression and send the data to a dental laboratory. The laboratory can then design and mill the restoration using CAD/CAM technology. They can also use the digital image to fabricate a hard resin model based on the data and proceed to fabricate the restoration in the conventional manner.
The E4D Dentist System
The E4D Dentist system, which made its debut in 2008, is presently the only other system besides CEREC that permits same-day in-office restorations. Dentists can purchase the design center and laser scanner alone, or also purchase the milling unit.
This system includes a laser scanner, called the IntraOral Digitizer, along with a design center and milling unit. The scanner is small, so patients do not need to open their mouth as wide ( Fig. 1 ).
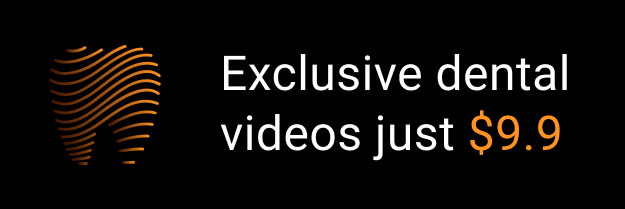