Abstract
Objectives
To evaluate the null hypotheses that hydrofluoric (HF) acid etching time would neither decrease the biaxial flexural strength of a glass-based veneering ceramic nor enhance it after silane and unfilled resin (UR) applications.
Methods
Disc-shaped IPS e.max ZirPress specimens were allocated into 12 groups: G1-control (no-etching), G2-30 s, G3-60 s, G4-90 s, G5-120 s, G6-60 s + 60 s. Groups (G7–G12) were treated in the same fashion as G1–G6, but followed by silane and UR applications. Surface morphology and roughness (Ra and Rq) of the ceramics were assessed by means of scanning electron microscopy (SEM) and profilometry, respectively. Flexural strength was determined by biaxial testing. Data were analyzed by two-way ANOVA and the Sidak test ( α = 0.05). Weibull statistics were estimated and finite element analysis (FEA) was carried out to verify the stress concentration end areas of fracture.
Results
The interaction (etching time vs. surface treatment) was significant for Ra ( p = 0.008) and Rq (0.0075). Resin-treated groups presented significantly lower Ra and Rq than non-treated groups, except for the 60 s group ( p < 0.005). SEM revealed that etching affected the ceramic microstructure and that the UR was able to penetrate into the irregularities. A significant effect of etching time ( p = 0.029) on flexural strength was seen. G7–G12 presented higher strength than G1–G6 ( p < 0.0001). None of experimental groups failed to show 95% confidence intervals of σ 0 and m overlapped. FEA showed lower stress concentration after resin treatment.
Significance
HF acid etching time did not show a damaging effect on the ceramic flexural strength. Moreover, the flexural strength could be enhanced after UR treatment.
1
Introduction
Numerous all-ceramic systems for indirect restorations such as veneers, multiple-unit posterior fixed dental prostheses (FDPs) and dental implant restorations have been developed and used clinically in oral rehabilitation . The success of all-ceramic restorations depends not only on a meticulous tooth preparation in addition to laboratory and clinical techniques of ceramic processing and preparation, but also on the bonding of these restorations to the tooth structure. Ceramic bonding to tooth structure can be accomplished by establishing a reliable bond between the internal surface of the restoration and the luting agent. Typically, the bond formed between the ceramic and luting agent is achieved via micro-mechanical interlocking between an etched (e.g., hydrofluoric/HF acid, acidulated phosphate fluoride/APF) or air-abraded (e.g., aluminum oxide particles) ceramic internal surface and a resin-based cement. After etching or air-abrasion of the ceramic surface, a silane coupling agent is often employed to promote chemical bonding through the formation of siloxane covalent and hydrogen bonds .
A great body of literature has indicated HF acid etching as one of the most effective methods in achieving high bond strength values and a durable bond between glass-based ceramics and resin cements. The rationale for the high bond strength values after etching is based on the fact that HF etching amplifies the ceramic surface roughness and surface energy by means of a selective glassy-phase removal and crystalline structure exposure, which improves the interaction ceramic–resin cement . Nonetheless, HF acid etching effect on the mechanical strength of glass-based ceramics remains uncertain. Even though some studies have reported that microstructural changes caused by HF acid at different etching regimes did not negatively impact the strength of ceramics , others have suggested that both HF acid concentration and etching time have to some extent a weakening effect on the strength of ceramics . Most importantly, recent studies have reported a significant and positive influence of unfilled resin (UR) application after silane treatment on the ceramic flexural strength . Therefore, this study sought to evaluate the null hypotheses that hydrofluoric (HF) acid etching time would neither decrease the biaxial flexural strength of a low-fusing nanofluorapatite veneering glass-ceramic also utilized to fabricate porcelain laminate veneers (IPS e.max ZirPress, Ivoclar-Vivadent) nor enhance it after silane and unfilled resin (UR) applications.
2
Materials and methods
2.1
Ceramic specimens preparation
One hundred and forty four disk-shaped IPS e.max ZirPress ceramic specimens (15 ± 1 mm in diameter and 0.8 ± 0.1 mm in thickness) were made from green casting wax (Corning’s wax, Ronkonkoma, NY). The complete investment ring was transferred to the ceramic furnace Programat EP 5000 (Ivoclar-Vivadent, Amherst, NY) and the e.max ZirPress program selected ( Table 1 ) following manufacturer instructions. After completion of the pressing stage, the investment ring was removed from the furnace and left to cool to room temperature. Once cooled, the investment was divested from the specimen with polishing glass beads: first at 4 bars (60 psi) and then at 2 bars (30 psi) of pressure. All specimens were then cleaned with Invex liquid (Ivoclar-Vivadent) and running water. The specimens were wet-ground with 400-grit and 600-grit silicon carbide paper to obtain standardized flat surfaces, cleaned in an ultrasonic bath with distilled water for 15 min, and then air-dried.
Material | Heat up temperature (°C) | Start temperature (°C) | Heat rate (°C/min) | Vacuum hold time (min) | Pressing temperature (°C) | Press time (min) |
---|---|---|---|---|---|---|
IPS e.max ZirPress | 900 | 700 | 60 | 15 | 910 | 6 |
2.2
Etching regimes and surface treatment
The specimens were divided into 6 groups ( n = 24) according to the etching regime received ( Table 2 ). A 5% hydrofluoric acid gel (IPS ceramic etching gel, Ivoclar-Vivadent) was used, as recommended by the manufacturer . Group 1 was left as-polished (control), Groups 2–5 were etched for 30, 60, 90 and 120 s, respectively. In the re-etched group (Group 6), which intended to simulate saliva contamination (IRB #0304-58) before cementation, the samples were immersed in saliva at 37 °C for 1 min, rinsed with distilled water, and air-dried before the second etching procedure. After etching, all groups were rinsed with distilled water for 20 s and then air-dried for 10 s. All specimens were then placed in isopropyl alcohol and sonicated for 60 min in order to ensure the elimination of contaminants (e.g., grease and oil from handling, surfactant from acid gels, and saliva) . More importantly this was carried out to remove salts formed over the ceramic microstructure that could impede proper resin infiltration.
IPS e.max ZirPress n = 144 | ||||||||||||
---|---|---|---|---|---|---|---|---|---|---|---|---|
Etching regimen | Non-etched n = 24 | 30 s n = 24 | 60 s n = 24 | 90 s n = 24 | 120 s n = 24 | Re-etched n = 24 | ||||||
Surface treatment | No | Silane + UR | No | Silane + UR | No | Silane + UR | No | Silane + UR | No | Silane + UR | No | Silane + UR |
Groups | G1 | G7 | G2 | G8 | G3 | G9 | G4 | G10 | G5 | G11 | G6 | G12 |
n = 12 | n = 12 | n = 12 | n = 12 | n = 12 | n = 12 | n = 12 | n = 12 | n = 12 | n = 12 | n = 12 | n = 12 |
Half of the specimens ( n = 12) in each of the 6 previously mentioned groups were then treated with a silane coupling agent (Silane Monobond S, Ivoclar-Vivadent) for 60 s, air-dried, and coated with a single layer of an unfilled resin (UR, Heliobond, Ivoclar-Vivadent). Single layer UR application was performed by applying one drop of the UR solution into a mixing well, using an applicator brush (Centrix Benda Brush–Centrix Inc., Shelton, CT, USA) to apply to the ceramic surface, and then polymerizing the UR layer for 10 s through a Mylar strip. The thickness of the specimens for the treated groups (G7–G12) was measured using a digital caliper (Mitutoyo Digimatic Caliper, Mitutoyo) after specimen preparation to ensure the thickness of the UR layer was not greater than 30 μm and thus considered a monolayered structure .
2.3
Surface micro-morphology and surface roughness evaluations
Ceramic specimens (G1–G12) were mounted on Al stubs, sputter-coated with Au-Pd alloy, and imaged at various magnifications using a JEOL SEM (JSM-6390, JEOL, Tokyo, Japan) at an acceleration voltage of 3–5 keV. Surface roughness values (Ra and Rq, in μm) were measured using a non-contact 3D optical profilometer (Proscan 2000, Scantron Industrial Products Ltd., Taunton, England, UK) and dedicated software (version 2.0.17 Scantron Industrial Products Ltd.). Each scanning area was limited to 1 × 1 mm 2 using the S5/03 sensor at 10 μm step size in both x and y directions.
2.4
Biaxial flexural strength test
The specimens from G1 to G6 were etched on the same day as the biaxial flexural test, performed by using a piston-on-three-ball technique as per ISO 6872. The ceramic surfaces of G7–G12 specimens were conditioned 24 h prior to the test and stored in a desiccator at 37 °C with a relative humidity of 16% before testing. After centering the disk-shaped specimens on the top of three steel spheres (i.e., 3.2 mm in diameter, 120° apart forming a circle of 10 mm diameter), the load was applied perpendicular to the center of the specimens by a steel piston with a 1.58 mm diameter flat-end tip using a universal testing machine until fracture at a rate of 1 mm min −1 (MTS Sintech ReNew 1123, Eden Prairie, MN) .
Biaxial flexural strength was calculated based on the recorded load at fracture using the standard equation:
S = −0.2387 P ( X − Y )/ d 2 , where S is the maximum tensile stress (in MPa) and the biaxial flexural strength at fracture, P is the load at fracture (in N), and d is the specimen thickness at fracture origin (in mm). The X { X = (1 + v )ln( B / C ) 2 + [(1 − ν )/2]( B / C ) 2 } and Y { Y = (1 + ν )[1 + ln( A / C ) 2 ] + (1 − v )( A / C ) 2 }, where ν is the Poisson’s ratio, A is the support sphere radius (mm), B is the radius of the tip of the piston (mm), and C is the specimen radius (mm). A 0.25 Poisson’s ratio was used since it is considered the standard recommendation .
2.5
Weibull statistics
The Weibull analysis was performed on the ascending order ranking of the biaxial flexural strength data. The Weibull distribution followed the equation:
<SPAN role=presentation tabIndex=0 id=MathJax-Element-1-Frame class=MathJax style="POSITION: relative" data-mathml='Pf=1−exp−σσ0m’>Pf=1−exp(−(σσ0)m)Pf=1−exp−σσ0m
P f = 1 − exp − σ σ 0 m
, where Pf is the probability of failure, σ is the strength at a given Pf , σ 0 is the characteristic strength, and m is the Weibull modulus.
Pf was calculated from the following formula: Pf = RANK /( N + 1), where RANK is the rank order of flexural strength and N is the total number of specimens. The Weibull distribution can be simplified as follows :
<SPAN role=presentation tabIndex=0 id=MathJax-Element-2-Frame class=MathJax style="POSITION: relative" data-mathml='lnln1(1−Pf)=mlnσ−mlnσ0′>lnln(1(1−Pf))=mlnσ−mlnσ0lnln1(1−Pf)=mlnσ−mlnσ0
ln ln 1 ( 1 − P f ) = m ln σ − m ln σ 0
.
2.6
Statistical analysis
Summary statistics (mean, standard deviation) were calculated for surface roughness and ceramic flexural strength data for each of the groups. Statistical analysis using two-way ANOVA and Sidak multiple comparisons procedure with a 5% significance level were used to evaluate the effects of etching time and treatment with UR on surface roughness and flexural strength data. In addition, Weibull characteristic strength and modulus parameters along with 95% confidence intervals were calculated using parametric Weibull survival analysis. Based on previous studies, the within-group standard deviation was expected to be 35 MPa for flexural strength . With a sample size of 12 specimens per group, the study had 80% power to detect differences of 60 MPa for flexural strength, assuming two-sided tests conducted at an overall 5% significance level.
2.7
Finite element analysis
The experimental biaxial flexural test was simulated using finite element analysis (FEA) to verify the stress concentration and validate the experimental results. A tri-dimensional finite element model was carried out only for the ceramic with and without the UR treatment, according to the experimental dimensions and configuration. An UR layer of 10 μm thick was modeled for the resin-treated group using a CAD (Computer Aided Design) Rhinoceros software (version 4.0 SR8, McNeel North America, Seattle, WA, USA). The solid geometry was imported by software Ansys (ANSYS 13.0, ANSYS Inc., Houston, TX, USA) using the . STEP file format. Solid tetrahedral elements were used for the mesh. The contacts between the geometries (i.e., spheres, tip and specimen) were considered with 0.12 frictional. Therefore, the UR layer and ceramic were assumed perfectly bonded.
The mechanical properties of the materials are summarized in Table 3 and were considered homogeneous, isotropic, and linearly elastic. The specific applied load in the finite element model was a displacement of tip application (0.01 mm) to keep on linear behavior of disk on the test. Additionally, the boundary displacement constraints reflected the experimental test configuration where a constraint was simulated by fixing the base of all spheres on the axial (vertical displacement) and allowing free horizontal displacement. The mesh was built with hexahedron elements with slow transition and high smoothing as mesh control and after a 10% of convergence test determined the total number of elements and nodes.
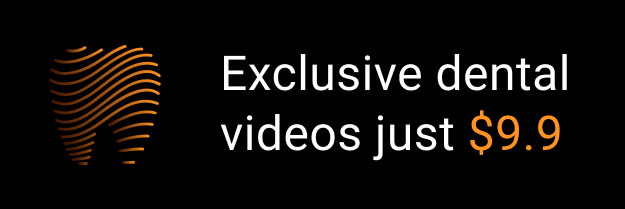