Abstract
Objectives
The purpose of this study was to ascertain whether the amount of Zn in gold alloys contributes to porcelain–metal bonding.
Methods
Experiments were carried out using a commercial Pd-free gold alloy with a nominal composition of 88.7 wt% Au, 9.49 wt% Pt, 1.5 wt% Zn, 0.1 wt% Mn, 0.2 wt% Rh, and 0.1 wt% Ir, which contains Zn and no other elements (In, Sn, Fe) known to affect porcelain–metal bond strength. To establish the effect of oxidation of the metal surface, porcelain was applied both to preoxidized and to non-preoxidized metal specimens. The bond strength was evaluated by means of the ISO 9693: 1999 crack initiation test. A conventional gold alloy was used as a control. The elemental distributions at the porcelain/alloy interfaces were analyzed in cross section by electron probe microanalysis. Additionally, after the bond strength test, cross-sections of the interfaces of the debonded specimens were microscopically analyzed to characterize the fracture mode.
Results
The Pd-free gold alloy joints showed significantly higher bond strength values than joints made with conventional gold alloy. Preoxidation treatment significantly increases the bond strength, in the preoxidized joints Zn was highly localized at the interface and diffused into the porcelain up to about 10 μm from the interface, and the joint failed by cohesive fracture in the porcelain. In contrast, the non-preoxidized joint showed mainly adhesive fracture at the porcelain/alloy interface.
Significance
The presence of Zn in gold alloys plays a part in establishing chemical bonding thus improving the bond strength between porcelain and alloy.
1
Introduction
A detailed understanding of the bonding mechanism between porcelain and alloy is necessary if new alloys are to be developed for metal–ceramic restorations. This knowledge provides a basis for establishing the rationale to generate proper clinical and laboratory techniques, which are essential for successful restorations.
Bonding between porcelain and alloy is accomplished by means of a sintering process, and is based on adhesion due to van der Waals forces, mechanical interlocking, compressive bonding force, and chemical bonds between porcelain and the oxide layer on the surface of the metal . Several theories indicate that chemical bonding is the primary contributing factor to bond strength , and that the maximum bond strength at the ceramic/metal interface is realized by the additional existence of a chemical bond which is represented by the presence of a continuous electronic structure across the interface . Electron microprobe studies have shown that minor elements in gold alloys such as In, Sn, and Fe oxidize selectively and form a surface oxide layer during heat treatment . Other microprobe studies have shown that these gold alloy minor elements are highly localized within a few micrometers of the porcelain/metal interface, and indicated that the oxide layer contributes to chemical bonding process by reacting with the porcelain during firing . Moreover, the strength of the bond between a gold alloy and porcelain has been shown to be affected by these minor elements and their concentrations . Thus, most of the conventional gold alloys for metal–ceramic restorations contain In, Sn and/or Fe.
Recently, Pd-free gold alloys which contain Zn in addition to In, Sn and/or Fe were developed in response to concern about allergic reactions resulting from the use of Pd in dental alloys . The alloy constituents of Pd-free gold alloys are different from those of conventional gold alloys based on Au–Pt–Pd–In. The inclusion of In in Au–Pt alloys assists the hardening process , and the presence of Pd permits, due to its narrow melting range with Au and Pt, a sufficient amount of In to be homogeneously dissolved in the alloy . For these reasons, Au–Pt–In alloys without Pd are not sufficiently strong. Hence, modern Pd-free gold alloys are based on the ternary system Au–Pt–Zn. It is known that the addition of Zn to this system has an important role in the improvement of the mechanical properties of the alloy , and serves as a deoxidizer because of its high oxidation tendency. However, there is no information on the effect of Zn on the mechanisms of bonding. We therefore investigate the hypothesis that the minor element of Zn in gold alloys plays a part in establishing chemical bonding between porcelain and alloy.
The purpose of this study was to confirm this hypothesis, experimental measurements (bond strength test, elemental analysis, and characterization of fracture mode) were carried out on a commercial Pd-free gold alloy which contains Zn and none of the elements (In, Sn, Fe) known to affect the bond strength between porcelain and alloy. A further purpose of this study was to obtain an understanding of the mechanism by which the chemical interaction affects the bond strength.
2
Materials and methods
A Pd-free gold alloy containing Zn but free of In, Sn and Fe (Bio Herador SG, Heraeus Kulzer GmbH, Hanau, Germany) was selected for this study. A conventional gold alloy based on Au–Pt–Pd–In (Degudent U, Degudent GmbH, Hanau, Germany) was used as a control for the bond strength test. The nominal compositions and physical properties of the alloys are shown in Table 1 .
Alloy | Composition (wt%) | Modulus of elasticity (GPa) | Coefficient of thermal expansion (×10 −6 °C −1 ) | ||||||||||||
---|---|---|---|---|---|---|---|---|---|---|---|---|---|---|---|
Au | Pt | Pd | Ag | Cu | In | Sn | Fe | Zn | Re | Mn | Rh | Ir | |||
Bio Herador SG | 89 | 9.5 | – | – | – | – | – | – | 1.5 | – | 0.1 | 0.2 | <0.1 | 90 | 14.5 |
Degudent U | 77 | 9.8 | 8.9 | 1.2 | 0.3 | 1.5 | 0.5 | 0.2 | – | 0.2 | – | – | 0.1 | 110 | 13.8 |
2.1
Bond strength test
Specimens to evaluate the bond strength by crack initiation test were prepared according to ISO 9693 . Six metal specimens were prepared for each alloy. In addition, six specimens were prepared using the Bio Herador SG material, contrary to manufacturer’s instructions these specimens were not pre-oxidized. Acrylic patterns (Clarex, Nitto Jushi Kogyo Co. Ltd., Aichi, Japan) of appropriate size were embedded into a phosphate bonded investment (Innovest HE, GC dental Industrial Corp., Tokyo, Japan). After curing for an hour, the specimens were placed in a burnout oven at room temperature and gradually heated to 800 °C. All the specimens were cast with a vacuum pressure casting machine (Neo Super Cascom, Denken Co. Ltd., Kyoto, Japan), bench cooled, and then divested. The specimens were hand shaped to dimensions of 25 mm × 3 mm × 0.5 mm with 1200 grit SiC abrasive paper. To prepare the surfaces for porcelain firing, the specimens were sandblasted using 50 μm alumina powder, and then ultrasonically cleaned for 30 min in distilled water. Six specimens of each alloy were given oxidation heat treatment before the application of porcelain according to the manufacturer’s instructions. The remaining six specimens of Bio Herador SG were left in an as-cast state. The specimens made from Bio Herador SG were oxidized by heating in a vacuum with a 10 min hold at 950 °C, whereas those made from Degudent U were oxidized by heating in air with a 10 min hold at 980 °C. All heat treatments were performed in a dental porcelain furnace (Vita Vacumat 40T, Vita Zahnfabrik, Bad Säckingen, Germany). Commercial porcelain (Vita VMK95, Vita Zahnfabrik, Bad Säckingen, Germany), with a thermal expansion coefficient of 13.3–13.7 × 10 −6 °C −1 , was selected because it is compatible with all the gold alloys used in this study. The preparation of the porcelain by firing and then cooling process, was performed according to the manufacturer’s instructions ( Table 2 ). The porcelain was applied symmetrically over the central 8 mm of the metal plate. First, two layers of opaque porcelain with a total thickness of approximately 0.3 mm were fired individually. Next, two layers of body porcelain with a total thickness of approximately 0.8 mm were added over the opaque porcelain and fired. Then, the ceramic specimen was shaped using a polisher to dimensions of 8 mm × 1.1 mm × 3 mm. Finally, the porcelain was glazed.
Pre-drying | Heating rate (°C/min) | Firing temperature (°C) | Holding time (min) | Vacuum (min) | Cooling after firing | ||
---|---|---|---|---|---|---|---|
Temperature (°C) | Time (min) | ||||||
Wash opaque | 500 | 6 | 75 | 950 | 1 | 6 | Rapid cooling * |
Opaque | 500 | 6 | 72 | 930 | 1 | 6 | Rapid cooling * |
1st dentin | 600 | 6 | 55 | 930 | 1 | 6 | Normal cooling ** or Slow cooling *** |
2nd dentin | 600 | 6 | 55 | 930 | 1 | 6 | Normal cooling ** or Slow cooling *** |
Glaze | 600 | 0 | 83 | 930 | 1 | 0 | Normal cooling ** or Slow cooling *** |
* At the end of the program the firing platform is driven down completely and firing tray with the objects is removed immediately.
** For Degudent U, the firing platform is driven down at the end of the program and the firing tray is left in the radiated heat for 3 min before it is removed.
*** For Bio Heredor SG, slow cooling for 6 min to the initial temperature is performed at the end of the program.
Specimens were then subjected to a three point bending test using the ISO 9693 standard method, using a mechanical testing machine (Model 4481, Instron Corporation, Canton, MA, USA). The porcelain–alloy joints were placed in the bending apparatus with the ceramic positioned on the side opposite to the applied load. The distance between the supports was 20 mm, and radius of the bending piston was 1 mm. The force was applied at a rate of 1.5 mm/min. The failure load ( F fail ) of each specimen was recorded at the point when a debonding crack occurred at one end of the ceramic layer. The bond strength ( τ b ) for each specimen was calculated according to the following formula:
τ b = k × F f a i l
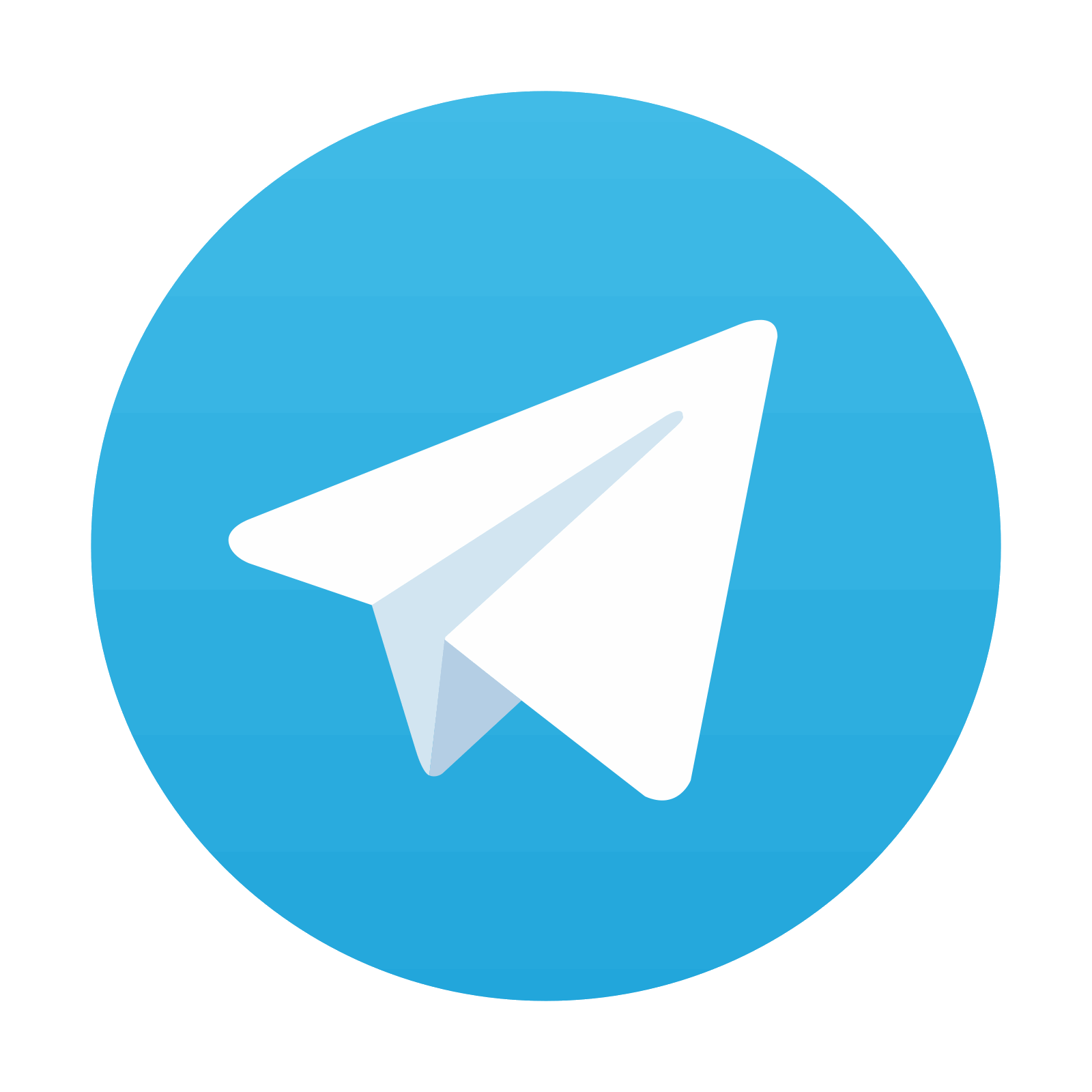
Stay updated, free dental videos. Join our Telegram channel

VIDEdental - Online dental courses
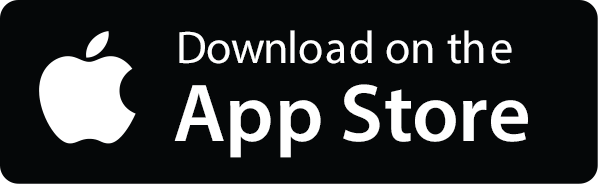
