Abstract
Objectives
The objectives of the study were to describe the surface structure and the chemical surface composition of Y-TZP ceramics produced by using the modified additive technique and to evaluate the flexural strength of Y-TZP with or without surface modification and with different pretreatments: etching before or after sintering combined with or without an adhesive cement system.
Methods
Y-TZP discs were used for surface analysis ( n = 48) and for biaxial flexural strength testing ( n = 200). The specimens were divided into groups depending on the cementation surface of Y-TZP: unmodified, sandblasted or glass-modified Y-TZP surfaces, and according to the production process: etching before or after sintering.
Results
The surface structure and the chemical composition of glass-modified Y-TZP differ; a rougher surface and phase transformation was identified compared to unmodified Y-TZP.
The unmodified Y-TZP groups showed significantly higher flexural strength compared to the glass-modified groups ( p < 0.001) and showed increased flexural strength after sandblasting ( p < 0.001). Furthermore, by adding cement to the surface, the value increased even further in comparison with the sandblasted non-cemented specimens ( p < 0.01). After thermocycling, however, the cement layer on the unmodified and the sandblasted surfaces had air pockets and regions with loose cement.
Significance
A rougher surface structure, superficial glass remnants and a higher content of m-phase was present in the cementation surface of glass-modified Y-TZP. The glass modification creates a bondable cementation surface that is durable. By etching the glass-modified Y-TZP before sintering, a more homogenous surface is created compared to one that is etched after sintering.
1
Introduction
Different surface treatments of stabilized zirconium dioxide (zirconia) have been proposed for adhesive cementation of zirconia-based restorations. The focus has been on surface treatments that increase the surface area in order to optimize the zirconia/cement bond and establish a strong and durable restoration . One method for producing bondable yttria-stabilized tetragonal zirconia polycrystals (Y-TZP) is to use an impaction-modification technique. During additive fabrication of a ceramic construction, an impaction glass medium is pressed into the cementation surface of the green-stage ceramic to create microretentions. Subsequently, the medium is removed using hydrofluoric acid to provide micromechanical and chemical retention to the surface .
Compared to etched glass ceramics, where the adhesive cement system is considered to seal the surface of the material and thereby contribute to increased strength of the restoration, it is difficult to obtain an adhesive bond between Y-TZP and an adhesive cement system without any pretreatment of the cementation surface . Surface modification techniques and other pretreatments, such as airborne particle abrasion, tribochemical silica coating, plasma spraying, glass fusing, selective infiltration etching, nanostructured alumina powder coating, laser etching and acid treatment, should therefore create micro-retention and activation of the surface without affecting the material properties of the Y-TZP . Evaluation of different surface treatments and their effect on the surface topography and roughness of different brands of zirconia show, however, that this is product-related. Several brands of Y-TZP are available on the market and they all use slightly different processing techniques – differences that may influence the final grain size, microstructure and physical properties of the material .
A possible drawback of the impaction-modification technique is that remnants of the impaction medium may affect the final properties of the oxide ceramic by inducing production-related flaws that could act as fractural impressions, thus reducing the strength of the material. The influence of the medium and the effect of etching the cementation surface have yet not been investigated as regards chemical composition and strength of the surface-modified Y-TZP.
The aims of this study were therefore:
- a)
to describe the surface structure and the chemical surface composition of Y-TZP ceramics produced by using modified additive technique.
- b)
to evaluate the flexural strength of Y-TZP with or without surface modification and with different pretreatments: etching before or after sintering – used with or without an adhesive cement system.
The hypotheses tested are:
- a)
there are differences in surface roughness between the surface-modified Y-TZP, regardless of pretreatment with etching, compared to an unmodified Y-TZP-surface.
- b)
glass phase remnants and different phases, both resulting from modified additive production, will be present on the surface of the Y-TZP after sintering.
- c)
there is no difference in strength, regardless of the surface modification and pretreatments, with or without an adhesive cement system.
2
Materials and methods
In this study, Y-TZP discs were used for surface analysis ( n = 48) and for biaxial flexural strength testing ( n = 200). The specimens were divided into groups depending on the cementation surface of Y-TZP: unmodified Y-TZP (C), or glass-modified Y-TZP surface (G), and according to the production process: etching before sintering (CE/GE), sintering (CS/GS), sintering followed by etching (CSE/GSE), sintering followed by sandblasting (CSS), and sintering and sandblasting followed by etching (CSSE), Table 1 .
Groups (Abbreviation) | Materials used | Pretreatment/sintering | Surface analysis ( n = 6) | Flexural strength test ( n = 25) |
---|---|---|---|---|
CE | Y-TZP a + HF b | Etched b before sintered c | IFM, AFM, SEM, EDS, XRD | – |
CS | Y-TZP | Sintered | IFM, AFM, SEM, EDS, XRD | Yes |
CSE | Y-TZP + HF | Sintered + etched | IFM, AFM, SEM, EDS, XRD | – |
CSC | Y-TZP + Panavia™F2.0 d | Sintered + cement d | – | Yes |
CSS | Y-TZP + Al 2 O 3 100 μm e | Sintered + sandblasted e | IFM, AFM, SEM, EDS, XRD | Yes |
CSSE | Y-TZP + Al 2 O 3 100 μm + HF | Sintered + sandblasted + etched | IFM, AFM, SEM, EDS, XRD | – |
CSSC | Y-TZP + Al 2 O 3 100 μm + Panavia™F2.0 | sintered + sandblasted + cement | – | Yes |
GE | Glass-modified Y-TZP f + HF | Etched before sintered | IFM, AFM, SEM, EDS, XRD | Yes |
GEC | Glass-modified Y-TZP + HF + Panavia™F2.0 | Etched + sintered + cement | – | Yes |
GS | Glass-modified Y-TZP | Sintered | IFM, AFM, SEM, EDS, XRD | – |
GSE | Glass-modified Y-TZP + HF | Sintered + etched | IFM, AFM, SEM, EDS, XRD | Yes |
GSEC | Glass-modified Y-TZP + HF + Panavia™F2.0 | Sintered + etched + cement | – | Yes |
a Y-TZP: grade TZ-3YSB-C (batch S306269B, Procera Zirconia, Nobel Biocare™ AB, Gothenburg, Sweden).
b HF: etched with 9% hydrofluoric acid (Ultradent ® Porcelain Etch, 9%, LOT B7814, Ultradent Products, Inc., South Jordan, Utah, USA) in 2 min, neutralized (IPS Ceramic, Neutralizing powder, LOT M04796 IvoclarVivadent, Schaan, Liechtenstein) in 2 min followed by thorough rinsing with water according to the cement manufacturer’s recommendation.
c Sintered: sintered in a sintering furnace (Everest Therm 4180, KaVo Everest ® , Biberach, Germany) according to the manufacturer’s instructions.
d Panavia™F2.0: treated with a primer (Clearfil Ceramic Primer, LOT 0025AA, Kuraray Noritake Dental Inc., Okayama, Japan) prior to application of the adhesive cement, Panavia™F 2.0 (Panavia™F 2.0, base paste LOT 0112AA and catalyst paste LOT 0575AA, Kuraray Noritake Inc., Okayama, Japan) and oxygen-blocking gel (Panavia™F 2.0 Oxyguard II, LOT 00655A, Kuraray Medical Inc., Okayama, Japan) according to the cement manufacturer’s recommendation.
e Al 2 O 3 100 μm: sandblasted with 110 μm Al 2 O 3 particles for 10 s with an air pressure of 2 bar and at a distance of 10 mm then thoroughly rinsed in water.
f Glass-modified YTZP: modified with glass granules Experimental Impaction Medium, Cerasci AB, Malmö, Sweden.
2.1
Manufacturing of specimens
A special dry-press punching tool made of stainless steel was made to fabricate the Y-TZP discs. Fabrication of the specimens was performed according to a previous study . Briefly: the tool was filled with 0.75–1.15 ± 0.01 g of Y-TZP granulated powder that was mechanically compressed uniaxially with 140 MPa for 5 min using a cuvette press. The bottom punch surface of the pressing tool that defines the cementation surface of the Y-TZP was used either with no medium added prior to compaction (C), or glass granules with a particle size of 40 μm or less added to the bottom punch prior to compaction (G), Table 1 . The tool was cleaned with 95% ethanol (ethanol 95%, batch no. SE10016023, Kemetyl AB, Haninge, Sweden) prior to each compaction.
Before sintering, the specimens with the unmodified surface (CE, n = 6) and with the glass-modified surface (GE, n = 31; GEC, n = 25) were etched with 9% hydrofluoric acid for 2 min, neutralized for 2 min, and then rinsed thoroughly with water and stored at room temperature for 24 h. All specimens, regardless of group, were finally sintered in a sintering furnace according to the manufacturer’s instructions. After sintering, the specimens with the unmodified surface (CS, n = 31) were left with no further treatment or were sandblasted with 110 μm Al 2 O 3 particles for 10 s with an air pressure of 2 bar and at a distance of 10 mm with the blasting nozzle moved gently perpendicular to the surface, then thoroughly rinsed with water (CSS, n = 31, CSSC, n = 25). The remaining specimens with the unmodified surface (CSE, n = 6), sandblasted surface (CSSE, n = 31) and glass-modified surface (GSE, n = 31, GSEC, n = 25) were etched with 9% hydrofluoric acid according to the prior etching procedure as described above, Table 1 .
2.2
Surface analysis
During all the steps in the fabrication process of the specimens, the cementation surface was analyzed with a light microscope (Leica DM 2500M, Leica Microsystems CMS, Wetzlar, Germany) at 500× magnification. Interferometry (IFM), atomic force microscopy (AFM), scanning electron microscopy (SEM), energy-dispersive X-ray spectroscopy (EDS) were used to define and characterize the surface, and X-ray diffraction (XRD) was used to identify the crystalline structure.
Topographical analysis was performed using IFM (MicroXAM™, ADE, Phase Shift Technology, Inc., Tucson, AZ, USA) with MapVue software (MetaMAP, Lexington, KY, USA) and by AFM (XE-100, Park Systems, Suwon, Korea) in order to characterize the surface roughness at micrometer level and nanometer level respectively. The IFM had a maximum resolution of 0.05 nm in the vertical direction and 0.3 μm in the lateral direction. The measured area of the specimens was 200 μm × 260 μm. Parametric calculations were performed after errors of form and waviness were removed using a Gaussian high pass filter (size 50 μm × 50 μm). AFM analysis was performed in intermittent contact mode using etched silicon probes with cantilever lengths of 125 nm and nominal resonance frequencies of 270–310 kHz. A scanning area of 10 μm × 10 μm with atomic level resolution in the vertical direction and 2 nm in the lateral direction was used and the measurements were performed at a scan rate of 0.2–0.4 Hz. Three specimens from each group and three measurements per specimen ( n = 9/group) were performed. Three parameters were selected according to proposed guidelines for biomaterial surface characterization : one height descriptive, S a (μm) = the arithmetic average height deviation from mean plane, one spatially descriptive, S ds (μm −2 ) = the density of summits, and one hybrid parameter S dr (%) = the developed surface ratio. Descriptive 3D images were reconstructed with imaging software MountainsMap 6.2 (Digital Surf, Paris, France)
Morphological examination was performed with SEM using a LEO Ultra 55 FEG high resolution SEM (Leo Electron Microscopy Ltd, Cambridge, UK) equipped in combination with an Oxford Inca EDS system (Oxford Instruments Nano Analysis, Bucks, UK) operating between 5 and 10 kV at 5000–100,000× magnification and with high vacuum. The samples were examined after surface sputtering for 60 s at 10 mA resulting in a 30 nm thick gold layer. EDS analysis at 15 kV and WD 10 at 10,000× magnification was performed to describe the atomic composition. One specimen from each group was analyzed. XRD was performed to analyze the crystalline structure of the unmodified and modified Y-TZP using a Bruker D8 Advance X-ray diffractometer (Bruker BioSpin Corp., Billerica, MA, USA) collecting a 2 θ scanning range of 27–60°, with a step size of 0.05° and with Cu K a1 radiation ( λ = 1.5405 Å) as the diffraction light source.
2.3
Biaxial flexural strength test
Two hundred specimens of Y-TZP were prepared for the biaxial flexural strength test according to a power analysis, two-sample test with a significance level of 5% with true difference of means set at 50 N and with a power of 95%. A total of four subgroups with or without an adhesive cement system, Panavia™F 2.0, were used ( n = 25), Table 1 . The fabrication process was performed in a precise order as the specimens were fabricated for the surface analysis and the final size of the discs was 12.8 ± 0.2 mm in diameter and 1.29 ± 0.11 mm in height, in accordance with ISO 6872:2008 . All discs were subjected to heat treatment to simulate the firing cycles of a recommended veneering porcelain (GC Initial ZR-FS, GC Europe N.V., Leuven, Belgium). The firing cycles were carried out in a calibrated furnace and each disc underwent four firings: frame modifier, dentin 1 and 2 and self-glaze firing, all steps according to the manufacturer’s recommendations, Table 2 .
Firing program | Preheating temperature (°C) | Dryingtime (min) | Heating rate (°C/min) | Final temperature (°C) | Holding time (min) | Vacuum start (°C) | Vacuum stop (°C) |
---|---|---|---|---|---|---|---|
Frame Modifier | 450 | 4.00 | 55 | 800 | 1.00 | 450 | 800 |
Dentin 1st | 450 | 6.00 | 45 | 810 | 1.00 | 450 | 810 |
Dentin 2nd | 450 | 6.00 | 45 | 800 | 1.00 | 450 | 800 |
Glaze | 480 | 2.00 | 45 | 820 | 1.00 | – | – |
b Programat ® EP 5000, IvoclarVivadent ® AG, Schaan, Liechtenstein.
All subgroups with surfaces that were to be covered by cement (CSC, CSSC, GEC, GSEC) were etched as described above for the CE, GE and GEC groups to clean the surface prior to cementation. All discs were treated with a primer prior to application of the adhesive cement Panavia™F 2.0 according to the cement manufacturer’s recommendation, Table 1 . The cement was applied on the cementation surface of the Y-TZP and a 0.12 mm thick plastic film was placed between an alignment apparatus with a seating load of 15 N during polymerization. The excess resin was removed from the margin using disposable brushes and the cement was light-cured with a curing lamp (Heraeus Translux ® Power Blue ® , Heraeus Kulzer GmbH, Hanau, Germany). The polymerization light intensity was 1000 mW/cm 2 and the curing time was set to 20 s for each of four directions 90° apart and finally 60 s in one direction with the seating load removed. Subsequently, an oxygen-blocking gel was applied for 3 min followed by thorough rinsing with water for 1 min to remove any residues of the oxygen-blocking gel, Table 1 . All the excess resin was removed with a surgical blade after polymerization was completed and the discs were then stored in water at room temperature (22 °C) for 24 h to avoid desiccation during storage.
Before the biaxial flexural strength test, all specimens were artificially aged by means of cyclic preloading and thermocycling. All specimens were subjected to cyclic preloading at loads between 10 and 100 N at 1 Hz in a wet environment for 10,000 cycles using a specially constructed preloading device (MTI Engineering AB, Lund, Sweden/Pamaco AB, Malmö, Sweden). The discs were placed on three supporting steel balls (Ø 2.5 mm) and the load was applied in the center and perpendicular to the discs using a centrally placed stainless steel punch (Ø 1.4 mm). A 0.12 mm thick plastic film was placed between the three supporting balls and the disk, and between the punch and the disk . Subsequently, all specimens were thermocycled at 5000 cycles in two baths; one at 5 °C and the other at 55 °C. Each cycle lasted 60 s (20 s in each bath and 10 s for transfer between the baths). The specimens were placed in a testing device, according to the cyclic preloading performed, and loaded to fracture in a wet environment using a universal testing machine (Instron model 4465, Instron ® , Canton, MA, USA). The crosshead speed was 0.5 mm/min. Load at fracture (N) was registered when a visible fracture occurred. The flexural strength in megapascals (MPa) was calculated according to ISO 6872:2008 and with the Poisson’s ratio of 0.25 . Throughout the test period, whenever the specimens were not being actively tested they were stored in a humid environment at room temperature.
2.4
Statistical analysis
One-way ANOVA, Tukey’s test was used to determine differences in surface structure and flexural strength between the groups (IBM SPSS Statistics 20, SPSS Inc., Chicago, IL, USA). The level of significance was set to α = 0.05.
2
Materials and methods
In this study, Y-TZP discs were used for surface analysis ( n = 48) and for biaxial flexural strength testing ( n = 200). The specimens were divided into groups depending on the cementation surface of Y-TZP: unmodified Y-TZP (C), or glass-modified Y-TZP surface (G), and according to the production process: etching before sintering (CE/GE), sintering (CS/GS), sintering followed by etching (CSE/GSE), sintering followed by sandblasting (CSS), and sintering and sandblasting followed by etching (CSSE), Table 1 .
Groups (Abbreviation) | Materials used | Pretreatment/sintering | Surface analysis ( n = 6) | Flexural strength test ( n = 25) |
---|---|---|---|---|
CE | Y-TZP a + HF b | Etched b before sintered c | IFM, AFM, SEM, EDS, XRD | – |
CS | Y-TZP | Sintered | IFM, AFM, SEM, EDS, XRD | Yes |
CSE | Y-TZP + HF | Sintered + etched | IFM, AFM, SEM, EDS, XRD | – |
CSC | Y-TZP + Panavia™F2.0 d | Sintered + cement d | – | Yes |
CSS | Y-TZP + Al 2 O 3 100 μm e | Sintered + sandblasted e | IFM, AFM, SEM, EDS, XRD | Yes |
CSSE | Y-TZP + Al 2 O 3 100 μm + HF | Sintered + sandblasted + etched | IFM, AFM, SEM, EDS, XRD | – |
CSSC | Y-TZP + Al 2 O 3 100 μm + Panavia™F2.0 | sintered + sandblasted + cement | – | Yes |
GE | Glass-modified Y-TZP f + HF | Etched before sintered | IFM, AFM, SEM, EDS, XRD | Yes |
GEC | Glass-modified Y-TZP + HF + Panavia™F2.0 | Etched + sintered + cement | – | Yes |
GS | Glass-modified Y-TZP | Sintered | IFM, AFM, SEM, EDS, XRD | – |
GSE | Glass-modified Y-TZP + HF | Sintered + etched | IFM, AFM, SEM, EDS, XRD | Yes |
GSEC | Glass-modified Y-TZP + HF + Panavia™F2.0 | Sintered + etched + cement | – | Yes |
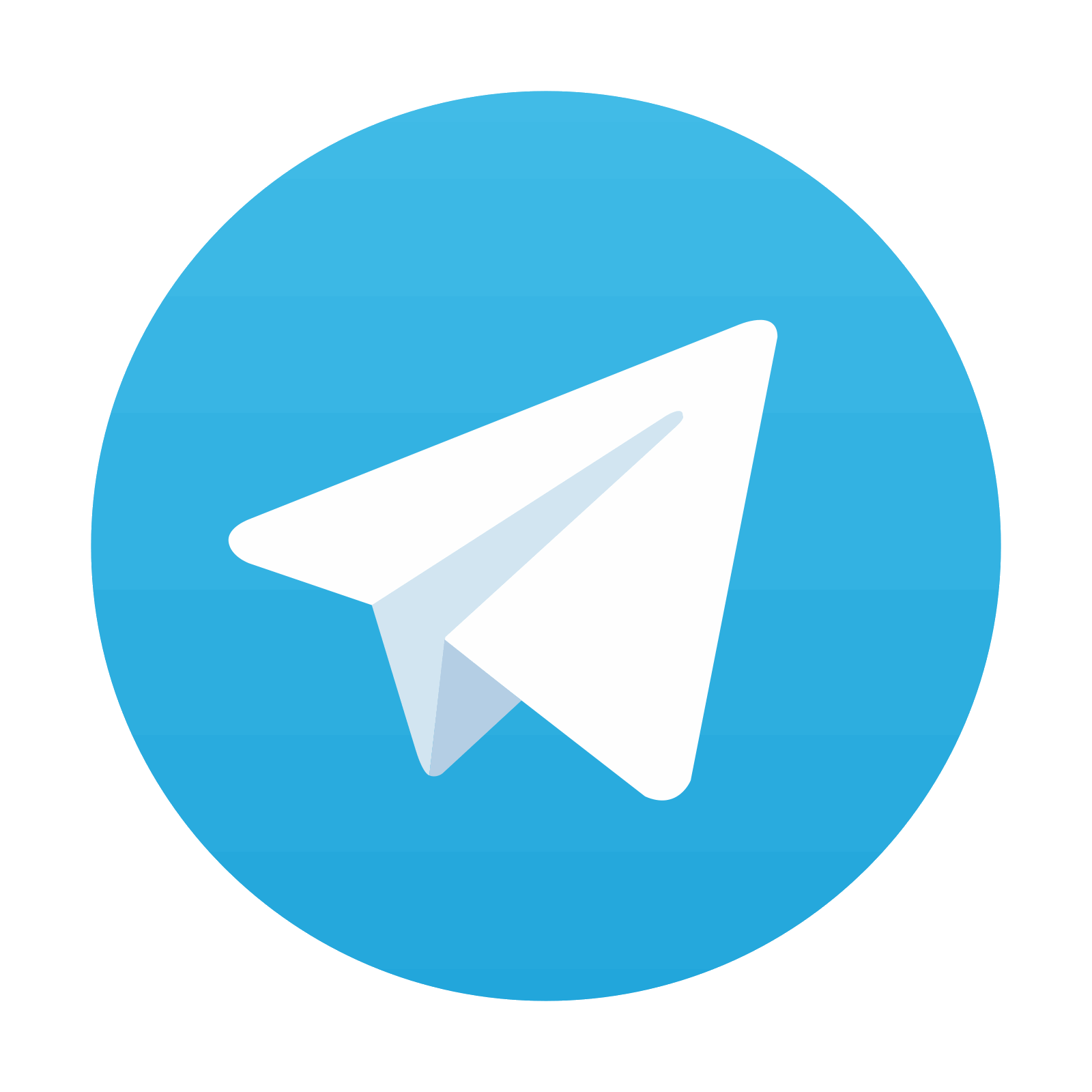
Stay updated, free dental videos. Join our Telegram channel

VIDEdental - Online dental courses
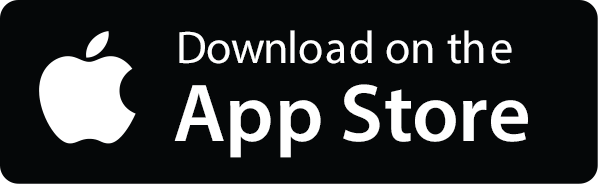

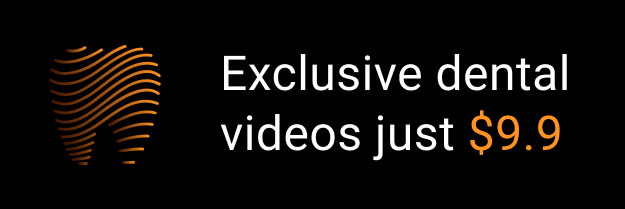