Abstract
Objective
To determine the slow crack growth (SCG) and Weibull parameters of five dental ceramics: a vitreous porcelain (V), a leucite-based porcelain (D), a leucite-based glass-ceramic (E1), a lithium disilicate glass-ceramic (E2) and a glass-infiltrated alumina composite (IC).
Methods
Eighty disks (Ø 12 mm × 1.1 mm thick) of each material were constructed according to manufacturers’ recommendations and polished. The stress corrosion susceptibility coefficient ( n ) was obtained by dynamic fatigue test, and specimens were tested in biaxial flexure at five stress rates immersed in artificial saliva at 37 °C. Weibull parameters were calculated for the 30 specimens tested at 1 MPa/s in artificial saliva at 37 °C. The 80 specimens were distributed as follows: 10 for each stress rate (10 −2 , 10 −1 , 10 1 , 10 2 MPa/s), 10 for inert strength (10 2 MPa/s, silicon oil) and 30 for 10 0 MPa/s. Fractographic analysis was also performed to investigate the fracture origin.
Results
E2 showed the lowest slow crack growth susceptibility coefficient (17.2), followed by D (20.4) and V (26.3). E1 and IC presented the highest n values (30.1 and 31.1, respectively). Porcelain V presented the lowest Weibull modulus (5.2). All other materials showed similar Weibull modulus values, ranging from 9.4 to 11.7. Fractographic analysis indicated that for porcelain D, glass-ceramics E1 and E2, and composite IC crack deflection was the main toughening mechanism.
Significance
This study provides a detailed microstructural and slow crack growth characterization of widely used dental ceramics. This is important from a clinical standpoint to assist the clinician in choosing the best ceramic material for each situation as well as predicting its clinical longevity. It also can be helpful in developing new materials for dental prostheses.
1
Introduction
The esthetic limitations of metal-ceramic restorations have triggered the development of new all-ceramic materials which can be used for both single restorations and short-span fixed partial dentures. Currently, many all-ceramic systems are commercially available and most offer superior esthetics, since they allow for light transmission in a manner similar to those of natural dental structures. Despite the progress made in the last decade, due to their brittle nature, all-ceramic restorations still have lower clinical longevity compared to metal-ceramic restorations .
The fracture of ceramics in service occurs with little or no plastic deformation when cracks propagate in an unstable manner under applied tensile stresses. Fracture occurs when the stress intensity factor at the crack tip ( K I ) reaches a critical level ( K Ic ), defined by a combination of applied stress ( σ ), crack length ( a ) and a dimensionless constant ( Y ), which depends on the stress mode, shape and dimensions of the material, and geometry of the crack .
It has been demonstrated that ceramic materials show considerable variation in strength, primarily due to their extreme sensitivity to the presence of cracks of different sizes. The unstable fracture of ceramics starts from critical flaws, and this phenomenon may be explained by the “weakest link” theory, which determines that fracture always propagates from the largest flaw favorably oriented to the tensile stress. For a given ceramic material, the distribution of crack size, shape, and orientation differs from sample to sample and its strength is statistically distributed according to the flaw size distribution. It is recognized that the strength of ceramics needs to be analyzed using different statistical approaches, especially because the probability of failure depends on the presence of a potentially dangerous crack of size greater than a characteristic critical crack size. Also, fracture depends on the stressed area or the volume of the material, since larger areas or volumes increase the probability of critical flaw content .
The most commonly used method for the characterization of strength and structural reliability of ceramic materials is the Weibull statistical theory , which describes the strength of a brittle material based on the survival probability at a given stress level, S , which is a function of the stressed volume, the characteristic strength (a normalizing parameter, corresponding to the stress at which 63% of the specimens have failed), and the Weibull modulus ( m ), which indicates the nature, severity and dispersion of flaws. Higher values of Weibull modulus correspond to materials with uniform distribution of highly homogeneous flaws with narrower strength distribution, whereas lower values of m indicate non-uniform distribution of highly variable crack length (broad strength distribution).
One important aspect of the critical cracks in ceramic materials is the fact that they may exhibit a slow and stable crack growth (SCG) when subjected to stresses below the critical value, especially in the presence of water or water vapor, as observed in the oral environment. Such phenomenon will eventually lead to strength degradation over time, decreasing the lifetime of dental prostheses. SCG occurs when water molecules approach a crack tip that is under stress, resulting in a chemical reaction between water and ceramic that breaks the metal oxide bonds with subsequent production of hydroxides. In this way, the crack will grow slowly until reaching the critical size for fracture (for a given applied stress), leading to catastrophic failure . The oral environment has many elements that favor SCG in ceramic restorations, such as water from saliva and from the dentin tubules, masticatory stresses, temperature and pH variations .
In addition to the probable aspects of failure, lifetime predictions indicating how long a restoration can serve its purpose reliably are of great importance. In order to obtain this information, SPT (strength–probability–time) diagrams must be obtained, since they characterize the time-dependent degradation of the material’s strength, combining Weibull and slow crack growth parameters. Unfortunately, lifetime predictions for dental ceramics are scarce in the dental literature .
The literature reports few studies that investigate the slow crack growth parameters of dental ceramics. The values of the slow crack growth susceptibility coefficient ( n ) determined for porcelains ranged from 15 to 38 ; for leucite- and lithium disilicate-based glass-ceramics, from 20 to 31 ; and for glass-infiltrated alumina composites, from 16.5 to 36.5 . Regarding the Weibull modulus (m), the literature reports m values for dental ceramics between 5 and 15 . In this study, the authors intend to present a detailed microstructural and slow crack growth characterization of widely used dental ceramic materials for prosthetic applications. These observations indicate that understanding the fracture behavior of dental ceramics and its relation to microstructural characteristics is important from a clinical point of view to assist the clinician in choosing the best ceramic material for each situation as well as predicting its clinical longevity. It also can be helpful in developing new materials for dental prostheses.
Since dental ceramics present different microstructures, depending on the presence and volume fraction of a crystalline phase, mean particle size and distribution throughout the glassy matrix; and microstructure strongly affects crack propagation and the mechanical properties , the objective of this study was to determine the slow crack growth parameters, Weibull parameters and build SPT diagrams for five dental ceramics, including two porcelains, two glass-ceramics and one glass-infiltrated alumina composite.
2
Materials and methods
The dental ceramics used in this study are described in Table 1 . Materials were selected in order to provide different microstructures, including porcelains, glass-ceramics and ceramic composites. Eighty disks (12 mm in diameter and 2 mm thick) of each material were produced according to each manufacturer instructions.
Material | Manufacturer/brand name | Poisson’s ratio | Crystalline content (%) | Mean particle size (μm) | Porosity (%) | Mean pore size (μm) |
---|---|---|---|---|---|---|
V | Vita Zahnfabrik/VM7 | 0.215 (0.006) c | – | – | 2.0 (0.2) b | 5.8 (4.2) a |
D | Ivoclar Vivadent/d.Sign | 0.217 (0.003) c | 16.2 (4.6) d | 0.7 (0.6) b | 2.7 (0.6) a | 5.9 (5.8) a |
E1 | Ivoclar Vivadent/IPS Empress | 0.210 (0.007) c | 29.4 (2.6) c | 1.1 (0.7) a | 0.7 (0.3) c | 4.4 (6.4) b |
E2 | Ivoclar Vivadent/IPS Empress 2 | 0.225 (0.012) b | 58.0 (1.0) b | Length: ∼10 Thickness: ∼1 * | 0.3 (0.1) c | 4.6 (3.5) b |
IC | Vita Zahnfabrik/In-Ceram Alumina | 0.239 (0.008) a | 65.4 (5.7) a | ∼1 to ∼20 ** | 2.9 (0.6) a | 2.0 (1.7) c |
* For the elongated lithium disilicate particles, 20 of these particles were measured in each micrograph for the determination of their mean length and thickness.
** Because of the variety of shape and size of alumina particles, mean values are not presented. This is an estimate of their size range by measuring some of the smaller and larger particles.
For porcelains V (VM7, Vita Zahnfabrik, Bad Sackingen, Germany) and D (d.Sign, Ivoclar Vivadent, Schaan, Liechtenstein), green specimens were prepared by applying the porcelain slurry to a stainless steel mold (condensation method) and sintered in a conventional dental porcelain furnace (Keramat I, Knebel, Porto Alegre, Brazil) following the firing schedules recommended by the manufacturers (peak sintering temperatures of 970 and 875 °C for porcelains V and D, respectively).
Glass-ceramics [IPS Empress (leucite-based glass-ceramic) and IPS Empress 2 (lithium disilicate glass-ceramic), both from Ivoclar Vivadent] were processed by the heat-pressing technique. Two wax disks (with specimen dimensions) attached to wax sprues were connected to a circular plastic base which was confined with a special paper forming a cylindrical mold. Empress refractory material was mixed with a special investment liquid and distilled water according to the manufacturer recommendation. The mixture was then poured into the mold and vibrated. After hardening of the refractory, the plastic base and molding paper were removed. The cylindrical refractory was then transferred to a furnace (Mastercasting, Dental Pioneria, São Paulo, Brazil) to burn out the wax, according to the lost wax technique. The glass-ceramic ingots were placed into a pressing furnace (EP 600, Ivoclar Vivadent) and heated to 1075 °C (for IPS Empress) or 920 °C (for IPS Empress 2). At these temperatures, the viscous glass-ceramic was pressed into a mold. After pressing and cooling to room temperature, divesting of the investment material and cleaning of the surface was performed by sandblasting.
The composite IC (InCeram Alumina, Vita Zahnfabrik) specimens were obtained by preparing an alumina powder slurry as recommended by the manufacturer and pouring it into a silicon mold mounted over special plaster which drained the water (slip casting technique). The slip cast disk was left to dry for at least 24 h and then sintered at 1120 °C for 2 h in an electric furnace (InCeramat II, Vita Zahnfabrik) to form a rigid porous pre-form (the shrinkage during the sintering was negligible). Then the alumina pre-form was infused with a lanthanum-silicate glass at 1110 °C for 6 h in the same electric furnace. After cooling, the excess glass over the infiltrated alumina-glass composite disk was removed by sandblasting.
All disks were machined to reduce thickness to 1.3 mm, following the guidelines in ASTM C 1161 . Then, one of the disk surfaces was mirror polished using a polishing machine (Ecomet 3, Buehler, Lake Bluff, IL, USA) with diamond suspensions (45, 15, 6 and 1 μm). The final dimensions of the disk samples were approximately Ø 12 mm × 1.1 mm. By this procedure, a full 200 μm of material was removed by polishing to eliminate any initial damage and preliminary grinding damage. Polishing was performed in order to create a flaw population similar to the one obtained in clinical procedures, such as glazing or fine polishing.
In the dynamic fatigue test, the specimens were fractured in biaxial flexure using a piston-on-3-balls fixture in a universal testing machine (MTS Syntech 5G, São Paulo, Brazil). The tests were conducted at five stress rates: 10 −2 , 10 −1 , 10 0 , 10 1 and 10 2 MPa/s. Ten specimens were tested at each stress rate, in accordance with ASTM C 1368-00 , except for the 1 MPa/s rate, where 30 specimens were tested for Weibull statistical analysis, in accordance to the proposed approach to construct stress–probability–time (SPT) diagram . The specimens were tested at constant temperature (37 °C) in a glass receptacle containing artificial saliva with the following composition: 100 mL of KH 2 PO 4 (2.5 mM); 100 mL of Na 2 HPO 4 (2.4 mM); 100 mL of KHCO 3 (1.5 mM); 100 mL of NaCl (1.0 mM); 100 mL of MgCl 2 (0.15 mM); 100 mL of CaCl 2 (1.5 mM); and 6 mL of citric acid (0.002 mM) . Also, 10 disks were tested in the inert condition, with a high stress rate (10 2 MPa/s) and with the surface subjected to tensile stress coated with a layer of silicone oil to minimize the effects of environmentally assisted subcritical crack growth. Thus, the eighty specimens were distributed as follows: 10 for each stress rate (10 −2 , 10 −1 , 10 1 , 10 2 MPa/s), 10 for inert strength (10 2 MPa/s, silicon oil) and 30 for 10 0 MPa/s.
The fracture stress ( σ f ) for the disk central region under the central loading piston was calculated according to the following formula (ASTM F 394-78) :
σ f = − 0.2387 F ( X − Y ) w 2
where F is the fracture load, w is the specimen thickness and X and Y were determined as follows:
X = ( 1 + υ ) ln B C 2 + ( 1 − υ ) 2 B C 2
Y = ( 1 + υ ) 1 + ln A C 2 + ( 1 − υ ) A C 2
where υ is Poisson’s ratio, A is the radius of the support circle (4 mm), B is the radius of the tip of the piston (0.85 mm), and C is the radius of the specimen (∼6 mm). The piston had a total length of 250 mm and a radius of 3.5 mm, except at the reduced tip section (length of 10 mm), and the steel balls had radius of 0.8 mm. The design of the piston-on-3-ball fixture was based on the one proposed by Wachtman et al. . Poisson’s ratio was determined for each material using the pulse-echo method . The specimen size outside the support circle (overhanging material) affects the stress distribution during loading, and tests performed with a large overhang may result in substantially different measured strengths than tests performed with a much smaller overhang . In this work, the ratio of radii C / A was ∼1.5, a value slightly higher than that indicated in ASTM F 394-78 ( C / A = 1.25). The fracture stress was also calculated using an alternative expression derived by taking into account the overhanging material , and the results using this formula were almost identical to those using Eq. (1) , showing that the larger overhanging material adopted in this work did not significantly affect the fracture stress.
At the lower stress rate, 10 −2 MPa/s, due to the length of time required for the test, a pre-load was applied with approximately 50% of the fracture load. This pre-load value was calculated based on regression analysis using the results obtained from the other four stress rates. ASTM C 1368-00 indicates that a pre-load up to 80% of the fracture load has little effect on the results of dynamic fatigue testing, since the significant crack growth only occurs at load values close to the fracture.
Fatigue parameters ( n and σ f 0 ) and their standard deviations were calculated according to the equations presented in ASTM C 1368-00 , which are based on the following:
log σ f = 1 n + 1 log σ ˙ + log σ f 0
where σ f is the flexural strength (MPa), <SPAN role=presentation tabIndex=0 id=MathJax-Element-5-Frame class=MathJax style="POSITION: relative" data-mathml='σ˙’>σ˙σ˙
σ ˙
is the stress rate (MPa/s), n the slow crack growth susceptibility coefficient and σ f 0 is a scaling parameter. One assumption used in the traditional dynamic fatigue equations is that stresses are constant in the test piece. Provided that flaws are small, this assumption is upheld for most cases with four-point loaded bend bars that break in the middle inner span section and with the disk specimens that broke in the middle loaded region as used in this study.
For the 30 specimens tested at 1 MPa/s in artificial saliva at 37 °C, the Weibull parameters m (Weibull modulus) and σ 0 (characteristic strength) were calculated, based on the following equation :
P f = 1 − exp − σ σ 0 m
where P f is the characteristic strength at fracture probability of 63.2%. The Weibull parameters were calculated based on the maximum likelihood method, according to ASTM C 1239 .
The introduction of the Weibull statistics and the time dependency of strength makes it possible to build SPT (strength–probability–time) diagrams, where the time to failure under constant stress for different failure probability levels can be estimated using the results obtained in the dynamic fatigue test, according to the theory proposed by Davidge et al. .
For each of the materials tested, the macroscopic fracture patterns of specimens broken in biaxial flexure test, and the number of broken pieces of all specimens at each test condition was inspected with the naked eye. Fracture surfaces of selected specimens (including all stress rates, n = 20) were examined using optical microscopy (OM) and scanning electron microscopy (SEM) to investigate the fracture origin. The critical flaws were identified and their size was determined. Critical crack size ( c ) was calculated as follows:
c = ( a b ) 1 / 2
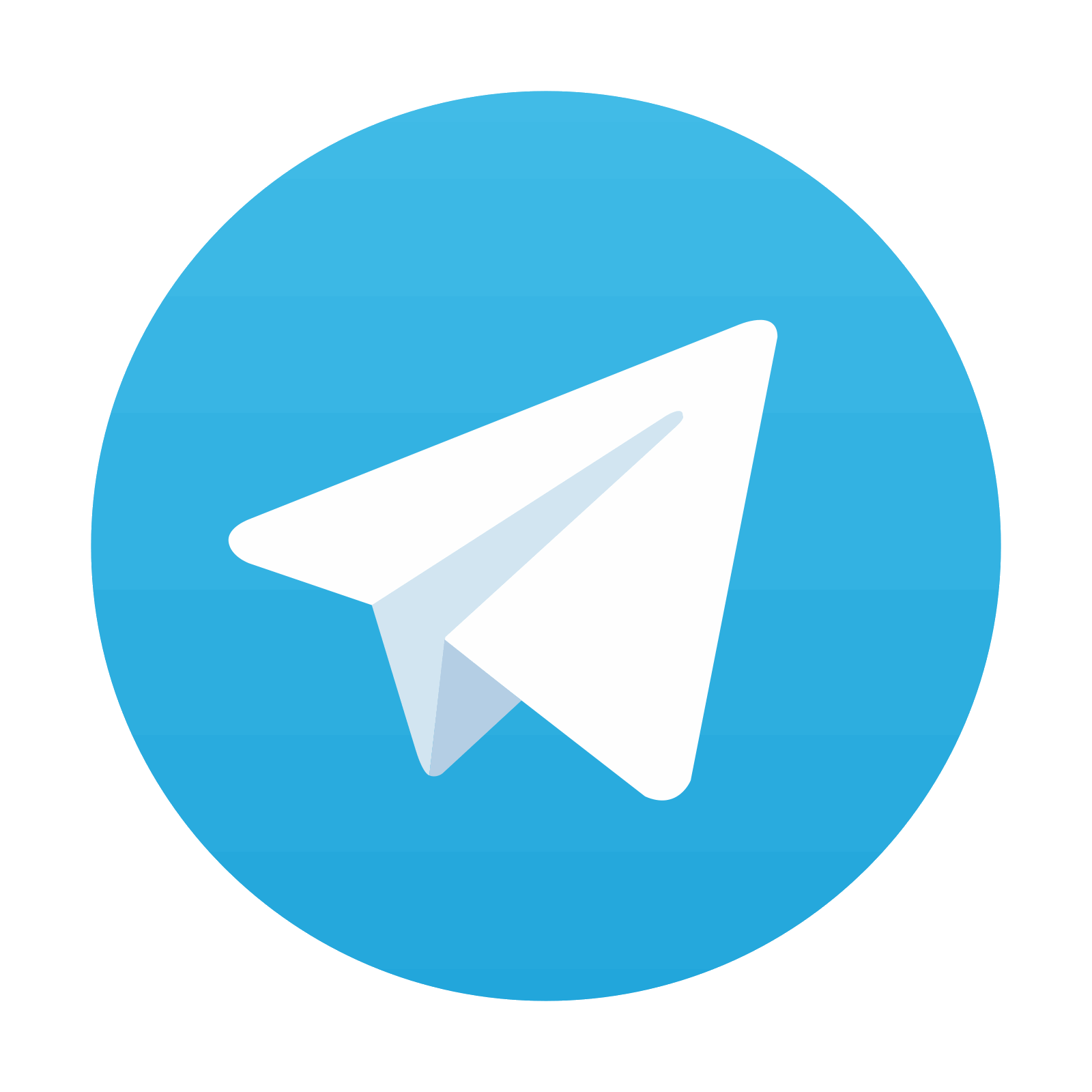
Stay updated, free dental videos. Join our Telegram channel

VIDEdental - Online dental courses
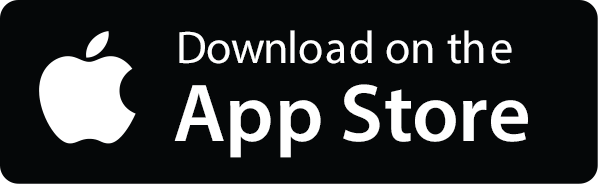
