Abstract
Objective
The aim of this study is to explain the influence of peripheral interface stress singularities on the testing of tensile bond strength. The relationships between these theoretically predicted singularities and the effect of specimen size on the measured bond strength are evaluated.
Methods
Finite element method (FEM) and boundary element method (BEM) analyses of microtensile bond strength test specimens were performed and the presence of localized high stress concentrations and singularities was analyzed. The specimen size effect predicted by the models was compared to previously published experimental data.
Results
FEM analysis of single-material trimmed hour-glass versus cast cylindrical specimens showed different theoretical stress distributions, with the dumbbell or cylindrical specimens showing a more homogeneous distribution of the stress on the critical symmetry plane. For multi-material specimens, mathematical singularities at the free edge of the bonded interface posed a computational challenge that resulted in mesh-dependence in the standard FEM analysis. A specialized weighted-traction BEM analysis, designed to eliminate mesh-dependence by capturing the effect of the singularity, predicted a specimen size effect that corresponds to that published previously in the literature.
Significance
The results presented here further support the attention to specimen dimensions that has already broadened the empirical use of the microtensile test methods. FEM and BEM analyses that identify stress concentrations and especially marginal stress singularities must be accounted for in reliable bonding strength assessments. Size-dependent strength variations generally attributed to the effects of flaw distributions throughout the interfacial region are not as relevant as the presence of singularities at bonded joint boundaries – as revealed by both FEM and BEM analyses, when interpreted from a generalized fracture mechanics perspective. Furthermore, this size-dependence must be considered when evaluating or designing dental adhesive systems.
1
Introduction
Bonding of dental restorations to tooth structure was one of the major advances in dentistry during the past century. Since the first dental adhesive systems were developed, numerous modifications have been performed to enhance their bonding ability and increase longevity of the restorations. Along with these bonding agents, test methods have been developed to determine the efficacy of the bonded interface under in vitro conditions.
The most widely used methods to test bond strength to dental substrata are the tensile bond strength test (TBS) and the shear bond strength test (SBS) . Different versions of these two methods exist regarding the size and shape of the specimens. For example, TBS is also known as microtensile bond strength test (μTBS) when the bonded area is below 1 mm 2 . A similar differentiation exists for the SBS test versus the microshear bond strength test (μSBS). On the other hand, the TBS test can be performed using different processes to prepare the samples, which result in different shapes of the final tested specimens. The ‘stick’, ‘dumbbell’, and ‘hourglass’ shapes are the most popular in the literature .
Due to the different procedures used in the in vitro bond strength tests, results obtained in different studies can differ largely and the same materials are ranked differently by μTBS and μSBS . Being able to reproduce the results obtained in a laboratory setting is key in order to determine objectively the properties of the materials and their behavior after the bonding process. Without an agreement among the test results, trying to establish a relationship between the laboratory data and the clinical outcomes becomes meaningless.
In 1994, the first ISO document describing a standardized process to test adhesion to dental tissues was released as ISO/TR 11405 – Dental Materials – Guidance on testing of adhesion to tooth structure. This document was updated in 2003 as the ISO/TS 11405 – Dental Materials – Testing of adhesion to tooth structure. Despite the details described in the ISO document regarding the sample preparation, some parameters such as the bonding area are not clearly defined. The large variability of the bond strength test results has been pointed out in several reviews and some authors even question that any clinically relevant data can be obtained from such tests . The lack of reproducibility of some methods and the high cost and complexity level of others seem to prevent any practical solution from arising .
In an attempt to discern the mechanical factors contributing to the scattering of the results in the in vitro setting, finite element methods (FEMs) have been used in the dental field since the 1970s . These models allow estimation of the stress distribution on the bonded surface under an applied load.
The present paper focuses on the evaluation of stress concentration and generalized stress intensity factors that have been overlooked in the past and should be considered to understand better the results of the TBS and μTBS tests.
Models of bonded joints present several challenges. In the theoretical stress evaluation, singularities occur at the borders of the specimen due to the shape of the bonded surface and the different stiffness of the materials. A singularity is a mathematical effect caused by the geometry of the specimen and the mismatch in elastic material properties. Discontinuities such as re-entrant corners, cracks, and/or the interface between two dissimilar materials can lead to singularities. When modeled using standard FEM formulations, the stress solutions become mesh dependent, with localized stresses diverging to infinity as the mesh is refined by using smaller finite elements. In fact, when the most frequently used linear elastic models are selected, the mentioned geometric discontinuities almost invariably produce singularities. Specifically, when modeling a bonded interface between dentin and a composite resin, a singularity will appear due to the inherent difficulty to maintain continuity of displacements and tractions across the interface. One can consider the effect of the singularity as a finite force applied on a very small area (the edge of the bonded surface in the case of a bonded joint), leading to increasingly high stress values because, mathematically, the calculated maximum stress at the point where the force is concentrated tends to infinity.
In a series of papers, Reedy and Guess conducted experiments and developed novel approaches to characterize the mechanical tensile strength of metal–epoxy butt joints . Although materials and sample sizes in their work are very different from those in the TBS and μTBS specimens, the mechanics is quite similar and many of the ideas on generalized fracture mechanics, size-dependent strength and the corresponding extensions of FEM originating from Reedy and Guess can be applied to the dental adhesive problem. Other relevant literature includes the theoretical work on stress singularities by Williams , Bogy , Carpinteri and Dunn et al. . In fact, here we will adopt several of these conceptual developments, but will use a different analysis approach.
As an alternative to energy based approaches, such as finite element methods, one can develop integral equations to solve linear elastic boundary value problems, including those involving bonded interfaces between two materials. In simple terms, starting from a basic reciprocal theorem, the displacement at any point in an elastic body can be written in terms of the displacements and tractions everywhere on the boundary. This traditional boundary integral formulation uses knowledge of the elastostatic fundamental representation of the displacement at any point in an elastic body (of infinite extent) due to a point force applied at the origin, as summarized in the beginning of Appendix 1 .
Standard BEM formulations also suffer from mesh dependence when applied to problems with stress singularities. However, several different approaches exist to address problems with cracks in homogeneous specimens. The most popular uses quarter point and traction singular elements . For mechanical problems involving bonded joints of dental materials, more general singularities must be considered, including those associated with bi-material free edges and cracks .
Here we show that weighted-traction boundary element models (BEM) provide accurate, mesh-independent results for bonded joints, and recommend these approaches be used in studies of bonded dental materials. The presence of singularities does not impact weighted traction BEM as much as conventional BEM or FEM, so a better representation of the characteristics of the bonded interface can be obtained by treating the mathematical complexities of infinite stresses analytically, rather than numerically. The weighted traction BEM is described in further detail in Appendix 1 . A more complete treatment of singularities, material failure characteristics and size-dependent strength is provided in Appendix 2 , where the limitations of all linear elastic theories also are discussed, along with further details on the bi-material interface work by Reedy and Guess .
In the present work, the weighted traction boundary element formulation developed by Dargush and Hadjesfandiari is adopted in order to compute the generalized stress intensity factors K g . The main goal of the present work is to evaluate the influence of singularities in TBS specimens and their effects on the outcomes from standard FEM and weighted traction BEM for predicting dental adhesive system failures.
We should emphasize that finite element methods also can be extended to address such singular problems . However, in the present work, only standard FEM approaches are employed. This is done to illustrate the mesh dependence that one should expect when modeling problems with stress singularities using standard FEM, an approach that has dominated the dental adhesive literature. As we will show, this mesh sensitivity must be considered carefully, if any meaningful conclusions are to be reached from standard FEM analyses of the dental adhesive problem.
2
Materials and methods
Fig. 1 shows a representation of the basic bonded dental joint considered here, along with the elastic modulus and Poisson’s ratio values used for each of the materials involved. Additional models were also created to study the behavior of the stresses and the singularities in different situations as described below.

As a first example, the effects of the geometry on the stresses imposed by a tensile load on hourglass and dumbbell specimens were analyzed using FEM. Two FEM models were created using typical TBS specimen shapes and dimensions, but eliminating the adhesive layer and replacing the dentin–adhesive interface by a symmetry plane. The elastic modulus and Poisson’s ratio of dentin, as defined in Fig. 1 , were used for these models. The geometries and meshes for these two models are shown in Fig. 2 .
Although the test specimens are axisymmetric, we chose to use fully three dimensional models, primarily for display purposes. Both models were created in ANSYS Meshing, v14 using hexahedral elements. The elements chosen were twenty node isoparametric elements with three degrees of freedom at each node and the finite element equations were developed assuming linear elastic material behavior. A uniaxial tensile load was applied to the left end of each specimen in the normal direction to produce a nominal stress of 20 MPa on the minimum cross-section. On the symmetry plane, at the right end in Fig. 2 , a frictionless support boundary condition was imposed in order to constrain the axial displacement while allowing free transverse displacements. The finite element equations for the two models were solved in double precision using ANSYS Mechanical, v14. We should note that in Van Noort et al. , a similar investigation comparing hourglass and dumbbell specimens has been conducted.
Next, the problem of a bonded interface was studied using an FEM cylindrical model, such as the one shown in Fig. 3 .In constructing the corresponding finite element mesh, the smallest elements were located inside the adhesive layer at the specimen surface, as depicted in Fig. 3 , where the geometry and mesh are shown. The mesh spacing for the model in the figure was set at 0.01 mm in both the axial and radial directions. A tensile load equivalent to 20 MPa for the nominal interface normal stress was applied to the specimen and the finite element equations were solved in double precision using ANSYS Mechanical, v14.
To characterize the impact of the singularities on the stress distribution, the mesh was refined in four steps. In the first case, the axial and radial mesh spacing of the elements surrounding the singularity was set at 0.02 mm. In the three subsequent cases, the mesh size in this critical region wasreduced to 0.01, 0.005, and 0.002 mm, respectively. For each case, the same loading conditions were applied and the FEM equations were solved.
The problem geometry, material properties and loading conditions for the BEM analyses were as defined in Fig. 1 . In order to characterize the system more completely using BEM, two different approaches were adopted for the weighted traction boundary element analysis; the first with fully bonded interfaces and the second with a small crack on one of the interfaces at the free edge. In both cases, an axisymmetric formulation was used to model the problem allowed by the purely cylindrical geometries of the dentin and resin components, the bonding adhesive layer and uniaxial loading. The surfaces of the dentin and resin domains were modeled with 88 quadratic boundary elements, whereas 72 quadratic elements were used to represent the response of the adhesive. This boundary element mesh was graded such that very small elements of approximate length 0.0025 mm were used near the intersection of the interfaces and the free edge, where the stress singularities occur.
Weighted traction boundary element solutions were obtained for 0.5, 0.6, 0.7, 0.8, 0.9, 1.0, and 1.1 mm specimen radii and adhesive thicknesses of 0.025, 0.050, and 0.100 mm in order to investigate the size dependence of the response. The results were compared with previously published experimental data .
With current understanding, one cannot predict the critical value of weighted traction from first principles, although promising damage mechanics based approaches do exist for certain material systems . Instead, here the critical values of the weighted traction are estimated from physical testing. From a theoretical standpoint, this is equivalent to selecting a nominal tensile strength at any one particular specimen size. Based upon the failure data from Phrukkanon et al. , the nominal tensile strength for a specimen with 0.6 mm radius is estimated to be 19 MPa, which incidentally is quite close to the nominal value of 20 MPa assumed for all standard FEM analyses performed here. By using the estimated strength at this one particular radius, the size dependency of the tensile strength predicted by the weighted traction BEM models was computed and then compared with all of the experimental strength values presented in Phrukkanon et al. .
The size dependence of the tensile strength was also investigated by introducing a small crack near the outer surface of one of the cylinders on the interface. The same cases described above were analyzed for a crack location on the dentin–adhesive interface and, separately, on the resin–adhesive interface. A baseline crack length of 5 μm was selected to study the scaling behavior of this overall dental adhesive system and the sensitivity of the results to that particular crack length also was investigated.
To summarize our approach, we first apply standard FEM to monolithic specimens and study the resulting stress concentrations under uniaxial tensile loading. Next, we use standard FEM for adhesively bonded specimens and investigate mesh dependence due to the presence of stress singularities on the free edge of the interfaces. Then, we apply a weighted traction BEM to these interface problems, assuming perfect bonding, in an effort to obtain mesh independent solutions that could be useful in determining size-dependent strength of the specimens. Finally, we introduce small interface edge cracks and again apply the weighted traction BEM to study the influence of specimen size on strength. For all of the bonded dental specimens, a specific geometric configuration is considered, which permits comparison with previously published experimental data.
2
Materials and methods
Fig. 1 shows a representation of the basic bonded dental joint considered here, along with the elastic modulus and Poisson’s ratio values used for each of the materials involved. Additional models were also created to study the behavior of the stresses and the singularities in different situations as described below.
As a first example, the effects of the geometry on the stresses imposed by a tensile load on hourglass and dumbbell specimens were analyzed using FEM. Two FEM models were created using typical TBS specimen shapes and dimensions, but eliminating the adhesive layer and replacing the dentin–adhesive interface by a symmetry plane. The elastic modulus and Poisson’s ratio of dentin, as defined in Fig. 1 , were used for these models. The geometries and meshes for these two models are shown in Fig. 2 .
Although the test specimens are axisymmetric, we chose to use fully three dimensional models, primarily for display purposes. Both models were created in ANSYS Meshing, v14 using hexahedral elements. The elements chosen were twenty node isoparametric elements with three degrees of freedom at each node and the finite element equations were developed assuming linear elastic material behavior. A uniaxial tensile load was applied to the left end of each specimen in the normal direction to produce a nominal stress of 20 MPa on the minimum cross-section. On the symmetry plane, at the right end in Fig. 2 , a frictionless support boundary condition was imposed in order to constrain the axial displacement while allowing free transverse displacements. The finite element equations for the two models were solved in double precision using ANSYS Mechanical, v14. We should note that in Van Noort et al. , a similar investigation comparing hourglass and dumbbell specimens has been conducted.
Next, the problem of a bonded interface was studied using an FEM cylindrical model, such as the one shown in Fig. 3 .In constructing the corresponding finite element mesh, the smallest elements were located inside the adhesive layer at the specimen surface, as depicted in Fig. 3 , where the geometry and mesh are shown. The mesh spacing for the model in the figure was set at 0.01 mm in both the axial and radial directions. A tensile load equivalent to 20 MPa for the nominal interface normal stress was applied to the specimen and the finite element equations were solved in double precision using ANSYS Mechanical, v14.
To characterize the impact of the singularities on the stress distribution, the mesh was refined in four steps. In the first case, the axial and radial mesh spacing of the elements surrounding the singularity was set at 0.02 mm. In the three subsequent cases, the mesh size in this critical region wasreduced to 0.01, 0.005, and 0.002 mm, respectively. For each case, the same loading conditions were applied and the FEM equations were solved.
The problem geometry, material properties and loading conditions for the BEM analyses were as defined in Fig. 1 . In order to characterize the system more completely using BEM, two different approaches were adopted for the weighted traction boundary element analysis; the first with fully bonded interfaces and the second with a small crack on one of the interfaces at the free edge. In both cases, an axisymmetric formulation was used to model the problem allowed by the purely cylindrical geometries of the dentin and resin components, the bonding adhesive layer and uniaxial loading. The surfaces of the dentin and resin domains were modeled with 88 quadratic boundary elements, whereas 72 quadratic elements were used to represent the response of the adhesive. This boundary element mesh was graded such that very small elements of approximate length 0.0025 mm were used near the intersection of the interfaces and the free edge, where the stress singularities occur.
Weighted traction boundary element solutions were obtained for 0.5, 0.6, 0.7, 0.8, 0.9, 1.0, and 1.1 mm specimen radii and adhesive thicknesses of 0.025, 0.050, and 0.100 mm in order to investigate the size dependence of the response. The results were compared with previously published experimental data .
With current understanding, one cannot predict the critical value of weighted traction from first principles, although promising damage mechanics based approaches do exist for certain material systems . Instead, here the critical values of the weighted traction are estimated from physical testing. From a theoretical standpoint, this is equivalent to selecting a nominal tensile strength at any one particular specimen size. Based upon the failure data from Phrukkanon et al. , the nominal tensile strength for a specimen with 0.6 mm radius is estimated to be 19 MPa, which incidentally is quite close to the nominal value of 20 MPa assumed for all standard FEM analyses performed here. By using the estimated strength at this one particular radius, the size dependency of the tensile strength predicted by the weighted traction BEM models was computed and then compared with all of the experimental strength values presented in Phrukkanon et al. .
The size dependence of the tensile strength was also investigated by introducing a small crack near the outer surface of one of the cylinders on the interface. The same cases described above were analyzed for a crack location on the dentin–adhesive interface and, separately, on the resin–adhesive interface. A baseline crack length of 5 μm was selected to study the scaling behavior of this overall dental adhesive system and the sensitivity of the results to that particular crack length also was investigated.
To summarize our approach, we first apply standard FEM to monolithic specimens and study the resulting stress concentrations under uniaxial tensile loading. Next, we use standard FEM for adhesively bonded specimens and investigate mesh dependence due to the presence of stress singularities on the free edge of the interfaces. Then, we apply a weighted traction BEM to these interface problems, assuming perfect bonding, in an effort to obtain mesh independent solutions that could be useful in determining size-dependent strength of the specimens. Finally, we introduce small interface edge cracks and again apply the weighted traction BEM to study the influence of specimen size on strength. For all of the bonded dental specimens, a specific geometric configuration is considered, which permits comparison with previously published experimental data.
3
Results
The axial stress contours on a longitudinal cutting plane and the right symmetry plane of the models of the monolithic dentin specimens are shown in Fig. 4 . These plots show that the axial stress on the right symmetry plane is not uniform for the hourglass model while it is uniform for the dumbbell model, achieving the nominal stress of 20 MPa.
Fig. 5 shows the axial stress for both specimens on the right symmetry plane along a radial line extending from the model center to its circumference. Clearly, the dumbbell-shaped specimen provides a uniform axial stress distribution on the entire symmetry plane, while the hourglass specimen does not. Consequently, dumbbell-shaped specimens are preferred for meaningful dental testing protocols. For these two problems, standard FEM approaches provide accurate stress distributions, which converge with mesh refinement because no singularities are present.
Next, we consider the bonded dentin–adhesive–resin specimen of Fig. 1 . The axial stress distribution on an axial cutting plane through a cylindrical specimen diameter is illustrated in the contour plot from standard ANSYS FEM analysis in Fig. 6 . This figure shows that the presence of the singularities produces a completely different stress distribution at the adhesive interfaces than the homogeneous dumbbell-shaped model. We also observe that the surface profile of the specimen is distorted by a Poisson effect due to the large axial strains in the more flexible adhesive material.
A highly zoomed view of the FEM axial stress contours on the outer surface of the cylindrical specimen near the adhesive layer is provided in Fig. 7 . The surface mesh is superimposed on the contour plot to show the location of the singularities. The right singularity, shown in red, occurs at the resin composite–adhesive interface and the left singularity, shown in yellow, occurs at the dentin–adhesive interface. Also, the maximum axial stress from the FEM analysis for this baseline mesh is 30.63 MPa, which occurs at the resin composite interface.
Fig. 8 shows a highly magnified view of the axial stress distribution on a cross-sectional cutting plane through the resin composite singularity. This plot provides a view of the high radial gradient of the axial stress near the free edge interface singularity.
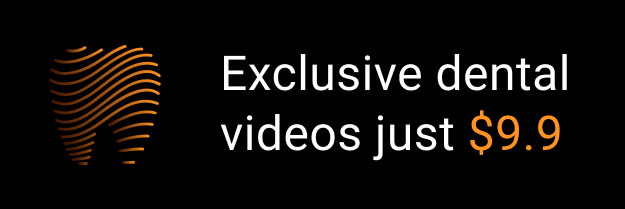