Highlights
- •
Different ratios of an organosilane were tested on nanofilled composites.
- •
Chemo-mechanical properties, hydrolytic stability and surface gloss were studied.
- •
Physical challenge was induced by toothbrushing simulation on the resins.
- •
Organosilane ratios modified the physicochemical properties of composites.
- •
At least 2 wt.% of the organosilane was required for the nanofilled composite.
Abstract
Objective
To determine the effect of organosilane content on the physicochemical properties of model composites formulated with nano-sized fillers.
Methods
Model composites were formulated with dimethacrylate-based monomers, a photoinitiator/co-initiator system and silicon dioxide nano-sized fillers treated with different amounts of 3-methacryloxypropyltrimethoxysilane (MPTS): 1.0 (G 1% ), 2.0 (G 2% ), 5.0 (G 5% ), 7.5 (G 7.5% ) and 10 (G 10% ) wt.% relative to SiO 2 . Non-silanized fillers (G 0% ) were used in the control group. Degree of conversion (DC) was assessed by Fourier-transformed infrared spectroscopy (ATR-FTIR). Knoop hardness (KHN) and elastic modulus were determined before and after water storage for 4 months. Water sorption (Wsp) and solubility (Wsl) were calculated by successive mass determinations in analytical balance. Surface gloss and roughness were characterized before and after toothbrushing simulation.
Results
With the exception of those fillers treated with 1% MPTS, DC was not dependent on the silane content. Within the silanized groups, G 1% showed the lowest initial and final KHN, without statistical difference from G 0% . The elastic modulus was not affected by the silane content, regardless of the storage condition, but those groups formulated with at least 5% silane presented improved values after storage. Silane content did not affect the WSl, but affected Wsp, in which those groups formulated with at least 2 wt.% of MPTS produced a more resistant material than G 0% . The use of treated particles with at least 2 wt.% of silane was able to produce materials that did not change their gloss after the brushing process. Additionally, these materials presented lower surface roughness than G 0% after the brushing process (p < 0.05).
Significance
The concentration of MPTS affected the physicochemical properties of nano-filled composites. Therefore, 2 wt.% of silane was the optimized quantity to produce materials resistant to degradation, both in bulk and surface properties.
1
Introduction
Restorative dental composites are prone to degradation due to exposure in the oral environment [ , ]. Physical and chemical factors such as water, acids, salivary enzymes, and bacterial metabolism products are involved in chemical degradation and could jeopardize the surface integrity of a composite restoration [ ]. In this context, properties such as hardness and surface texture may degrade [ , ], decreasing the wear resistance and long-term clinical performance of composite restorations [ ].
Solvent uptake and hydrolytic degradation are usual experiences for dental polymers, due to the release of unreacted reagents and degradation products [ ]. Individual variables such as the masticatory frequency and strength, occlusal contacts, and diet profile are also essential aspects related to materials’ resistance to chemical and mechanical degradation [ ]. Not only the intraoral factors but also the composite´s constituents and concentration have an important response against materials’ degradation [ , ].
Resin composites are basically formulated with inorganic fillers and an organic blend of monomers, and they are widely used as dental material [ ]. While the organic blend is responsible for the dental bonding ability and the possibility to manipulate the material at room temperature, inorganic fillers can modify aesthetics characteristics, increase mechanical properties, and according to the concentration, to improve the chemical stability [ ]. To effectively act, inorganic fillers should be bonded with the organic blend via the interconnection of a coupling agent [ ].
Organozirconate, 4-methacryloxyethyl trimellitic anhydride (4-META), organotitanate, and organosilanes are commonly used as coupling agents to coat the surface of inorganic fillers [ ]. Coupling agents work as a bridge, connecting both phases of composite resins via covalent bond [ , ]: the monomer blend and the inorganic fillers [ ]. Although these agents represent a low fraction within composites formulation, they have a significant effect on their properties [ ]. The coupling agents act in the stress transference from the polymer to the inorganic fillers, reinforcing the composite, and improving the filler distribution through the organic matrix [ ]. Besides enhancing properties such as the flexural strength, coupling agents reduce the hydrolytic degradation of composite resins [ ].
Organosilanes have been used in dentistry for more than fifty years [ ] to compose the interfacial segment between the continuous phase of monomers/oligomers and the dispersed phase of fillers [ ]. These molecules are organic silicon combinations with functional groups that impart their reaction with inorganic and organic structures [ ]. When the organic radical presents an active functional group, such as methacrylate, organosilanes are very useful in creating hybrid structures [ ]. 3-methacryloxypropyltrimethoxysilane (MPTS) has been extensively used in dental materials due to its efficiency and also due to its lower cost than other components (like organozirconates) [ ]. MPTS is a bifunctional molecule that is able to interact with itself, fillers, and monomers. It forms siloxane bonds (Si OS i) via reaction with oxides or hydroxyl groups on the particles’ surfaces [ , ] and carbon-carbon covalent bonds with the monomers [ ]. Commonly applied fillers such as silicon dioxide (SiO 2 ), silicate glasses, and quartz in micro and nanoscale size have been functionalized with MPTS [ ].
It was already demonstrated that the amount of coupling agent needed to coat the filler particles could affect dental composite’s behavior [ , , , ]. While the insufficient coverage leads to non-homogeneous dispersion within and bond to the polymer, the excess may also drawback the mechanical properties. To overcome these issues, studies have investigated the optimal amount of coupling agents on fillers silanization [ , ], but just a few with nano-sized fillers [ ], to which the amount of silane might significantly impact due to the increased surface area to volume ratio.
The use of nano-sized filler particles to resin composite formulations’ has increased in recent years. Therefore, it is mandatory to perform further investigations on this issue, especially over the surface properties, as they are related to materials aesthetics and biofilm formation over time. Due to the aforementioned facts, the present study aimed to determine:
- –
the effect of MPTS amount on the physicochemical properties of model composites formulated with nano-sized fillers – with possible effects on the degree of conversion, Knoop hardness and elastic modulus before and after storing in water, water sorption, water solubility, surface gloss and surface roughness before and after toothbrushing simulation; and
The research hypothesis tested was that:
- –
the use of different concentrations of MPTS affects dental composites’ properties.
2
Materials and methods
2.1
Filler silanization
Spherical silica (SiO) particles, with an average diameter of 40 nm, (Aerosil OX50, Evonik, Piscataway, NJ, USA) were silanized with organosilane 3-metacrilioxipropil trimetoxisilano (MPTS, Sigma-Aldrich, St. Louis, Missouri, USA). The silanization methodology was performed according to previous studies [ , , ]. The minimum amount of silane to cover the filler particles was calculated by using the following Eq. (1) :
X=Aωf
Where, A is the silica surface area (Aerosil OX50 = 50 m 2 /g); ω is the coverage surface area / 1 g of silane (MPTS = 2525 m 2 /g); f is the amount of silica in grams. According to this equation, to every 5.0 g of silica, 0.1 g of silane is necessary in order to achieve a uniform minimum coverage (only 2 wt.% of silane). Thus, the organosilane, for each experimental group, was added at 1.0, 2.0, 5.0, 7.5, and 10 wt.% relative to silica concentration.
The nanoparticles of silica, the organosilane MPTS, the solvent (cyclohexane, 100 mL) and n-propylamine (0.1 ± 0.01 g) were stirred at room temperature for 30 min, then for further 30 min at 60 ± 5 °C in a magnetic stirrer (Model Q261A11 – Quimis). The mixture was then placed on a rotary evaporator (Model G344B1 – Quimis) at 60 ± 5 °C in order to remove any solvent. The resulting powder was heated to 95 ± 5 °C for one hour on a rotary evaporator and then dried in the oven (Model 22-Q317 M – Quimis) at 50 °C for 48 h. The silanized fillers were carefully powdered by using a glass piston.
2.2
Energy-dispersive X-ray (EDS) analysis
Energy-dispersive X-Ray (EDS) analysis using an SEM (JSM-6510LV – Jeol) were used to identify the chemical content of inorganic filler surfaces after the silanization process. Approximately 10 mg of each filler silanized with different percentages 1.0, 2.0, 5.0, 7.5, and 10 wt.% relative to silica concentration were fixed with a double carbon tape in stubs and coated with carbon. An electron beam reached on the sample generating a small amount of X-rays, quantifying the elements present in each group.
2.3
Model composite formulation
The mixture 2,2 bis[4-2(2-hydroxy-3-methacryloxypropoxy)phenyl] propane (Bis-GMA): triethyleneglycol dimethacrylate (TEGDMA) (Esstech Inc.,Essington PA, USA) was used at ratio 50:50 wt.%. To this, 0.5% camphorquinone (ESSTECH Inc., Essington, PA, USA) and 1 mol% ethyl 4-dimethylaminobenzoate (EDMAB) (Sigma-Aldrich, Chemie, Steinheim, Germany) were added as photoinitiator/co-initiator system. The silanizated inorganic fillers with different amounts of organosilane (1.0, 2.0, 5.0, 7.5 and 10 wt.% relative to silica concentration) were added to the organic blend at 60 wt.% and the composites were hand-mixed. Groups were named according to the amount of organosilane used and being arranged as follows: G 0% , G 1% , G 2% , G 5% , G 7.5% and G 10% . Fig. 1 display components in the formulation of the nanostructured model composites.

All samples were photoactivated for 40 s with a light-curing unit (Radii Cal, SDI, Australia) with 1140 mW/cm 2 . The irradiance was constantly checked with a radiometer (LED Radiometer, Demetron SDS Kerr, Middleton, WI, USA), standardized at a distance of 0.5 mm between the photopolimerizer’s tip and the curing material. The same curing unit and conditions were used for all subsequent methodologies.
2.4
Degree of conversion
The degree of conversion (DC) was determined by Fourier Transform Infrared Spectroscopy (FTIR, Prestige 21 Shimadzu, Kyoto, Japan) using the technique with the attenuated total reflectance (ATR) device. Increments of the composite resins were placed on the diamond crystal on the ATR, and the spectra were obtained with 32 scans and 4 cm −1 resolution. After that, the increments were photoactivated on the ATR. The peaks of 1608 cm −1 and 1638 cm −1 were used corresponding to carbon-carbon double bonds in the aliphatic chain and the aromatic chain, respectively. The DC of each composite resin was calculated (Eq. (2)) by using the bands’ area of both signs of the polymerized and unpolymerized resins [ ].
DC=100×Abs1638cm−1cured/Abs1608cm−1curedAbs1638cm−1uncured/Abs1608cm−1uncured
2.5
Knoop hardness
Resin composites were placed on metallic molds and covered with a polyester strip before the photoactivation. Five discs per group were prepared (Ø 4 mm × 2 mm h). After 24 h, stored in a dark and dry environment, the irradiated surfaces were indented using 25 N of load for 15 s with a Knoop diamond tip at five different locations (Micromet 5104, Buehler, Lake Bluff IL, USA). After initial measurements, samples were stored in distilled water, and Knoop hardness measurements were repeated after 4 months.
2.6
Elastic modulus
Twenty bar-shaped samples were prepared in a metallic mold (with 1 mm thickness, 2 mm wide, 10 mm length dimensions) for each material. Composites were placed in a single increment. Each uncured sample had its top and bottom covered by polystyrene strips before the photoactivation. The surfaces were then grounded to remove irregularities with 600-grit SiC paper. Ten samples per group were stored in distilled water at 37 °C. After 24 h, samples were measured with a digital caliper and submitted to the flexural strength test using a three-point bend method in a universal testing machine (DL2000, EMIC, São José dos Pinhais, PR, Brazil) with 5 kgf load cell and displacement of 0.5 mm/min.The elastic modulus (EM) was obtained from the stress-strain curve in the elastic regime of materials behavior and from the final load applied for material rupture using the following Eq. (3) :
E=l3F4wh3d
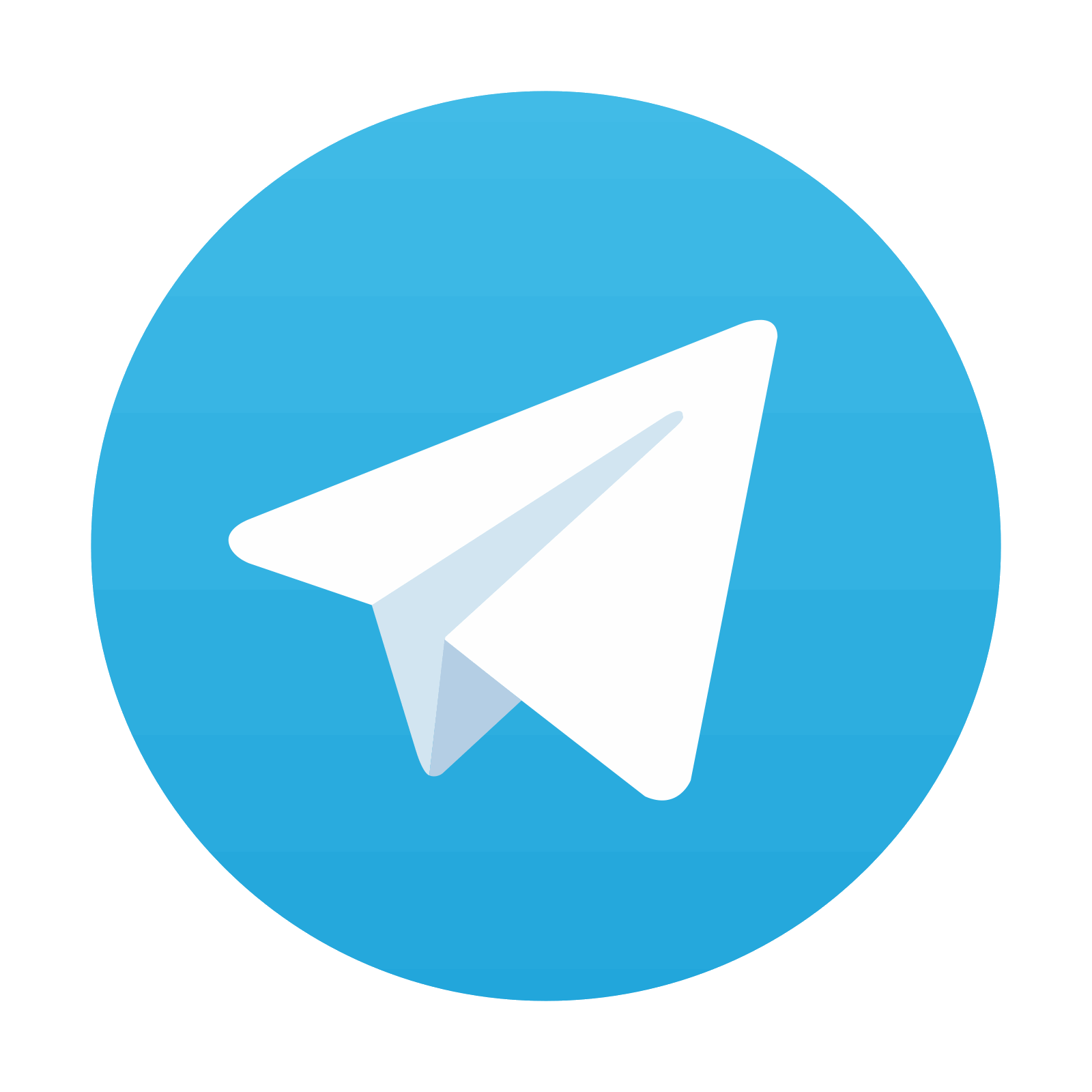
Stay updated, free dental videos. Join our Telegram channel

VIDEdental - Online dental courses
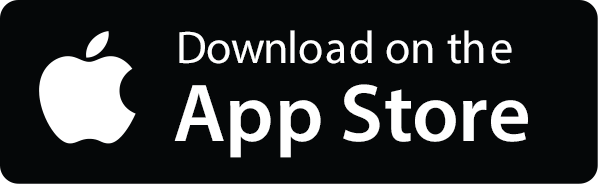

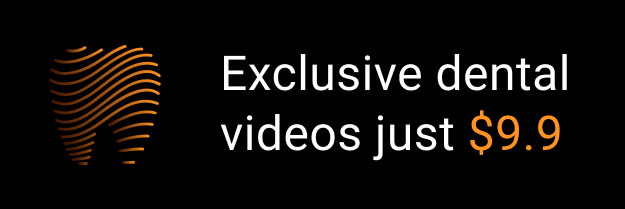