14
Restoring Dental Implants
Computer‐aided design/computer‐aided manufacturing (CAD‐CAM) technology was originally developed and commercialized for industrial manufacturing but is of growing importance within dentistry. In fact, it has virtually revolutionized the fabrication of crowns and bridgework and has become the preferred method of making crowns and fixed partial dentures. In contrast to conventional dentistry, with an in‐house CAD/CAM system, the dentist typically can fabricate and lute a prosthesis the same day.
Continuing developments in computer‐based dental technologies have provided the dental profession with new opportunities for improved clinical workflow and, as indicated above, facilitated manufacturing of dental restorations. Over the last decade or so, CAD/CAM of dental restorations became an established fabrication process, especially for all‐ceramic restorations. With the more recent introduction of intraoral scanning systems, digital techniques are now capable of replacing conventional treatment workflow. Numerous clinical trials have demonstrated that single‐tooth restorations fabricated in a completely digitized workflow have a clinical fit that is equal to, or better than, conventionally fabricated restorations. Further, when compared with conventional impressions, digital impressions can be more time‐efficient and improve the treatment comfort for patients, and clinicians.
In addition to ongoing improvements in digital technologies, new restorative materials that are optimized for CAD/CAM processing have led to further advances and optimization of digital workflows. Biomaterials research in recent years has focused on the development of materials that offer a combination of adequate translucency, improved mechanical strength, and optimized timesaving machining.
CAD/CAM Dentistry
Although most dentists may be familiar to some degree with CAD/CAM dentistry, a brief discussion might be useful here. This is because the predominant trend in dental implantology is to take maximum advantage of digital technology in almost every aspect of the process other than the physical surgical implant placement.
There are numerous systems for digital restoration processing and although specific details vary with each system, all rely upon comparable basics underlying their operation and all CAD/CAM systems contain three components:
- Digital scanner or imaging system
- Software to process the scanned image into data that allows fabrication of the prosthesis
- Hardware that fabricates the prosthesis from the data.
The overall process starts from a three‐dimensional (3D) image used by computer software to design the restoration. Imaging systems can now record images of the adjacent and opposing dentition as well as bite registration data. After the information is uploaded into the computer, a data file is assembled which, together with the computer’s internal library of tooth shapes, is used to design the restoration.
After the implant and the healing cap are placed and the operative area has healed to the point that there is adequate osseointegration of the implant body, an image or scan is taken of the implant (or implants) and the adjacent/abutment teeth utilizing an intra‐oral scanner (Fig. 14.1). Some clinicians, however, will scan the operative area at the time of implant placement to allow for restorative planning.
This image or digital impression is digitized by the recording software in the scanner and the data fed into a computer. Proprietary software then creates a virtual restoration, i.e., a prosthesis that replaces the missing dentition (Fig. 14.2). In technological terms, this process is termed reverse engineering and constitutes the CAD part of the overall operation. The software transmits this virtual data to a milling machine where the prosthesis is machined out of a solid (monolithic) block of ceramic or composite resin (Fig. 14.3). The latter process is the CAM part of the operation. Stains and glazes can be fired onto the surfaces of the milled ceramic crown or bridge to correct the otherwise monochromatic appearance of the restoration, Figure 14.4. The restoration is then adjusted in the patient’s mouth and cemented or screwed in place.

Figure 14.1 Intra‐oral scanner.

Figure 14.2 A digital image of a scanned cast.

Figure 14.3 A completed CAD/CAM fabricated restoration.
The CAD/CAM systems can either be used chair‐side with the restoration fabricating hardware in an adjoining laboratory or the digital data is fed to a remote production center.
Typically, CAD/CAM dental restorations for implants are milled from solid (monolithic) blocks of ceramic or composite resin closely matching the basic shade of the restored tooth or adjacent teeth. Metal alloys may also be milled or digitally produced, often for the posterior teeth in patients with heavy bites and/or bruxers. The choice of restorative material is discussed below.

Figure 14.4 Finishing and characterization of a CAD‐CAM ceramic restoration
(Source: Courtesy of Sirona Dental Inc., Charlotte, NC).
It should be mentioned that additive manufacturing (once known as rapid prototyping) has now entered CAD/CAM dentistry. At first, additive manufacturing, also known as 3D printing, was almost an experimental laboratory approach to fabricating dental restorations but now there is increasing interest in the scope of its applicability in dentistry. The underlying concept of additive manufacturing is in complete contrast to the subtractive manufacturing process of milling the object (prosthesis) from a solid block.
The term 3D printing is commonly applied to all types of additive manufacturing, but this term should refer only to fabricating objects through the deposition of a material using printer technology such as a printer head or precision spray nozzle. In fact, “additive manufacturing” strictly refers to the construction of objects from 3D data, usually layer‐by‐layer until fabrication is complete. The three most common additive manufacturing methods are Selective Laser Sintering (SLS), Direct Metal Laser Sintering (DMLS) and Selective Laser Melting (SLM). SLS and DMLS are basically the same process in that the applied laser beam coalesces the particles in the deposited material through partial fusion but without achieving a full melt. When this sintering methodology is used for non‐metallic materials, it is commonly referred to as SLS whereas DMLS is the term used for processing metallic particles. In contrast, with SLM technology, the metal particles are fully melted and then cooled to consolidate the constructed object. Although the two processes are somewhat similar, the major difference is that with SLM, the processed objects do not have the porosity found with DMLS because the complete melting/cooling cycle of the deposited particles ensures greater solidity and density of the fabricated object.
Advantages and Drawbacks of CAD/CAM Technology
Many commercial CAD/CAM systems are available, including the CEREC (CERamic REConstruction), Planmeca, E4D, 3Shape Dental and Cera systems. Examples of chair‐side and laboratory CAD‐CAM systems are shown in Figs. 14.5 and 14.6. In addition to the increasing variety of CAD/CAM systems available, continuing technological advances include increasingly versatile software, direct digital recording of the dentition and CAM units with greater speed and accuracy in milling operations.

Figure 14.5 A CAD CAM chairside system
(Source: Courtesy of E4D).

Figure 14.6 A CAD‐CAM laboratory system
(Source: Courtesy of Planmeca).
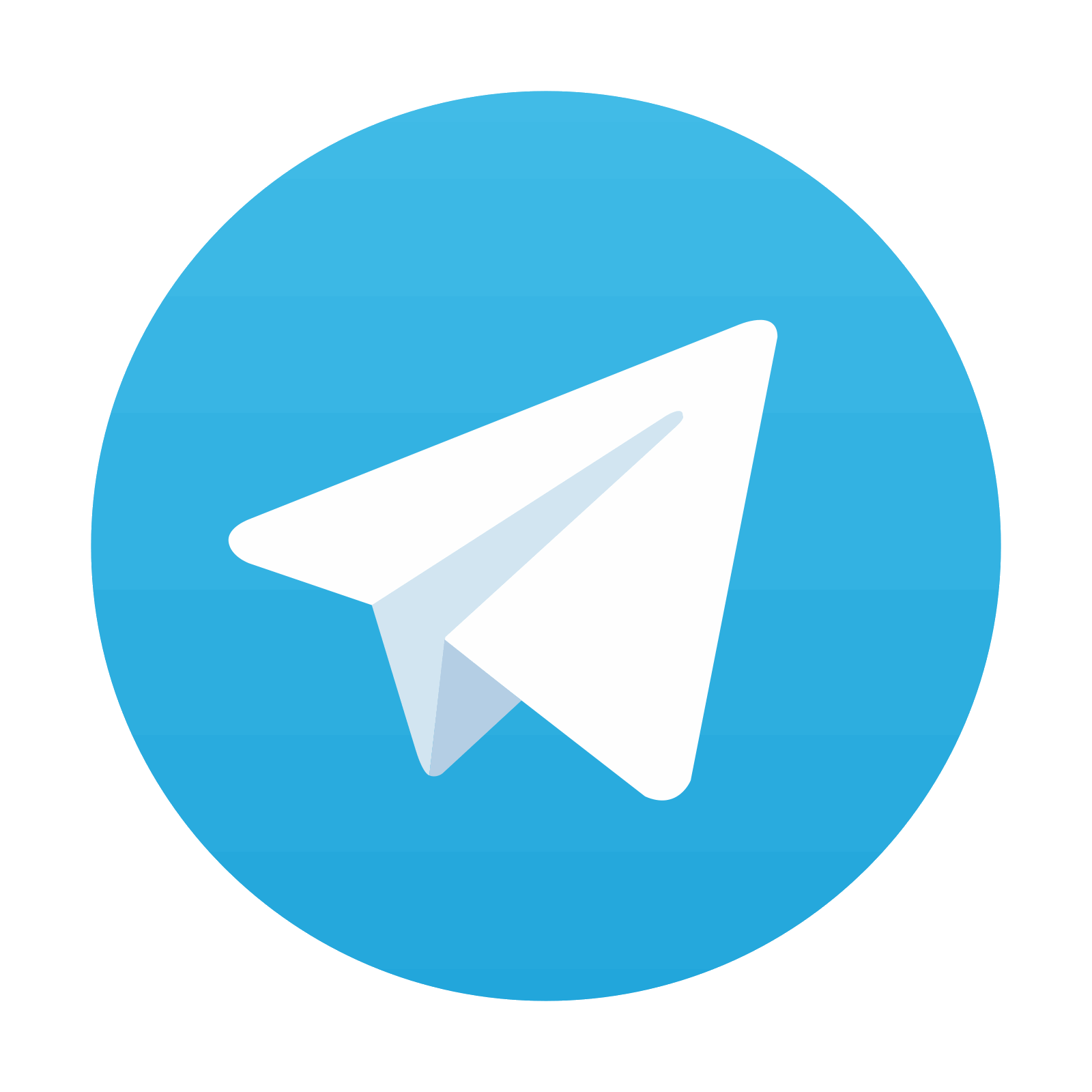
Stay updated, free dental videos. Join our Telegram channel

VIDEdental - Online dental courses
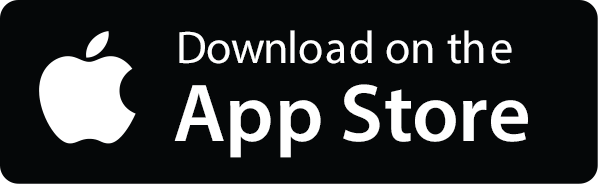
