Abstract
Objectives
The aim of this study was to thermo-polymerize under high pressure four commercially available dental resin composites to obtain and characterize composite blocks suitable for CAD/CAM procedures.
Methods
Gradia (GC, Japan), Vita VM LC (Vita Zahnfabrik, Germany), Grandio (VOCO, Germany), and EsthetX (Dentsply, Germany), were selected for this study. Paradigm (3 M ESPE, USA), a CAD/CAM composite block, was included for comparison. Composite blocks were obtained through polymerization at high-temperature high-pressure (HT/HP). Samples for mechanical/physical characterizations were cut from Paradigm and HT/HP composite blocks while control samples were obtained by photo-polymerizing (PP) the materials in molds. Flexural strength ( σ f ), fracture toughness ( K IC ), hardness, and density ( ρ ) were determined and compared by pairwise t -tests ( α = 0.05). Fractured surfaces were characterized under a scanning electron microscope.
Results
The results have shown that HT/HP polymerization resulted in a significant ( p < 0.05) increase in σ f , hardness, and ρ for all composites investigated. Even if K IC of all materials was increased by HT/HP polymerization, significant increases were detected only for Gradia and EsthetX. The Weibull modulus of HT/HP polymerized composites was higher than that of PP counterparts. HT/HP materials had higher σ f , Weibull modulus, and K IC compared to Paradigm. The most significant SEM observation of fractured K IC specimens from all the materials tested was the presence of fewer and smaller voids in HT/HP polymerized composites.
Significance
The results of this study suggest that HT/HP polymerization could be used to obtain dental resin composite blocks with superior mechanical properties, suitable for CAD/CAM processing.
1
Introduction
Due to esthetic considerations and to the growing concern related to metal ion release from alternative restorative materials (amalgam), it is expected that “future developments will focus on highly esthetic organic–inorganic systems with good bonding to tooth structure, long-term stability and wear resistance, high biocompatibility, and simplicity of clinical handling” . Resin composites, along with adhesive dentistry – the associated procedure of attaching them to hard tooth tissues, represent probably the most promising development in restorative dentistry. Over the last ten years, significant progress has been achieved in improving the properties of dental resin composites to enable their usage in posterior, load bearing restorations . Furthermore, the use of resin composites has expanded from a direct restorative material to laboratory processed composite blocks to be used in CAD/CAM systems for the fabrication of indirect restorations, such as inlays, onlays, crowns, and even bridges . The foreseen advantages of a CAD/CAM processed composite block over a direct composite restoration are multiple and comprise a better polymerized material, less porosity, more homogeneity, the avoidance of the in vivo polymerization shrinkage, and the avoidance of operator-related variables, to mention only a few. Moreover, using resin composite blocks instead of ceramic blocks for CAD/CAM procedures could significantly reduce the time of fabrication and have less wear on the cutting equipment . Resin composite restorations could be maintained and repaired easier than ceramic ones. In comparison, however, with ceramic blocks intended for the same application, resin composite blocks have inferior mechanical properties and, therefore, major concerns exist with regards to their long term in vivo performance.
The aim of this study was to thermo-polymerize under high pressure four commercially available resin composites to obtain and then characterize resin composite blocks suitable for use in CAD/CAM procedures. The null hypothesis tested was that physical and mechanical properties of composite blocks obtained via thermo-polymerization under high pressure are no different from those of photo-polymerized counterparts.
2
Materials and methods
Four commercially available dental resin composites, Gradia (GC, Japan), Vita VM LC (Vita Zahnfabrik, Germany), Grandio (VOCO, Germany), and EsthetX (Dentsply, Germany), were selected for this study. Paradigm (3 M ESPE, USA), a commercially available resin composite block for CAD/CAM, was also included for comparison. Table 1 summarizes the details regarding the materials used, while samples preparation and characterization are described in the following sections.
Composite (manufacturer) | Matrix b | Filler | Filler content | Group | Polymerization parameters |
---|---|---|---|---|---|
Gradia (GC) | UDMA, EDMA | Silica & Pre-polymerized filler | Weight:75% | GCL | Light polymerization |
GCP | 250 MPa + 180 °C for 1 h | ||||
Grandio (VOCO) | BisGMA, TEGDMA, Urethane-BisGMA adduct | Barium-alumino-borosilicate; fumed silica | Weight: 87% Volume:71.4% | VOL | Light polymerization |
VOP | 250 MPa + 180 °C for 1 h | ||||
EsthetX (Dentsply) | BisGMA, TEGDMA, bis-EMA adduct | Barium-fluoro-alumino-borosilicate; fumed silica | Weight:77% Volume: 60% | DEL | Light polymerization |
DEP | 250 MPa + 180 °C for 1 h | ||||
VitaVM LC (VITA Zahnfrabrik) | UDMA, TEGDMA, BisGMA, 2-dimethylaminoethyl methacrylate | Silica filler | Weight: (45-48) % | VIL | Light polymerization |
VIP | 250 MPa + 180 °C for 1 h | ||||
Paradigm (3 M ESPE) | BisGMA, TEGDMA | Silane-treated ceramic | Weight: (80-90) % | P | As received CAD/CAM blocks |
a The composition of the organic matrix and filler content was obtained from manufacturers’ data.
b BisGMA is bisphenol A glycol-dimethacrylate; TEGDMA is triethyleneglycol dimethacrylate; EDMA is ethyleneglycoldimethacrylate; EMA is ethylenemethacrylate; UDMA is urethanedimethacrylate.
Gradia and VITA VM LC are light-curable indirect composites and are indicated for inlays, onlays, veneers, and for full and partial crowns, whereas Grandio and EsthetX are light-curable direct composites. In order to replicate manufacturers’ recommended laboratory curing procedures for the indirect composites, the initial photo-polymerization of all composites was followed by a 30 min post-cure in a curing chamber (PLC 4000, Schütz Dental, Germany). This procedure, furthered referred to as “photo-polymerization” (PP), would increase the degree of conversion and would therefore maximize the mechanical/physical properties of all materials.
2.1
Thermo-polymerization under high pressure
A differential scanning calorimeter (DSC 823, Mettler Toledo, Greifensee, Switzerland) was used to determine the thermo-polymerization temperature of each material at atmospheric pressure (0.1 MPa). Since the determined polymerization temperatures were in the (160–180) °C range, it was decided to perform all the polymerization reactions at 180 °C. Thereafter, approximately 100 g of each material was placed inside a flexible silicone tube (25 mm internal diameter), which was then introduced into an autoclave (custom-built for this study) with pressure and temperature control (LabVIEW version 8.2, National Instruments, USA). A thermocouple was placed in the proximity of the sample to enable accurate monitoring and, via feed-back, control of the temperature. In the first stage, the pressure within the autoclave was increased to 250 MPa at a rate of 0.1 MPa/s at ambient temperature. In the second stage, the temperature was increased to 180 °C, at a rate of 2 °C/min. The sample was then maintained at 250 MPa and 180 °C for 60 min before being cooled off and the pressure released. Four cylindrical composite blocks (25 mm × ∼200 mm), one from each composite, were made.
2.2
Flexural strength
One part of each high-temperature high-pressure (HT/HP) polymerized composite block was cut, with an Isomet saw (Buehler) under water irrigation, into 25 to 30 rectangular bars [(2 mm × 2 mm × 20 mm)]. Paradigm blocks were cut similarly to obtain 25 samples.
Control specimens ( n = 30) were obtained by photo-polymerizing resin composites packed into (2 × 2 × 20) mm stainless steel molds. The samples were irradiated three times (once on the middle of the sample and one time on each extremity of the sample) for 40 s with a LED curing unit (Radii, SDI, Victoria, Australia) operating at a power density of 897 mW/cm 2 (measured with a Curing radiometer, Dentsply Caulk, Milford, USA). After de-molding, the samples were post-cured for 30 min in a curing chamber.
Each sample was polished on 4000 grit silicon carbide (SiC) paper on a water-irrigated grinding wheel and its dimensions were measured with a digital caliper (Mitutoyo Co., Kawasaki, Japan) before being tested.
Flexural strength ( σ f ) was determined by loading the samples in a three point bending device (with a 16 mm span between the supports) at a cross-head speed of 1 mm/min, using a computer controlled (NexyGen ® , Lloyd, UK) Lloyd LRX (Lloyd, UK) universal testing machine.
Flexural strength was calculated using the formula:
where F is the load at fracture, L the specimen span, h the specimen width, and c the specimen height.
2.3
Fracture toughness
One part of each HT/HP polymerized composite block was cut, with an Isomet saw (Buehler) under water irrigation, into eight rectangular bars [(8 × 8 × 15) mm], which were then wet ground on 800 grit SiC to obtain (6 × 6 × 6 × 12) mm equilateral triangular prisms. Eight Paradigm samples were obtained in the same manner.
Eight control specimens for each material were obtained by photo-polymerizing (PP) resin composites, packed and cured in increments, into (6 × 6 × 6 × 12) mm teflon molds. The increments were irradiated for 40 s with a LED curing unit (Radii, SDI, Victoria, Australia) operating at a power density of 897 mW/cm 2 (measured with a Curing radiometer, Denstsply Caulk, Milford, USA). After de-molding, the samples were post-cured for 30 min in a curing chamber.
Fracture toughness ( K IC ) was determined using the notchless triangular prism (NTP) specimen K IC test. The prisms were secured into one half of the specimen holder and a sharp scalpel was used create a small (<0.1 mm-deep) defect along the loading edge before securing the second half of the specimen holder. The specimens were loaded in tension, using a computer controlled (Bluehill, Instron) universal testing machine (Instron model 4301, Instron Canada Inc.), at a crosshead speed of 0.01 mm/min until crack arrest or fracture. The maximum load recorded before crack arrest or complete failure ( P max ) was used to calculate K IC in MPa m 1/2 using the following equation, proposed by Barker and adopted by ASTM standard E1304:
where Ymin
Y min
is the minimum dimensionless stress intensity coefficient (28 for NTP samples ) D the specimen holder diameter (12 mm), and W the specimen holder length (10.4 mm).
2.4
Hardness
Fractured flexural strength specimens were used for microhardness determinations. Experimental HT/HP, Paradigm, and control PP samples, were surface coated with a thin (∼10 nm) gold layer, in a sputter-coater (SC500, Bio-Rad, UK), in order to improve reading. Surface microhardness was measured by means of a Vickers indenter (MH3, Metkon, Bursa, Turkey), under a 10 N loading and a 20 s dwell time. Thirty determinations on five specimens were made for each material.
2.5
Density
Fractured K IC specimens were used for density determinations. The density of HT/HP, Paradigm, and control PP samples, was determined based on Archimedes’s principle using a XS205 (Mettler Toledo, Greifensee, Switzerland) balance. They were weight in air and in deionized water and the density was then calculated using the following formula:
where ρ is density of the sample, A the mass of the sample in air, B the mass of the sample in deionized water, ρ w the density of deionized water determined from the measurement of water temperature, and ρ a the density of air (0.0012 g/cm 3 ). Thirty determinations on five specimens were made for each material.
2.6
Fractured surface morphology
Representative fractured NTP specimens of HT/HP polymerized, Paradigm, and control PP composites were sputter-coated (SC500, Bio-Rad, UK) with gold. The surface morphology was then characterized under a scanning electron microscope (SEM) (JSM-6400, JEOL Ltd., Tokyo, Japan) at low and high magnification.
2.7
Statistical analysis
Since the main purpose of this study was to assess the effect of HT/HP polymerization on the physical/mechanical properties and not to compare materials among themselves, the results of mechanical/physical tests for each material were analyzed by t -tests, performed at a 0.05 level of significance. The results obtained for Paradigm were used as a reference only and were not included in the statistical analysis.
Weibull statistics parameters were calculated for the flexural strength data. The description of the Weibull distribution is given by
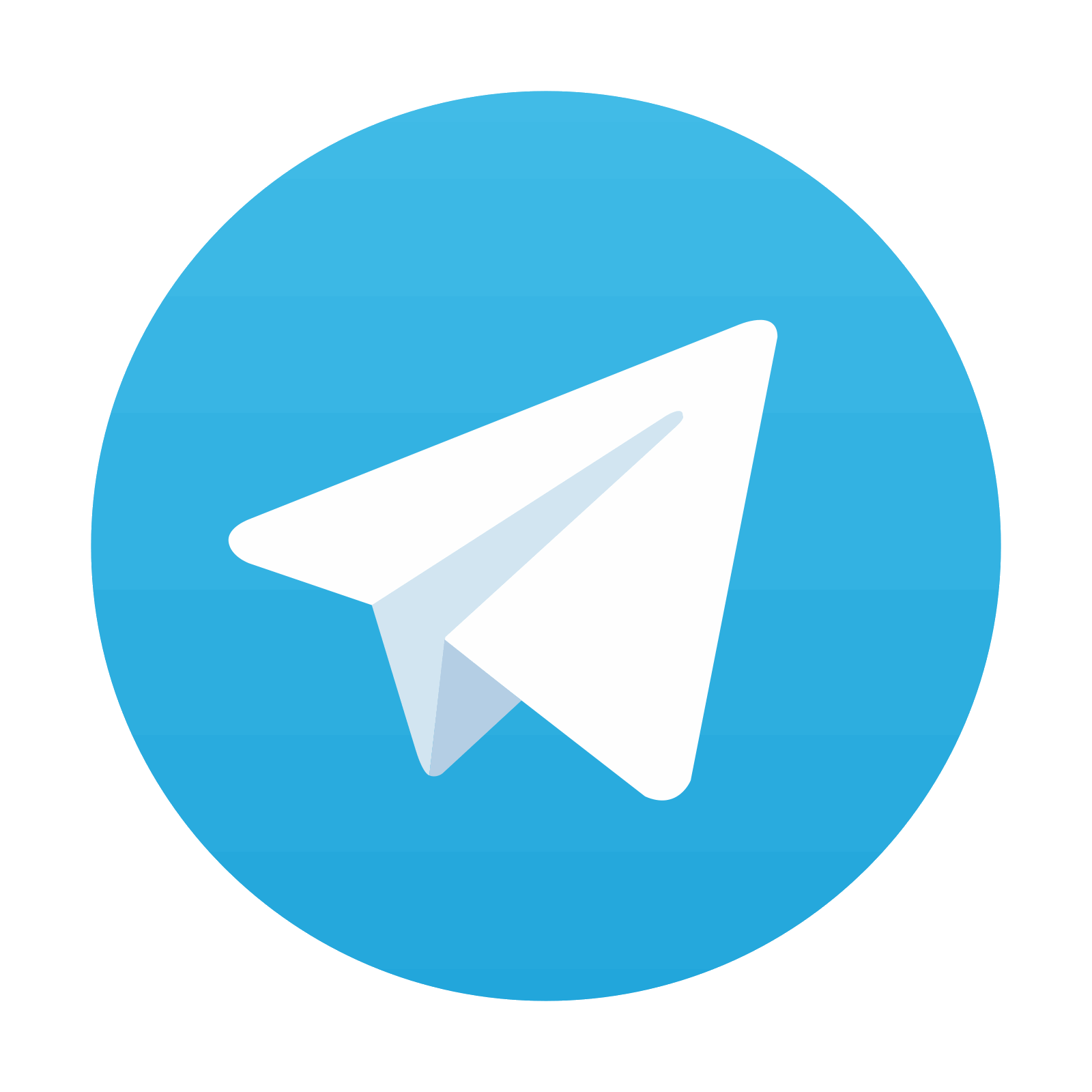
Stay updated, free dental videos. Join our Telegram channel

VIDEdental - Online dental courses
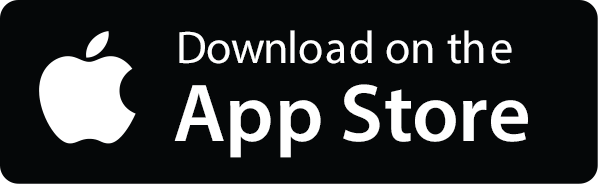
