Prosthetic Polymers and Resins
Fabrication of Dentures
Several processing techniques are available for the fabrication of denture bases (Figures 19-1 to 19-11). Each technique requires a suitable impression of the associated dental arch followed by fabrication of an accurate gypsum cast. In turn, a resin record base is fabricated on the cast. Wax is added to the record base, and prosthetic teeth are positioned in the wax, related to the opposing dentition, and evaluated in the patient’s mouth before proceeding.
Acrylic Resins
One decided advantage of polymethyl methacrylate is the relative ease with which it can be processed. Polymethyl methacrylate denture base material is commonly supplied as a powder-liquid system. The liquid contains mostly nonpolymerized methyl methacrylate and the powder contains predominantly prepolymerized polymethyl methacrylate resin in the form of micro-sized beads (or spheres). When the liquid and powder are mixed in the proper proportions, a workable mass is formed. The material is introduced into a properly formed mold cavity and polymerized. The chemical basis for this reaction is described in Chapter 6.
Heat-Activated Denture Base Resins
Composition
As previously noted, most polymethyl methacrylate resin systems include powder and liquid components (Figure 19-1). The powder consists of prepolymerized spheres of polymethyl methacrylate and a small amount of benzoyl peroxide, termed the initiator, which is responsible for starting the polymerization process. The liquid is predominantly nonpolymerized methyl methacrylate monomer with small amounts of hydroquinone. Hydroquinone is added as an inhibitor, which prevents undesirable polymerization or “setting” of the liquid during storage. Inhibitors also retard the curing process and thereby increase working time.
A cross-linking agent can also be added to the liquid. Glycol dimethacrylate is used commonly as a cross-linking agent in polymethyl methacrylate denture base resins. Glycol dimethacrylate is chemically and structurally similar to methyl methacrylate. Therefore, it can be incorporated into growing polymer chains (Figure 19-2). One should note that methyl methacrylate possesses one carbon-carbon double bond per molecule and glycol dimethacrylate possesses two double bonds per molecule. As a result, an individual molecule of glycol dimethacrylate can participate in the polymerization of two separate polymer chains that unites the two polymer chains. If sufficient glycol dimethacrylate is included in the mixture, several interconnections can be formed and solvent swelling may occur, such as that caused by exposure to ethanol in alcoholic beverages. These interconnections yield a netlike structure that provides increased resistance to deformation. Cross-linking agents are incorporated into the liquid component at a concentration of 1% to 2% by volume.
Compression Molding Technique
Preparation of the Mold
At this stage, the master cast and completed tooth arrangement are removed from the dental articulator (Figure 19-3, A). The master cast is coated with a thin layer of separator to prevent adherence of dental stone to the master cast during the flasking process. The lower portion of a denture flask is filled with freshly mixed dental stone, and the master cast is placed into this mixture. The dental stone is contoured to facilitate wax elimination, packing, and deflasking procedures (Figure 19-3, B). Upon reaching its initial set, the stone is coated with an appropriate separator.
The upper portion of the selected denture flask is then positioned atop the lower portion of the flask. A surface tension-reducing agent is applied to exposed wax surfaces and a second mix of dental stone is prepared. The dental stone is poured into the denture flask. Care is taken to ensure that the investing stone achieves intimate contact with all external surfaces of the mounted teeth. The investing stone is added until all surfaces of the tooth arrangement and denture base are completely covered. Incisal and occlusal surfaces are minimally exposed to facilitate subsequent deflasking procedures (Figure 19-3, C). The stone is permitted to set and is coated with separator.
At this point an additional increment of dental stone is mixed and the remainder of the flask is filled. The lid of the flask is gently seated and the stone is allowed to harden (Figure 19-3, D).
After the stone has hardened, the record base and wax must be removed from the mold. To accomplish this task, the denture flask is immersed in boiling water for 4 min. The flask is then removed from the water and the appropriate segments are separated. The record base and softened wax remain in the lower portion of the denture flask while the prosthetic teeth remain firmly embedded in the investing stone of the remaining segment (Figure 19-3, E). The record base and softened wax are carefully removed from the surface of the mold. Residual wax is removed from the mold cavity using wax solvent. The mold cavity is subsequently cleaned with a mild detergent solution and rinsed with boiling water.
Selection and Application of A Separating Medium
Placement of an alginate-based separating medium is relatively uncomplicated. A small amount of separator is dispensed into a disposable container. Then a fine brush is used to spread the separating medium onto the exposed surfaces of a warm, clean stone mold (Figure 19-3, F). Separator should not be permitted to contact exposed portions of acrylic resin teeth, since its presence interferes with chemical bonding between acrylic resin teeth and denture base resins. Subsequently, the mold sections are oriented to prevent “pooling” of separator, and the solution is permitted to dry.
Packing
While in a doughlike state, the resin is removed from its mixing container and rolled into a ropelike form. Monomer is painted over the necks of the denture teeth to promote bonding to the denture base. Subsequently, the resin form is bent into a horseshoe shape and placed into the portion of the flask that houses the prosthetic teeth (Figure 19-4, A). A thin polyethylene separator sheet is placed over the master cast, and the flask is reassembled.
The flask assembly is placed into a specially designed press and pressure is applied incrementally (Figure 19-4, B). Slow application of pressure permits the resin dough to flow uniformly throughout the mold space. Excess material is displaced eccentrically. The application of pressure is continued until the denture flask is fully closed. Next the flask is opened and the polyethylene packing sheet is removed from the surface of the resin with a rapid, continuous tug.
Excess resin will be found on the relatively flat areas surrounding the mold cavity. This excess resin is called flash. Using a gently rounded instrument, the flash is carefully teased away from the body of resin that occupies the mold cavity (Figure 19-4, C). Care is taken not to chip the gypsum surfaces of the mold. Pieces of gypsum that have become dislodged must be removed so that they are not incorporated into the processed denture base.
When flash is no longer apparent, the mold is closed for the last time with no polyethylene sheet interposed. The mold sections are properly aligned and placed in the flask press. Again, pressure is incrementally applied. Following definitive closure, the flask is transferred to a flask carrier (Figure 19-4, D). The flask carrier maintains pressure on the flask assembly during denture base processing. A cross-sectional representation of the denture flask assembly is presented in Figure 19-5.
Injection Molding Technique
In addition to compression molding techniques, denture bases can be fabricated via injection molding using specially designed flasks. One half of the flask is filled with freshly mixed dental stone, and the master cast is settled into this mixture. The dental stone is appropriately contoured and permitted to set. Subsequently, sprues or ingates are attached to the wax denture base, which lead to an inlet or pressure port (Figure 19-6, A). The remaining half of the flask is positioned, and the investment process is completed (Figure 19-6, B). Wax elimination is performed as previously described (Figure 19-6, C), and the flask is reassembled. Subsequently, the flask is placed into a carrier that maintains pressure on the assembly during resin introduction and processing.
Upon completion of the foregoing steps, resin is mixed and injected into the mold cavity (Figure 19-6, D). The flask is then placed into a water bath for polymerization of the denture base resin if a heat-curing resin is used. Upon completion, the denture is recovered, adjusted, finished, and polished.
Polymerization Procedure
As previously noted, denture base resins generally contain benzoyl peroxide. When heated above 60 °C, molecules of benzoyl peroxide decompose to yield electrically neutral species containing unpaired electrons. These species are termed free radicals. Each free radical rapidly reacts with an available monomer molecule to initiate chain-growth polymerization. Since the reaction product also possesses an unpaired electron, it remains chemically active. Consequently additional monomer molecules become attached to individual polymer chains. This process occurs very rapidly and terminates by either (1) the direct connection of two growing chains (i.e., combination) or (2) the transfer of a single hydrogen ion from one chain to another. (See also Figures 6-7, 6-8 and 6-9 in Chapter 6).
Temperature Rise
The polymerization of denture base resins is exothermic, and the amount of heat evolved can affect the properties of the processed denture bases. Representative temperature changes occurring in water, investing stone, and resin are presented in Figure 19-7. The temperature profile of the investing stone (identified as “plaster”) closely parallels the heating curve for the water. The temperature of the denture base resin lags somewhat during the initial stages of the heating process. This can be attributed to the fact that the resin occupies a position in the center of the mold and therefore heat penetration takes a longer time.
Polymerization Cycle
The curing cycle presented in Figure 19-7 is unsatisfactory because of the marked temperature increase during the early stages of polymerization. Rapid heating of the resin mass may cause the monomer to boil, producing porosity within the polymerized denture base. Fortunately this process can be controlled by heating the resin more slowly during the polymerization cycle.
The relationship between the rate of heating and temperature rise within the denture base resin is illustrated in Figure 19-8. The polymerization cycle represented by curve C probably would yield porosity in thick portions of the denture, since the temperature of the resin exceeds the boiling point of the monomer (100.8 °C). On the other hand, the polymerization cycle represented by curve A probably would result in the presence of unreacted monomer, since the resin temperature fails to reach the boiling temperature of the monomer (100.8 °C). Thus, it is logical to assume that an optimum polymerization cycle lies somewhere between curves A and C.
Polymerization via Microwave Energy
Polymethyl methacrylate resin can be polymerized using microwave energy because the methyl methacrylate molecule is asymmetric. This technique employs a specially formulated resin and a nonmetallic flask (Figure 19-9). A conventional microwave oven is used to supply the thermal energy required for polymerization.
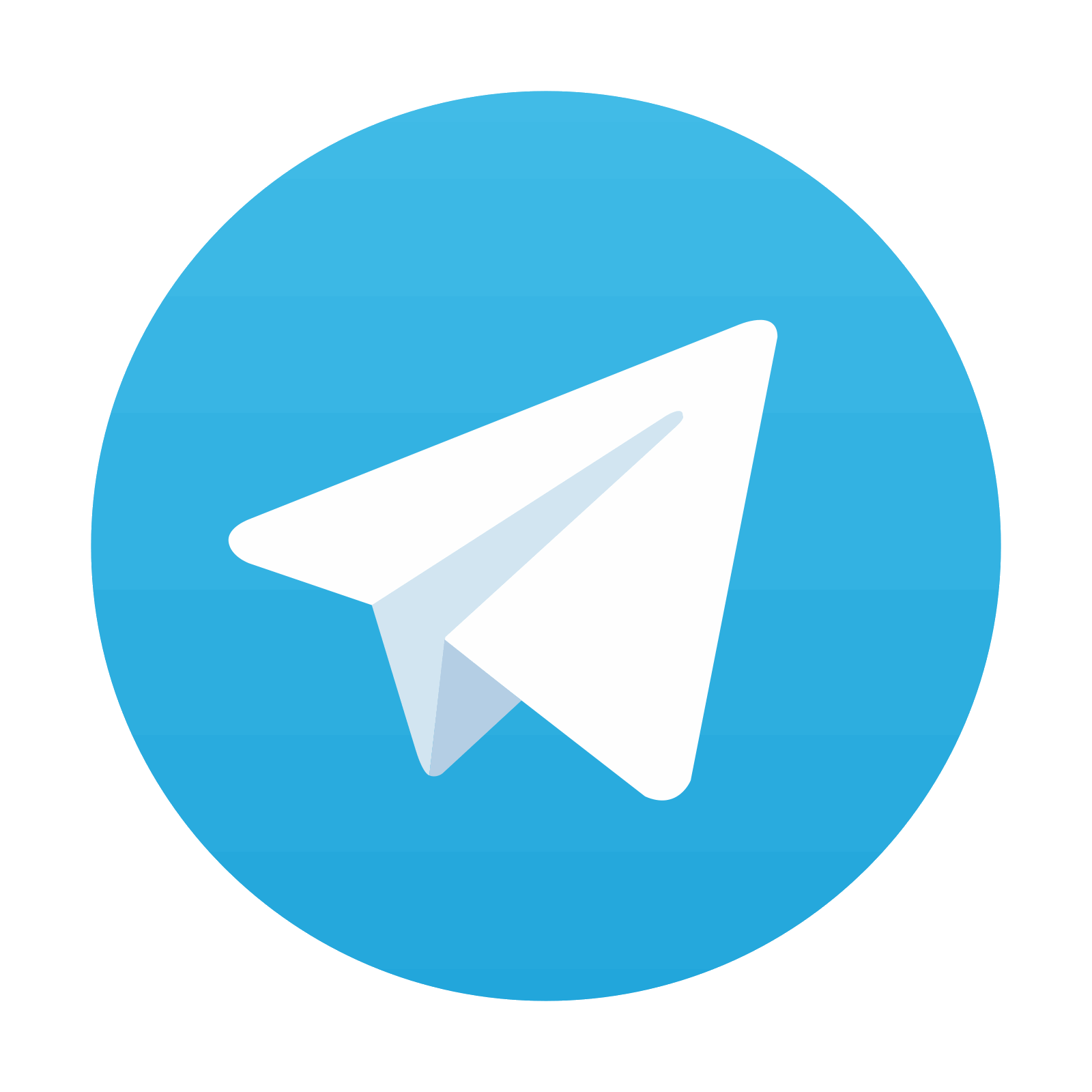
Stay updated, free dental videos. Join our Telegram channel

VIDEdental - Online dental courses
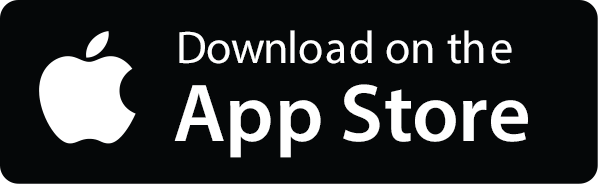
