Abstract
Objectives
This study seeks to correlate the interrelated properties of conversion, shrinkage, modulus and stress as dimethacrylate networks transition from rubbery to glassy states during photopolymerization.
Methods
An unfilled BisGMA/TEGDMA resin was photocured for various irradiation intervals (7–600 s) to provide controlled levels of immediate conversion, which was monitored continuously for 10 min. Fiber optic near-infrared spectroscopy permitted coupling of real-time conversion measurement with dynamic polymerization shrinkage (linometer), modulus (dynamic mechanical analyzer) and stress (tensometer) development profiles.
Results
The varied irradiation conditions produced final conversion ranging from 6% to more than 60%. Post-irradiation conversion (dark cure) was quite limited when photopolymerization was interrupted either at very low or very high levels of conversion while significant dark cure contributions were possible for photocuring reactions suspended within the post-gel, rubbery regime. Analysis of conversion-based property evolution during and subsequent to photocuring demonstrated that the shrinkage rate increased significantly at about 40% conversion followed by late-stage suppression in the conversion-dependent shrinkage rate that begins at about 45–50% conversion. The gradual vitrification process over this conversion range is evident based on the broad but well-defined inflection in the modulus versus conversion data. As limiting conversion is approached, modulus and, to a somewhat lesser extent, stress rise precipitously as a result of vitrification with the stress profile showing little if any late-stage suppression as seen with shrinkage.
Significance
Near the limiting conversion for this model resin, the volumetric polymerization shrinkage rate slows while an exponential rise in modulus promotes the vitrification process that appears to largely dictate stress development.
1
Introduction
Polymer-based composites have become the most common dental restorative material with a current use rate more than twice that of amalgam filling materials . These resin composites fulfill many of the requirements for clinical restorative applications, including excellent esthetics, practical clinical manipulation steps for chair-side applications, high mechanical properties, low coefficient of thermal expansion and high resistance to softening and wear. However, a major limitation of the resin phase used to construct the dental composite is its volumetric polymerization shrinkage and even more critically, the accompanying stress evolution that occurs during polymerization of bonded restorations for which free shrinkage is constrained .
The reduction in free volume based on polymerization shrinkage in dental composites is a direct function of the proportion of the resin phase of the composite, and more specifically, depends on the initial reactive group concentration and the degree of conversion attained within the resin phase during polymerization. This shrinkage, when coupled with the clinical requirement for relatively high modulus restorative materials, creates the potential for high polymerization stresses within the composite and at the interface between the composite and tooth substrate, which adds complexity to the bonding protocol. These acute and chronic stresses severely strain the interfacial bond between the composite and the tooth, leading to small gaps that can allow marginal leakage of saliva and microorganisms that potentially lead to the development of marginal staining and recurrent decay . In addition, the stress can exceed the tensile strength of enamel that might be compromised by the cavity preparation procedures with the result of stress cracking and enamel fracture along the interface .
Dental resins are typically composed of mixtures of two or more monomers that combine a relatively viscous dimethacrylate base monomer, such as bisphenol A glycidyl methacrylate (BisGMA) or urethane dimethacrylate (UDMA), with a lower-viscosity diluent dimethacrylate comonomer, such as triethylene glycol dimethacrylate (TEGDMA) . During resin photopolymerization, viscosity, modulus and glass transition temperature ( T g ), all increase as the proportion of free monomer and partially reacted pendant monomer is consumed as the polymer network evolves .
With advancing polymerization, several interrelated physical and kinetic landmarks, are passed, including the gel point, auto-acceleration leading to a rate maximum and vitrification that leaves a substantial degree of residual unsaturation in the final glassy polymer. Therefore, there are several distinct stages to the polymerization process as the reaction progresses from a liquid pre-gel regime to a rubbery gelled phase and finally reaches a glassy state . This final stage of the polymer network development extends over significant time scales due to vitrification and the associated persistence of active free radicals , which allows for small degrees of additional chemical-based conversion, but also due to slow network densification that has been referred to as physical aging .
Gel point is defined as the appearance of an insoluble polymer fraction and it involves a continuous network structure, regardless of its density, that spans macroscopic specimen dimensions . Several studies have pointed out that shrinkage strain that occurs prior to gelation does not contribute to stress development since this involves viscous but unrestricted flow . There are limited options to delay the gel point conversion , which otherwise occurs at a very early stage in typical dimethacrylate bulk polymerizations. As the reaction progresses through the rubbery post-gel regime, modulus continues to increase along with conversion, until the T g of the developing polymer becomes limited by the effective cure temperature . Unlike the physically well delineated gel point, vitrification, which involves the transition from a rubbery to a glassy polymeric state, is a gradual process that is extended by the breadth of the evolving tan δ peak (the maximum of which represents an averaged T g ) due to the structural heterogeneity that is characteristic of dimethacrylate network formation. Stress development is known to be concentrated in this late stage of conversion due to a significant increase in modulus that is expected to accompany the rubbery to glassy transition .
Several prior studies have focused on the conversion-dependent evolution of polymerization shrinkage stress and modulus development during polymerization , but conversion measurements typically involved separate specimens and even different specimen geometries or curing protocols compared with those used to analyze property development. With the current investigation, efforts are directed to obtain true conversion-indexed property development with an emphasis on the critical vitrification stage of the polymerization process where significant changes in modulus and stress evolution are anticipated. This information may provide improved insights into new methods and materials approaches that can ultimately lower polymerization stress without jeopardizing the degree of conversion or important polymeric performance properties.
Therefore, the aim of the present study is to correlate the interrelated properties of conversion, shrinkage, modulus and stress as a model dimethacrylate network transitions from the rubbery to the glassy state during and to a limited extent, following photopolymerization.
2
Materials and methods
A resin composed of bisphenol A glycidyl methacrylate (BisGMA; Esstech, Essington, PA, USA) and triethylene glycol dimethacrylate (TEGDMA; Esstech) in a 70:30 mass ratio was used. A photoinitiator, 2,2-dimethoxy-2-phenylacetophenone (DMPA; Aldrich, Milwaukee, WI, USA), was added at 0.1 wt% to render the resin photo-curable with UV irradiation. The UV source is acknowledged to introduce differences in light transmission and initiator efficiency compared with visible light irradiation, but it does not alter the structure of the polymer formed at a given initiation rate. The rationale for the use of the UV curing was to allow uniform irradiation of the entire specimen in one exposure cycle. In addition, significantly lower irradiance was used compared with conventional dental curing units to allow adequate sampling of the various evolving properties. This difference would be expected to affect the exothermic response during polymerization and the final conversion limits but does not otherwise affect the fundamental property development processes described here.
2.1
Degree of conversion and photopolymerization reaction kinetics
Real-time monitoring of the polymerization kinetics based on the methacrylate CH 2 absorption at 6165 cm −1 was carried out using near–infrared (NIR) spectroscopy at 2 scans per spectrum with 4 wavenumber resolution, which provides a greater than 2 Hz data acquisition rate. Regardless of the irradiation interval, kinetic data was collected continuously for 10 min. Samples ( n = 3) were irradiated for the following exposure times: 10, 15, 20, 30, 60 and 600 s with the filtered 365 ± 10 nm output of a mercury arc lamp (Acticure 4000, EFOS, Mississaguga, Canada) at an incident irradiance of 10 mW/cm 2 with a 6 cm distance between the liquid light guide (6 mm output diameter) and the specimen to assure uniform irradiance over at least a 25 mm spot size. Specimens were 10 mm in diameter and 0.8 mm thick laminated between two glass slides. In selected specimens, an embedded mini-thermocouple (120 μm, diameter) with a 1 Hz sampling rate (Tecpel DTM-322, Taipei, Taiwan) was used to track temperature change during and following the irradiation. The average conversion ( n = 2) at which the temperature maximum was observed rise is reported.
2.2
Volumetric polymerization shrinkage
Volumetric shrinkage was measured using a linometer (ACTA; Amsterdam, The Netherlands). A standardized volume of the resin was placed onto an aluminum disc and covered with a glass slide through which the UV curing light irradiation at 10 mW/cm 2 was applied under the previously described conditions. The space between the aluminum disc and glass slide provided a fixed specimen thickness of 1.25 mm with a diameter of approximately 6 mm. An alignment guide was attached to the linometer to orient two 100 μm optical fibers such that a real-time NIR signal was transmitted along the transverse axis of the sample. The specimens were irradiated for 10, 15, 20, 30, 60 and 600 s. This approach allows simultaneous monitoring of the degree of conversion with the dynamic volumetric shrinkage . Use of a thin layer of grease to minimize substrate adhesion with the polymer permits the real-time measured displacement caused by linear shrinkage to be converted to the corresponding volumetric shrinkage. The dynamic shrinkage data and degree of conversion were recorded during and extended beyond the specified irradiation intervals for a total period of 10 min. Three measurements were carried out for each exposure time.
2.3
Dynamic mechanical analysis
For the dynamic studies to track modulus development during the later stages of polymerization, a technique is introduced here that allows simultaneous real-time monitoring of conversion and modulus achieved by integration of fiber optic transmission NIR spectroscopy with a photo-accessible dynamic mechanical analyzer (DMA; PerkinElmer 8000, Waltham, MA, USA; Fig. 1 ). Bar-shaped specimens (2 mm × 2 mm × 25 mm) were prepared by partial photopolymerization to a post-gel stage (approximately 30–40% conversion) using a bifurcated light guide to achieve simultaneous, uniform irradiance of both the upper and lower surfaces. The specimens ( n = 3) were subjected to ambient temperature, single cantilever DMA testing (2.5% strain at 1 Hz) along with the introduction of a secondary irradiation interval (20, 60, 120 and 600 s) at an incident UV irradiance of 10 mW/cm 2 (again supplied via bifurcated light guides at a 6 cm distance). An additional group of pre-cured specimens ( n = 3) were subjected to 600 s of 100 mW/cm 2 incident irradiance in the same manner. Simultaneous scanning of the storage modulus development and degree of conversion were recorded for 20 min from the start of the second curing cycle. To accurately assign conversion before and during the secondary reaction in the DMA, the NIR aromatic absorbance associated with BisGMA (4620 cm −1 ) was used as an internal reference .
2.4
Polymerization shrinkage stress
The shrinkage stress was determined using a tensometer (ADAF-PRC, Gaithersburg, MD). Specimens with dimensions of 1 mm thick × 6 mm diameter were prepared for each exposure time ( n = 3) and photopolymerized through the quartz rod attached to the bottom of the specimen for the previously mentioned exposure times with appropriate intensity to obtain the same standardized 10 mW/cm 2 incident irradiance condition. Along with the dynamic stress development profile, simultaneous real-time conversion data during polymerization were collected via NIR fiber optic cables .
2.5
Statistical analysis
Normally distributed data were subjected to one-way ANOVA and Student-Newman–Keuls post hoc test, and any data that failed the normality test were then subjected to Kruskal–Wallis one-way analysis of variance on rank and Dunn’s post hoc test. All of the dynamic data presented represent averaged results rather than individual specimen profiles.
2
Materials and methods
A resin composed of bisphenol A glycidyl methacrylate (BisGMA; Esstech, Essington, PA, USA) and triethylene glycol dimethacrylate (TEGDMA; Esstech) in a 70:30 mass ratio was used. A photoinitiator, 2,2-dimethoxy-2-phenylacetophenone (DMPA; Aldrich, Milwaukee, WI, USA), was added at 0.1 wt% to render the resin photo-curable with UV irradiation. The UV source is acknowledged to introduce differences in light transmission and initiator efficiency compared with visible light irradiation, but it does not alter the structure of the polymer formed at a given initiation rate. The rationale for the use of the UV curing was to allow uniform irradiation of the entire specimen in one exposure cycle. In addition, significantly lower irradiance was used compared with conventional dental curing units to allow adequate sampling of the various evolving properties. This difference would be expected to affect the exothermic response during polymerization and the final conversion limits but does not otherwise affect the fundamental property development processes described here.
2.1
Degree of conversion and photopolymerization reaction kinetics
Real-time monitoring of the polymerization kinetics based on the methacrylate CH 2 absorption at 6165 cm −1 was carried out using near–infrared (NIR) spectroscopy at 2 scans per spectrum with 4 wavenumber resolution, which provides a greater than 2 Hz data acquisition rate. Regardless of the irradiation interval, kinetic data was collected continuously for 10 min. Samples ( n = 3) were irradiated for the following exposure times: 10, 15, 20, 30, 60 and 600 s with the filtered 365 ± 10 nm output of a mercury arc lamp (Acticure 4000, EFOS, Mississaguga, Canada) at an incident irradiance of 10 mW/cm 2 with a 6 cm distance between the liquid light guide (6 mm output diameter) and the specimen to assure uniform irradiance over at least a 25 mm spot size. Specimens were 10 mm in diameter and 0.8 mm thick laminated between two glass slides. In selected specimens, an embedded mini-thermocouple (120 μm, diameter) with a 1 Hz sampling rate (Tecpel DTM-322, Taipei, Taiwan) was used to track temperature change during and following the irradiation. The average conversion ( n = 2) at which the temperature maximum was observed rise is reported.
2.2
Volumetric polymerization shrinkage
Volumetric shrinkage was measured using a linometer (ACTA; Amsterdam, The Netherlands). A standardized volume of the resin was placed onto an aluminum disc and covered with a glass slide through which the UV curing light irradiation at 10 mW/cm 2 was applied under the previously described conditions. The space between the aluminum disc and glass slide provided a fixed specimen thickness of 1.25 mm with a diameter of approximately 6 mm. An alignment guide was attached to the linometer to orient two 100 μm optical fibers such that a real-time NIR signal was transmitted along the transverse axis of the sample. The specimens were irradiated for 10, 15, 20, 30, 60 and 600 s. This approach allows simultaneous monitoring of the degree of conversion with the dynamic volumetric shrinkage . Use of a thin layer of grease to minimize substrate adhesion with the polymer permits the real-time measured displacement caused by linear shrinkage to be converted to the corresponding volumetric shrinkage. The dynamic shrinkage data and degree of conversion were recorded during and extended beyond the specified irradiation intervals for a total period of 10 min. Three measurements were carried out for each exposure time.
2.3
Dynamic mechanical analysis
For the dynamic studies to track modulus development during the later stages of polymerization, a technique is introduced here that allows simultaneous real-time monitoring of conversion and modulus achieved by integration of fiber optic transmission NIR spectroscopy with a photo-accessible dynamic mechanical analyzer (DMA; PerkinElmer 8000, Waltham, MA, USA; Fig. 1 ). Bar-shaped specimens (2 mm × 2 mm × 25 mm) were prepared by partial photopolymerization to a post-gel stage (approximately 30–40% conversion) using a bifurcated light guide to achieve simultaneous, uniform irradiance of both the upper and lower surfaces. The specimens ( n = 3) were subjected to ambient temperature, single cantilever DMA testing (2.5% strain at 1 Hz) along with the introduction of a secondary irradiation interval (20, 60, 120 and 600 s) at an incident UV irradiance of 10 mW/cm 2 (again supplied via bifurcated light guides at a 6 cm distance). An additional group of pre-cured specimens ( n = 3) were subjected to 600 s of 100 mW/cm 2 incident irradiance in the same manner. Simultaneous scanning of the storage modulus development and degree of conversion were recorded for 20 min from the start of the second curing cycle. To accurately assign conversion before and during the secondary reaction in the DMA, the NIR aromatic absorbance associated with BisGMA (4620 cm −1 ) was used as an internal reference .
2.4
Polymerization shrinkage stress
The shrinkage stress was determined using a tensometer (ADAF-PRC, Gaithersburg, MD). Specimens with dimensions of 1 mm thick × 6 mm diameter were prepared for each exposure time ( n = 3) and photopolymerized through the quartz rod attached to the bottom of the specimen for the previously mentioned exposure times with appropriate intensity to obtain the same standardized 10 mW/cm 2 incident irradiance condition. Along with the dynamic stress development profile, simultaneous real-time conversion data during polymerization were collected via NIR fiber optic cables .
2.5
Statistical analysis
Normally distributed data were subjected to one-way ANOVA and Student-Newman–Keuls post hoc test, and any data that failed the normality test were then subjected to Kruskal–Wallis one-way analysis of variance on rank and Dunn’s post hoc test. All of the dynamic data presented represent averaged results rather than individual specimen profiles.
3
Results and discussion
3.1
Reaction kinetics
Statistical analysis of the discrete kinetics data revealed that statistically higher final conversion values were achieved as the exposure times were increased ( p < 0.001) ( Table 1 ), except for the 20 s and 30 s irradiation times ( p = 0.083) ( Fig. 2 a ). However, there was no statistically significant difference regarding maximum rate of conversion associated with the different irradiation times ( p = 0.778) ( Fig. 2 b) since all the exposure intervals matched or exceeded that necessary to reach the rate maximum under these curing conditions. The kinetic data demonstrated that the rate maximum consistently occurs at approximately 18% conversion ( Table 1 ). These results are in agreement with other studies where the rate maxima in photopolymerizations of a variety dental resins and composites were encountered over the conversion range of approximately 10–20% . The kinetic plot ( Fig. 2 b) for the 60 s irradiation interval shows an inflection at approximately 45% conversion. This kinetic transition point has been suggested as an indication of the vitrification stage of the polymerization where the reaction continues at a very low rate over an extended time span. While not examined here, macrogelation of this dimethacrylate resin would be anticipated to occur at or below approximately 5% conversion . A single sample was photocured for only 7 s at the same 10 mW/cm 2 irradiance level. In that case, conversion at the end of the irradiation was approximately 2%, which is well ahead of the expected rate maximum and also presumably close to the gel point. While the reaction rate quickly dropped to near zero when the light was shuttered under this circumstance, the conversion plateau displayed a slight but clearly positive slope ending at a conversion of approximately 6% within the 10 min observation interval. This indicates that even in this highly mobile early stage of polymerization, persistent radicals are present in the incipient heterogeneous polymer.
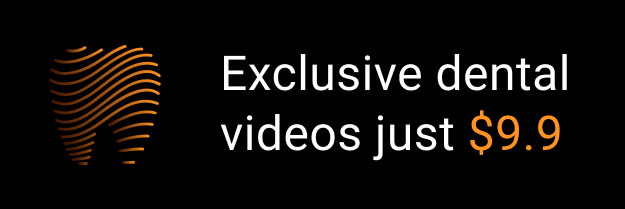