Introduction
Orthodontic treatment of palatally impacted maxillary canines raises many difficulties; to minimize complications, careful planning of orthodontic extrusion and the use of physiologic force are crucial. The aim of this study was to quantitatively evaluate a simple and reproducible system for orthodontic extrusion of impacted canines that can provide the correct amount of force.
Methods
Ten specimens were constructed, consisting of a cantilever made with a 0.6-mm or 0.7-mm stainless steel wire modeled around a transpalatal bar with 3, 5, or 7 loops in the shape of a helical torsion spring. A mechanical testing machine was used to measure the force produced by the cantilever at 3, 6, 9, 12, and 15 mm of activation.
Results
The force values ranged from 1.24 ± 0.13 N for the 0.7-mm wire with 3 loops to 0.48 ± 0.04 N for the 0.6-mm wire with 7 loops. The forces measured for the 0.6-mm wire with 3 loops and the 0.7-mm wire with 7 loops were similar at 15 mm of deflection.
Conclusions
The proposed system has a simple and robust design, is easy to construct and manage, and can provide the desired amount of force by changing the wire diameter and number of loops.
Graphical abstract

Highlights
- •
Few studies have evaluated the force used by devices for maxillary canine extrusion.
- •
The appliance uses a stainless steel cantilever arm with a helical torsion spring.
- •
Changing the wire diameter and the number of loops produces different forces.
- •
Physiologic force values below the recommended 0.6 N can be predictably reached.
- •
This device is simple, economical, easy to manage, stiff, and resistant to breakage.
Orthodontic treatment of impacted teeth is often challenging for both the patient and the clinician because of prolonged treatment time, the need for surgical intervention to expose the tooth, and difficult biomechanics. The treatment of a palatally impacted canine involves accurate anchorage preparation, careful planning of orthodontic traction vectors to prevent root contact, management of the arch space, and special attention during the finishing phase. Some risks that can accompany orthodontic extrusion and alignment of an impacted canine include loss of vitality, loss of periodontal attachment, and root resorption of both the canine and the adjacent teeth. To reduce the risk of complications, it is important to respect bone biology and use light forces that should range between 0.4 and 0.6 N according to the literature. In addition to the magnitude of the applied force, biomechanical and directional control of the canine movement is necessary; poorly controlled orthodontic extrusion while the impacted tooth is near other roots may lead to root resorption and introduce moments that cause unwanted rotations of the maxillary canine.
Several methods have been described to perform orthodontic extrusion of a palatally impacted canine. The use of cantilevers, springs, elastomeric chains, and double archwires (ie, piggyback) are all effective techniques. Despite their diffusion and wide clinical use, none of these appliances or systems has been adequately quantified clinically. In a study, 3 commonly used systems were analyzed, and all of them showed force entities far beyond the physiologic limit for orthodontic extrusion, which ranges from 2.35 to 2.57 N. Since the impacted canine moves according to the applied orthodontic force system, quantification of this force is important for the validation and selection of 1 system over the others.
The appliance that is used at the Department of Biotechnological and Applied Clinical Sciences, University of L’Aquila, L’Aquila, Italy, for orthodontic extrusion of maxillary palatally impacted canines is made of a stainless steel cantilever welded to a transpalatal bar. The free end of the cantilever wire is rolled multiple times around the transpalatal bar. This device is defined as a helical torsion spring and is described by the following equation :
where F is the force produced by the spring, D is the radius of the loop, d is the diameter of the wire, n is the number of loops, R is the length of the arm, E is the elastic modulus, and β is the angle at which the arm is bent ( Fig 1 ).

The purpose of this study was to precisely quantify the forces produced by this type of appliance for orthodontic extrusion of an impacted maxillary canine, and to give the clinician useful information about a system that is simple and easy to construct and manage, and how to use it to provide the appropriate and desired force levels.
Material and methods
The appliance was made of a fixed transpalatal bar made of 0.9-mm stainless steel wire with a distal loop soldered to 2 molar bands. A cantilever, which can be made of stainless steel wires with different diameters, was then welded to the transpalatal bar after wrapping it with a variable number of loops; the opposite free end had an eyelet that was used for ligature ties ( Fig 2 ).

To measure the force exerted by this appliance, specimens made of a 50-mm straight segment of 0.9-mm stainless steel wire (Leowire; Leone S.p.a., Sesto Fiorentino, Firenze, Italy), with a 30-mm cantilever welded perpendicular to it, were prepared. The cantilever was constructed using either a 0.6- or 0.7-mm stainless steel wire; for both wire diameters, different specimens were constructed with 3, 5, or 7 loops around the 0.9-mm wire ( Fig 3 ). The loops had an inner diameter of 1.4 mm. For each wire diameter and loop number combination, 10 samples were prepared, for a total of 60 samples. To improve accuracy, the mechanical properties of the wire were obtained from the technical sheet of the specific lot of production.

To measure the force produced by the different types of cantilever, a mechanical testing machine (3365 series; Instron, Norwood, Mass) with a loading cell of 100 N was used, and a specific support for the cantilever specimen was designed and manufactured ad hoc ( Fig 4 ). The specimen was positioned and firmly secured into the vise using the support of 6 screws; to prevent rotation of the specimen, 1 side of the vise was flat, and the other had a groove that partly housed the 0.9-mm wire. A flat-headed bit was connected to the crosshead of the testing machine and positioned at a fixed distance of 20 mm from the center of the cantilever’s loops. The crosshead was set to run for 17 mm pushing over the cantilever at a speed of 5 mm per minute, and the force produced was recorded at 3, 6, 9, 12, and 15 mm. The cantilever arm was bent in the same direction used for the fabrication of the loops. The loading cell was calibrated before every test sequence.

Statistical analysis
The Shapiro-Wilk normality test, indicated for small samples, was performed to assess the data distribution ( P <0.05). One-way analysis of variance (ANOVA) was conducted to examine the effect of the different combinations of wire diameter and number of loops on the force values measured at 15-mm deflection. The Levene test was used to test the assumption of equal error variance. The Tukey Honestly Significant Difference test or the Games-Howell test was performed for the post hoc analysis. After applying the Bonferroni correction for multiple tests, first-type error was set at 0.008.
Results
The mechanical properties of the stainless steel wires are provided in Table I . Descriptive statistics are reported in Table II . Force value increases as the cantilever bends, although not in a linear fashion as described by the equation, or if a stiffer wire is used; in addition, the force value decreases as the number of loops increases ( Fig 5 ). The highest force values were produced by the cantilever made of 0.7-mm wire with 3 loops, which were as high as 1.24 ± 0.13 N when the cantilever arm was bent at 15 mm; the lowest forces (0.48 ± 0.04 N at 15 mm of deflection) were measured using the 0.6-mm wire with a 7-loop cantilever. The forces measured for the 0.6-mm wire with 3 loops and the 0.7-mm wire with a 7-loop cantilever at 15 mm of deflection were similar (0.74 ± 0.08 N and 0.77 ± 0.05 N, respectively).
Wire diameter | Tensile strength (Mpa) | Yield strength 0.2% (Mpa) | Elongation at 100 mm (%) |
---|---|---|---|
0.6 mm | 1901-1938 | 1517-1569 | 0.8-1.6 |
0.7 mm | 1904-1953 | 1400-1579 | 1.2-1.8 |
Cantilever type | Activation | |||||||||
---|---|---|---|---|---|---|---|---|---|---|
3 mm | 6 mm | 9 mm | 12 mm | 15 mm | ||||||
Mean ± SD | Minimum- maximum | Mean ± SD | Minimum- maximum | Mean ± SD | Minimum- maximum | Mean ± SD | Minimum- maximum | Mean ± SD | Minimum- maximum | |
0.6-mm wire, 3 loops | 0.27 ± 0.03 | 0.24-0.32 | 0.47 ± 0.04 | 0.42-0.53 | 0.61 ± 0.07 | 0.54-0.72 | 0.67 ± 0.09 | 0.55-0.84 | 0.74 ± 0.08 | 0.65-0.89 |
0.6-mm wire, 5 loops | 0.22 ± 0.02 | 0.19-0.25 | 0.38 ± 0.03 | 0.34-0.42 | 0.47 ± 0.04 | 0.4-0.55 | 0.52 ± 0.05 | 0.45-0.6 | 0.54 ± 0.05 | 0.48-0.64 |
0.6-mm wire, 7 loops | 0.17 ± 0.02 | 0.13-0.2 | 0.3 ± 0.02 | 0.25-0.34 | 0.4 ± 0.02 | 0.34-0.43 | 0.45 ± 0.04 | 0.4-0.52 | 0.48 ± 0.04 | 0.43-0.54 |
0.7-mm wire, 3 loops | 0.44 ± 0.03 | 0.4-0.51 | 0.79 ± 0.06 | 0.71-0.88 | 1.04 ± 0.09 | 0.94-1.16 | 1.18 ± 0.1 | 1.01-1.35 | 1.24 ± 0.13 | 1-1.39 |
0.7-mm wire, 5 loops | 0.36 ± 0.03 | 0.31-0.42 | 0.62 ± 0.05 | 0.54-0.7 | 0.82 ± 0.07 | 0.7-0.91 | 0.93 ± 0.09 | 0.77-1.04 | 0.99 ± 0.12 | 0.78-1.12 |
0.7-mm wire, 7 loops | 0.29 ± 0.03 | 0.25-0.33 | 0.5 ± 0.04 | 0.44-0.57 | 0.66 ± 0.05 | 0.58-0.74 | 0.74 ± 0.05 | 0.66-0.85 | 0.77 ± 0.05 | 0.69-0.84 |

The Shapiro-Wilk normality test showed that all measurements were normally distributed, except for the 0.6-mm wire with 3 loops at a deflection of 3 mm ( P = 0.022). There was a statistically significant difference between the force values at the 15-mm deflection using the different cantilevers as determined by 1-way ANOVA (F [5] = 112.2; P <0.001; adjusted R 2 = 0.90) and reported in Table III . The Levene test showed that the error variances were not equal between groups ( P = 0.003); therefore, the Games-Howell post hoc test was used. All comparisons were statistically significant ( P <0.008), except between the 0.6-mm wire with 3 loops and the 0.7-mm wire with 7 loops, and between the 0.6-mm wires with 5 loops and 7 loops ( Table IV ).
Source | Sum of squares | df | Mean square | F | P | Partial eta squared |
---|---|---|---|---|---|---|
Cantilever type | 4,025 | 5 | 0.805 | 112,206 | <0.001 | 0.912 |
Error | 0.387 | 54 | 0.007 | |||
Total | 42,128 | 60 |
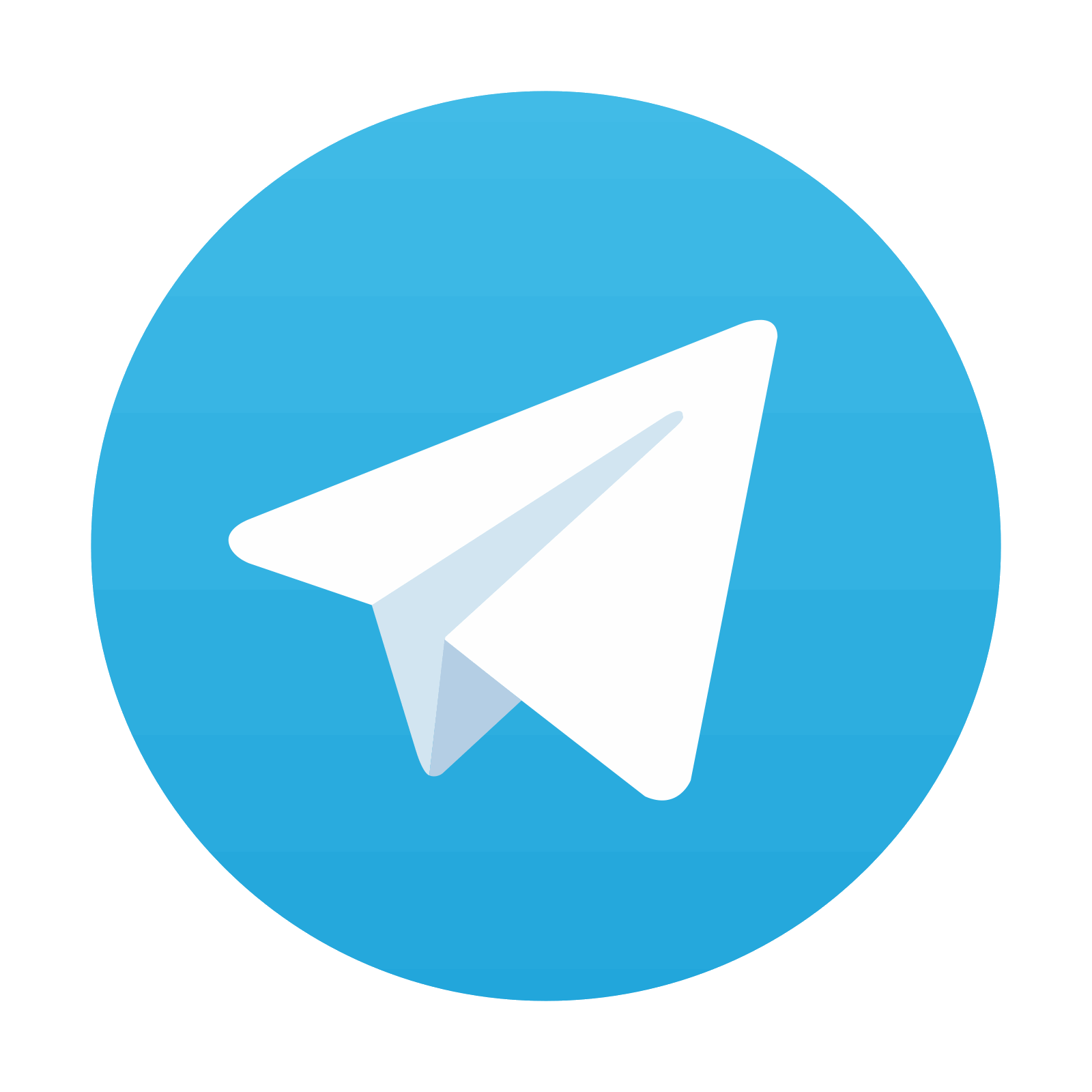
Stay updated, free dental videos. Join our Telegram channel

VIDEdental - Online dental courses
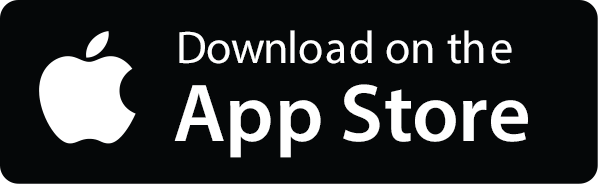

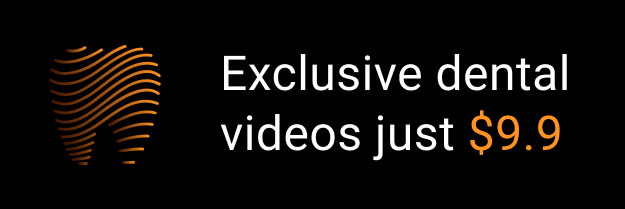