Highlights
- •
The ability of polymer infiltrated ceramic network (PICN) monolithic crowns to sustain high bite force and wear challenge has been evaluated.
- •
PICN crowns can withstand mouth-motion cyclic loading up to 1700 N and 300 K cycles.
- •
PICN crowns have only suffered minor wear following prolonged sliding-contact cyclic loading under clinically relevant conditions.
- •
Under extreme loads (>2000 N), fracture may occur by splitting the crowns mesio-distally.
Abstract
Objective
To investigate fatigue fracture resistance and wear behavior of a polymer infiltrated ceramic network (PICN) material (ENAMIC, Vita Zahnfabrik).
Methods
Anatomically shaped ENAMIC monolithic crowns were milled using a CAD/CAM system. The crowns were cemented on aged dentin-like composite abutments (Z100, 3M ESPE) with resin-based cement (Vita DUO Cement, Vita). The specimens were subjected to 2 types of fatigue and wear tests: (1) accelerated sliding-contact mouth-motion step-stress fatigue test ( n = 24) in water; and (2) long-term sliding-contact mouth-motion fatigue/wear test using a clinically relevant load ( P = 200 N, n = 8) in water. Failure was designated as chip-off or bulk fracture. Optical and scanning electron microscopes were used to examine the occlusal surface and subsurface damage, as well as to reveal the material’s microstructure. In addition, wear volume and depth were measured by X-ray micro-computed tomography.
Results
For accelerated mouth-motion step-stress fatigue testing, 3 out of the 24 ENAMIC crowns fractured following cyclic loading up to 1700 N. Minor occlusal damage and contact-induced cone cracks were observed in all surviving specimens, but no flexural radial cracks were seen. For long-term mouth-motion fatigue/wear testing under a 200 N load in water, a small wear scar without significant cracks was observed in all 8 tested ENAMIC crowns.
Significance
Monolithic CAD/CAM ENAMIC crowns showed superior resistance to sliding-contact fatigue fracture and wear.
1
Introduction
A polymer infiltrated ceramic network (PICN) material—VITA ENAMIC (Vita Zahnfabrik, Bad Säckingen, Germany), in which each phase is topologically interconnected throughout the microstructure has been recently launched in the dental CAD/CAM market. Although ENAMIC is so far the only dental material commercially available in this category, the concept of interpenetrating microstructures was first introduced to the field of dental materials in the mid-1980s . This has led to the development of the In-Ceram systems (Vita Zahnfabrik), which consist of a porous ceramic network (alumina, zirconia toughened alumina, or spinel) that is infiltrated with a low viscosity glass. The In-Ceram restorative systems have been used successfully for 25 years . However, the transition from glass infiltration to polymer infiltration of a porous ceramic network has taken quite a long time with a lot of efforts .
The ENAMIC material consists of 86 wt.% or 75 vol.% inorganic phase and 14 wt.% or 25 vol.% organic phase. The inorganic phase is a feldspathic ceramic, whereas the organic phase is composed of dimethacrylates (UDMA and TEGDMA). The three dimensional interconnected dual network structure differs from traditional composites in which only the matrix phase is continuous . The ceramic network provides resistance to deformation and wear, but it is brittle and susceptible to fracture. The ductile polymer network, capable of undergoing plastic deformation, yields resistance to fracture . PICN materials combine enhanced resistance to distinct damage modes, exhibiting physical properties that are different and often superior than conventional composites .
A lot of attention has been drawn to developing and improving PICN materials since the release of ENAMIC in 2013 . A comprehensive review of this class of materials has been recently published by Swain et al. . The authors have concluded that PICN materials present a combination of low hardness and modulus coupled with higher toughness and R-curve behavior than glass-ceramic materials, enabling rapid milling with minimal chipping at the margin/edge, as well as the ability to cope with severe occlusal contact loading. However, the authors have also indicated that no information regarding wear and fatigue behavior of PICN was available. It has been discussed that resistance to fatigue fracture and wear damage are important determinants of the clinical longevity of direct and indirect dental restorations .
Accordingly, the aim of this study is to elucidate the resistance to fatigue fracture and wear damage of monolithic ENAMIC molar crowns by means of accelerated sliding-contact mouth-motion step-stress fatigue test and long-term fatigue/wear test with a clinically relevant load in water.
2
Materials and methods
2.1
Specimens fabrication
Anatomically correct mandibular first molar crowns were designed and milled from VITA ENAMIC CAD/CAM blocks, using a CEREC System (Sirona, Charlotte, NC, USA). A standard die of a mandibular first molar preparation was scanned into the system and adjusted to compensate for the cement layer thickness (50 μm) . Tooth preparation was modeled by reducing the proximal walls by 1.5 mm and the occlusal surface by 2.0 mm. The anatomically correct crown specimens were polished using the VITA ENAMIC technical polishing set (Vita Zahnfabrik), as recommended by the manufacturer. A single operator performed all polishing procedures with the aid of a magnification loupe (4.5 magnification Zeiss, Jena Germany).
For ENAMIC restorations, which cannot be placed in the oven for traditional glazing treatments, fine polishing after milling is a very important step to reduce the roughness and population of surface defects. It is well-established that fatigue and wear behavior are governed by material properties, surface characteristics, contact geometry, and the interfacial friction coefficient . Polishing also reduces the friction between the contacting surfaces . In surfaces subjected to cyclic sliding, pre-existing defects act as stress-concentrators and can become the origins of cracks. Propagation of these cracks is associated with mechanical fatigue, such as hydraulic pumping, as well as moisture-assisted slow crack growth .
All crowns were cemented to aged resin-based composite dies (Filtek Z100, 3M ESPE, St. Paul, MI, USA), which were stored in distilled water at 37 °C for 3–5 weeks. Z100 was selected as abutment material because it has an elastic modulus of 18 GPa , which is similar to the elastic modulus of 16–18 GPa for human dentin . The effective elastic moduli of the supporting abutment and luting cement were found to play a governing role in the fracture resistance of dental crowns .
All cementation procedures followed the manufacturers’ instructions: Z100 abutments were thoroughly cleaned with ethanol and air-dried, followed by application of VITA A.R.T. BOND adhesive (Vita Zahnfabrik), rubbing it for 20 s and air drying for 5 s. The crowns were cleaned in ultrasonic bath and air-dried. The inner surfaces were then thoroughly cleaned with ethanol and air-dried. A 5% hydrofluoric acid gel (VITA CERAMICS ETCH, Vita Zahnfabrik) was applied to the inner surfaces of the crowns for 60 s, rinsed in tap water, and air dried for 20 s. VITASIL (Vita Zahnfabrik) silane coupling agent was applied to the etched surface, followed by 60 s waiting time, and air drying. The adhesive VITA A.R.T. BOND was rubbed on the cementation surface for 20 s and air-dried. VITA DUO CEMENT (Vita Zahnfabrik) 1:1 base & catalyst pastes were mixed and applied to the inner surface of the crown. The crowns were then pressed onto the abutment by hand. Caution was taken to ensure that marginal gaps were closed uniformly. Excess cement was chipped away after 2–3 s light curing. Photopolymerization of the luting agent was carried out by exposing each surface of the crown to a dental curing light with an irradiance of 850 mW/cm 2 for 40 s (Ultra Lume LED 5, Ultradent Products Inc., South Jordan, UT, USA). All cementation procedures were carried out by a single operator. After cementation, the specimens were stored in distilled water at 37 °C for 5–7 days for continued polymerization and the hydration of the cement layer prior to mechanical testing.
2.2
Mechanical testing
Fatigue and wear resistance of ENAMIC was tested by means of two methods: (1) accelerated sliding-contact mouth-motion step-stress fatigue test ( n = 24) and (2) long-term sliding-contact mouth-motion fatigue/wear test using a clinically relevant load ( n = 8). Crowns were immersed in distilled water during all tests.
To determine the cyclic loading profiles that constitute the accelerated sliding-contact mouth-motion step-stress fatigue test, four crowns were subjected to single cycle load to failure test . The crown/tooth replica assembly was mounted in a universal testing machine (Model 5566, Instron, Canton, MA, USA), and load was applied axially at the central fossa of the occlusal surface of the crown through a tungsten carbide (WC) spherical indenter ( r = 3.18 mm). Specimens were loaded monotonically at a constant rate of 1 mm/min until failure.
Accelerated sliding-contact mouth-motion step-stress fatigue test were used to determine cyclic fatigue behavior of ENAMIC. Three step-stress profiles (mild, moderate, and aggressive) were designed based upon results from the single load to fracture test. Crowns were distributed across the three profiles in the ratio of 4:2:1 for mild ( n = 12), moderate ( n = 6), and aggressive ( n = 3) profiles, respectively. The mild profile starts at 400 N indentation load and goes to 1200 N at 170k cycles; the moderate profile starts at 500 N and goes to 1400 N at 120k cycles; and the aggressive profile at 600 N and goes to 1700 N at 70k cycles. Three additional ENAMIC crowns were subjected to the extended aggressive profile with load up to 1700 N and 300k cycles (including 30k at 1700 N). It is well-established that ceramic and composite materials are sensitive to load/stress rate. Therefore, a clinically relevant loading rate (1000 N/s) was used . As a result, the loading frequency, including load, slide, and lift-off phases, varied from 0.3 Hz at 1700 N to 2 Hz at 200 N. The crowns were subjected to accelerated step-stress fatigue by sliding a spherical WC indenter ( r = 3.18 mm) 0.7 mm down the distobuccal cusp toward the central fossa, using an electrodynamic fatigue testing machine (EL-3300, Enduratec Division, TA Instruments, Minnetonka, MN). At the end of each load cycle, all specimens were inspected under a polarized light stereomicroscope for cracks and damage. Bulk fracture and chip-off fracture of the crowns were considered as failures.
In an attempt to simulate loading conditions relevant to those occurring during chewing, 8 crowns were subjected to long-term sliding-contact mouth-motion fatigue/wear by sliding a spherical steatite indenter ( r = 3 mm) 0.7 mm down the disto-buccal cusp toward the central fossa, using the electrodynamic fatigue testing machine at a maximum load of 200 N and 2 Hz frequency for 1.25 million cycles in water. These fatigue testing conditions are believed to simulate 5 years of clinical service .
A steatite indenter was chosen for the long-term sliding-contact mouth-motion fatigue/wear test because it presents physical properties in the midrange of those of dental porcelains, glass-ceramics, and dental enamel . Therefore, simulating the wear of the crown and its antagonist would undergo clinically relevant conditions. On the other hand, a hard WC indenter was used for accelerated step-stress test in order to continually apply higher loads (stresses) during cyclic sliding, avoiding contact wear. Relatively soft indenter materials like steatite would undergo greater wear, increasing the contact area as the number of cycle increases, thus decreasing contact pressure, which goes against the fundamentals of the step-stress testing method. A WC indenter was also used for the single cycle load to failure test, since the results of the latter are needed to guide the design of step-stress profiles. The radii of both steatite and WC indenters (3 mm and 3.18 mm, respectively) were in the midrange of the molar cuspal radii (2–4 mm) .
2.3
Characterization of fatigue and wear damage
2.3.1
Microstructural analysis
For better understanding of the material fatigue and wear behavior, a scanning electron microscope (SEM—S3500N, Hitachi, Tokyo, Japan) was employed to analyze the microstructure of ENAMIC. Energy-dispersive X-ray spectroscopy (EDX) was used for elemental and phase analyses. Two randomly chosen crowns were cross-sectioned, polished with 3 μm diamond suspension and treated by one of two different etching techniques. One specimen was thermally etched at 500 °C for 30 min. The other specimen was acid etched with 5% hydrofluoric acid gel for 60 s. Prior to SEM examination, specimens were carbon coated to prevent electrostatic charge accumulation.
2.3.2
Accelerated step-stress fatigue damage analysis
All crowns were examined for occlusal surface damage associated with the fatigue scar and its surrounding areas using polarized light stereomicroscopy (Leica MZ-APO, Wetzlar, Germany). Failures were designated as chip-off fracture or bulk-fracture through the crown. Crowns that did not present fracture were evaluated for subsurface damage using a sectioning technique rather than a residual strength measurement using the monotonic load to failure test . The authors believe that more information can be obtained by identifying surface and subsurface structural changes than from very high load fracture patterns or reduction in initial strength. Therefore the crowns were embedded in the clear epoxy resin, cross-sectioned bucco-lingually along the direction of the sliding contact and slightly away from the center of the fatigue scar, using a water cooled low speed saw with a diamond wafering blade (Isomet, Buehler, Lake Buff, IL). Cross-sectioned crowns were polished up to the center of the fatigue scar using a sequence of diamond grinding discs of 15, 9, 6, and 3 microns (Apex, Buehler), and analyzed using polarized light stereomicroscopy for the presence of cracks and damages.
2.3.3
Long-term fatigue/wear damage analysis
Long-term sliding-contact mouth-motion fatigued crowns were evaluated by a micro-computed tomography scanner (μCT Scanco 40 medical AG, Bassersdorft, Switzerland) operated at 70 kVp energy, intensity of 114 μA (0.5 mm AL Filter), integration time 248 ms, and threshold 440. Each crown was scanned in high resolution for 18.2 min, resulting in 305 slices, with a voxel size of 8 μm. The standard error of measurement for the testing conditions was 4.95 μm. The top (occlusal) 171 slices were selected for evaluation and 3D reconstruction. Advanced software (Dataviewer version1.5.0.2, CT An version 1.13, CT vox version 2.6, Adobe Photoshop CC) was used for image processing to compare the original topography of the occlusal surface with that after fatigue/wear testing, and determine the maximum wear depth and volume loss at the fatigue scar.
2
Materials and methods
2.1
Specimens fabrication
Anatomically correct mandibular first molar crowns were designed and milled from VITA ENAMIC CAD/CAM blocks, using a CEREC System (Sirona, Charlotte, NC, USA). A standard die of a mandibular first molar preparation was scanned into the system and adjusted to compensate for the cement layer thickness (50 μm) . Tooth preparation was modeled by reducing the proximal walls by 1.5 mm and the occlusal surface by 2.0 mm. The anatomically correct crown specimens were polished using the VITA ENAMIC technical polishing set (Vita Zahnfabrik), as recommended by the manufacturer. A single operator performed all polishing procedures with the aid of a magnification loupe (4.5 magnification Zeiss, Jena Germany).
For ENAMIC restorations, which cannot be placed in the oven for traditional glazing treatments, fine polishing after milling is a very important step to reduce the roughness and population of surface defects. It is well-established that fatigue and wear behavior are governed by material properties, surface characteristics, contact geometry, and the interfacial friction coefficient . Polishing also reduces the friction between the contacting surfaces . In surfaces subjected to cyclic sliding, pre-existing defects act as stress-concentrators and can become the origins of cracks. Propagation of these cracks is associated with mechanical fatigue, such as hydraulic pumping, as well as moisture-assisted slow crack growth .
All crowns were cemented to aged resin-based composite dies (Filtek Z100, 3M ESPE, St. Paul, MI, USA), which were stored in distilled water at 37 °C for 3–5 weeks. Z100 was selected as abutment material because it has an elastic modulus of 18 GPa , which is similar to the elastic modulus of 16–18 GPa for human dentin . The effective elastic moduli of the supporting abutment and luting cement were found to play a governing role in the fracture resistance of dental crowns .
All cementation procedures followed the manufacturers’ instructions: Z100 abutments were thoroughly cleaned with ethanol and air-dried, followed by application of VITA A.R.T. BOND adhesive (Vita Zahnfabrik), rubbing it for 20 s and air drying for 5 s. The crowns were cleaned in ultrasonic bath and air-dried. The inner surfaces were then thoroughly cleaned with ethanol and air-dried. A 5% hydrofluoric acid gel (VITA CERAMICS ETCH, Vita Zahnfabrik) was applied to the inner surfaces of the crowns for 60 s, rinsed in tap water, and air dried for 20 s. VITASIL (Vita Zahnfabrik) silane coupling agent was applied to the etched surface, followed by 60 s waiting time, and air drying. The adhesive VITA A.R.T. BOND was rubbed on the cementation surface for 20 s and air-dried. VITA DUO CEMENT (Vita Zahnfabrik) 1:1 base & catalyst pastes were mixed and applied to the inner surface of the crown. The crowns were then pressed onto the abutment by hand. Caution was taken to ensure that marginal gaps were closed uniformly. Excess cement was chipped away after 2–3 s light curing. Photopolymerization of the luting agent was carried out by exposing each surface of the crown to a dental curing light with an irradiance of 850 mW/cm 2 for 40 s (Ultra Lume LED 5, Ultradent Products Inc., South Jordan, UT, USA). All cementation procedures were carried out by a single operator. After cementation, the specimens were stored in distilled water at 37 °C for 5–7 days for continued polymerization and the hydration of the cement layer prior to mechanical testing.
2.2
Mechanical testing
Fatigue and wear resistance of ENAMIC was tested by means of two methods: (1) accelerated sliding-contact mouth-motion step-stress fatigue test ( n = 24) and (2) long-term sliding-contact mouth-motion fatigue/wear test using a clinically relevant load ( n = 8). Crowns were immersed in distilled water during all tests.
To determine the cyclic loading profiles that constitute the accelerated sliding-contact mouth-motion step-stress fatigue test, four crowns were subjected to single cycle load to failure test . The crown/tooth replica assembly was mounted in a universal testing machine (Model 5566, Instron, Canton, MA, USA), and load was applied axially at the central fossa of the occlusal surface of the crown through a tungsten carbide (WC) spherical indenter ( r = 3.18 mm). Specimens were loaded monotonically at a constant rate of 1 mm/min until failure.
Accelerated sliding-contact mouth-motion step-stress fatigue test were used to determine cyclic fatigue behavior of ENAMIC. Three step-stress profiles (mild, moderate, and aggressive) were designed based upon results from the single load to fracture test. Crowns were distributed across the three profiles in the ratio of 4:2:1 for mild ( n = 12), moderate ( n = 6), and aggressive ( n = 3) profiles, respectively. The mild profile starts at 400 N indentation load and goes to 1200 N at 170k cycles; the moderate profile starts at 500 N and goes to 1400 N at 120k cycles; and the aggressive profile at 600 N and goes to 1700 N at 70k cycles. Three additional ENAMIC crowns were subjected to the extended aggressive profile with load up to 1700 N and 300k cycles (including 30k at 1700 N). It is well-established that ceramic and composite materials are sensitive to load/stress rate. Therefore, a clinically relevant loading rate (1000 N/s) was used . As a result, the loading frequency, including load, slide, and lift-off phases, varied from 0.3 Hz at 1700 N to 2 Hz at 200 N. The crowns were subjected to accelerated step-stress fatigue by sliding a spherical WC indenter ( r = 3.18 mm) 0.7 mm down the distobuccal cusp toward the central fossa, using an electrodynamic fatigue testing machine (EL-3300, Enduratec Division, TA Instruments, Minnetonka, MN). At the end of each load cycle, all specimens were inspected under a polarized light stereomicroscope for cracks and damage. Bulk fracture and chip-off fracture of the crowns were considered as failures.
In an attempt to simulate loading conditions relevant to those occurring during chewing, 8 crowns were subjected to long-term sliding-contact mouth-motion fatigue/wear by sliding a spherical steatite indenter ( r = 3 mm) 0.7 mm down the disto-buccal cusp toward the central fossa, using the electrodynamic fatigue testing machine at a maximum load of 200 N and 2 Hz frequency for 1.25 million cycles in water. These fatigue testing conditions are believed to simulate 5 years of clinical service .
A steatite indenter was chosen for the long-term sliding-contact mouth-motion fatigue/wear test because it presents physical properties in the midrange of those of dental porcelains, glass-ceramics, and dental enamel . Therefore, simulating the wear of the crown and its antagonist would undergo clinically relevant conditions. On the other hand, a hard WC indenter was used for accelerated step-stress test in order to continually apply higher loads (stresses) during cyclic sliding, avoiding contact wear. Relatively soft indenter materials like steatite would undergo greater wear, increasing the contact area as the number of cycle increases, thus decreasing contact pressure, which goes against the fundamentals of the step-stress testing method. A WC indenter was also used for the single cycle load to failure test, since the results of the latter are needed to guide the design of step-stress profiles. The radii of both steatite and WC indenters (3 mm and 3.18 mm, respectively) were in the midrange of the molar cuspal radii (2–4 mm) .
2.3
Characterization of fatigue and wear damage
2.3.1
Microstructural analysis
For better understanding of the material fatigue and wear behavior, a scanning electron microscope (SEM—S3500N, Hitachi, Tokyo, Japan) was employed to analyze the microstructure of ENAMIC. Energy-dispersive X-ray spectroscopy (EDX) was used for elemental and phase analyses. Two randomly chosen crowns were cross-sectioned, polished with 3 μm diamond suspension and treated by one of two different etching techniques. One specimen was thermally etched at 500 °C for 30 min. The other specimen was acid etched with 5% hydrofluoric acid gel for 60 s. Prior to SEM examination, specimens were carbon coated to prevent electrostatic charge accumulation.
2.3.2
Accelerated step-stress fatigue damage analysis
All crowns were examined for occlusal surface damage associated with the fatigue scar and its surrounding areas using polarized light stereomicroscopy (Leica MZ-APO, Wetzlar, Germany). Failures were designated as chip-off fracture or bulk-fracture through the crown. Crowns that did not present fracture were evaluated for subsurface damage using a sectioning technique rather than a residual strength measurement using the monotonic load to failure test . The authors believe that more information can be obtained by identifying surface and subsurface structural changes than from very high load fracture patterns or reduction in initial strength. Therefore the crowns were embedded in the clear epoxy resin, cross-sectioned bucco-lingually along the direction of the sliding contact and slightly away from the center of the fatigue scar, using a water cooled low speed saw with a diamond wafering blade (Isomet, Buehler, Lake Buff, IL). Cross-sectioned crowns were polished up to the center of the fatigue scar using a sequence of diamond grinding discs of 15, 9, 6, and 3 microns (Apex, Buehler), and analyzed using polarized light stereomicroscopy for the presence of cracks and damages.
2.3.3
Long-term fatigue/wear damage analysis
Long-term sliding-contact mouth-motion fatigued crowns were evaluated by a micro-computed tomography scanner (μCT Scanco 40 medical AG, Bassersdorft, Switzerland) operated at 70 kVp energy, intensity of 114 μA (0.5 mm AL Filter), integration time 248 ms, and threshold 440. Each crown was scanned in high resolution for 18.2 min, resulting in 305 slices, with a voxel size of 8 μm. The standard error of measurement for the testing conditions was 4.95 μm. The top (occlusal) 171 slices were selected for evaluation and 3D reconstruction. Advanced software (Dataviewer version1.5.0.2, CT An version 1.13, CT vox version 2.6, Adobe Photoshop CC) was used for image processing to compare the original topography of the occlusal surface with that after fatigue/wear testing, and determine the maximum wear depth and volume loss at the fatigue scar.
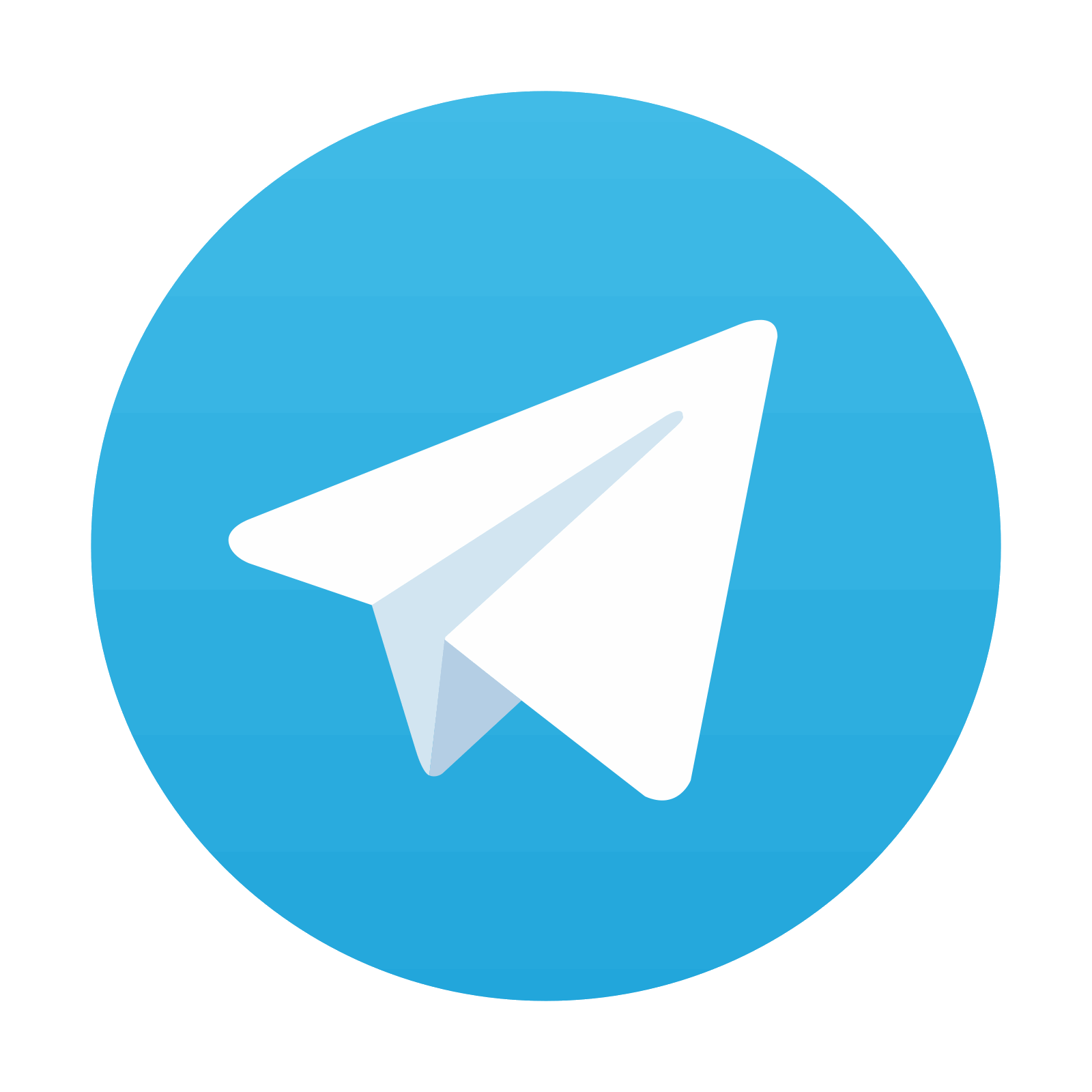
Stay updated, free dental videos. Join our Telegram channel

VIDEdental - Online dental courses
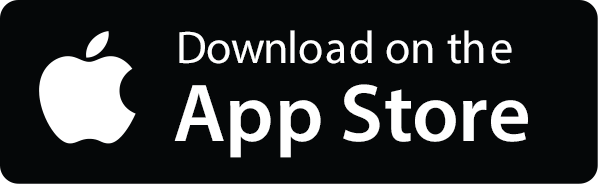
