Highlights
- •
The results have shown that HP UDMA polymers have DC superior to that of the control group.
- •
E ′ and E ″ were not significantly different between control and HP polymers.
- •
The damping factor, tan δ , decreased with increasing pressure, while <SPAN role=presentation tabIndex=0 id=MathJax-Element-1-Frame class=MathJax style="POSITION: relative" data-mathml='E′rub’>E′rubE′rub
E ′ rub
and T g increased. - •
Polymerization at 150 MPa or higher resulted in significantly higher <SPAN role=presentation tabIndex=0 id=MathJax-Element-2-Frame class=MathJax style="POSITION: relative" data-mathml='E′rub’>E′rubE′rub
E ′ rub
and T g . - •
The results have also suggested that 200 MPa is an optimum polymerization pressure, resulting in polymers with significantly higher DC, <SPAN role=presentation tabIndex=0 id=MathJax-Element-3-Frame class=MathJax style="POSITION: relative" data-mathml='E′rub’>E′rubE′rub
E ′ rub
, and T g , while maintaining adequate damping capacity (tan δ ).
Abstract
Objectives
The aim of this study, part of our research to improve properties of resin composite blocks suitable for CAD/CAM and to better understand underlying mechanisms associated with high-temperature/high-pressure (HT/HP) polymerization, was to determine an optimum polymerization pressure of urethane dimethacrylate (UDMA) in the presence of an initiator (0.5% benzoyl peroxide) by determining the degree of conversion (DC) and viscoelastic properties of polymers obtained at 90 °C under varying HP.
Methods
DC and viscoelastic properties of 16 UDMA polymers, two controls (thermo-cured and thermo-cured followed by post-cure relaxation) and 14 experimental groups (HP polymers, in the range of 50–350 MPa, in 50 MPa increments, without and with post-cure relaxation) were determined via near infrared spectroscopic analysis and dynamic mechanical analysis, respectively.
Results
The results have shown that HP UDMA polymers have DC superior to that of the control group. With regards to E ′ and E ″, the results have shown no significant difference between control and HP polymers. The damping factor, tan δ , decreased with increasing pressure, while <SPAN role=presentation tabIndex=0 id=MathJax-Element-4-Frame class=MathJax style="POSITION: relative" data-mathml='E′rub’>E′rubE′rub
E ′ rub
and T g increased. Polymerization at 150 MPa or higher resulted in significantly higher <SPAN role=presentation tabIndex=0 id=MathJax-Element-5-Frame class=MathJax style="POSITION: relative" data-mathml='E′rub’>E′rubE′rub
E ′ rub
and T g .
Significance
The results of this study suggested that HP polymerization at 90 °C of UDMA reduced the number of defects and the free volume, leading to a more homogeneous polymer network. The results have also suggested that 200 MPa is an optimum polymerization pressure, resulting in polymers with significantly higher DC, <SPAN role=presentation tabIndex=0 id=MathJax-Element-6-Frame class=MathJax style="POSITION: relative" data-mathml='E′rub’>E′rubE′rub
E ′ rub
, and T g , while maintaining adequate damping capacity (tan δ ).
1
Introduction
Research and development in dental computer-aided design/computer-aided manufacturing (CAD/CAM) systems has been actively pursued worldwide since the 1980s due to the advantages that it can provide, such as automation of fabrication procedures, increased quality, minimized inaccuracies, and faster delivery . Progress in CAD/CAM technology has been accompanied by developments in associated dental materials, ceramics, and resin composites. Easier machinability, considerable reduction in manufacturing time and wear on cutting tools, along with lower cost lead to increased interest in resin composite blocks (RCB) as viable alternative to ceramic blocks .
One of the major drawbacks of light- or thermo-cured dental resin composites is their incomplete polymerization, as identified by the relatively low (55–67% ) degree of conversion (DC), i.e., the percentage of double bonds reduced during the polymerization process. Problems associated with inadequate polymerization include inferior physical/mechanical properties, chemical instability, increased solubility in the oral environment due to the release of unreacted monomers and/or small molecular weight reaction products, and increased microleakage. All these problems may result in recurrent decay and/or irritation of the pulp .
The use of high-temperature high-pressure (HT/HP) polymerization in the fabrication of RCB suitable for CAD/CAM applications, recently reported , has led to materials that demonstrated significant increase in physical/mechanical properties , increased cross-linking , and dramatic decrease in monomer release . The effects of HP polymerization at 300 MPa on the polymeric matrix have been assessed in a previous study . However, HP polymerization represents a considerable cost in the chain of material production, a cost that increases exponentially with the pressure used. Therefore, the determination of an optimal pressure was considered important from both research and industrial points of view. Moreover, previous results have suggested that the presence of an initiator (0.5 wt% benzoyl peroxide) lead to improved properties and that a post-cure treatment (90 °C, 0.1 MPa, 12 h) lead to a relaxation of polymerization stresses . Therefore, the aim of this study, which is part of our research effort to improve the properties of RCB suitable for CAD/CAM and to better understand the underlying mechanisms associated with HT/HP polymerization, was to attempt to determine an optimum polymerization pressure of urethane dimethacrylate (UDMA) in the presence of an initiator by determining DC and viscoelastic properties of polymers obtained at 90 °C under varying HP conditions in the range of 50–350 MPa, in 50 MPa increments. The null hypothesis tested was that varying polymerization pressure has no effect on DC and on the viscoelastic properties of the polymers obtained in comparison with those of control, thermo-cured UDMA polymers.
2
Materials and methods
2.1
Specimen preparation
The monomer used in this study was urethane dimethacrylate (UDMA; MW = 470.56; CAS 41137-60-4; Esstech, Germany), which was polymerized at 90 °C in the presence of 0.5% benzoyl peroxide (BPO; Sigma Aldrich, Steinheim, Germany). Sixteen different UDMA polymers, including two control groups [thermo-cured (TC) and thermo-cured followed by post-cure relaxation (TCRX)] and 14 experimental groups (HP polymers, in the range of 50–350 MPa, in 50 MPa increments, without and with post-cure relaxation) were made. Table 1 summarizes the materials, the polymerization parameters, and the group designation of the 16 polymers made, while the experimental details are given below.
Test a | Group | Polymerization parameters | Post-polymerization parameters |
---|---|---|---|
DC | TC | 90 °C, 0.1 MPa for 4 h | None |
50 | 90 °C, 50 MPa for 4 h | None | |
100 | 90 °C, 100 MPa for 4 h | None | |
150 | 90 °C, 150 MPa for 4 h | None | |
200 | 90 °C, 200 MPa for 4 h | None | |
250 | 90 °C, 250 MPa for 4 h | None | |
300 | 90 °C, 300 MPa for 4 h | None | |
350 | 90 °C, 350 MPa for 4 h | None | |
DMA | TCRX | 90 °C, 0.1 MPa for 12 h | None |
50RX | 90 °C, 50 MPa for 4 h | 90 °C, 0.1 MPa for 12 h | |
100RX | 90 °C, 100 MPa for 4 h | 90 °C, 0.1 MPa for 12 h | |
150RX | 90 °C, 150 MPa for 4 h | 90 °C, 0.1 MPa for 12 h | |
200RX | 90 °C, 200 MPa for 4 h | 90 °C, 0.1 MPa for 12 h | |
250RX | 90 °C, 250 MPa for 4 h | 90 °C, 0.1 MPa for 12 h | |
300RX | 90 °C, 300 MPa for 4 h | 90 °C, 0.1 MPa for 12 h | |
350RX | 90 °C, 350 MPa for 4 h | 90 °C, 0.1 MPa for 12 h |
a DC is degree of conversion; DMA is dynamic mechanical analysis.
2.1.1
Control, thermo-cured UDMA (group TC), intended for the determination of DC
The monomer–initiator mix was thermally cured at 90 °C, at ambient pressure (0.1 MPa), in an oven (Memmert, Schwabach, Germany), for 4 h.
2.1.2
Experimental, HP cured UDMA (groups 50 to 350), intended for the determination of DC
The monomer–initiator mix (100 g) was placed inside a flexible silicone tube (25 mm internal diameter) and cured at 90 °C under HP (in the range of 50–350 MPa, in 50 MPa increments), in a custom-built autoclave, for 4 h .
2.1.3
Control, thermo-cured UDMA (group TCRX), intended for the determination of viscoelastic properties
The same protocol was applied as for the TC group, except the time of polymerization was 12 h.
2.1.4
Experimental, HP cured UDMA with post-cure relaxation (groups 50RX to 350RX), intended for the determination of viscoelastic properties
The groups 50RX to 350RX were obtained with the same protocol as groups 50 to 350 (90 °C; 50–350 MPa, in 50 MPa increments; for 4 h) and then were subjected to post-cure relaxation in an oven at 90 °C under 0.1 MPa for 12 h.
2.2
Degree of conversion
Ten specimens (19 mm × 12 mm × 3 mm) were made from each polymer and were polished with a 2400 grit silicon carbide (SiC) paper on a water-irrigated grinding wheel. After drying, they were placed in a metal holder between two glass cover slips. In order to assess if NIR determination of DC could only be performed with dedicated NIR spectrometers or if commonly used IR could be used as well, the measurements of DC were done using two apparatuses:
- –
Transmission NIR analysis using a Cary 5000 UV-VIS-NIR double beam spectrophotometer (Agilent Technologies, Santa Clara, USA), equipped with a 30 Hz chopper beam Splitting System and a cooled PbS Photocell detector.
- –
Transmission NIR analysis using a Nicolet IS10 FT-IR Spectrometer (Thermo Scientific, Madison, WI, USA).
The spectra were recorded at a rate of 300 cm −1 min −1 and a data interval of 0.5 cm −1 for Cary and with 32 scans at a resolution of 2 cm −1 for Nicolet. The absorption intensity of peaks was measured after baseline correction in the 5000–8000 cm −1 region for both techniques. An initial high-resolution static spectrum of UDMA monomer allowed analysis of the peak area of the fully resolved methacrylate (=C–H first overtone absorption centered at 6164 cm −1 ) . The degree of conversion was calculated using changes in the molar ratios of polymer (P)/monomer (M) =C–H first overtone peak areas. Conversion was calculated by using the following equation:
% Conversion = 1 − P M × 100 ,
where P is the area of the peak absorbance of the =C–H UDMA polymer, and M is the area of the peak absorbance of the =C–H UDMA monomer. The results were analyzed by one-way ANOVA followed, if warranted, by Scheffe multiple mean comparisons (α=0.05), using PASW Statistics 18 (SPSS, USA).
2.3
Dynamic mechanical analysis
One part of each polymerized polymer block obtained was cut with a low-speed Isomet saw (Buehler, Lake Bluff, Il, USA) under water irrigation into 20 rectangular bars (1 mm × 4 mm × 20 mm), from which seven were randomly selected. Each sample was polished on an 800-grit SiC paper on a water-irrigated grinding wheel and stored at room temperature under dry conditions.
The viscoelastic properties of the polymers were determined via dynamic mechanical analysis (DMA) , operating in a three-point bending mode, using a RSA3 instrument (TA Instrument, New Castle, DE, USA). A static load of (0.3 ± 0.02) N was applied. The dynamic load was applied in the form of a sinusoidal wave with the corresponding static load being 10% higher than the dynamic load. The experiments were strain-controlled and maximum flexural strain has been maintained at 0.05% for the entire set of experiments. The dimensions of each sample were measured with a digital caliper (Mitutoyo Co, Kawasaki, Japan) before testing. Measurements were carried out each two degrees from 30 to 180 °C at a frequency of 1 Hz and a 10 mm spread of the three-point bending arrangement. The properties determined under this oscillating loading conditions were storage modulus ( E ′, at 32 °C), loss modulus ( E ″, at 32 °C), and damping factor (tan δ , at T g ). In DMA, E ′ is a measure of stored energy without phase difference between stress and strain and represents the elastic component of a viscoelastic material; E ″ is a measure of the energy lost as heat and represents the viscous component of a viscoelastic material; δ represents the phase lag between the applied stress and the corresponding strain in a viscoelastic material, while tan δ is the ratio (in percentage) of loss modulus to storage modulus ( E ″/ E ′) and is a measure of the energy dissipation, or damping. tan δ reaches a maximum as the polymer undergoes transition from the glassy to the rubbery state at the glass transition temperature, T g . From the DMA results, T g was determined as the position of the maximum on the tan δ vs. temperature plot. The value of T g is dependent on the degree of polymerization and crosslinking present in the analyzed polymer. In the rubbery plateau, the area above T g and before the melting temperature, at 170 °C, the storage modulus, <SPAN role=presentation tabIndex=0 id=MathJax-Element-8-Frame class=MathJax style="POSITION: relative" data-mathml='E′rub’>E′rubE′rub
E ′ rub
, was determined for each polymer. The value of <SPAN role=presentation tabIndex=0 id=MathJax-Element-9-Frame class=MathJax style="POSITION: relative" data-mathml='E′rub’>E′rubE′rub
E ′ rub
is dependent on the molecular weight between entanglements or crosslinks.
The normality of the distribution of the results was assessed using the Shapiro-Wilk’s test. The Levene test was used to compare variance across the groups. The results were analyzed by one-way analysis of variance (ANOVA) followed, if warranted, by Scheffé multiple-mean comparisons ( α = 0.05), using PASW Statistics 18.
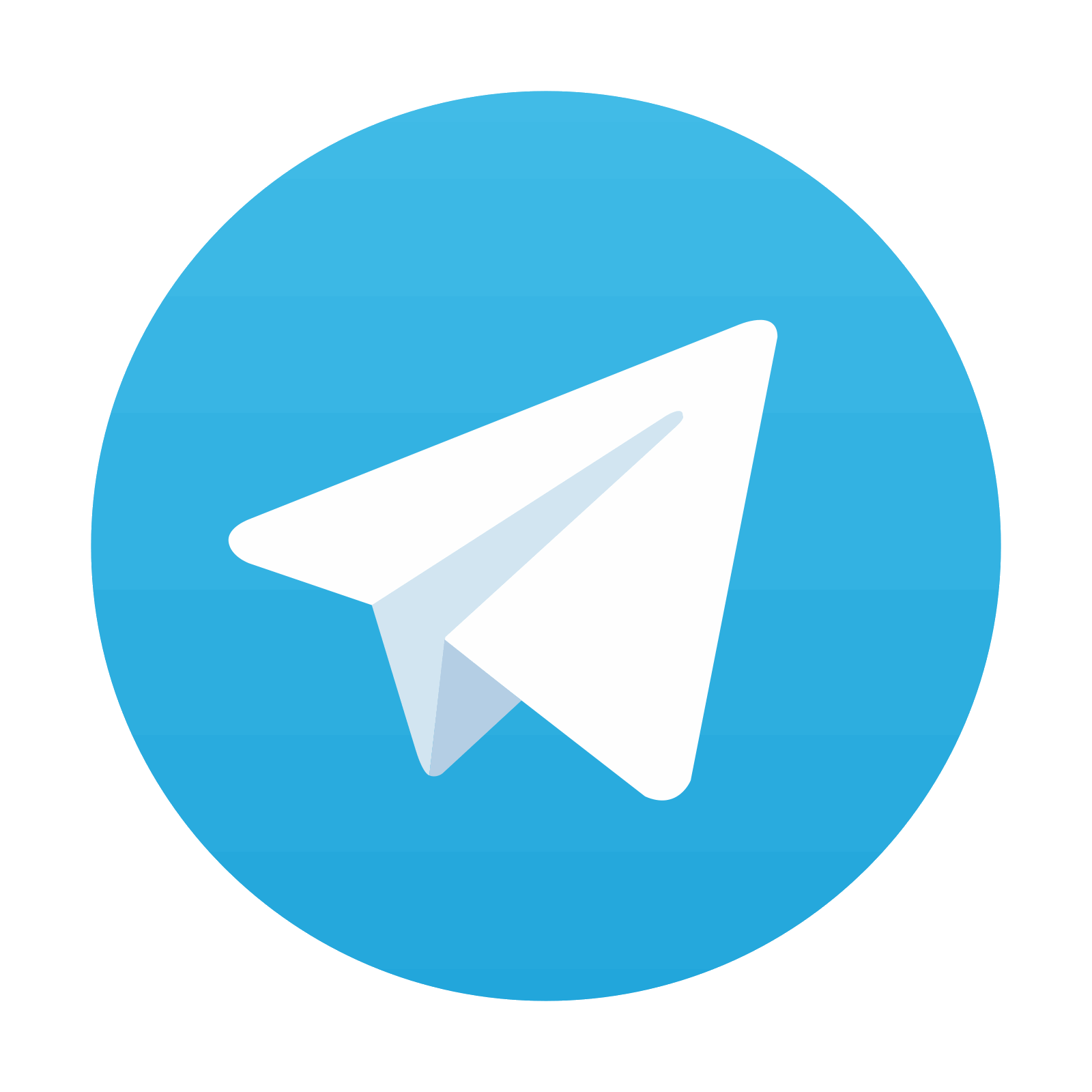
Stay updated, free dental videos. Join our Telegram channel

VIDEdental - Online dental courses
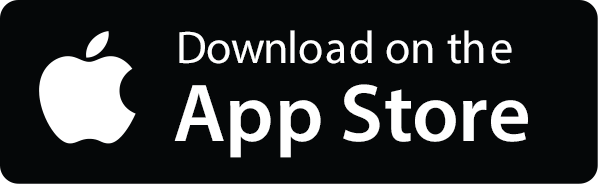
