Abstract
Objectives
This study aimed to investigate the collective influence of material properties and design parameters on the fracture behavior of monolithic dental crowns.
Methods
Three-dimensional (3D) models ( N = 90) with different combinations of design parameters (thickness, cusp angle and occlusal notch geometry) and material type (lithium disilicate, feldspar ceramic, zirconia, hybrid resin ceramic and hybrid polymer-infiltrated ceramic) were developed for the failure analysis using extended finite element method (XFEM) to identify the stress distribution, crack initiation load, fracture surface area and fracture pattern. Analytical formulation, in vitro fracture tests and fractographic analysis of dedicated models were also performed to validate the findings of the XFEM simulation.
Results
For all material types considered, crowns with a sharp occlusal notch design had a significantly lower fracture resistance against occlusal loading. In most of the models, greater crown thickness and cusp angle resulted in a higher crack initiation load. However, the effect of cusp angle was dominant when the angle was in the low range of 50° for which increasing thickness did not enhance the crack initiation load.
Significance
Comparing the critical load of crack initiation for different models with the maximum biting force revealed that for the studied monolithic materials excluding zirconia, a design with a rounded occlusal notch, 70° cusp angle and medium thickness (1.5 mm occlusal) is an optimum combination of design parameters in terms of tooth conservation and fracture resistance. Zirconia crowns exhibited sufficient strength for a more conservative design with less thickness (1.05 mm occlusal) and sharper cusp angle (60°).
1
Introduction
Monolithic dental crowns fabricated via computer-aided design and manufacturing (CAD/CAM) technology have been widely employed in prosthetic dentistry in recent years attributable to their high level of dimensional accuracy, marginal adaptation, mechanical properties and attractive optical characteristics . In addition, they present lower risk of lab processing errors and cohesive failure compared with classically veneered frameworks . Despite their many advantages, ceramic crowns are potentially susceptible to mechanical failure, possibly resulting in catastrophic fracture and chipping .
Mechanical performance of ceramic materials is dominated by their compositional and microstructural properties as well as the presence of defects and impurity phases. Accordingly, there has been continuous development of new CAD/CAM materials with enhanced mechanical properties through modification of composition and reduction of structural flaws. Currently, a variety of materials such as glass ceramics, zirconia, hybrid resin ceramics and polymer infiltrated ceramics are commercially available for constructing monolithic crowns in clinic . The most recently developed hybrid materials benefit from the structural and property combination of high strength ceramics and more compliant polymers .
Among these hybrid materials are heavily particle filled ceramic resin nanocomposites, polymerized under high-temperature (180–200 °C) and high-pressure (300 MPa) conditions in order to achieve a higher degree of conversion and polymerization as well as improved mechanical properties . A novel type of hybrid material is Enamic, which is a polymer infiltrated ceramic (PIC) material, developed through infiltration of a pre-sintered porous ceramic network (80% volume fraction) by the resin which fills the residual porosity of the ceramic and creates a dual network of ceramic and resin .
Not only do the clinical performance and durability of ceramic dental crowns depend on the physico-mechanical properties of the basic prosthetic materials, but are also determined by a range of clinical design parameters such as the thickness, preparation height, margin geometry, cusp inclination as well as the presence of surface irregularities and sharp features of the occlusal anatomy. Researchers have investigated different mechanical properties of CAD/CAM crown materials and the effects of design and preparation factors on the fracture behavior of the monolithic ceramic crowns in vitro .
Considering the variations in experimental methods and fabrication of specimens, however, systematic experimental and numerical studies are still needed to understand the collective role of structural variables and material properties (elastic modulus and toughness) in this process. Therefore, the current paper provides a comparative study using three-dimensional (3D) extended finite element method (XFEM) to explore stress distribution, crack initiation and fracture pattern of five types of monolithic dental crown materials with various clinical design parameters. Analytical formulation, in vitro fracture tests and fractographic analysis of dedicated models were also performed to validate the findings of the simulation study.
2
Materials and methods
2.1
Micro-CT scanning and development of finite element models
An extracted human premolar tooth (Ethics protocol No X12-0065 & HREC/12/RPAH/106) was imaged using a high-resolution desktop micro computed tomography system (Skyscan 1172, Skyscan N.V, Aartselaar, Belgium) at an accelerating source voltage of 100 keV, a source current of 100 μA, and an exposure time of 885 ms, resulting in 8.9 μm voxel size. The generated tomographic images were imported into ScanIP (Simpleware Pty. Ltd, UK) to segment the different anatomical parts of the tooth including enamel, dentine and pulp. Following surface refinement of the model components, the parameterized solid model was exported as an IGES file to SolidWorks (SolidWorks Corp., USA) to predominantly replace the enamel part of the tooth by a ceramic crown with a shoulder margin. Fig. 1 illustrates the various design variables of the crown models. Three cusp angles (50°, 60°, 70°) and three different crown thicknesses (thin, medium and thick) at different parts of the crown, including buccal, lingual and occlusal area ( Table 1 ), were adopted to construct different crown models.

Thickness | Margin thickness (mm) | Occlusal and Buccal-lingual thickness (mm) |
---|---|---|
Thin | 0.7 | 1.05 |
medium | 1 | 1.5 |
Thick | 1.3 | 1.95 |
Thickness | Thin | Medium | Thick |
---|---|---|---|
Margin thickness (mm) | 0.7 | 1 | 1.3 |
Occlusal and buccal–lingual thickness (mm) | 1.05 | 1.5 | 1.95 |
The cusp angle was defined as the angle between the slope of the cusp (blue dashed line in Fig. 1 ) and the vertical reference plane (red dashed line in Fig. 1 ). Two designs, namely a rounded (U) and a sharp (V) design ( Fig. 1 (a)), were considered for the occlusal features of the crown. The cement component of the model was created by offsetting the upper dentine surface by 0.1 mm in SolidWorks (SolidWorks Corp., USA). The assembly of different components, including the restorative crown, dentine, pulp, adhesive cement and the loading ball, are shown in Fig. 1 (b). During the assembly, the interfaces between the different components, including crown, cement and dentine, were assumed to be all bonded perfectly. The loading ball was carefully placed on the occlusal surface of the crown and was in frictional contact with both cusp slopes.
The finite element (FE) models were meshed using four-node linear tetrahedron elements. The mesh convergence test was conducted to determine the appropriate mesh size for the models by balancing the computational accuracy and cost . According to the convergence test, the global mesh size was 0.1 mm for the tooth/crown model and 0.8 mm for the loading ball; consequently, the corresponding number of elements was 259,294 (degree of freedom – DOF: 141,504) and 948 (DOF: 686).
The models were loaded using a 5 mm ball controlled by a downward force, linearly increasing from 0 to 10 kN. The loading ball was modeled to be a rigid body and the contact between sphere, and crown surface was assigned a friction coefficient of 0.3 . All the FE models were kinematically constrained on the bottom surfaces of the dentine and pulp , as shown in Fig. 1 (b).
2.2
Material properties of the components of the FE model
Five different types of the CAD/CAM materials were investigated in the study, namely (1) lithium disilicate (LDS) (e.g. Ivoclar, IPS e.max CAD), (2) feldspar ceramic (FC) (e.g. Vita, Mark II), (3) yttria stabilized tetragonal zirconia (Zr) (e.g. Ivoclar, E.max Zircad), (4) hybrid high-performance polymer (HPP) composite resin (e.g. GC Cerasmart), and (5) hybrid polymer-infiltrated ceramic (PIC) (Vita, Enamic). Table 2 summarizes the material properties for each component in the FE models. All the materials were considered to be isotropic and homogeneous .
Materials | Young’s modulus E (GPa) | Poisson’s ratio v | Tensile stress σ TS (MPa) | Fracture toughness K IC (MPa m 1/2 ) | Strain energy release rate G (J/m 2 ) |
---|---|---|---|---|---|
Lithium disilicate (LDS) | 98 | 0.23 | 210 | 2.27 | 52.6 |
Yttria stabilized tetragonal zirconia (Zr) | 204 | 0.27 | 865 | 5 | 122.5 |
Hybrid polymer-infiltrated ceramic network material (PIC) | 35 | 0.23 | 148 | 1.2 | 41.1 |
Feldspar ceramic (FC) | 72 | 0.22 | 112 | 1.25 | 21.7 |
Hybrid high-performance polymer composite resin (HPP) | 10 | 0.3 | 216 | 1.2 | 145.2 |
Cement | 8 | 0.3 | – | – | – |
Dentine | 20 | 0.31 | – | – | – |
Pulp | 0.01 | 0.49 | – | – | – |
The critical strain energy release rate G (J/m 2 ) is a key material parameter related to the fracture toughness K IC (MPa m 1/2 ), indicating the strain energy required to propagate unit area of crack extension, which can be calculated as follows:
G=KIC2E
where E is the Young’s modulus and K IC is the fracture toughness of the material.
2.3
Extended finite element method (XFEM)
In the present study, the XFEM fracture analysis was conducted to simulate the initiation and propagation of cracks in the dental crown using Abaqus 6.14 (ABAQUS, Inc, Providence, RI). The cracking criterion used was the maximum principal stress in terms of:
fe=(σ1e)σmax0
where <SPAN role=presentation tabIndex=0 id=MathJax-Element-3-Frame class=MathJax style="POSITION: relative" data-mathml='σmax0′>?0maxσmax0
σ max 0
refers to the allowable maximum stress (fracture strength) of the CAD/CAM materials, <SPAN role=presentation tabIndex=0 id=MathJax-Element-4-Frame class=MathJax style="POSITION: relative" data-mathml='σ1e’>?e1σ1e
σ 1 e
is the first principal stress in element (e), and f e represents the stress ratio, which determines if cracking will initiate in the element. A crack was assumed to occur when the maximum principal stress in tension exceeds the pre-defined tensile strength of the material. The subsequent crack growth was associated with the strain energy release rate . The cracking region was only considered for the crown part in the XFEM models . Detailed background information about the mechanics of XFEM fracture analysis can be consulted in the literature .
2.4
Crack surface area determination
Fracture simulation results were post-processed using an in-house developed program to determine the exposed area of a crack. Measuring this parameter at every timeframe of simulation provided a means for quantitative assessment and monitoring of crack evolution in the 3D crown models, which are outlined as follows. First, each element of the model was interrogated to determine the subset for which the Abaqus output STATUSXFEM is equal to one. In the XFEM analysis, STATUSXFEM defines the state of the crack in each model. Specifically, a value of 0 represents an undamaged element; a value between 0 and 1 indicates that the element is damaged but is still able to withstand some traction forces; and a value of 1 shows that there is full fracture failure in the element with no traction force remaining, which also corresponds to the occurrence of the crack in the model. Second, for the given mesh type, i.e. linear tetrahedral in this study, the nodal level-set quantity that defines the cracking surface was interpolated throughout the elements to locate the zero crossings. Elements bisected by the crack would have three or four such crossings. Third, the crack surface was obtained as the union of all the elemental zero crossings.
2.5
Fabrication of monolithic ceramic crowns and compression testing
An in vitro experiment was dedicated to the tests of the monolithic crowns to validate the XFEM simulation results. The STL files of the crown models, created in SolidWorks (Dassault Systèmes SolidWorks Corp., USA), were used by a dental milling system to fabricate PIC (Enamic) and Zr (Zircad) crowns. A 3D printing system was used to fabricate the die parts for supporting the crowns during the physical experiment using STL files of the die models generated in SolidWorks (Dassault Systèmes SolidWorks Corp., USA).
The fabricated crowns were cleaned and checked for any defects. The abutment dies were then etched with 37% phosphoric acid for 20 s, in order to produce the highest bond strengths to ceramic crowns. Finally, the crowns were cemented on the dies using a dual cure cement (Total C-ram, ITENA CLINICAL, France). The margins of each crown were light-cured (Satelec Mini L.E.D) for 20 s on each tooth surface. Eighteen pre-molar crowns bonded to the abutments were tested in a universal testing machine (Instron 5965; Instron, Canton, MA) using a 4 mm diameter steel cylindrical bar at a cross head speed of 1 mm/min until fracture took place. This approach for testing all-ceramic premolars was initially developed by Burke and Watts .
3
Results
The influence of material properties and selected design variables on the fracture characteristics of crown models including maximum principal stress, crack formation pattern, crack initiation load and crack surface area are presented in the following sections.
3.1
Maximum principal stress
Maximum principal stress (MPS) criterion postulates that the crack will initiate if the MPS in the crown exceeds the pre-defined value and the crack will grow in a direction perpendicular to the MPS to release the maximum strain energy . During the simulation the MPS contours in the crown models were extracted at the same time point so that the corresponding load values were equal for all the models.
Three regions were the most commonly observed areas of stress concentration within the crowns ( Fig. 2 ), which included the occlusal notch, areas adjacent to the contact points between the loading ball and crown surface, as well as the intaglio (internal) surface of the crown specifically in the occlusal area. Fig. 2 (a) shows the MPS distributions of two representative crown models (50° cusp angle, medium crown thickness and similar material properties) with two different occlusal notch designs (rounded U-shape and sharp V-shape, respectively). Accordingly, at a normal load of 150 N on the ball, the rounded notch design presented a lower peak MPS (86.94 MPa) compared to the model with a sharp notch (101.83 MPa). Coronal and sagittal views of the stress contours indicated that the rounded notch design, had a more even stress distribution in the entire crown and a reduced stress concentration in the central occlusal notch ( Fig. 2 (a)).

Fig. 2 (b) depicts the principal stress distributions for three crown designs with the same thickness (medium), notch design (rounded) and material properties but different cusp angles, i.e. 50°, 60° and 70° It was found that the model with 50° cusp angle had the highest peak MPS value (17.75 MPa), followed by the models with 60° (15.96 MPa) and 70° (8.98 MPa) cusp angles under the same loading.
Not only did changing the cusp angle affect the magnitude of MPS, but also altered the distribution pattern of MPS in the crowns as shown in Fig. 2 (b). While with a cusp angle of 50° (steeper cusps), MPS was mainly concentrated in the central groove area; the increase of the cusp angle to 60° (decreasing the steepness) resulted in a wider distribution of the MPS and its extension to the secondary occlusal grooves. Further increase in the cusp angle to 70° led to a more evenly distributed stress pattern, which almost eliminated the stress concentration from the central groove ( Fig. 2 (b)).
Fig. 2 (c) shows the effects of crown thickness (thin, medium and thick) on the MPS magnitude and distribution pattern of the three representative crown models with a rounded notch, 50° cusp angle and the same material properties. In general, a greater thickness decreased the MPS value and generated smaller stress concentration areas in the crown. In the thick crowns, there was a shallow stress concentration area close to the occlusal notch surface; while in the thin crowns, the stress concentration area had a higher magnitude and extended to the internal surface of the crown.
Fig. 2 (d) shows the maximum principal stress (MPS) contours for the two nominated crown models with the same design parameters (50° cusp angle, rounded notch and medium thickness) but different material properties (HPP with a Young’s modulus of 9.92 GPa and a toughness of 1.2 MPa m 1/2 ; and Zr with a Young’s modulus of 204 GPa and a toughness of 5 MPa m 1/2 ). While the peak MPS for the crown was strongly affected by the material type, the stress distribution pattern was not noticeably different among various groups of materials. Accordingly, the peak MPS value at 130 N load exhibited an increasing rank for HPP (8.73 MPa), PIC (15 MPa), FC (16.95 MPa), LDS (17.75 MPa), and Zr (21.05 MPa) respectively, with central groove being the main stress concentration area in all these material groups ( Fig. 2 (d)).
3.2
Crack initiation load
Fig. 3 shows the crack initiation loads for the models made of the same material but with various cusp angles, notch designs and thicknesses. It was observed that in general, the crack initiation load rises with the increase in the cusp angle for different crown designs and material types. In most of the models, the increase in crack initiation load was more significant when the cusp angle increased from 50° to 60° compared to the increase from 60° to 70°. The effect of increasing cusp angle was less prominent in the thin crowns, in which a higher cusp angle did not significantly enhance the fracture resistance of the crown.

Concerning the effect of occlusal notch design, the rounded notch geometry led to a higher load of crack initiation compared to the sharp notch for all the study materials. This effect was minimal in the thin crowns but more significant in the thick crowns, in which the crack initiation load almost doubled in the rounded compared to the sharp notch design.
Crown thickness was a key determinant of the fracture resistance in all the materials and it had a direct relationship with the crack initiation load. Accordingly, a greater crown thickness resulted in a higher load of crack initiation in different models. However, the effect of cusp angle was dominant when the angle was in the low range of 50° for which increasing the thickness did not enhance the fracture initiation load.
In addition to various design parameters, material properties also had a significant effect on the crack initiation loads and fracture resistance of the crowns ( Fig. 3 ). Accordingly, the zirconia (Zr) crown models had the highest crack initiation load, followed by the LDS glass ceramic, HPP, PIC and feldspathic material (FC), respectively.
3.3
Crack surface area
The evolution of the crack surface area with increasing load for nominated crown designs and materials are presented in Fig. 4 . For different crown designs and materials, the crown models with the least thickness demonstrated increased crack surface area at the lowest load value compared to the medium and high thickness models ( Fig. 4 (a)). The increased crack area at a lower load value was also observed for the crown models with sharp occlusal notch geometry compared to the rounded notch design ( Fig. 4 (b)).

For the effect of cusp angle, a more acute angle led to a lower load at crack initiation, and a generally greater crack area for a given load. For instance, at a load value of 1400 N, the model with 50° cusp angle already had catastrophic fracture with a crack area of 0.4 mm 2 and the crack surface area for the 60° cusp angle was under 0.2 mm 2 ; whilst there was no crack in the model with 70° cusp angle ( Fig. 4 (c)).
Regarding the effect of material type, FC was found to initiate cracking at the lowest load, followed by PIC, HPP, LDS and Zr, respectively. FC was the most brittle in the simulations, demonstrating a large increase in the crack surface area when there was a relatively small increase in the applied load ( Fig. 4 (d)).
3.4
Crack pattern
The crack growth in all the investigated models was found to be stable, in which the crack was initiated at a lower load then progressively extended with increasing load until final fracture of the crown. The crack pattern and location for a representative model (PIC, rounded occlusal notch, medium crown thickness and 60° cusp angle) at different time points during the simulation (crack initiation, and propagation) are presented in Fig. 5 . In most of the crown models, the crack originated on the occlusal surface from the base of the occlusal notch where the stress concentration was the highest ( Fig. 5 (a)). It then propagated along the length of the primary groove until it reached the proximal margins ( Fig. 5 (b)), after which it grew in a downward direction and extended through the entire thickness of the crown ( Fig. 5 (c)). According to the simulation results, the location of the crack was not affected by changing the crown thickness, notch design and material properties. However, for some very resistive crown models, e.g. with a high cusp angle, greatest thickness and rounded occlusal notch, the crack initiation and extension occurred in the fissural area but at a point closer to the loading point ( Fig. 5 ).

Examination of the fracture surfaces of the in vitro tested crowns with scanning electron microscope (SEM) revealed multiple hackle lines, crack propagations and arrest lines in the fractured specimens. Fracture origins were identified in the fissure region as well as below the loading contact area at the occlusal surface of the crown with associated radiating hackle lines converging on this point ( Fig. 6 ). Multiple arrest lines were observed especially in fractured hybrid ceramic crowns, indicating higher fracture compliance compared to the zirconia crowns.

3.5
Experimental validation of the XFEM results
Fig. 7 (a) compares the force–displacement curves of the numerical (red line) and experimental (blue line) studies; and Fig. 7 (b) compares the fracture load values among experimental, numerical and analytical results for a nominated crown model (PIC, medium thickness, 60° cusp angle and rounded notch design).

In the experimental force–displacement curve (in blue), the first major drop in the force was recorded at the crack initiation stage. At the final stage of the experiment, the loading force dropped suddenly when it reached the ultimate strength of the crown structure, in which the sample experienced complete bulk failure. According to the simulation results, the premolar crown model exhibited almost linear force–displacement behavior with relatively small load drops prior to the catastrophic failure. Comparing the XFEM simulation with the experimental test, good correlation can be identified in the fracture patterns, in which both the experimental and simulated cracks initiated from the bottom of the central occlusal fissure, and then propagated toward the proximal margins and proximal surfaces of the crown.
The simulated crack initiation load and total failure load also exhibited reasonable agreement with the experimental results. It should be noted that since a loading ball was used for the simulation part of the study, the authors initially tried using a steel ball for the laboratory experiment as well. However, lack of stability of the ball on the premolar cuspal slopes, led to the selection of a cylinder for the experiment. Further validation of the simulation results was performed to estimate the effect of the difference in the loading element; and it was found that the XFEM results were very similar in terms of the crack initiation load (<6%) and final failure load (<8%) for the same model loaded with either a ball or cylinder (Appendix 1). Likewise, the fracture path was also almost identical for these two cases.
4
Discussion
Computational methods have compelling benefits for the fracture study of brittle materials with complicated geometry, such as dental crowns. This is because the issues caused by asymmetry and misalignment of specimens in experimental settings cannot be compensated by small amounts of plastic deformation as happens for ductile materials; therefore potentially causing uncontrolled fracture behavior and associated scatter of testing results in such experiments . In the present study, an in-silico computational modeling approach called eXtended Finite Element Method (XFEM) was adopted as it has been shown to have high predictive ability in forecasting the fracture behavior of complex structures. A key advantage of XFEM for fracture studies is its independence of the element mesh from the morphology of the crack surface and crack front . This eliminates the need for remeshing during crack propagation and therefore enables convenient simulation of crack evolution.
The developed XFEM model for quantifying the crack surface area also provided an accurate approach for observing the evolution of the crack through different stages including crack initiation, stable propagation and final catastrophic failure. For some of the cases, the crack surface area showed a steady or gradual growth following crack initiation (see Fig. 4 ), indicating the fracture resistance of the structure to the localized ball loading condition and restriction of the crack propagation. With increasing loading, there was usually a significant final jump in crack extension for most of the models ( Fig. 4 ), which indicates catastrophic crack propagation; and the corresponding load values were deemed the fracture load. The simulated fracture load obtained from the quantification of XFEM crack surface area also showed strong correlation with that obtained from the experimental testing of the crowns.
As shown in Fig. 2 , stress concentration was more evident in three regions within the crowns, which were the occlusal notch, areas adjacent to the loading contact points, as well as the intaglio surface of the crown particularly in the occlusal area. The locations of these stress concentration areas identified in the simulation ( Fig. 2 ) correlate well with the common areas where different types of cracks develop in structurally failed crowns . Accordingly, while splitting cracks mainly initiate in the central occlusal fissure, it is observed that contact-driven Hertzian cracking can develop beneath the contact points with the loading body (opposing tooth or the indenter). Tensile stresses at the internal surface of the crown generated from the flexure of the crowns under occlusal loading also cause flexural radial cracking, starting at the crown internal surface and growing toward the occlusal surface or the margins of the crown . Although the competitive distribution and magnitudes of stresses among these regions depends on the geometrical parameters of the crowns, the observed fracture mode in our study was predominantly the splitting bulk fracture (mode I). The crown material properties would mostly have an effect on the magnitude, but not on the distribution pattern of the MPS among the different models.
In addition to the thickness, cusp angle and notch design, two other interesting anatomical features were also found to play a key role in increasing the fracture resistance of the crown models. First, the proximal marginal ridge on both sides of the crown demonstrated a reinforcing and resistive role against splitting of the crown through confining the propagation of the splitting crack ( Fig. 5 (c)). In general, propagation of the crack along the primary groove arrested when it reached the marginal ridge, where it changed direction and grew downward. Apparently, lack or weakness of proximal ridge may be a potential factor in facilitating the splitting fracture of the crown. This highlights the importance of optimum design for the thickness and height of the marginal ridge area in restorative crowns considering that the marginal ridge is also the location of contact with the opposing cusp tips in the posterior teeth. Second, occlusal fissures also contributed to distributing and directing the stress away from the primary groove and toward the buccal and lingual cusps of the crown, therefore diminishing the stress concentration in the central primary groove ( Fig. 2 ).
Regarding the effect of occlusal notch geometry on the fracture resistance of the crown, the XFEM results confirmed that the presence of a sharp occlusal notch caused a higher stress concentration and significantly lower crack initiation load for all the materials, crown thicknesses and cusp angles considered in this study. As shown in the previous in vitro experiments , a rounded and curved notch morphology allows the stress to distribute more evenly and over a wider surface area, thereby preventing the concentration of the stress in the notch area.
Any surface irregularity including the sharp occlusal notch can be considered as a discontinuity in the microstructure of the material which can predispose the crown to crack initiation. This highlights the need for careful consideration by technicians and clinicians during the design, fabrication and occlusal adjustment of the crowns to avoid the generation of any surface irregularities or sharp points .
The cusp angle also played a significant role in the fracture resistance of the crowns, which affected the MPS distribution, crack initiation load and crack surface area to different extents in different models. Similar to the findings in the previous laboratory experiments , decreasing the cusp angle resulted in lower crack initiation load and fracture resistance and caused a more localized MPS distribution. This can be attributed to the increase of the lateral force component of the applied load and the resultant tensile stress around the occlusal notch area. The effect of a low cusp angle was a dominant factor and generally, it could not be compensated by changing the material type and/or increasing the crown thickness.
By comparing the average maximum bite force (800 N in the posterior region ) and the crack initiation load from each model, we could detect the safe cusp angle for a specific combination of material type and crown thickness. Accordingly, a steep cusp angle of 50°, resulted in a crack initiation load lower than the maximum bite force (800 N) for all the materials and thicknesses, except for medium to high thickness zirconia crowns with a rounded notch design that had crack initiation loads of 939 N and 1174 N, respectively.
At a cusp angle of 60°, only the crown designs with greater thickness and rounded notch were within the safe range of the load values for FC (853 N) and PIC (927 N). However, with increased material toughness in HPP, LDS and ZR, the medium thickness designs also achieved a higher crack initiation load than the maximum bite force of 800 N. While increasing the cusp angle from 60° to 70° in the medium thickness designs could bring the crack initiation load of FC and PIC crowns close to the maximum bite force, it was still below the maximum bite force (394 N for FC and 428 N for PIC) for their low thickness designs. These findings confirm the idea that a safe cusp angle could become steeper when the fracture toughness of the crown material increases .
Crown thickness is a key clinical parameter during the preparation of the full coverage restorations; and clinicians commonly aim to achieve the most conservative yet strong design for the crowns. This issue is of more importance to the posterior crowns where higher occlusal forces and loading contacts are typically imposed on the teeth. In the current study, the thickness displayed a considerable effect on the fracture resistance of crowns, with a higher thickness resulting in decreased stress concentration and a more even distribution of the MPS in the crowns ( Fig. 2 (c)). The thickness of the crown also revealed a direct relationship with the crack initiation load in most of the models except for the models with low cusp angle (50°), where there was no significant difference among the crowns with different thicknesses ( Fig. 3 ).
The relation between failure load and design variables, including crown thickness ( T ), notch design and cusp angle ( θ ), can be considered in terms of the stress intensity factor ( K I ). As the geometry of a monolithic crown is rather complex, it is challenging to estimate the stress intensity factor directly. According to the studies by Barani et al. and Sornsuwan and Swain , the splitting configuration might be likened to the mode I compact tension (CT), which assumes the notch as a crack. The expression of stress intensity factor for standard C-shape CT model, shown in Fig. 1 (a) and Fig. A1 (Appendix 2) can be written as :
KI=FWBπa⋅YCTWR,XW,A⋅g(A)
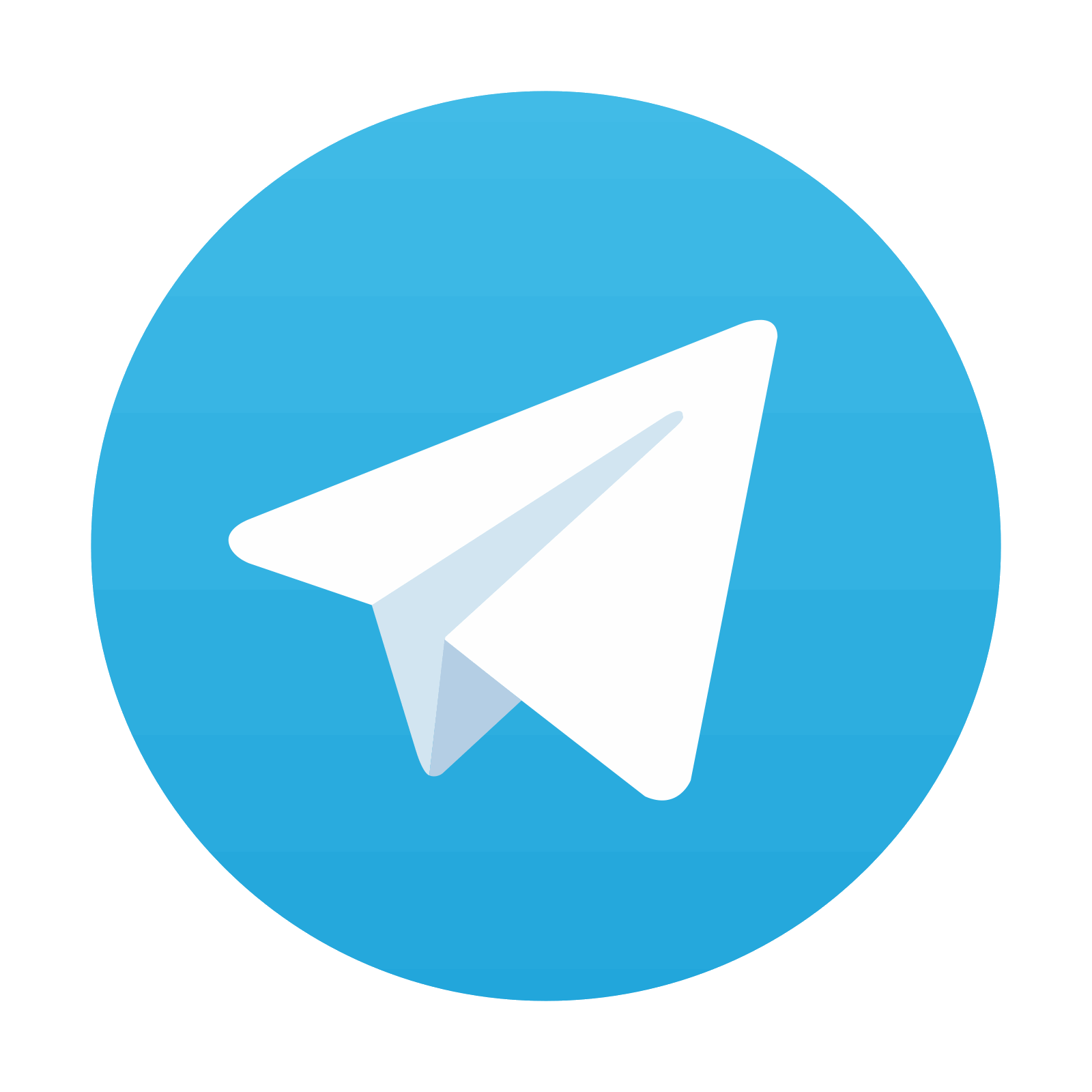
Stay updated, free dental videos. Join our Telegram channel

VIDEdental - Online dental courses
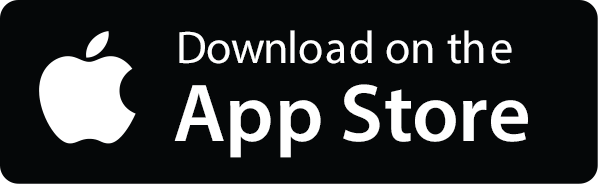

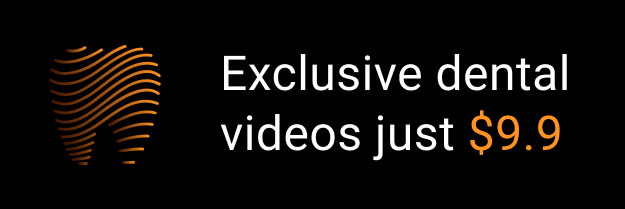