Abstract
Objective
Due to past failures of orthopedic 3Y-TZP femoral implants linked to accelerated tetragonal-to-monoclinic phase transformation ( t → m ), the susceptibility to ‘low-temperature degradation’ or ‘ageing’ of 3Y-TZP has been advertised as detrimental to its long-term structural stability. However, no systematic mechanistic experiments on the fatigue resistance of aged 3Y-TZP under cyclic loading can support such statement. In this study, we aim to clarify this issue.
Methods
Here we evaluate the subcritical crack growth behavior of 3Y-TZP under cyclic loading after 0–50 h of accelerated ageing in an autoclave at 134 °C. The same 3Y-TZP sintered at two different temperatures (1450 °C or 1650 °C) allows for the comparison of materials containing grains with different susceptibilities to transformation. The volume fraction of surface transformed grains was measured using Raman spectroscopy, and the depth of the transformed surface layer from trenches milled with a Focus-Ion Beam. The fracture toughness before and after ageing was determined using the Chevron-notch Beam method. The quasi-static flexural strength was measured in dry conditions and the cyclic lifetime in water at 10 Hz and R-ratio = 0.3 in 4-point-bending at different applied stresses. The fatigue parameter n was derived from 3 different methods, namely S N curves, crack velocity plots and Weibull distributions.
Results
The progression of transformation showed linear kinetics with higher rates for the 3Y-TZP sintered at 1650 °C. Accelerated transformation induced severe crack formation within the transformed layer with parallel orientation to the surface plane, which supposedly behaved as the critical crack size population governing fracture. The stress intensity factor within the transformed layer was increased due to compressive stresses. Consequently, the fatigue parameter n increased consistently from 5 to 50 h of ageing, regardless of the derivation method, suggesting an increased resistance against crack growth during cyclic loading in bending.
Significance
Our results do not support the long suggested negative clinical implications of LTD regarding mechanical performance, to the contrary, LTD seems to increase the resistance against subcritical crack growth in a humid environment in bending.
1
Introduction
Dental zirconia, more specifically 3 mol%-stabilized zirconium dioxide, is suffering from a reputational crisis. A crisis involving the metastability of the tetragonal ( t ) phase, precisely the property accounted for the transformation toughening mechanism that provides resistance against crack initiation and growth, once conferring zirconia the stature of ‘ ceramic steel ’ [ ]. It was later on observed that, in a diffusion-controlled chemical reaction, the transformation back to the stable monoclinic ( m ) allotrope (i.e. t → m ) seem to occur in the presence of moisture at temperatures as low as room and body temperatures, a phenomenon coined Low-Temperature Degradation (LTD), or alternatively Hydrothermal Ageing . Supposedly, oxygen anions dissociated from water molecules destabilize tetragonal grains by occupying free vacancies in the lattice [ ]. Starting at the surface, the stress induced by the volume increase associated with the t → m transformation triggers a nucleation-and-growth process [ ] ‘infecting’ neighboring grains in a slow but continuous event into the subsurface.
LTD is generally seen as a malignant process since an abnormal large amount of medical grade zirconia femoral heads fractured in service in the early 2000’s at much shorter lifetimes than expected. Analyses of retrieved pieces revealed advanced signs of LTD which, associated with the concomitant mechanical wear process, poorly sintered batches [ ], and surface machining residual stresses, were accredited as the underlying causes of the observed premature mechanical deterioration [ ]. It has been since then demonstrated that morphological alterations begin at the nanometric scale by means of grain roughening und micro-cracking, up to macroscopic ramifications, like grain pull-out and surface pitting. The prominence of the case of the hip-joint prostheses snowballed in a rush of scientific interest aimed to understand how exactly LTD operates, and how it can endanger the reliability of zirconia as a biomaterial. Experiments have found that a handful of factors affect the susceptibility and evolution rate of LTD, mainly: (i) grain size (controlled mainly by sintering temperature) [ ]; (ii) amount and type of alloying oxides (Y 2 O 3 , CeO 2 , Al 2 O 3 ) [ ] and; (iii) initial amount of cubic phase in the as-sintered material [ ].
Despite the intense research efforts, the mechanical implications of LTD are not yet set in stone. Some mechanical testing has shown a negative effect of LTD on bending strength [ , ], while others found the opposite [ , ], including tests in actual dental implants [ ]. The effects of LTD on strength are related to the zone of compressive (strengthening) stresses generated by the transformation itself, the tensile (weakening) stress zone generated underneath the transformed zone [ ], and how this change in stress state affects the natural defect population of the material. It all seems to depend on how far LTD is let on to evolve [ ].
It is however the mechanical significance of LTD on the long run that remains elusive. This is based on the general scarcity of experiments that probe the crack growth behavior of LTD-degraded zirconia systematically under relevant (cyclic) loading conditions. Exemplary, in the recent review by Chevalier et al. [ ] – an ensemble of a >15 years body of work on LTD- there is not a single mention of such an experiment. Despite that, authorities in the field seem to recommend LTD be avoided altogether [ , ]. Here we append isolated attempts to address this issue.
Through extensive cyclic loading experiments, we aim to clarify if and to which extent the LTD t → m transformation negatively affects the crack growth behavior during cyclic loading. For that effect to be highlighted, one 3Y-TZP material was sintered at different maximum temperatures, inducing microstructures (grain growth) that are susceptible to the t → m transformation at different degrees. By increasing the LTD time, we intend to provide a relationship between extent of transformation and the cyclic fatigue parameter n in bending. Based on the negative reputation of LTD regarding mechanical degradation suggested in the literature, we hypothesize that increasing sintering temperature and LTD time, will accelerate crack growth rates accordingly (decrease in the n -value).
2
Materials and methods
2.1
Materials and characterization
A 3 mol% Yttria-stabilized tetragonal zirconia polycrystal (3Y-TZP) was obtained from a single manufacturer (IPS e.max ZirCAD, Ivoclar-Vivadent, Liechtenstein). The material is supplied in a partially-sintered state as blocks of 15.5 × 19 × 39 mm 3 intended for computer-aided manufacturing, and undergoes a final sintering step with shrinkage of approx. 20 vol.%. All specimens in this study were fabricated by cutting these blocks with a diamond coated saw under water irrigation in oversized specimens to compensate for shrinkage. In order to obtain two variations of the same 3Y-TZP material with different degrees of susceptibility to LTD, two target sintering temperature were chosen: 1450 °C or 1650 °C (200 °C/h heating rate, 2 h at the maximum temperature and overnight cooling in the oven). Specimens of each sintering temperature were further assorted into four different experimental groups, subjected to increasing periods of LTD (ageing) in an autoclave at 134 °C and 2 bar pressure, namely for 5, 20 or 50 h, with a non-aged group (as-sintered, 0 h) as control.
The fraction of t → m transformed grains was quantified using Raman spectroscopy by acquiring Raman signals with a Thermo Scientific Nicolet™ Almega Raman spectrometer coupled with a Olympus microscope and high-resolution grating. The single spectra were collected with an Ar + laser excitation at 532 nm through a 50× objective with a 100 μm pinhole aperture in 5 successive measurements of 60 s integration time each (n = 5). Spectra were normalized to the total area in the frequency range, after subtraction of a linear background. The volume fraction of monoclinic phase V m , was calculated as recommended in Ref. [ ]:
Vm=Im176+Im1880.32It147+It256+Im176+Im188
where the intensities of the tetragonal peaks at 147 cm −1 and 256 cm −1 , and of the monoclinic peaks at 176 cm −1 and 188 cm −1 , were calculated as the integrals of the Gaussian-Lorenzian fits for each of the peaks of interest using a dedicated software (LabSpec®).
Sputter-coated samples were observed in a scanning electron microscope (SEM, Auriga, Carl Zeiss AG, Germany) for microstructural characterization. Grain size distribution was performed using SEM images of 5 different specimens in a dedicated software tool (ImageJ). The depth of the degraded layer was determined by FIB-milling in a SEM dual beam station Neon 40 (Carl Zeiss AG), where FIB trenches were milled and polished after the deposition of a protective Pt strip. The exposed subsurface layer at 90° to the surface was observed at a tilt angle of 36°, and the transformed layer thickness ( TLTm ), evidenced by stripped pattern of transformed grains and microcracking, was measured following appropriate geometrical corrections.
2.2
Monotonic and cyclic loading experiments
Specimens for inert flexural strength (n = 30) and flexural cyclic fatigue (n > 50) had final dimensions of (height W × width B × length L ) of 2 × 2.5 × 25 mm 3 , with ± 0.05 mm tolerance. The bending surface of the beams was polished (wet, P2500 SiC paper) still in the pre-sintered state and not further treated after sintering (mean R z = 0.8 ± 0.2 μm). Immediately before testing of the inert strength, the specimens were dried in an oven for 3 h at 150 °C and subsequently immersed in silicon oil (also dried in the oven to avoid thermal shock) in an attempt to remove any surface water from the specimens and provide for an inert environment during testing. The uniaxial flexural strength was determined using a 4-point ¼-point bending fixture (10/20 mm spans, see Fig. 4 a) having fully-articulated support and loading rollers. Specimens dimensions were determined with 0.002mm precision using a digital caliper. Testing was carried out in a pneumatic universal testing machine (Dyna-Mess Prüfsysteme, Stolberg, Germany), at a cross-head speed of 0.1 mm/s (specimens fractured within 5–10 s). The flexural strength was calculated using standard bending relations and treated using Weibull statistics.




Cyclic loading was conducted in the same equipment and bending fixture in water at room temperature,at at a frequency of 10 Hz and R-ratio (R = σ min / σ max ) set to 0.3 in a sinusoidal loading profile. The maximum applied stress σ max was set to a fraction of the characteristic strength determined under inert conditions, between 0.45 σ 0 and 0.80 σ 0 , in at least four different stress levels for each experimental group, with with 30 specimens being tested in at least one stress level. Experiments were interrupted at 4 × 10 6 cycles for survivals, and ended altogether when at least 5 specimens survived per group. The number of cycles to failure was used to derive the subcritical crack growth susceptibility parameter n , which describes under cyclic loading conditions the cumulative effect of water-assisted stress corrosion (responsible for slow crack growth in silicate and oxide ceramics [ ]) and the degradation of crack shielding mechanisms during periodic loading and unloading load profiles. The higher the n -value, the lower is the susceptibility to slow crack growth. To obtain the n -values, three methods were used, namely, the construction of S—N and d a /d N – K I curves [ ], and from the Weibull distributions.
Specimens for fracture toughness measurement were prepared in oversized dimensions to obtain beams of 4 × 3 × 25 mm 3 after sintering to be tested using the Chevron-notch Beam (CNB) method according to the standard ASTM C1421 [ ]. V-shaped notches were sawed with a 0.15 mm-thick diamond disc in the specimens still in the pre-sintered stage, as described in Ref. [ ]. After sintering according to the two aforementioned maximum temperatures, five to seven specimens were assigned to the experimental groups to be subjected to the accelerated ageing protocol described above. Before testing, the specimens were dried in an oven at 150 °C for 3 h and dipped in dried silicon oil. Specimens were tested at a displacement rate of 0.01 mm/s in a 4-PB configuration (10/20 spans) with load-line displacement controlled by an image system (LaserXtens, Zwick/Roell, Germany) based on the image digital correlation approach for accurate detection of the stable crack growth at the tip of the notch before instability (see Fig. 4 b). The fracture toughness was calculated with the solutions provided in the standard:
KIc=FmaxSo-SiBW3/2×Ymin103,
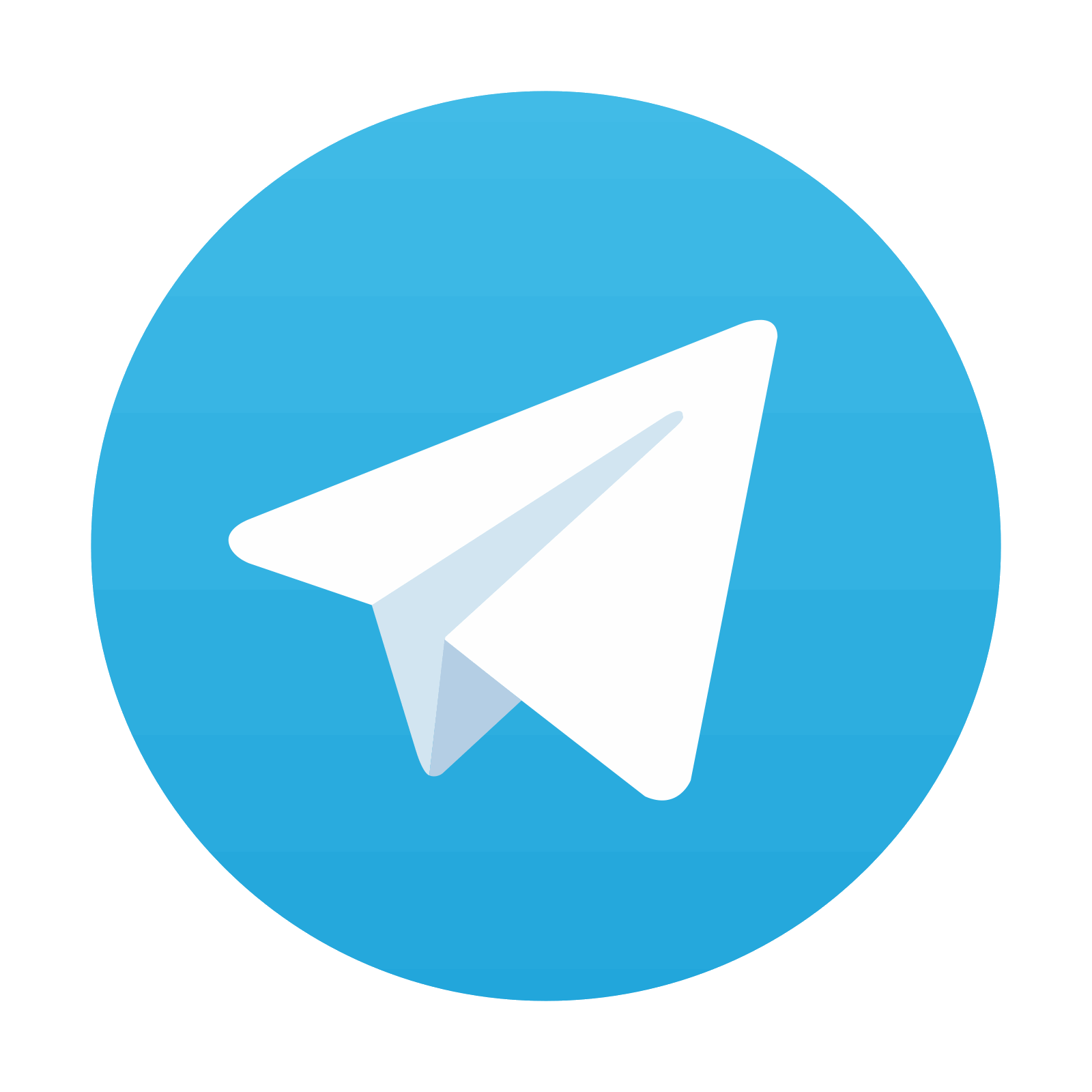
Stay updated, free dental videos. Join our Telegram channel

VIDEdental - Online dental courses
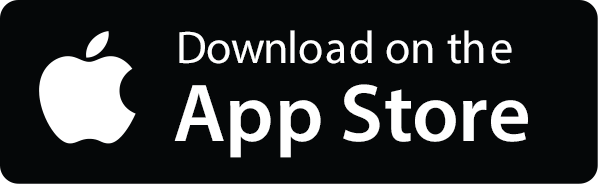

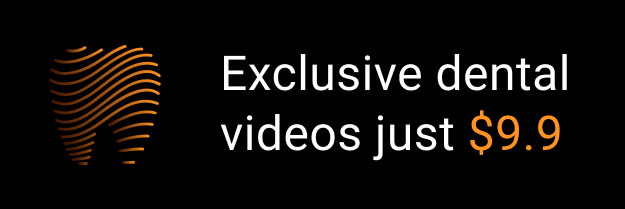