Highlights
- •
We studied the effect of various thermal processing on the crystallization kinetics, crystallite microstructure, and strength of a lithium disilicate system.
- •
The growth of Li 2 O–2SiO 2 crystals was independent of the overall heating time but dependent on a minimum temperature threshold.
- •
The lithium disilicate system formed three evolutionary stages through controlled devitrification via distinctive heating schedules.
- •
Each stage yielded a principal microstructure that possessed interesting, sometimes peculiar, combinations of glassy-crystalline properties.
- •
Groups heated above the minimum temperature threshold exhibited improved flexural strength, fracture toughness, and elastic modulus.
Abstract
Background
Elucidating the microstructural responses of the lithium disilicate system like the popular IPS e.max® CAD (LS 2 ), made specifically for computer-aided design and computer-aided manufacturing (CAD-CAM), as a temperature-dependent system unravels new ways to enhance material properties and performance.
Objective
To study the effect of various thermal processing on the crystallization kinetics, crystallite microstructure, and strength of LS 2 .
Methods
The control group of the LS 2 samples was heated using the standard manufacturer heating-schedule. Two experimental groups were tested: (1) an extended temperature range (750–840 °C vs. 820–840 °C) at the segment of 30 °C/min heating rate, and (2) a protracted holding time (14 min vs. 7 min) at the isothermal temperature of 840 °C. Five other groups of different heating schedules with lower-targeted temperatures were evaluated to investigate the microstructural changes. For each group, the crystalline phases and morphologies were measured by X-ray diffraction (XRD) and scanning electron microscope (SEM), respectively. Differential scanning calorimeter (DSC) was used to determine the activation energy of LS 2 under non-isothermal conditions. A universal testing machine was used to measure 3-point flexural strength and fracture toughness, and elastic modulus and hardness were measured by a nanoindenter. A one-way ANOVA/Tukey was performed per property (alpha = 0.05).
Results
DSC, XRD, and SEM revealed three distinct microstructures during LS 2 crystallization. Significant differences were found between the control group, the two aforementioned experimental groups, and the five lower-targeted-temperature groups per property ( p < 0.05). The activation energy for lithium disilicate growth was 667 (±29.0) kJ/mol.
Conclusions
Groups with the extended temperature range (750–840 °C) and protracted holding time (820–840 °C H14) produced significantly higher elastic-modulus and hardness properties than the control group but showed similar flexural-strength and fracture-toughness properties with the control group. In general, rapid growth of lithium disilicates occurred only when maximum formation of lithium metasilicates had ended.
1
Introduction
Lithium disilicate glass–ceramics were first introduced into the dental community in 1998 by Ivoclar Vivadent. Since its inception, dental research on the lithium disilicate glass–ceramics have been based on the commercial product, IPS Empress® 2 (Ivoclar Vivadent, Schaan, Liechtenstein). It contained approximately 65% volume fraction of lithium disilicates, 34% volume fraction of residual glass, and 1% volume fraction of porosity after heat treatments . Unlike the binary lithium disilicate system that was first developed by Stookey , the IPS Empress® 2 was derived from a multi-component system, formulated from SiO 2 –Li 2 O–K 2 O–ZnO–Al 2 O 3 –La 2 O 3 –P 2 O 5 compositions . Scanning electron micrographs of IPS Empress® 2 revealed that the microstructures of lithium disilicates were elongated crystals with a mean grain length and diameter of 5.2 and 0.8 μm, respectively . In contrast to IPS Classic®, for which uncontrolled devitrification of leucites occurred only on the surface , the controlled crystallization of IPS Empress® 2 ensured that nucleation and crystal growth of lithium disilicates propagated uniformly throughout the bulk structure during heat treatments . The nucleation in IPS Empress® 2 was achieved with the aid of special additives (e.g., P 2 O 5 , TiO 2 and ZrO 2 ) . Additionally, these additives could alter the eutectic composition and temperature of the IPS Empress® 2 glass–ceramic . According to Headley and Loehman, at low temperature, P 2 O 5 amassed and formed the crystalline nuclei of lithium orthophosphates. Then, lithium metasilicates, lithium disilicates, and cristobalites could be crystallized by epitaxial growth on those lithium orthophosphates .
Besides the special additives, the growth of lithium disilicate crystals could also be affected by a one- or two-stage heating schedule. The one-stage heating schedule only involved a single heating rate and holding time. The two-stage heating schedule typically entailed first and second heat treatments for nucleation then crystallization, respectively . The initial heat-treatment stage was important to establish a kinetically favorable setting for stabilizing lithium metasilicates . The second heat-treatment stage, usually at a higher temperature range than the initial, supplied the thermal energy to induce growth of lithium disilicates and to thermodynamically destabilize the lithium metasilicates . According to Borom et al., the growth of lithium disilicate crystals was not dependent on the crystalline nuclei of lithium metasilicates . Rather, lithium metasilicates kinetically competed with lithium disilicates but slowly diminished since it was thermodynamically less stable than lithium disilicates at high temperatures . In contrast, Zheng et al. suggested an interdependence between lithium metasilicates and lithium disilicates, where lithium disilicates could be epitaxially grown on lithium metasilicates . Past investigations have argued that a two-stage heating schedule precipitated more and larger lithium disilicate crystals than a single-stage heating schedule . Even though the single-stage heating schedule might require less overall processing time, it tended to lack the appropriate thermal enrichment for maturation of lithium disilicate crystals . Because of this, when a DSC was used to investigate the non-isothermal crystallization kinetics of a lithium disilicates system, the separation between the exothermic peaks of lithium metasilicates and lithium disilicates were less distinguishable, which further indicated that amidst the glass–ceramic microstructures, the lithium metasilicates and lithium disilicates were less identifiable from one to another for the single-stage heating schedule that encourages a fast or ultrafast heating rate. Hence, in theory the timing of the sequential heat treatments and the heating rates were critical to the origin, as well as discontinuation, of the microstructural segregation and to the nucleation and propagation of lithium disilicate crystals.
With the advent of CAD-CAM technology and phasing out of IPS Empress® 2, newer generations of glass–ceramic blocs were introduced to accommodate the ease of milling, to maximize cutting efficiency, and to prolong the life of the milling tools. Today, the insertion of a chair-side IPS e.max® CAD prosthesis involves three fabricating progressions: industrial casting of the blocs, CAD milling, and final thermal refinement for enriching lithium disilicate crystallization. First, according to the manufacturer, glass compositions (mainly SiO 2 , Li 2 O, P 2 O 5 , ZrO 2 , ZnO, and K 2 O) are incongruently melted, quenched, and annealed to form blue ingots, IPS e.max® CAD blocs . The blue tint, acquired from the added colorants, is evidence that the bloc has undertaken a partially glassy-crystalline transformation and signifies its readiness for the second process, CAD milling. In this partially crystallized state, these intermediates inherit a mild to moderate strength and hardness, which can be easily machined by any popular CAD-CAM system. Often, this second process can be conveniently done in a private dental practice. After milling, it is then transformed by a two-stage heat treatment into a dental prosthesis containing both glassy phase and lithium disilicate crystals. Different heating parameters can upset the driving force for growing lithium disilicates and can alter the overall percentage of residual glasses . Theoretically, glass–ceramic prostheses, containing an extra residual glassy phase, are more likely to adversely impact a number of properties including load-bearing capacity, resistance to acidic attacks, and fracture toughness . In contrast, amplifying crystallization lowers the coefficient of thermal expansion, improves the resistance to thermal shock, and increases prosthetic strength .
Although many studies have been conducted to evaluate the clinical performance and potential shortcomings of lithium disilicate glass–ceramics in comparison to other popular types of dental materials, only a few focus on the glass–ceramics’ properties from an intrinsic perspective of crystallization, phase assembly, thermal history, and kinetics. Additionally, most of that handful of studies has been confined within the erudite realms of the pure or binary Li 2 O–SiO 2 systems . Exploration on how a “multi-component” CAD-CAM bloc crystallizes has been very limited . Further investigation in describing the intricate interplay between thermal treatments and crystalline architecture exhibited by these materials can offer insights on how their atomic-scale behaviors can transcend to distress or to fortify their macroscopic material properties. Most importantly, clarification on why lithium metasilicates tend to evolve to form lithium disilicates needs to be addressed, so their desired clinical properties can be deliberately manifested through the manipulation of heat treatments. Here, we studied the history-dependent response (thermal versus physical) of a multi-component glass–ceramic, named IPS e.max® CAD that is sold in the form of a partially crystallized precursor, and endeavored to comprehend its kinetic process through analysis of its emergent microstructures and macroscopic physical properties. The aim of this study was to characterize the transformative behavior, crystallizing kinetics, and microstructural evolution of a partially crystallized glass precursor (IPS e.max® CAD) into lithium disilicate glass–ceramics. According to the manufacturer, the heating schedule for inducing crystallization of lithium disilicates within an IPS e.max® CAD bloc consisted of two (double) heating rates and two holding times, each of which was initiated and held at a specific targeted temperature (see Table 1 for the group labeled as 820–840 °C). Initially, the partially crystallized precursor was heated at a rapid rate of 90 °C/min from 403 °C (furnace stand-by-temperature) to 820 °C and held for 10 s at 820 °C (first targeted temperature). This was followed by a slower, second heating rate of 30 °C/min. Then, it was held for a period of 7 min at 840 °C (second targeted temperature). In this study, we hypothesized that when IPS e.max® CAD is thermally processed under a two-stage heating schedule, an early onset of the second heating rate at a lower targeted temperature (750 °C) than the recommended (820 °C), which causes a time extension of the heating interval for the second heating stage, will have an impact on the glass–ceramic’s flexural strength, fracture toughness, elastic modulus, and hardness. We also hypothesized that protracting the holding time at the isothermal temperature, 840 °C, of the second heating stage will have an impact on the glass–ceramic’s flexural strength, fracture toughness, elastic modulus, and hardness.
Not fired | 530–590 °C | 590–750 °C | 590–750 °C (H14) | 750–780 °C | 750–840 °C | Recommended 820–840 °C |
820–840 °C (H14) | |||||||||
---|---|---|---|---|---|---|---|---|---|---|---|---|---|---|---|---|
Stage 1 | Stage 2 | Stage 1 | Stage 2 | Stage 1 | Stage 2 | Stage 1 | Stage 2 | Stage 1 | Stage 2 | Stage 1 | Stage 2 | Stage 1 | Stage 2 | Stage 1 | Stage 2 | |
B (°C) | Not applicable | 403 | 403 | 403 | 403 | 403 | 403 | 403 | ||||||||
S (min) | 0.3 | 0.3 | 0.3 | 0.3 | 0.3 | 0.3 | 0.3 | |||||||||
t (°C/min) | 90 | 30 | 90 | 30 | 90 | 30 | 90 | 30 | 90 | 30 | 90 | 30 | 90 | 30 | ||
T (°C) | 530 | 590 | 590 | 750 | 590 | 750 | 750 | 780 | 750 | 840 | 820 | 840 | 820 | 840 | ||
H (min) | 0:10 | 7 | 0:10 | 7 | 0:10 | 14 | 5 | 14 | 0:10 | 7 | 0:10 | 7 | 0:10 | 14 | ||
V 1 (°C) | 450 | 530 | 450 | 590 | 450 | 590 | 550 | 750 | 450 | 750 | 550 | 820 | 550 | 820 | ||
V 2 (°C) | 530 | 590 | 590 | 750 | 590 | 750 | 750 | 780 | 750 | 840 | 820 | 840 | 820 | 840 | ||
Heating time (min) | Not applicable | 10.88 | 14.88 | 21.88 | 24.16 | 14.32 | 12.77 | 19.77 |
2
Materials and methods
2.1
Heating schedules
Based on past studies and manufacturer recommendations, seven unique two-stage heating schedules were developed to evaluate the IPS e.max® CAD blocs. See Table 1 . Group 820–840 °C represented the manufacturer’s recommended two-stage heating schedule and was the control group. Here, the two-stage heating schedule was designed to thermally process a glass precursor in two successive stages, where each stage consisted of a unique heating rate, holding time, and targeted temperature. The targeted temperature was defined as the terminal temperature point at which the ramping of heat at a particular heating rate was ended and as the start of an additional ramping of heat at a new heating rate. Usually, the first heating rate was ramped much faster than the second heating rate. In this work, we followed the manufacturer’s recommendation for which the first and second heating rates were maintained at 90 and 30 °C/min respectively. The reason behind this was for consistency, ease of comparison, and minimizing covariates.
All heating schedules were derivatives of the recommended two-stage heating schedule, but the targeted temperatures and the second holding times were modified. The heating schedules for the 530–590, 590–750, 590–750 (H14), and 750–780 °C groups allowed us to study the evolutionary development of the lithium disilicate system. For the 750–840 °C group, the second heating rate (30 °C/min) began at a lower onset temperature than the control group (750 °C vs. 820 °C). This would protract the time for the second heat ramping to reach the final temperature of 840 °C since it was ramping at a speed of 30 °C/min instead of 90 °C/min. The control group would take less time to complete its second heat ramping as compared with the 750–840 °C group since it was ramping through a narrower temperature interval of 20 °C scale versus an interval of 90 °C scale for the 750–840 °C group. For the 820–840 °C (H14) versus the control group, their difference was the longer holding time of 14 min as opposed to the regular 7 min at 840 °C. For this study, furnace stand-by temperature, door closing time, and heating rates were held constant. Additionally, an ultra-short first holding time of 10 s was followed by a second holding time of either 7 or 14 min. Thus, the overall heating time was calculated by summing the time for closing the furnace door, the two two-stage ramp periods, and the holding times.
2.2
Specimen preparation
Following the ISO Specification 6872 , the IPS e.max® CAD blocs were sectioned into bars using a diamond saw (Isomet 1000, Buehler, Lake Forest, IL). The rectangular bars were randomly but equally divided into the eight groups of various firing schedules. See Table 1 . Twelve rectangular bars per group were used (i.e., for the flexural test, n = 96, and for the fracture toughness test, n = 96). After firing, all surfaces of the bar were polished using silicon carbide paper of 600-, 800-, 1000-, and 1200-grit (EXAKT Technologies, Oklahoma City, OK, USA) under running water at 300 rpm on a polishing machine (EXAKT 400 CS, EXAKT Technologies, Oklahoma City, OK, USA). After polishing with each of the various grits, the specimens were rinsed with water. The specimens were stored dry until testing was performed.
2.3
X-ray diffraction (XRD)
The XRD data were collected from three representative specimens per group (obtained from the fragments of the 3-point flexure test) by using a D8 Discover X-ray diffractometer with two-dimensional VÅNTEC-500 detector (Bruker Instruments, Billerica, MA, USA). Using monochromatic radiation ( λ Kα = 1.5406 Å), each specimen was scanned in bulk over the 2 θ range, 16–82°, with an angular resolution of 0.005° for identifying the crystalline phases.
2.4
Flexural strength
The 3-point flexure test was performed as recommended by ISO Specification 6872 , and the flexural strengths, σ FS (MPa), were calculated according to the following formula: σ FS = 3 Fl /2 bd 2 , where F was the breaking load (N); l was the test span (mm); b was the width of the specimen (mm); and d was the thickness of the specimen (mm). The 3-point flexure test fixture consisted of two cylinders with a radius of 0.8 mm (span distance, 15 mm) and a loading, cylindrical head with a radius of 0.8 mm. The IPS e.max® CAD blocs were prepared into bars (1.3 mm × 4 mm × 18 mm) as described in the sample preparation section. Each specimen was loaded to failure (crosshead speed = 0.5 mm/min) using a universal testing machine (MTS Sintech ReNew 1123, MTS Systems, Eden Prairie, MN, USA), at room temperature. The flexural modulus was acquired from the slope of the best-fitted linear region of the load-deflection curve using TestWorks® software (MTS Systems, Eden Prairie, MN, USA). The mean and standard deviation were then calculated.
2.5
Fracture toughness
The fracture toughness values were determined by a single-edge notched-beam method, ISO Specification 6872 . The IPS e.max® CAD blocs were prepared into bars (1.3 mm × 4 mm × 18 mm) as described in the sample preparation section. The notches of the specimens were prepared with a diamond saw (blade thickness = 0.3 mm, EXAKT 300, EXAKT Technologies, Oklahoma City, OK, USA). All root radii of the prepared notches were then manually refined using a single-edged razor blade and diamond polishing paste. The final notch depth and root radius were 1.0 ± 0.2 and 0.05 ± 0.02 mm, respectively, which was verified by using a stereomicroscope (Nikon Measurescope UM-2, Shinjuku, Tokyo, Japan). The K IC (MPa m 0.5 ) values were calculated using the following equations:
K IC = P S b w w 3 α 2 ( 1 − α ) 1.5 Y
where Y = 1.9472 − 5.0247 α + 11.8954 α 2 − 18.0635 α 3 + 14.5986 α 4 − 4.6896 α 5 and <SPAN role=presentation tabIndex=0 id=MathJax-Element-2-Frame class=MathJax style="POSITION: relative" data-mathml='α=a/w’>α=a/wα=a/w
α = a / w
; and, where P , S , a , b , and w were peak load (MPa), test span length (m), notch depth (m), specimen thickness (m), and specimen width (m), respectively. The specimens were tested in a similar manner as flexural strength in a universal testing machine at a crosshead speed of 1 mm/min. The mean and standard deviation were then calculated.
2.6
Nanoindentation
A MTS Nanoindenter® XP (MTS Systems, Eden Prairie, MN, USA) equipped with TestWorks® software (MTS Systems, Eden Prairie, MN, USA) and fitted with a tetrahedral Berkovich diamond indenter tip (Serial # TB20128, MTS Systems, Eden Prairie, MN, USA) of 20 nm radius (faces 65.3° from vertical axis) was used to measure all specimens. A linear array of indents (100 indents/group) was diagonally imprinted on the polished surfaces obtained from the fragments of the 3-point flexure test. Each consecutive indent was spaced 30 μm apart from each other to avoid any interference of residual stresses from adjacent imprints. Force–displacement curves for the indents were used to evaluate the elastic moduli. For each indent, elastic modulus was calculated using the standard methods of Oliver and Pharr . The Elastic modulus, E (GPa), per group was computed with the following expression,
E = ( 1 − v 2 ) 1 E r − v i 2 E i − 1
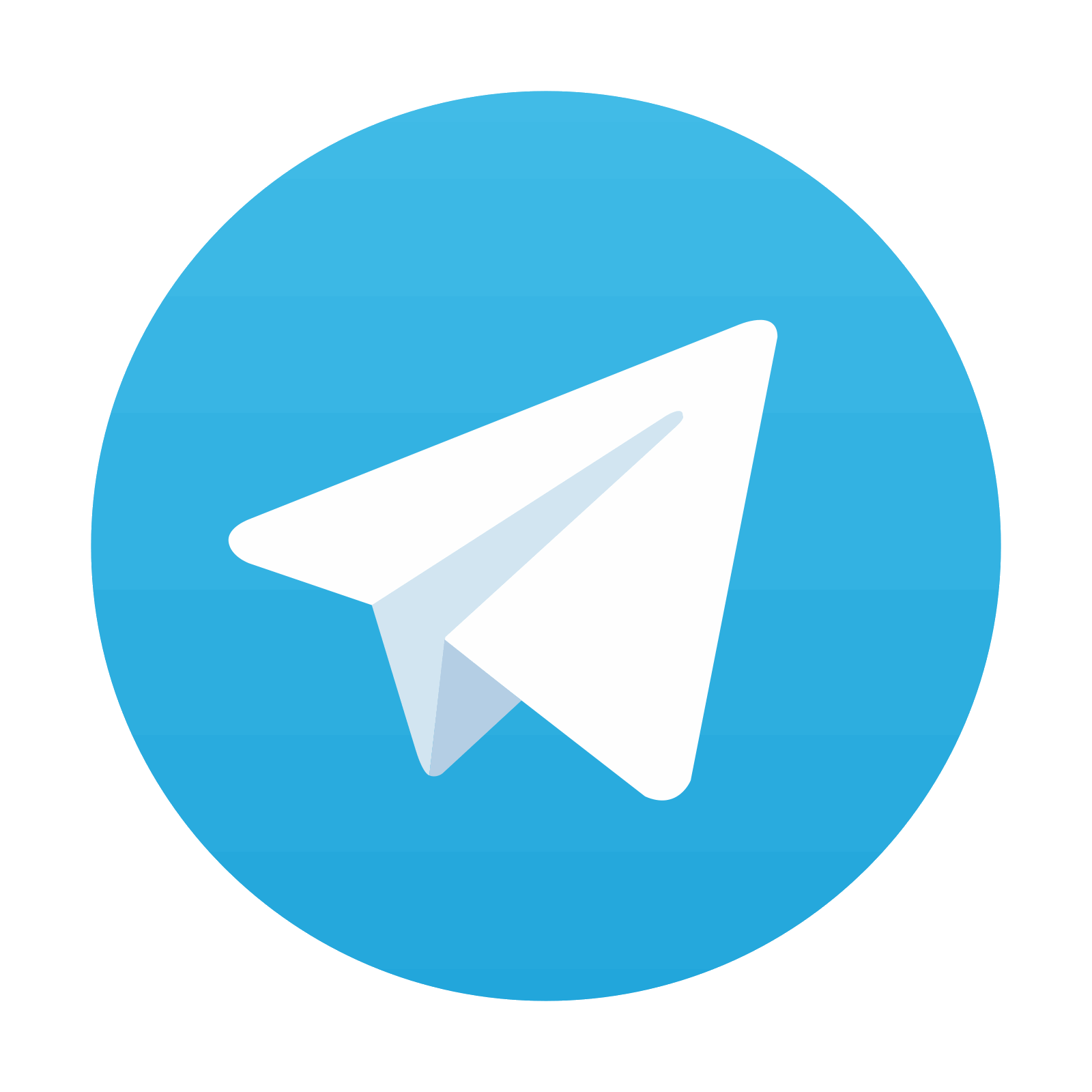
Stay updated, free dental videos. Join our Telegram channel

VIDEdental - Online dental courses
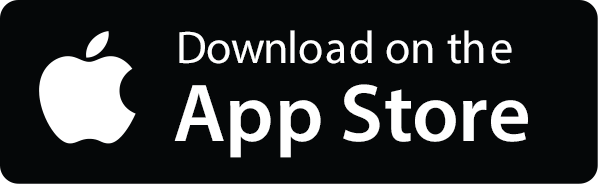
