Abstract
Objectives
The aim of this study was to evaluate the linear and volumetric dimensional changes of six denture base resins processed by their corresponding injection-molding systems at 3 time intervals of water storage.
Materials and methods
Two heat-curing (SR Ivocap Hi Impact and Lucitone 199) and four auto-curing (IvoBase Hybrid, IvoBase Hi Impact, PalaXpress, and Futura Gen) acrylic resins were used with their specific injection-molding technique to fabricate 6 specimens of each material. Linear and volumetric dimensional changes were determined by means of a digital caliper and an electronic hydrostatic balance, respectively, after water storage of 1, 30, or 90 days. Means and standard deviations of linear and volumetric dimensional changes were calculated in percentage (%). Statistical analysis was done using Student’s and Welch’s t tests with Bonferroni–Holm correction for multiple comparisons ( α = 0.05).
Results
Statistically significant differences in linear dimensional changes between resins were demonstrated at all three time intervals of water immersion ( p ≤ 0.05), with exception of the following comparisons which showed no significant difference: IvoBase Hi Impact/SR Ivocap Hi Impact and PalaXpress/Lucitone 199 after 1 day, Futura Gen/PalaXpress and PalaXpress/Lucitone 199 after 30 days, and IvoBase Hybrid/IvoBase Hi Impact after 90 days. Also, statistically significant differences in volumetric dimensional changes between resins were found at all three time intervals of water immersion ( p ≤ 0.05), with exception of the comparison between PalaXpress and Futura Gen.
Significance
Denture base resins (IvoBase Hybrid and IvoBase Hi Impact) processed by the new injection-molding system (IvoBase), revealed superior dimensional precision.
1
Introduction
Poly (methyl methacrylate) acrylic resin is commonly used as removable denture base material. The relative ease with which PMMA may be processed is one advantage of its use as a denture base material . To fabricate a denture base with an accurate fit to the oral supporting tissues, there must be good control of dimensional stability , since the retention of complete dentures depends, to a large extent, on a good base adaption and border seal to ensure retention by virtue of negative pressure .
Dimensional accuracy is therefore an important property of denture bases. However, when constructing denture bases from acrylic resins, polymerization shrinkage of the resin and distortion of the denture base due to the release of internal stresses induced during processing procedures is virtually unavoidable . These adverse effects cause movement of the artificial teeth position and increase the gap between the denture base and underlying mucosa and might result in an ill-fitting denture .
In contrast, wet storage results in a slight dimensional increase of the denture base caused by water sorption of the acrylic resin. This phenomenon may partially compensate for the polymerization shrinkage .
Conventional compression molding method has been widely used for the fabrication of denture bases. However, a further source of dimensional change associated with this technique can be the inevitable flash resulting from overfilling of the mold, and consequently, more increase in vertical dimension of occlusion (VDO) .
Attempts to overcome the problems associated with processing of denture base acrylic resins have resulted in the development of the continuous injection system by Pryor .
Continuous-injection molding eliminates the flash of resin between the halves of the flask , and allows directional control of the polymerization process through the flask design . A constant flow of new material from the feeding sprue compensates for the polymerization shrinkage . Various injection-molded denture base materials and processing techniques are now available, each claiming to produce more accurate denture bases, and the method is more commonly used.
Several studies evaluating the dimensional accuracy of denture base materials processed by injection-molding technique have been conducted using different dimensional change measuring methods. These changes have been, mainly, attributed to: (1) the choice of processing system , (2) type of polymerization .
Despite constant improvements in techniques and materials, the quest is still to develop a system that can totally compensate for the processing shrinkage of denture bases .
Recently, a new injection device (IvoBase Injector, Ivoclar Vivadent, Schaan, Liechtenstein) has been introduced to the profession. This new “all-in-one” injector permits a fully automated, controlled injection and polymerization process of newly developed PMMA resins (IvoBase Hybrid, IvoBase Hi Impact) which are coordinated with the system.
The current study was conducted to compare the dimensional stability of six commercially available poly (methyl methacrylate) denture base acrylics, processed by their corresponding injection-molding system. This was done by comparing the linear and volumetric dimensional change of the processed denture base materials at different time intervals of water storage.
The null hypothesis was that there is no difference in dimensional changes between the various acrylic resins used with their specific injection-molding systems.
2
Materials and methods
Six denture base resins were selected for this study. The materials, manufacturers, proportions of powder to liquid, fabrication system, the type of polymerization, and the polymerization parameters are shown in Table 1 .
Product | Abbreviation | Manufacturer | Batch no. | Polymer:monomer ratio | Fabrication system | Polymerization type | Polymerization parameters |
---|---|---|---|---|---|---|---|
IvoBase Hybrid | IBHY | Ivoclar Vivadent AG, Schaan, Liechtenstein | NM0188 | 34 g:20 ml | IvoBase Injection System | Auto-polymerizing | Electromechanical injection, 35 min, initiating temperature 40 °C, dry heat |
IvoBase Hi Impact | IBHI | Ivoclar Vivadent AG, Schaan, Liechtenstein | NM0157 | 30 g:20 ml | IvoBase Injection System | Auto-polymerizing | Electromechanical injection, 50 min, initiating temperature 40 °C, dry heat |
SR Ivocap Hi Impact | ICHI | Ivoclar Vivadent AG, Schaan, Liechtenstein | N35171 | 20 g:30 ml | SR Ivocap Injection System | Heat-polymerizing | Pneumatic injection, 35 min in boiling water |
FuturaGen | FUT | Schütz Dental Gmbh, Rosbach, Germany | 2010006210 (powder) 2010005960 (liquid) |
35 g:16 ml | UNIPRESS Injection System | Auto-polymerizing | Manual injection, 30 min, 30 °C-40 °C, bench-curing |
PalaXpress | PLX | Heraeus Kulzer Gmbh, Hanau, Germany | 011095 (powder) 010471 (liquid) |
30 g:15 ml | Palajet Injection System | Auto- polymerizing | Pneumatic injection, 30 min, water bath 55 °C, pressure-pot 2 bar |
Lucitone 199 | LUC | Dentsply International Inc., York, PA, USA | 100506 (powder) 100406 (liquid) |
21 g:10 ml | Success Injection System | Heat-polymerizing | Pneumatic injection, water bath 90 min at 72 °C and 30 min in boiling water |
2.1
Specimen preparation
In order to fabricate the specimens, a master die was constructed using Invar* metal (CTE ≤ 2 μm/°C) with the dimensions given in ( Fig. 1 ).
*Invar – Controlled Expansion Alloy, Goodfellow, Ermine Business Park, Huntingdon England
The shape of the master die, double-sided isosceles trapezoid, enabled direct comparison of linear and volumetric dimensional changes. The vertical walls were fabricated with a 10-degree convergence to facilitate removal of the die from the investment after the flasking procedure.
To compare the dimensional changes of the specimens, a total of 36 specimens were prepared with 6 specimens for each resin. A wax injection sprue was attached to the shortest (anterior) side of the master die. Sprue length and diameter were determined according to manufacturers’ instructions of each studied denture base resin. Hereinafter, the master die was directly invested in the denture flask by pouring the stone (Dura-Halbhartgips grün, Siladent Dr. böhme& Schöps, Goslar, Germany) into the lower half of the flask and embedding the master die in the stone of the lower half of the flask at the same height as the level of flask edge. After the stone of the lower half of the flask had set (45 min), the master die and the exposed stone surfaces were isolated with Isofix 2000 separator (Isofix 2000 No.1720, Renfert, Hilzingen, Germany).
Subsequently, the top half of the flask was placed on the bottom half, ensuring complete intimate contact and closure of the halves, and filled with the same stone. All flasks, which were used in our study to prepare specimens, were poured by using vacuum-spatulated stone according to manufacturers’ recommendations and a single pouring technique. After the stone had set (45 min), the flask was heated and the two halves of the flask were separated to flush out the wax sprue, and to remove the master die. Two layers of Sodium alginate (ISO-K blau, Candulor, Wangen bei Dübendorf, Switzerland) were applied to the exposed stone surfaces and allowed to dry. Thereafter, the flask was clamped and the powder/liquid mixture of denture base material was prepared to be polymerized. The investigated denture base resins were mixed according to the respective manufacturer’s instruction. The curing cycles were also set in accordance with the manufacturer’s instructions. After the completion of processing, the flask was cooled to room temperature (24 °C ± 1).
Following processing, the specimen was carefully removed from the stone mold, and the injection sprue was sectioned by means of a saw (Isomet 1000 precision saw; Buehler, Lake Bluff, IL, USA), leaving the specimen’s injection side without any sprue remains ( Fig. 2 ).
All specimens within each resin group were made from the same batch number and stored in (37 °C ± 1) distilled water for 1, 30, and 90 days before being tested.
2.2
Measurements
The measurements obtained from the metal die were used as the baseline readings, and all values were calculated with these measurements as the starting point. All measurements were carried out by the same investigator. At each time interval the specimens were removed from the water and dried by blotting with absorbent tissue.
2.3
Linear dimensional change measurements
Using a digital caliper (Orion, Hahn + Kolb Werkzeuge, Stuttgart, Germany), that read to an accuracy of 0.01 mm, 3 repeat readings of the distance between the two reference points a and b (the tips of the 2 sharp corners at the metal die) were recorded by the investigator, and the average of the readings was considered the baseline reading ( L 0 ).
The prepared specimens were measured following the same previously described procedure at each protocol interval, and the mean of the 3 readings was used as the measurement ( L ). Subsequently, the percentage of the linear dimensional change (Δ L ) of the studied denture base resins was calculated as follows:
2.4
Volumetric dimensional change measurements
Archimedes’ principle was used to determine volumetric dimensional changes. This has been achieved by using an electronic hydrostatic balance (UW620H, Shimadzu Corporation, Japan) which is accurate to the nearest 0.001 g and consists of combination pans (upper and lower), pan frame, tank, tank table, and frame supporters. The electronic hydrostatic balance can determine not only the weight but also the density of specimens based on the buoyancy of a material in fluid, which means the weight of displaced fluid. Solid specimen submerged in the medium liquid, which is usually distilled water, receives buoyancy that equals to the weight of the medium liquid of the specimen volume. When the weight of solid specimen in air and the weight in the medium liquid are known, the density of the solid specimen can be obtained with the density of the medium liquid. The balance computes the solid specimen’s density ( ρ ) according to the below given expression, and displays the result. This expression is derived from Archimedes’ principle.
ρ = W a W a − W l ρ l
W a : Solid specimen weight in air, W l : Solid specimen weight in the medium liquid, ρ l : Density of the medium liquid.
Firstly, the master die has been weighed on the upper balance’s pan. Three weight readings were obtained, and their mean was considered the baseline reading ( W 0 ). Secondly, the die was removed from the upper balance’s pan and placed in the lower balance’s pan immersed in distilled water and the displayed apparent density was noted. Three density readings were obtained, and the mean was considered the baseline reading ( D 0 ). This procedure was done with extreme care to ensure that no air bubbles adhered to the die’s surface. The volume of the die was calculated as follows:
V 0 = W 0 D 0
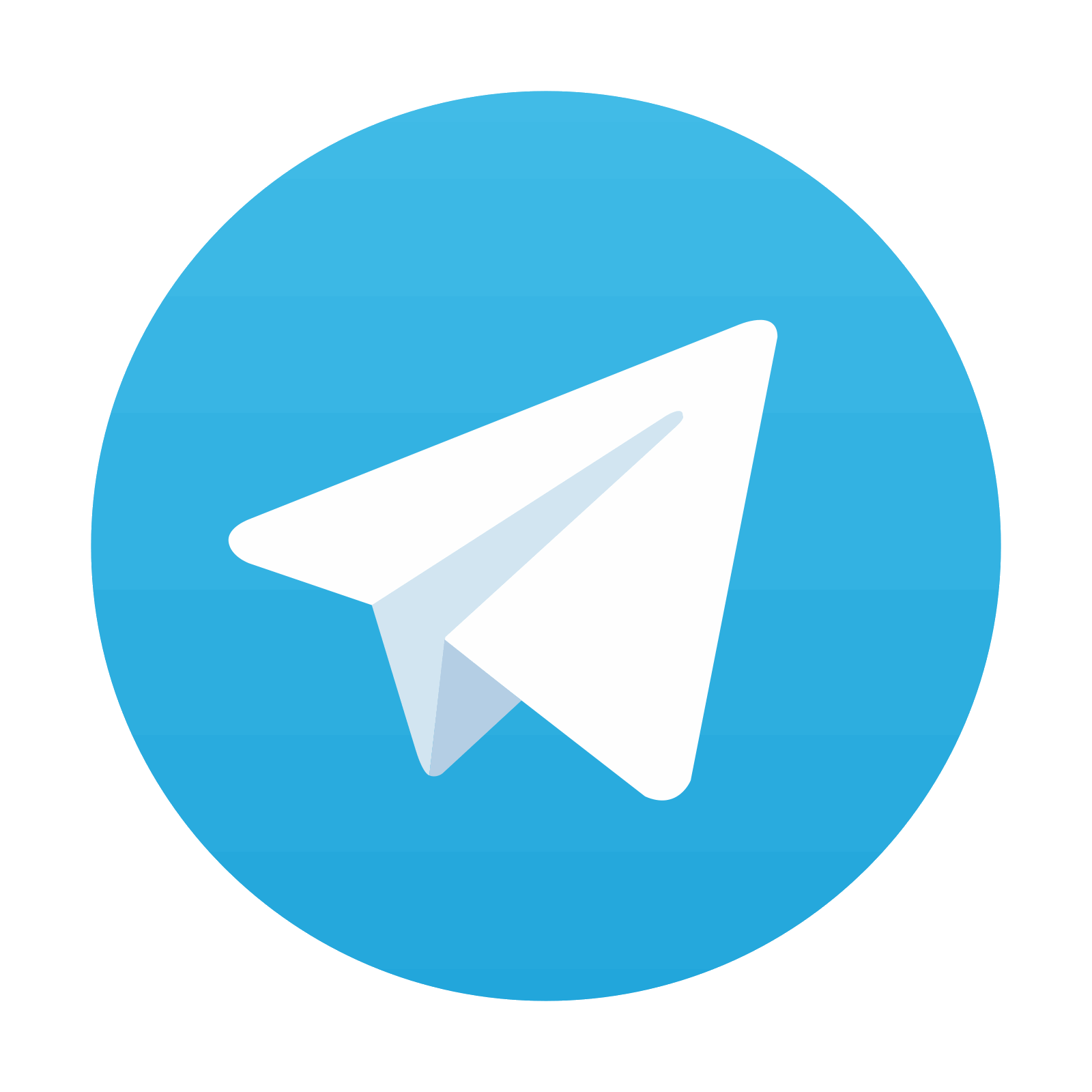
Stay updated, free dental videos. Join our Telegram channel

VIDEdental - Online dental courses
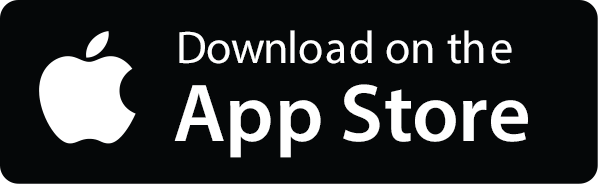
