Abstract
Objective
To investigate the effect of indenter size on the failure mode of amalgam and its interaction with thickness.
Methods
Dental silver amalgam (Lojic+, SDI) discs, 10 mm diameter, thickness h = 0.4–8.0 mm, were stored in air at 37 °C for 7 days before testing in ‘Hertzian contact’, resting freely on a 30% glass fibre-reinforced nylon 6,6 substrate (E: 10 GPa) at 23 °C in air at a crosshead speed of 0.2 mm/min. The load at the first crack, detected acoustically, was recorded. Two series of tests were conducted. In the first, a 3 or 20 mm diameter hard steel ball was used to apply the load to discs with h = 0.4–8.0 mm. The second was performed on discs with h = 2.0 and 5.0 mm with indenter diameters D = 2–40 mm.
Results
The failure loads for these two groups were substantially different, with most values for D = 3 mm being lower than those for D = 20 mm. The transitions of the main failure mode with increasing thickness were similar, i.e ., from RC-dominant for h small to CC-dominant for h large, except that this occurred over a greater range for the larger indenter. For h = 2 mm, failure load was constant for D = 2–40 mm; all specimens consistently failed from bottom RC. For h = 5 mm, failure load increased with D with a quadratic relationship up to about 10 mm ( r 2 = 0.85), after that, values were near constant; the failure mode gradually changed with D from PD- or CC-prevailing for D small (≤5 mm) to RC-prevailing for D very large (30 and 40 mm).
Significance
The failure mode of amalgam is dependant on the indenter size; indenter size and coating thickness have reciprocal effects.
1
Introduction
It has been well demonstrated from Hertzian contact theory that the local stress state of a brittle specimen under a spherical indenter is profoundly influenced by the indenter size. In monolithic ceramic structures, quasi -plastic deformation (QP) dominates at small indenter diameter, while brittle fracture prevails at large diameter . Research on this issue has been extended to laminated structures since the 1990s, where failure mode has been reported to show a similar dependence in both physical experiments and finite element analysis: a borosilicate glass-polymer bi-layer structure tended to produce cone cracking (CC) ( i.e ., initiated from the top, loading, surface) with a small indenter, but radial cracking (RC) (initiated from the coating–substrate interface) for larger sizes . Such effects would seem to make it necessary have a rational selection of indenter size. However, in previous reports, indenter diameters ranging from a few millimeters to one meter have been used . The choice appears to have been arbitrary in that none mentions a selection rationale. On the other hand, it is known that specimen thickness also controls failure mode . Generally, as the coating thickness ( h ) increases, the main failure mode for a (relatively) soft coating on a hard substrate, bi-layer structure has the tendency of changing from RC to CC or QP. However, the two factors have usually been investigated separately.
Given the lack of data on the interaction of indenter size and specimen thickness, the objective now was to investigate the failure mode of amalgam in the context of that interaction with a view to proper selection of appropriate values for the routine use of this indentation test.
2
Materials and methods
Dental silver amalgam (Lojic+, SDI, Bayswater, VIC, Australia) discs of thicknesses ( h ) ranging from 0.4 to 8.0 mm were fabricated using 10 mm diameter moulds. The pre-dosed capsules were machine mixed (Silamat, Vivadent, Amherst, NY, USA) for 6 s, packed into the mould by hand in usual clinical fashion, and the specimen demoulded after 10 min, according to the manufacturer’s recommended hardening time. At 24 h after fabrication, specimens were then carefully ground from the top surface only to the chosen thickness on a metallographic pregrinder (Lunn-Major, Struers, Copenhagen, Denmark) using silicon carbide (SiC) abrasive paper from coarse (220 grit) to fine (1200 grit), under running water. The detailed specimen preparation method was as reported before . Preparation was at 23 ± 1 °C, 50 ± 10% RH. All the specimens were stored in air at 37 ± 1 °C for 7 days before testing. Rod-form 30% glass fibre-reinforced nylon 6,6, 10 mm diameter (Goodfellow Cambridge, Huntingdon, England), was cut into discs 5 mm thickness to be used as test substrate.
Two series of tests were conducted. Firstly, a hard steel ball of diameter d = 3 mm was used to load discs of h = 0.4–(0.8)–4.4, and 5.0–(1.0)–8.0 mm. These results were compared with previous data obtained using a 20 mm diameter indenter . Secondly, discs of h = 2.0 and 5.0 mm were tested with indenters of D = 2, 3, 5, 8, 10, 20, 30 and 40 mm.
Between 10 and 20 specimens were tested for each treatment. An amalgam disc, resting freely on a substrate disc, was loaded through the chosen indenter using a universal mechanical testing machine (1185, Instron, High Wycombe, England) at a crosshead speed of 0.2 mm/min. The load at the first crack was recorded. About 1/3 to 1/2 of the specimens of each group were randomly selected for inspection by scanning electron microscopy (SEM) (XL30CP, Philips Electron Optics, Eindhoven, Netherlands).
Statistical analysis was done in software (SigmaPlot 9.0, Systat Software, San Jose, CA, USA).
2
Materials and methods
Dental silver amalgam (Lojic+, SDI, Bayswater, VIC, Australia) discs of thicknesses ( h ) ranging from 0.4 to 8.0 mm were fabricated using 10 mm diameter moulds. The pre-dosed capsules were machine mixed (Silamat, Vivadent, Amherst, NY, USA) for 6 s, packed into the mould by hand in usual clinical fashion, and the specimen demoulded after 10 min, according to the manufacturer’s recommended hardening time. At 24 h after fabrication, specimens were then carefully ground from the top surface only to the chosen thickness on a metallographic pregrinder (Lunn-Major, Struers, Copenhagen, Denmark) using silicon carbide (SiC) abrasive paper from coarse (220 grit) to fine (1200 grit), under running water. The detailed specimen preparation method was as reported before . Preparation was at 23 ± 1 °C, 50 ± 10% RH. All the specimens were stored in air at 37 ± 1 °C for 7 days before testing. Rod-form 30% glass fibre-reinforced nylon 6,6, 10 mm diameter (Goodfellow Cambridge, Huntingdon, England), was cut into discs 5 mm thickness to be used as test substrate.
Two series of tests were conducted. Firstly, a hard steel ball of diameter d = 3 mm was used to load discs of h = 0.4–(0.8)–4.4, and 5.0–(1.0)–8.0 mm. These results were compared with previous data obtained using a 20 mm diameter indenter . Secondly, discs of h = 2.0 and 5.0 mm were tested with indenters of D = 2, 3, 5, 8, 10, 20, 30 and 40 mm.
Between 10 and 20 specimens were tested for each treatment. An amalgam disc, resting freely on a substrate disc, was loaded through the chosen indenter using a universal mechanical testing machine (1185, Instron, High Wycombe, England) at a crosshead speed of 0.2 mm/min. The load at the first crack was recorded. About 1/3 to 1/2 of the specimens of each group were randomly selected for inspection by scanning electron microscopy (SEM) (XL30CP, Philips Electron Optics, Eindhoven, Netherlands).
Statistical analysis was done in software (SigmaPlot 9.0, Systat Software, San Jose, CA, USA).
3
Results and analysis
The results for the fixed indenter diameter ( D /mm) tests are shown in Fig. 1 , and the statistical analysis in Table 1 . The pattern of variation of the failure load ( F / N ) with thickness ( h /mm) for D = 3 was as reported before for D = 20 , i.e ., increasing at first for small h but levelling off (or tending to level off) for h large, although the turning point was different. For D = 3, F was essentially constant from h = ∼3.6, while for D = 20, F continued to increase to the upper limit tested, i.e ., h = 8, and the slope for h = 6–8 was still significantly different from zero ( Table 1 : B, t 1 ). However, above h = 3.6 the slope for D = 20 decreased remarkably, the curve tending to a plateau from about h = 6.0, although the slope of the regression line of D = 20, h = 6–8 cannot be distinguished statistically from that for D = 3 and h = 4.4–7 ( Table 1 : B, t 2 ). Generally, a significant difference was found between the failure loads of these two groups, with most values for D = 3 being lower than those for D = 20: in the small thickness region ( h ≤ 3.6), a significant difference was found between the slopes of the two regression lines ( Table 1 : A, t 2 ); in the large thickness region ( h > 3.6), the discrepancy was even more obvious since the two curves diverged as described above, the intercepts of the two regression lines showing a significant difference ( Table 1 : B, t 3 ).

A | B | |||
---|---|---|---|---|
D = 3 h = 0.4–3.6 | D = 20 h = 0.4–3.6 | D = 3 h = 4.4–7.0 | D = 20 h = 6.0–8.0 | |
n | 67 | 49 | 54 | 34 |
r 2 | 0.978 | 0.97 | 0.078 | 0.166 |
Slope ± SE | 0.420 ± 0.008 | 0.366 ± 0.009 | 0.005 ± 0.009 | 0.023 ± 0.009 |
t 1 | 53.422 | 38.695 | 0.562 | 2.521 |
P 1 | <0.001 | <0.001 | 0.577 | 0.017 |
t 2 | 4.390 | 0.306 | ||
P 2 | ≤0.001 | 0.761 | ||
Intercept ± SE | 1.895 ± 0.017 | 2.070 ± 0.021 | 3.364 ± 0.047 | 3.649 ± 0.063 |
t 3 | 6.611 | 3.699 | ||
P 3 | <0.001 | ≤0.001 |
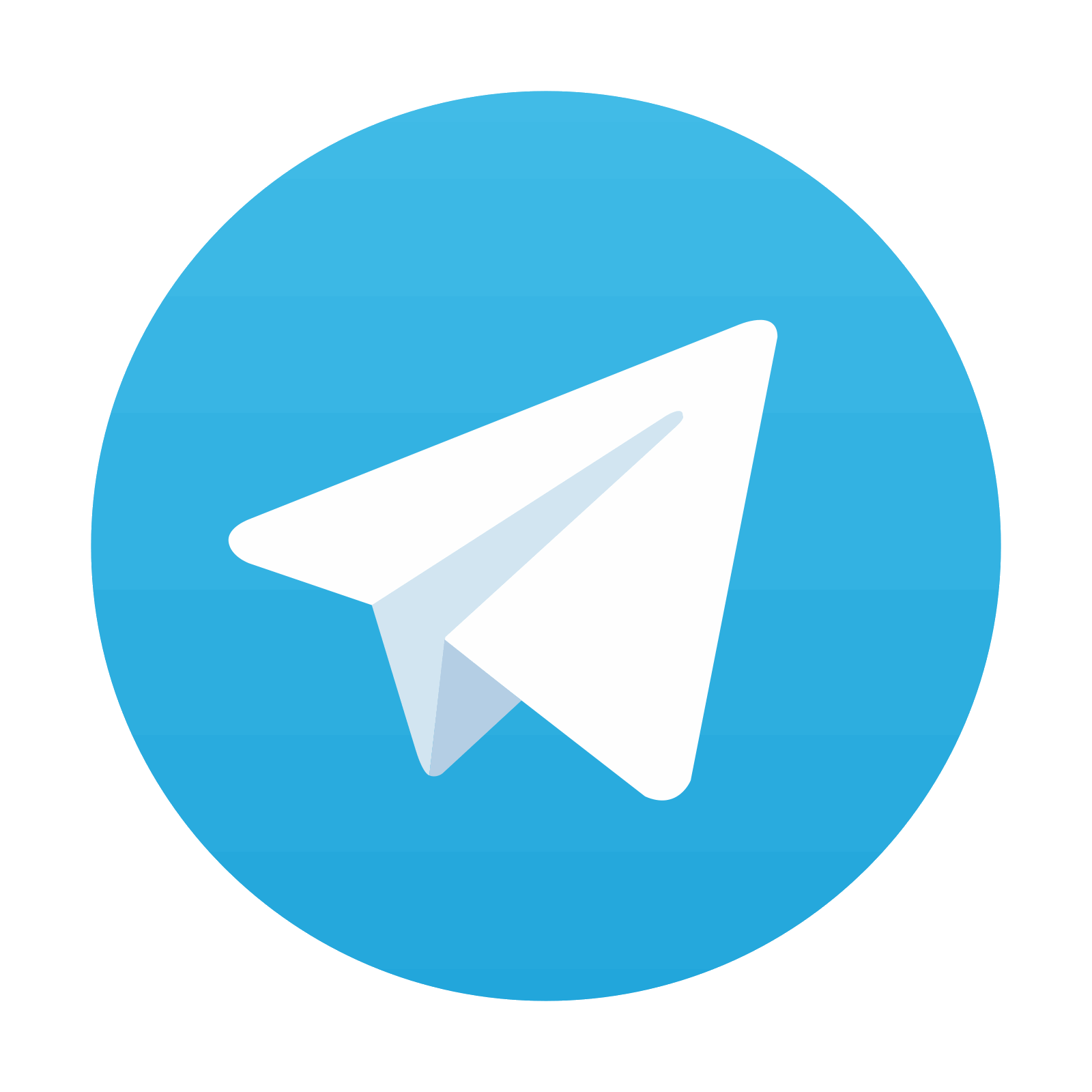
Stay updated, free dental videos. Join our Telegram channel

VIDEdental - Online dental courses
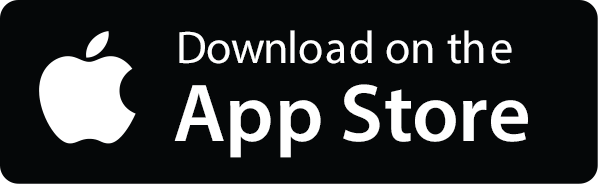

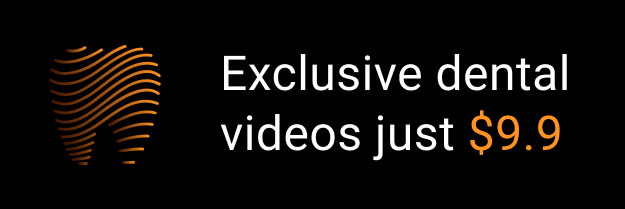