Abstract
Objectives
The aim of this study was to measure the initial dynamic viscoelastic modulus change of dental composites during light curing using a custom made oscillation rheometer.
Methods
Six commercial universal hybrid resin composites: Z100 (Z1), Z250 (Z2), Z350 (Z3), DenFil (DF), Tetric Ceram (TC), and Clearfil AP-X (CF) were examined. A custom designed oscillation rheometer was made, which consisted of three parts: (1) an oscillatory shear strain induction unit, (2) a measuring unit of parallel plates made of glass rods, and (3) a stress measurement unit. For the measurement of the initial viscoelastic modulus change of composites during light curing as a function of time, a dynamic oscillatory shear test was undertaken at a frequency of 6 Hz and strain amplitude of 0.00579 rad for 10 s. From the strain–stress curves, the complex shear modulus ( G *), storage shear modulus ( G ′), loss shear modulus ( G ″) and loss tangent (tan δ ), and the time to reach a G * of 10 MPa were determined. The data were analyzed with one-way ANOVA and Tukey’s post hoc test ( α = 0.05).
Results
There were great differences in the development of viscoelasticity among materials. At 10 s, the complex modulus G * of Z1 was the highest (563.7 MPa), followed by CF, Z2, Z3, TC, and finally DF being the lowest (150.3 MPa). The time to reach the G * of 10 MPa ranged from 2.55 s (Z1) to 4.06 s (DF). The tan δ of the composites decreased with time as the polymerization reaction proceeded.
Significance
The initial modulus development of composites during curing plays a very important role in determining the polymerization shrinkage stress. The custom made oscillation rheometer was able to measure the very initial dynamic viscoelasticity change of several commercial composites during light curing; therefore, the instrument can be used to study the initial curing kinetics of newly developed composites.
1
Introduction
Resin composite has many advantages as a restorative material, including improved esthetics over metallic restoratives and minimum tooth preparation when used with adhesives. However, the material has a polymerization shrinkage of 2–5% during curing . The polymerization shrinkage force is transmitted to the cavity wall if the bond between the restorative and tooth surface is well established. As a result, de-bonding, cusp deflection, and microcracks in enamel or dentin can be generated , potentially resulting in postoperative hypersensitivity, enhanced susceptibility to secondary caries, and failure of restorations.
In addition to the polymerization shrinkage, the increasing elastic modulus during curing plays a crucial role in the development of polymerization shrinkage stress . As the polymerization reaction proceeds, polymer chains grow in the resin matrix, resulting in rapidly increasing viscosity. The rubbery gel stage follows as crosslinking networks are formed between chains, and finally a rigid solid is produced. During this process, the modulus of composites rapidly increases and the material becomes mostly elastic. The contraction stress produced within the material is related to the product of the shrinkage strain times the elastic modulus, but is also affected by stress relieving mechanisms related to flow . Once gelation is reached, the stress relief by molecular flow in the polymer network structure is drastically reduced.
There have been many studies on the polymerization shrinkage and stress of composites, but few on the measurement of modulus development during light curing due to the difficulty in measuring this property as the material changes from a paste to a semi-rigid structure . Further, the photo polymerization reaction proceeds very fast, and the dynamic range of the viscoelastic modulus change of composites during curing is typically too wide for a single instrument to measure. The viscosity of a composite paste prior to cure is lower than 1000 Pa s while the modulus of a cured composite will be on the order of 1 GPa or more within 1 min after beginning light curing. Therefore, it is not possible to measure the modulus change for the whole curing process with one instrument. In general, the viscosity of composite pastes could be measured using a rheometer , but a universal testing machine (UTM) or a dynamic mechanical analyzer (DMA) should be used to measure the modulus of the cured specimen .
Sakaguchi et al. investigated the modulus change of composites during curing within a polyethylene tube using a DMA and reported that they could not measure the change during the very initial 12 s because of the limitation of the methods. They developed a correction for the data after measuring to remove the effect of the polyethylene sheath enclosing the composite. Dauvillier et al. applied several mathematical models to the experimental data measured using a UTM and reported that the composites behaved like a viscoelastic liquid, showing permanent flow within the initial 3 min after the beginning of curing, but little data was available for the initial change in elastic modulus.
It is essential to measure the modulus change accurately during curing in order to understand the origins of the contraction stresses in dental composites and to estimate their magnitude. The purpose of this study was to develop a custom designed oscillation rheometer for the specific purpose of investigating the initial dynamic viscoelasticity change occurring in commercial composites during light curing.
2
Materials and methods
Six commercial light curable restorative composites were used in the study ( Table 1 ). A tungsten halogen light curing unit (VIP junier, Bisco Inc., Schaumburg, IL, USA) was used to cure the composites with an irradiance of 600 mW/cm 2 .
Composite (Code) | Resin matrix | Filler contents (wt%) | Lot no. | Manufacturer |
---|---|---|---|---|
Filtek Z100 (Z1) | BisGMA, TEGDMA | 85 | 6LP | 3 M ESPE, St. Paul, MN, USA |
Filtek Z250 (Z2) | BisGMA, BisEMA, UDMA | 82 | 6LNJ | 3 M ESPE St. Paul, MN, USA |
Filtek Z350 (Z3) | BisGMA, BisEMA, UDMA | 82 | 6EP | 3 M ESPE, St. Paul, MN, USA |
DenFil (DF) | BisGMA, TEGDMA | 80 | DF7120522 | Vericom Co. Anyang, Korea |
Tetric Ceram (TC) | BisGMA, TEGDMA | 79 | J05450 | Ivoclar Vivadent, Schaan, Liechtenstein |
ClearFil AP-X (CF) | BisGMA, UDMA, TEGDMA | 89 | 917A | Kuraray Medical Inc., Tokyo, Japan |
2.1
System configuration and working principle of the custom made oscillation rheometer
A custom designed oscillation rheometer was constructed to measure the initial viscoelastic modulus change of composites during light curing. As shown in Fig. 1 , the rheometer consisted of three parts: (1) a measuring unit of glass parallel plates, on which the specimen was placed (2) an oscillatory shear strain induction unit with a geared brushless DC motor and a crank mechanism, and (3) a stress-measuring unit using an electromagnetic torque sensor which is made up of an electromagnetic actuator, a bi-cell photo diode (BCPD, SD 113-24-21-021, Advanced photonic Inc., Camarillo, CA, USA) and a negative feedback servo amplifier.

The working principle of the rheometer is as follows: a sinusoidal oscillating shear strain was generated by the geared DC motor and a crank mechanism. This oscillating movement is transmitted to the upper, moving part of the measuring unit, which is made of a glass rod with a diameter of 3.0 mm. The amplitude of the sinusoidal oscillating strain was measured by a potentiometer attached to the upper glass rod. The composite is placed between the upper and a similar lower glass rod support.
As the light-curing starts, the viscoelasticity of the composite sample increases rapidly as the material begins to polymerize. As the upper rod of the measuring unit oscillates, the increase in elastic modulus of the sample results in an increase in the shear force transmitted to the lower glass rod. This tends to rotate the arm of the torque sensor attached to the lower rod from its null position, which interrupts the infrared light emitted from a LED shined onto a bi-cell photo diode (BCPD). The deviation of the arm is detected by this BCPD, which generates an electrical voltage output that is fed to a servo amplifier allowing the current to flow into an actuator coil to restore the arm to its original position instantaneously using a feedback mechanism ( Fig. 1 b). Therefore, the arm of the torque sensor is always maintained at the null position during the measurement, and the sensor measures the torque linearly without deviation. The driving current of the servo amplifier is proportional to the torque, and is converted to a continuous voltage signal and stored on a computer in real time.
Calibration was performed using standard weights of 2.5–100 g at an interval of 2.5 g by hanging the weights on the arm of the torque sensor using a thin thread attached at a distance of 26.1 mm from the center via a low friction pulley. The relationship between the torque and the output voltage of the sensor was obtained ( Fig. 2 ).

The output signals from the potentiometer and the torque sensor were stored on a computer at a sampling rate of 1000 points/s using a data acquisition board USB-6009 (National instruments Co. Mopac Expwy, Austin, TX, USA) with 16 bit A/D converter and custom made software using Labview 7.1 (National instrument Co. Mopac Expwy, Austin, TX, USA). The switching on and off of the curing light was synchronized by the software with the initiation of data acquisition.
2.2
Measurement of the modulus change of composites during light curing
A certain volume (14.2 mm 3 ) of composite paste was measured using an aluminum mold and placed into a 2 mm gap between the upper and lower glass rods of the measuring unit (parallel plate geometry). The end faces of the glass parallel plates were sandblasted with 50 μm Al 2 O 3 powder and treated with one coat of a silane coupling agent (Porcelain primer, Bisco Inc., Schaunmburg, IL, USA). The light guide was positioned 2 mm from the sample. A dynamic oscillatory shear test was undertaken with an oscillation amplitude of 0.00579 rad and a frequency of 6 Hz. The oscillating strain was activated 10 s before beginning the light curing process to obtain a baseline. Five measurements were made for each composite at 25 ± 0.5 °C.
2.3
Theory of viscoelasticity
2.3.1
Dynamic oscillatory shear test
When a material is subjected to a sinusoidal oscillatory shear strain with frequency ω , the shear strain and shear stress are given by
shear strain γ ( t ) = γ o sin ω t
shear stress τ ( t ) = τ o sin ( ω t + δ )
In the latter equation, δ is the phase angle or phase lag between the stress and strain ( Fig. 3 a ). From these expressions, we can define two moduli:
G ′ = τ o γ o cos δ = G o cos δ and G ″ = τ o γ o sin δ = G o sin δ
where G ′ is the shear storage ( elastic ) modulus and G ″ is the shear loss ( viscous ) modulus . The storage modulus is a measure of the stored energy, i.e., the elastic part. The loss modulus is a measure of the energy lost as heat, i.e., the viscous part.

Alternatively, we can use complex variables and write:
γ ( t ) = γ o e i ( ω t )
τ ( t ) = τ o e i ( ω t + δ )
G ∗ = τ ( t ) γ ( t ) = τ o γ o e i δ = τ o γ o ( cos δ + i sin δ ) = G ′ + i G ″
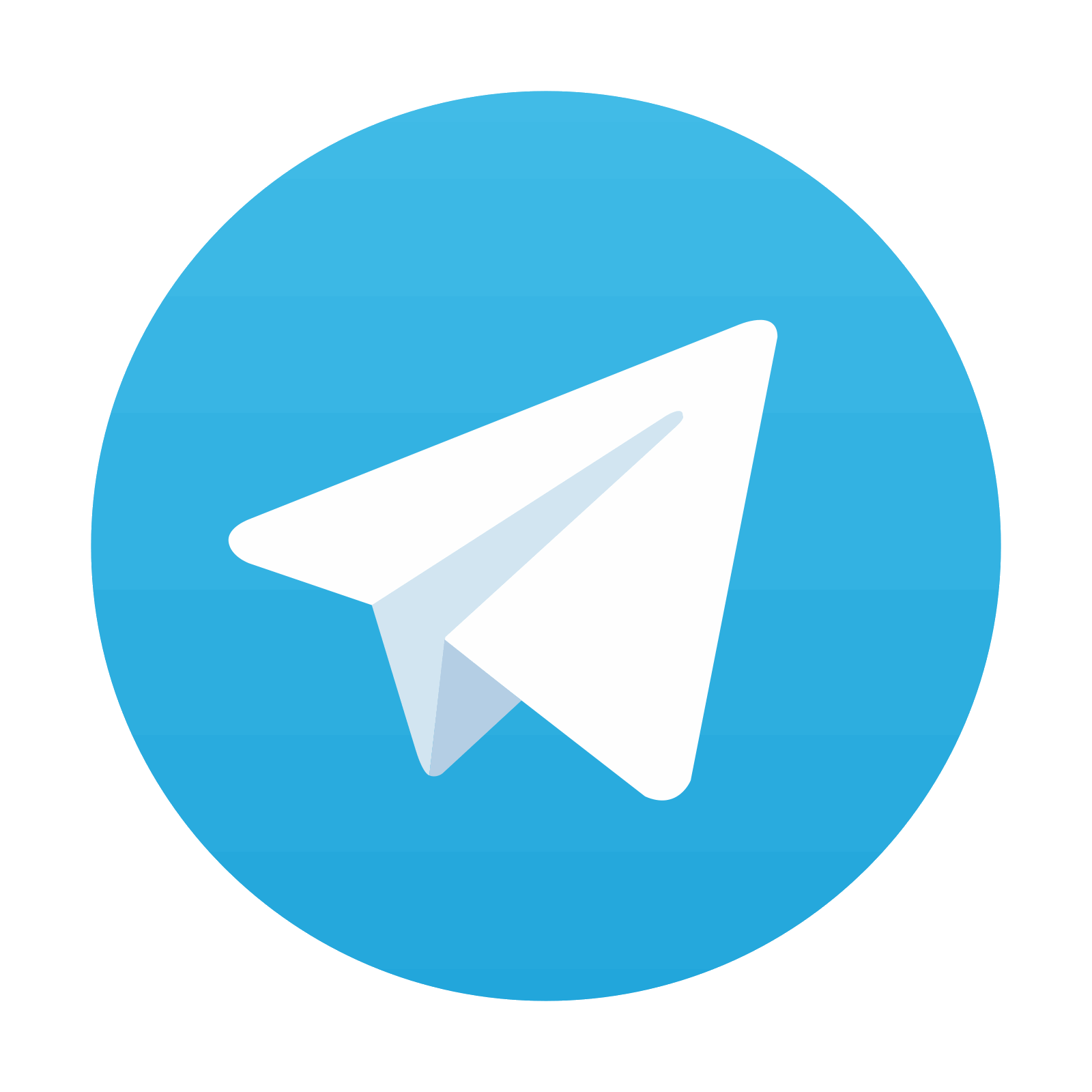
Stay updated, free dental videos. Join our Telegram channel

VIDEdental - Online dental courses
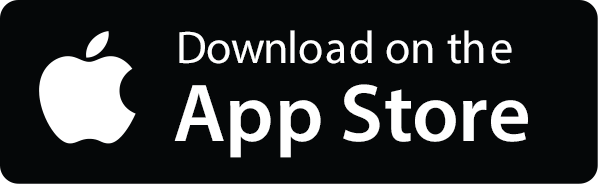
