div epub:type=”chapter” role=”doc-chapter”>
S. Stübinger et al. (eds.)Lasers in Oral and Maxillofacial Surgeryhttps://doi.org/10.1007/978-3-030-29604-9_18
18. Lasers in the Dental Laboratory
Abstract
For about 30 years, laser technology in all its different forms has been indispensable in the daily laboratory routine of dental technology. In the digital workflow, however, lasers are increasing rapidly. 3D printers are becoming increasingly important just like laser technology too. Resins can be processed easily and inexpensively with simple printers. Metals can already be laser-sintered in acceptable quality. The latest innovations even make it possible to print final sintered ZrO2 crowns.
Laser weldingCAD/CAMScannerZrO2StereolithographySLASelective laser meltingSLM
18.1 Laser for Joining Metals
The laser first became popular in dental laboratories in the early 1990s. With the broad introduction of titanium as a framework material, a suitable joining option had to be found. Laser welding was the easiest method.
The alternatives at that time were mainly bonding. The typical adhesive materials were plastics and therefore usually not heat-resistant. The temperature-resistant variants made of glass or ceramics were cumbersome and time-consuming to process. In addition, adhesives require a relatively large amount of space to guarantee a high mechanical load-bearing capacity. However, the “passive fit” is better than with all other alternatives.

Laborlink AG
Both joining options, bonding and soldering, were more than questionable, however, as far as the biocompatibility question, which really made titanium “in”, was concerned. Laser welding enabled us to join parts together with one and the same material.
Laser welding has remained an indispensable joining method for metal to this day. The laser can be used for almost all metals used in dental technology. Porous surfaces can be sealed with the laser or missing contact points can be created without great effort. Countless ready-made anchors and attachments are lasered onto all possible bases. With extensions, the laser makes it possible to attach retentions to model casted frameworks without destroying the surrounding plastic.
The main risks of laser welding are severe distortion and embrittlement of the material or its destruction (e.g. in titanium, if argon is not flooded enough). The different melting temperatures, thermal conductivity and surface reflection must also be taken into account.
18.2 CAD/CAM Laser as Scanner

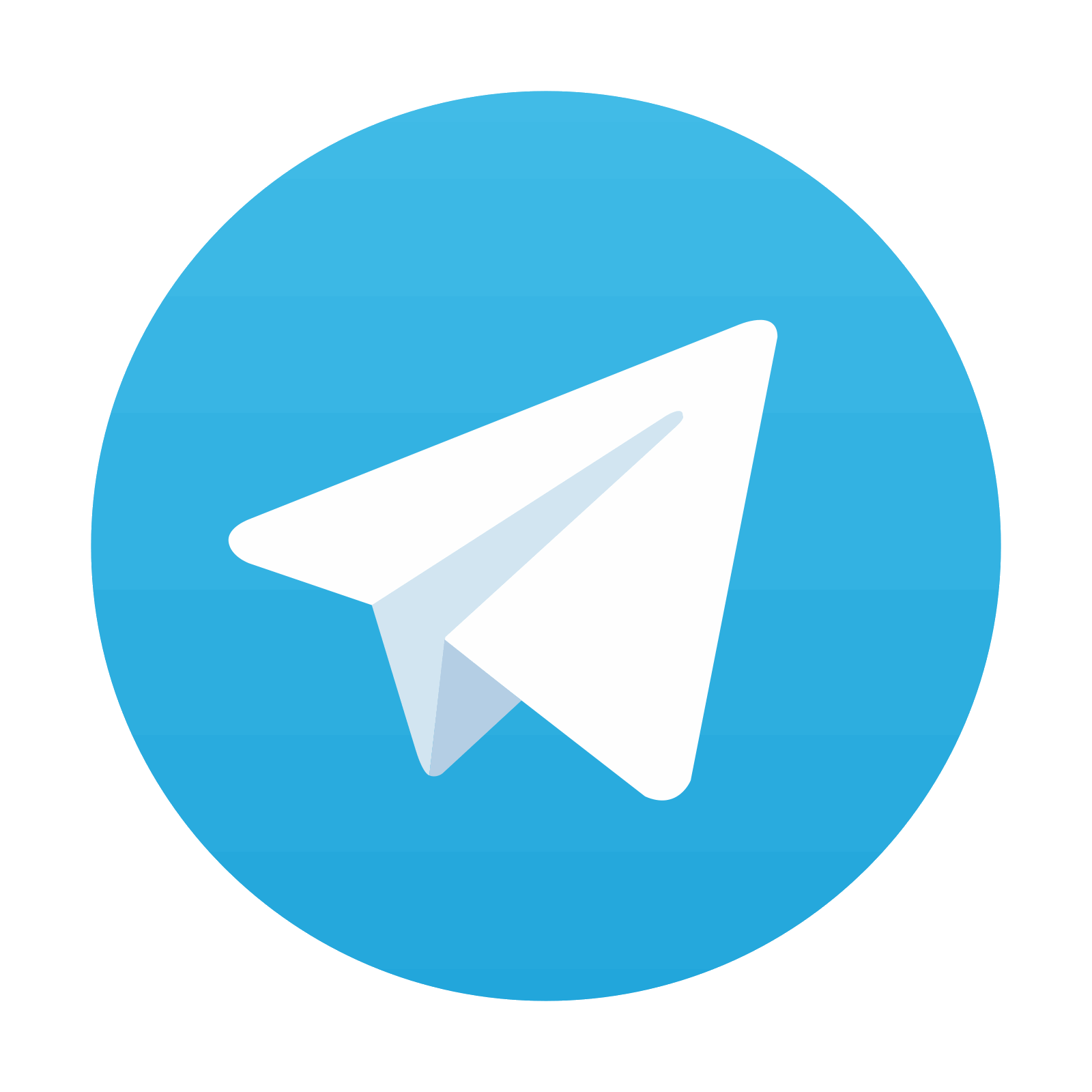
Stay updated, free dental videos. Join our Telegram channel

VIDEdental - Online dental courses
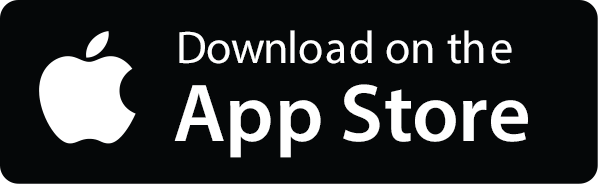
