Abstract
Mini-implants are widely used as skeletal anchorage in orthodontics. To reduce implant loss rate, sufficient primary stability is required. This study quantitatively analysed the impact of bone quality and pre-drilling diameter on the insertion torque of five different mini-implants. Twenty pig bone segments were dissected and embedded in resin. The insertion torques of two different mini-implant types (Tomas Pin, Dentaurum, Germany, 8 and 10 mm; and Dual Top, Jeil, Korea, 1.6 mm × 8 and 10 mm plus 2 mm × 10 mm) were measured. After preparation of the implant sites using pilot drill diameters 1.0, 1.1, 1.2 and 1.3 mm, 30 implants were inserted into each bone segment. Five reference implants were inserted into each segment for comparison. Micro CT evaluated bone compacta thickness. Insertion moments of orthodontic mini-implants, and hence primary stability, varied strongly depending on compacta thickness, implant design, and pre-drilling at the implant site. The Dual Top consistently showed higher primary stability than the Tomas Pin. Insertion moments higher than 230 Nmm resulted in fractures in some cases. Compacta thickness, implant design and preparation of implant site affect the insertion torque of mini-implants for orthodontic anchorage. To avoid fractures and high bone stresses, optimum pre-drilling diameters should be chosen.
One of the most important prerequisites for successful orthodontic treatment is a proper anchorage unit. Dental anchorage quality is often weakened due to periodontitis and missing teeth, especially in adults. In such cases, endosseous implants have proved useful as skeletal anchorage. Use of implants as anchorage reduces the need for patient compliance .
Compared with other skeletal anchorage devices, orthodontic mini-implants have become popular because of their versatility, minimal surgical invasiveness and low cost ( Fig. 1 ). The orthodontic therapy of adult patients sometimes only requires limited corrections, such as making molars upright or dealing with their intrusion. In such patients, skeletal anchorage by mini-implants offers new treatment options.

The literature primarily focuses on clinical applications. Implant failure rates were unsatisfactory in some of these studies. Which factors have an impact on loss rates and how relevant these factors are, is not well understood .
In dental implantology, the primary stability of an implant, as well as other factors such as bone quality and oral hygiene, directly determines its survival rate and reliability . Factors that have an impact on implant primary stability are bone quality, implant design, and insertion modalities.
O’S ullivan et al. , B eer et al. and da Cunha et al. recommended implant type selection and implant site preparation modalities based on the local bone quality. Despite the fact that primary stability is assumed to be a crucial factor for the successful use of orthodontic mini-implants , there is currently a lack of knowledge about the factors having an impact on this parameter. A valid method to assess the primary stability of implants quantitatively is the measurement of insertion torques . M otoyoshi et al. examined the insertion placement torques of mini-implants and recommended torque values of 50–100 Nmm (5–10 Ncm) for mini-implants with 1.6 mm diameter.
Based on this recommendation, the following questions are of interest to clinicians. Which implant designs reach this optimal area? What is the optimum insertion site preparation (pilot-drilling) required to reach this area. Does the implant site preparation procedure have to be adapted according to the bone quality/compacta thickness to reach the optimal area? At which torque values do the mini-implants break? These clinically important questions are not dealt with in the literature.
In a previously published study the pilot drilling depth had no relevant impact on the insertion torque . As a consequence, this study was conducted with a constant pilot drilling depth to achieve results with a statically higher value und to evaluate the exact relevance of the other factors such as implant design, compacta thickness and pilot drilling diameter.
The aim of this study was quantitatively to analyse the influence of these factors on the primary stability of five different mini-implants and to establish a recommendation for optimum preparation of the mini-implant insertion site, depending on the estimated bone quality.
Materials and methods
Two different mini-implant designs, the Tomas Pin (Dentaurum, Ispringen, Germany) and the Dual Top Anchor Screw (Jeil Medical Corporation, Seoul, Korea) of different sizes were examined. Five mini-implant types were tested: Tomas Pin 1.6 mm diameter × 8 mm length; Tomas Pin 1.6 mm × 10 mm; Dual Top Screw 1.6 mm × 8 mm; Dual Top Screw 1.6 mm × 10 mm; and Dual Top Screw 2.0 mm × 10 mm.
The ilium of pigs was chosen as the bone model. Compacta thickness of the bone segments was approximately 0.5 mm on the side towards the iliosacral joint and approximately 2.5 mm towards the hip joint ( Fig. 2 ). These values are comparable to the compacta thickness found in human maxilla and mandible. Segments, 5 cm × 5 cm, were prepared and embedded in resin (Probase, Ivoclar Vivadent, Schaan, Liechtenstein). Composite curing was performed under water cooling to avoid bone overheating from polymerisation energy. On the surface of the bone segments a raster of 30 implantation sites with a minimum distance of 4 mm between them was marked. Within a column (1–5) compacta thickness was nearly constant, inside a row (A–E) it increased continuously. The third row of each bone specimen was used as reference site. Measured insertion torques obtained from these implants (Dual Top 1.6 mm × 8 mm) were used to determine bone quality in the respective column ( Fig. 3 ).


Pilot drilling and insertion of mini-implants
The pilot drilling was performed using a bench drilling machine (Opti B 14 T, Rexon, Germany) at 915 rpm with pilot drills 1.1 and 1.2 mm (Dentaurum, Ispringen, Germany) and pilot drills from Dual Top system (Jeil Medical Corporation, Seoul, Korea) with diameters 1.0 and 1.3 mm.
Prior to the measurement of the insertion torques, the implants were manually inserted vertically to the bone surface using a handheld screwdriver (Jeil Medical Corporation, Seoul, Korea). The insertion depth was 7.3 mm for the 8 mm implants and 9.3 mm for 10 mm implants. All combinations of implant type and drill diameter were measured 25 times. In the case of the reference implants, pilot drilling was performed with a diameter of 1.0 mm. In this case, the insertion depth was 7.3 mm. Including the reference implants, 600 mini-implant insertions were conducted.
Measurement system
After the manually performed pre-insertion, final screwing by another 0.2 mm up to the definite insertion depth was performed by a robotic measurement system. The main component of the measuring system is a precision robot RX60 (StäubliTec-Systems GmbH, Bayreuth, Germany), which was equipped with a precision potentiometer (WHALE 300, Contelec, Biel/Bienne, Switzerland) functioning as a angle sensor as well a torque sensor (8625-5001, Burster Präzisionsmesstechnik GmbH Gernsbach Germany) ( Fig. 4 ). The moment sensor was coupled with the mini-implant using the driver shaft of the Dual Top system. The analogue signals delivered by the sensors were digitized by the multi-channel measuring device Spider 8 (Hottinger Baldwin Messtechnik GmbH, Darmstadt, Germany) and were stored in a personal computer.

Evaluation of the torque moments
The measuring system software was programmed so that the robot arm performed a rotation of 80° within 2 s. Considering the thread height of 0.9 mm, this represented a final insertion depth of 0.2 mm. After complete insertion, the implants were screwed out of the bone by a counter clockwise rotation of 80°. During rotation, insertion and removal torques were measured and recorded as a function of the rotation angle. Maximum torque values found in the measured data sets underwent further analysis.
Correlation of compacta thickness to insertion torques
The authors found a high correlation between compacta thickness, measured by micro CT ( Fig. 5 ), and insertion torques in earlier studies . Linear regression analysis delivered a correlation coefficient of R 2 = 0.83 ( P < 0.0001) with the following equation: y = 121.6 x + 9.35 ( Fig. 6 ). This equation, in combination with the reference implants, was used for the estimation of compacta thickness for all implantation sites. These data were used to analyse the insertion torques in this study. The measurements were examined using the following protocol: six bone segments were examined by micro CT (SkyScan micro CT 107 Torno NT version 3rd L.5, Skyscan, Aartselaar, Belgium). The data reconstruction and determination of the compacta thickness in the area of the five reference implants were carried out using the software Cone Beam Volumetric Reconstruction for Skyscan Micro CT instrument version 2.125 (Skyscan, Aartselaar, Belgium). The effective compacta thickness at the respective implant insertion site was computed as the mean value of the compacta thicknesses left and right of each of the overall 30 insertion sites (a 3D picture was rendered using Analyze 6.1 software by Bio Medical Imaging Resource Mayo Clinic, Rochester, MN, USA).


Statistical analysis
All maximum insertion torques were transferred to a pivot table (Excel 2003, Microsoft) and categorized depending on the parameters implant site preparation (pre-drilling diameter), implant type, and insertion depth.
The compacta thickness for each measurement was estimated using the following steps. Regression analysis between the insertion torques of the 30 reference implants and compacta thicknesses obtained from micro CT analysis. Calculation of the estimated compacta thickness for all 100 reference implants using the regression coefficient calculated. Columnwise transfer of the estimated compacta thicknesses to all the other measurements in the bone specimen.
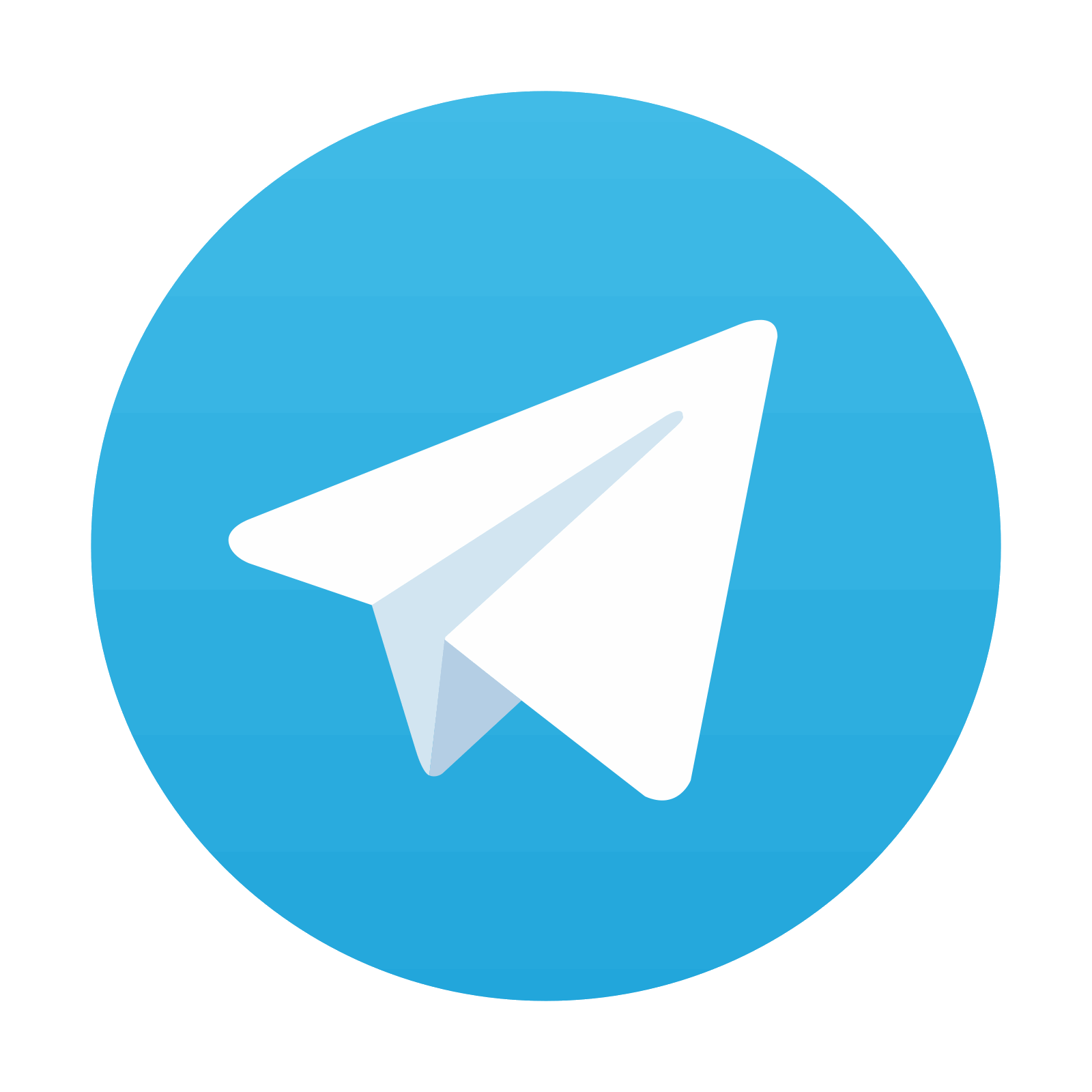
Stay updated, free dental videos. Join our Telegram channel

VIDEdental - Online dental courses
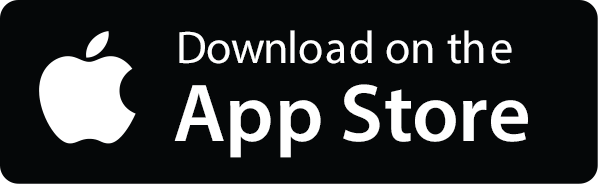
