Abstract
Objectives
To determine the effects of surface finish and mechanical loading on the rising toughness curve (R-curve) behavior of a fluorapatite glass-ceramic (IPS e.max ZirPress) and to determine a statistical model for fitting fatigue lifetime data with multiple flaw distributions.
Materials and methods
Rectangular beam specimens were fabricated by pressing. Two groups of specimens ( n = 30) with polished (15 μm) or air abraded surface were tested under rapid monotonic loading in oil. Additional polished specimens were subjected to cyclic loading at 2 Hz ( n = 44) and 10 Hz ( n = 36). All fatigue tests were performed using a fully articulated four-point flexure fixture in 37 °C water. Fractography was used to determine the critical flaw size and estimate fracture toughness. To prove the presence of R-curve behavior, non-linear regression was used. Forward stepwise regression was performed to determine the effects on fracture toughness of different variables, such as initial flaw type, critical flaw size, critical flaw eccentricity, cycling frequency, peak load, and number of cycles. Fatigue lifetime data were fit to an exclusive flaw model.
Results
There was an increase in fracture toughness values with increasing critical flaw size for both loading methods (rapid monotonic loading and fatigue). The values for the fracture toughness ranged from 0.75 to 1.1 MPa m 1/2 reaching a plateau at different critical flaw sizes based on loading method.
Significance
Cyclic loading had a significant effect on the R-curve behavior. The fatigue lifetime distribution was dependent on the flaw distribution, and it fit well to an exclusive flaw model.
1
Introduction
Fractography is an important tool in identification of the size and location of the fracture initiating crack or defect, the stress state at failure, and the presence or absence of local or global residual stress . Fractographic analysis of retrieved clinical restorations has been used to identify initial flaws and to determine the possible cause and mechanism of failure of restorations . It can also be used to determine the fracture toughness of the material by measuring the critical flaw dimensions on the fracture surfaces of standard geometry specimens .
Dental ceramics suffer from intrinsic, processing, and service flaws . It is challenging to predict the lifetimes of all-ceramic prostheses when multiple flaw types are present. Ceramic components show the presence of two or more types of flaws, with each flaw type having an independent distribution of flaw sizes . The presence of multiple flaw types can be detected by fractographic analysis showing more than one fracture initiating defect and a simultaneous deviation of strength data from the expected distribution function. The multiple flaw distributions can be divided into three types – concurrent, partially concurrent, and exclusive . If the flaw types are mutually exclusive within each specimen, then they are referred to as “exclusive flaw distributions”. When two flaw types are observed as in the present study, the probability of failure for the “exclusive flaw model”, P T , is given by the following equation,
P T = ( 1 − Π B ) P A + Π B P B
where Π B is the proportion of specimens having the flaw type B , P A is the probability of failure for specimens containing flaw type A , and P B is the probability of failure for specimens containing flaw type B .
Advanced ceramics such as partially stabilized zirconia, coarse-grained alumina, and silicon nitride show an increase in fracture toughness with increase in flaw size until a certain limit . This is called R-curve behavior. Previous studies have shown that the materials that exhibit R-curve behavior are susceptible to crack growth due to cyclic degradation . The mechanisms of cyclic degradation can be classified into two categories; intrinsic mechanisms where the cycle results in enhanced microstructural damage ahead of the crack tip (as in metals), and extrinsic mechanisms which act in the wake of the crack. In one extrinsic mechanism, premature contact upon unloading acts to diminish the effect of a crack-tip shielding process . Also, ceramics exhibiting grain-bridging show extrinsic cyclic degradation because of damage to the bridging zone . Kishimoto et al. studied the crack propagation behavior under static and cyclic loading in compact tension specimens of polycrystalline alumina with two types of average grain size. Cyclic loading decreased crack extension resistance to be below that for monotonic loading. This effect was greater in coarse-grained alumina compared to fine-grained alumina . Kruzic et al. investigated the crack growth under cyclic fatigue for both long and short cracks in 99.5% pure alumina. The crack growth rates were far higher at the same stress intensity factor range for short cracks than for long cracks, and fatigue thresholds were markedly lower for short cracks than for long cracks . Lathabai et al. tested disk specimens of alumina with indentation flaws under biaxial flexure. They showed that there was no significant cyclic degradation from possible damage to bridges for indentation cracks. However, the microstructure of the alumina used in the study might have been too fine for grain-bridging to happen .
Although currently available dental ceramic materials show R-curve behavior, they are not known to exhibit toughening due to grain-bridging. More knowledge about this area would advance the science of predicting the lifetimes of all-ceramic restorations. Thus, the first objective of this study was to determine the effects of surface finish and type of mechanical loading (monotonic vs. cyclic) on the rising toughness curve (R-curve) behavior of a fluorapatite glass-ceramic. The second objective of the study was to determine a statistical model for fitting fatigue lifetime data with multiple flaw populations. The hypotheses of the study were that cyclic loading has a significant effect on R-curve behavior of this glass-ceramic, and fatigue lifetime data with multiple flaw populations fit well to an exclusive flaw model.
2
Materials and methods
2.1
Specimen preparation
This study was performed on a pressable fluorapatite glass-ceramic (IPS e.max ZirPress, Ivoclar-Vivadent, Schaan, Liechtenstein). It is available in the form of prefabricated ingots, which must be injection molded into phosphate-based investment material via the lost-wax technique. The composition of IPS e.max ZirPress as provided by the manufacturer is (wt%) 57–62 SiO 2 , 12–16 Al 2 O 3 , 7–10 Na 2 O, 6–8 K 2 O, 2–4 CaO, 1.5–2.5 ZrO 2 , 1–2 P 2 O 5 , 0.5–1 F, and 0–6 other oxides. Rectangular beam specimens were fabricated to dimensions of 25 mm × 4 mm × 1.2 mm according to the ISO 6872 standard .
Rectangular bars of the abovementioned dimensions were cut from casting wax sheets (Kinco dental waxes, Kindt-Collins Company, Cleaveland, OH, USA). Sprueing, investing in the invest material (IPS PressVEST Speed, Ivoclar-Vivadent, Schaan, Liechtenstein), and preheating at 850 °C were performed following the manufacturer’s instructions. Immediately after wax burnout, ingots were placed into the open end of the mold, followed by an alumina plunger, and the whole assembly was placed into a press furnace (Multimat Touch & Press, Dentsply, Tulsa, OK, USA). This furnace uses lower air pressure than the air pressure of 5 bar recommended by the manufacturer. The mold was heated to 920 °C and held for 15 min, followed by a press time of 6 min at an air pressure of 2 bar. After cooling the investment ring to room temperature, divesting was carried out by airborne particle abrasion with glass beads (100 μm) at 4 bar pressure (for rough divestment) followed by at 2 bar pressure (for fine divestment) in an air abrasion unit (Quattro IS, Renfert, St. Charles, IL, USA).
Specimens for cyclic loading were ground to the final desired dimensions using a 30-μm diamond wheel and 200 g force with a polishing machine (Techprep, Allied High Tech, Rancho Dominguez, CA, USA). Specimens were polished to a 15-μm surface finish using circular rotating motion of diamond lapping films (30-μm film followed by 15-μm film). Thirty specimens were not polished but were treated by immersing in Invex liquid (Ivoclar-Vivadent) and cleaning in a sonicator (Aquasonic 150T, VWR Scientific Products, Radnor, PA) for 5 min, according to the manufacturer’s instructions. Subsequently, specimens were cleaned in running water and blown dry. The white reaction layer was removed by air abrasion with Al 2 O 3 particles (100 μm) at 2 bar pressure. The edges of all specimens were chamfered at a 45-degree angle using a motion parallel to the long axis of specimens with the help of a custom-made apparatus to minimize stress concentration and consequent failure from the edges during mechanical testing.
2.2
Mechanical testing
Polished specimens for cyclic fatigue were tested at two different frequencies, 2 Hz and 10 Hz, and at various peak stress levels ranging from 40 to 60 MPa, which were determined using fast fracture data in conjunction with ALTA PRO software (Reliasoft, Tucson, AZ, USA) to predict appropriate peak stress levels that corresponded to a small probability of fast fracture and achieved fatigue fracture of all specimens within the study timeline . The specimens for cyclic loading included two groups of 30 specimens each tested at 2 Hz and 10 Hz frequencies and a peak stress level of 45 MPa. The cyclic loading was applied using a custom-made fully articulated four-point flexure fixture in deionized water at 37 °C, and the number of cycles to failure and the lifetime were recorded for each specimen. Another group of 30 specimens with air abraded surface finish and a group of 30 polished specimens were tested in oil by rapid monotonic loading at a stressing rate of 1 MPa/s.
2.3
Fractography
All of the failed specimens were examined using fractographic techniques. The fracture toughness of each specimen was determined from the critical flaw dimensions and failure stress. The critical flaw depth, a , and half-width, b , were measured using an optical microscope (MZ12.5, Leica Microsystems, Bannockburn, USA) and a scanning electron microscope (SEM) (SUPRA 40, Carl Zeiss Microimaging, Thornwood, NY, USA). The stress intensity shape factor, Y , was determined for both the deepest point on the critical flaw and at the tensile surface using an equation developed by Newman and Raju . The critical flaw dimensions and failure stress were used for calculation of the fracture toughness using the following equation.
where K Ic is the fracture toughness of material, σ f is the failure stress, and a is the depth of the critical flaw. The specimens failing from edges and deep internal defects were excluded in determination of fracture toughness. For the purpose of comparing critical flaw sizes, the size of the equivalent semi-circular flaw radius, c , was calculated using the depth, a , and half-width, b , of the semi-elliptical flaw on the surface, so that the stress intensity factor is same for both flaws .
The fracture toughness values estimated from the specimens were compared to the corresponding critical flaw sizes to determine the presence of R-curve behavior. The following non-linear regression equation was used:
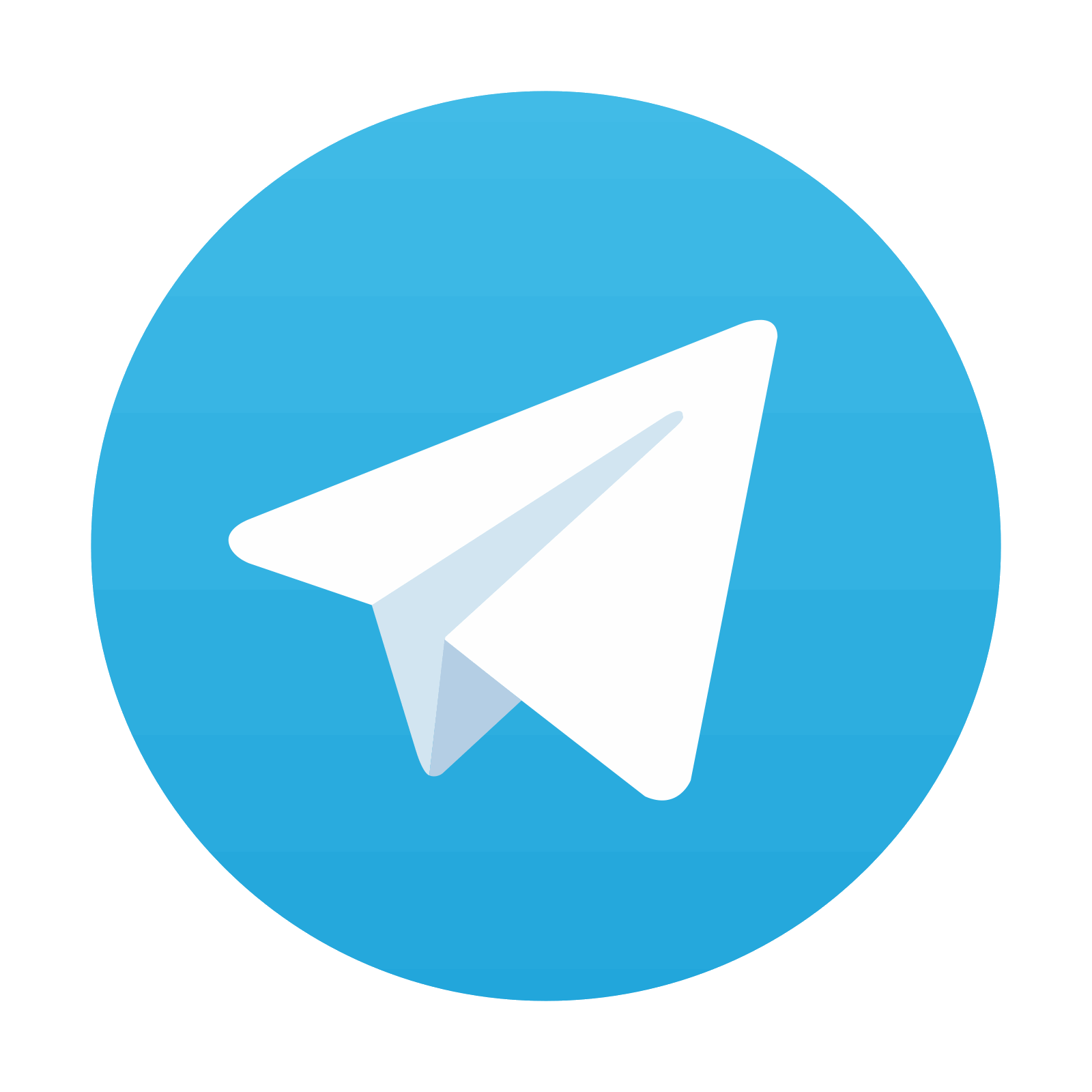
Stay updated, free dental videos. Join our Telegram channel

VIDEdental - Online dental courses
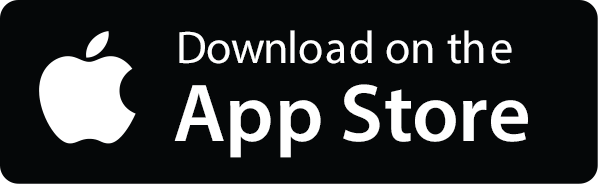
