Abstract
Objectives
The objective of this work was to develop a methodology for the prediction of fatigue life of the dentin–adhesive (d–a) interface.
Methods
At the micro-scale, the d–a interface is composed of dissimilar material components. Under global loading, these components experience different local stress amplitudes. The overall fatigue life of the d–a interface is, therefore, determined by the material component that has the shortest fatigue life under local stresses. Multiple 3d finite element (FE) models were developed to determine the stress distribution within the d–a interface by considering variations in micro-scale geometry, material composition and boundary conditions. The results from these models were analyzed to obtain the local stress concentrations within each d–a interface component. By combining the local stress concentrations and experimentally determined stress versus number of cycle to failure (S–N) curves for the different material components, the overall fatigue life of the d–a interface was predicted.
Results
The fatigue life was found to be a function of the applied loading amplitude, boundary conditions, microstructure and the mechanical properties of the material components of the d–a interface. In addition, it was found that the overall fatigue life of the d–a interface is not determined by the weakest material component. In many cases, the overall fatigue life was determined by the adhesive although exposed collagen was the weakest material component. Comparison of the predicted results with experimental data from the literature showed both qualitative and quantitative agreement.
Significance
The methodology developed for fatigue life prediction can provide insight into the mechanisms that control degradation of the bond formed at the d–a interface.
1
Introduction
In composite restorations that utilize a two-step adhesive system, dentin is etched with acidic agents to dissolve the mineral component. Dentin adhesive is applied to the etched surface to form a hybrid layer (HL); the hybrid layer is the demineralized dentin matrix infiltrated with adhesive resin. The characteristics of the hybrid layer depend upon the permeability and thickness of the demineralized dentin as well as the diffusibility of the applied adhesive resin. Typically, the hybrid layer has graded properties with depth . The thickness of the hybrid layer and amount of adhesive infiltration depends upon the type of adhesive, characteristics of the dentin substrate and operator technique. In some cases, the adhesive will not infiltrate to the depth of the demineralized dentin and under these circumstances, an exposed collagen layer may exist below the hybrid layer .
Clearly, the resultant dentin–adhesive (d–a) interface is a complex construct of dissimilar material components. The properties of these material components have a significant effect upon the mechanical performance and durability of the d–a interface. Based upon micro-scale structure-property measurements, we have previously developed an idealized microstructural representation of the d–a interface . This idealized model of the d–a interface can be utilized to perform micromechanical finite element (μFE) analyses.
The μFE analyses have shown that the each material phase at the d–a interface experiences different stress concentration under functional load . Since each component of the d–a interface reaches its failure strength at a different stress-level, the overall failure behavior is not determined by the weakest component. Indeed, the component whose stress concentration is closest to its failure strength determines the failure. Therefore, under function, the overall time dependent behavior of the interface is a complex function of the time-dependent behavior of the individual material phases.
In this paper, we have developed 3-dimensional models of the d–a interface and performed the μFE analyses. The resultant stress distributions were analyzed to show the effect of stress concentration on the overall fatigue failure behavior of the d–a interface. The stresses in the different phases of the d–a interface predicted by the μFE were used against S–N (stress-cycle) curves corresponding to each component of the d–a interface . The overall failure strength and S–N curve for the d–a interface were computed. The strength, the endurance limit, and the S–N curve of the d–a interface were found to be a function of the applied loading amplitude, the boundary conditions, the microstructure of the interface and the mechanical properties of the different material phases. The results from our methodology were compared with experimental data from the literature for model verification.
2
Materials and methods
2.1
Computational unit cell idealization for micro-scale 3d FE model
Based upon the results from micro-Raman spectroscopic, scanning acoustic microscopic and optical microscopic investigations , the d–a interface may be represented as shown in Fig. 1 . In this idealization the dentin–adhesive interface is considered to be composed of restorative dental composite, adhesive, the hybrid layer, exposed collagen, the partially demineralized dentin, and dentin. As a result, a 3d parallelepiped unit cell shown in Fig. 1 with square cross-section is used to represent the d–a interface.

To perform the micromechanical stress analysis a 3d linear elastic FE model of the representative unit cell was developed as shown in Fig. 2 . To reduce the computational effort, quarter symmetry was used in this study. The geometrical properties of the interface components were taken from the literature . The computational unit cell was 37.0 μm and 8.0 μm in longitudinal and transverse sections, respectively. The unit cell is further divided in different volumes to represent individual material components in the d–a interface as shown in Figs. 1 and 2 . The different material components are: adhesive–collagen composite (hybrid layer), adhesive, restorative dental composite, partially demineralized dentin, peritubular dentin and intertubular dentin. The adhesive appears as a layer underlying the restorative dental composite as well as the adhesive tags formed as the adhesive flows into the dentinal tubules (tubules were opened as a result of acid-etching). Also, the hybrid layer (adhesive–collagen composite) is divided into several layers in order to represent the variation of properties within this layer due to imperfect infiltration of adhesive into the demineralized dentin. The thicknesses (in μm) of the restorative dental composite, the adhesive layer, and the partially demineralized dentin are 5, 5, and 2.0, respectively. The width of the peritubular dentin varies and the height of the intertubular dentin is 18 μm. The thickness of the hybrid layer in this study varied from 10 to 5 μm.

2.2
Boundary conditions for the FE model
On the two symmetric sides as shown in Fig. 2 , symmetric boundary conditions were imposed and on the other two sides periodic boundary conditions were imposed. On the plane perpendicular to the Y -axis, the out-of-plane displacement (displacement in Y direction) is zero, i.e. that unit cell is only allowed to deform in the XZ plane. Similarly on the plane perpendicular to the X -axis, displacement in the X direction is zero and the unit cell is allowed to deform in the YZ plane. This means that the unit cell will retain its original cross-section under applied loading in the Z direction. The bottom surface of the unit cell is constrained in all three directions, i.e. zero displacement in X , Y and Z direction. The top surface of the idealized unit cell was subject to one of the following types of loading boundary conditions (1) stress controlled consisting of a uniform tensile traction of 20 MPa and (2) strain controlled consisting of displacement compatible with a uniform tensile unit strain.
These simplified boundary conditions are considered because the complex loading conditions at the d–a interface precludes modeling of actual boundary conditions. The complex loading condition at the d–a interface is clear from the stress distributions obtained for an example 3-d FE analysis of a restored tooth as shown in Fig. 3 . For this global analysis, a FEM model of mandibular right 2nd permanent molar was created. Quarter geometry was considered in order to reduce the computational time. The 3d global model considered the material component properties as follows: composite ( E = 30 GPa, ν = 0.30), enamel ( E = 70 GPa, ν = 0.20), dentin ( E = 28 GPa, ν = 0.25), and d/a interface ( E = 5 GPa, ν = 0.4). The model consists of 716,550 solid parabolic tetrahedral elements, of which 141,310 elements are within the 100 μm thick d–a interfacial region. Discretization refinement was performed to obtain converged results. The bottom boundary nodes of the 3D tooth were constrained in the vertical direction. The nodes on the surface in Z – X plane and surfaces in Y – Z planes were constrained in X and Y axis respectively. To simulate the physiological patterns of contact during chewing non-homogeneous morsels that contain a combination of hard gum and bone , a compressive traction force of 1 N/mm 2 is applied at 45° to the occlusal surface of the crown. The d–a interface stress distributions from the global model clearly show ( Fig. 3 c) that the actual loading conditions of the computational unit cell will be (i) complex, (ii) depend upon the occlusal loading conditions, and (iii) vary from location to location along the d–a interface. Qualitatively similar d–a interface stress distributions will be obtained for variations of the global model although the quantitative details may be different. Concurrent local–global modeling is too computationally intensive to provide practical, accurate results that capture all the physiologic loading conditions (such as soft versus hard morsels). On the other hand, it is well-known that traction and displacement boundary conditions provide an overall upper and lower-bound behavior of the computational unit-cell . Hence to calculate the bounds of the mechanical behavior of the unit cell under physiologic loading conditions, e.g. chewing, talking, grinding, etc. we have studied the behavior of the unit cell under two types of loading boundary conditions (listed above).

2.3
Material properties and meshing
We have assumed a linear elastic and isotropic behavior of the unit cell. In addition, we have assumed an imperfect bond between the resin tags and tubule walls, such that there is insignificant stress transfer between these two components. Mechanical loads under function are characterized by low amplitude relative to material strength and linear elasticity is a reasonable assumption for performing stress distribution analysis. The elastic properties for different phases in the unit cell are taken from the literature . Since the adhesive is a viscoelastic material , the effective elastic modulus of the adhesive is dependent on the loading rate. In our finite element calculation, we simulate the condition in which the load is applied at a relatively fast rate hence the elastic modulus of the adhesive corresponds to the value reported for a high loading rate . Material properties for the different material components are given in Table 1 .
Material | Young’s modulus, E (GPa) | Poisson’s ratio, ν |
---|---|---|
Composite | 30 | 0.29 |
Adhesive | 5 | 0.29 |
Peritubular dentin | 26 | 0.29 |
Intertubular dentin | 20 | 0.29 |
Partially demineralized dentin | 13 | 0.29 |
Hybrid layer-1-10 | 4–1.75 | 0.29 |
Free meshing is used to generate the mesh. This type of meshing is not constrained by the geometry hence we can mesh volumes with sharp edges and corners with minimum element distortion and better accuracy. In addition, convergence studies were performed to minimize the effect of element size. Different components in the 3d unit cell are meshed using 10 node parabolic tetrahedron elements. The size of the elements used for meshing depends upon the phase. Partially demineralized dentin and the proximal hybrid layer were meshed with an element size of 0.1 μm, the adhesive tag and peritubular dentin were meshed with 0.25 μm element size, and the other components were meshed with 0.5 μm element size. In the final discretized models, the total number of nodes was 575,705 and total number of elements was 409,345.
2.4
Parametric study
Parametric studies were performed on the computational unit cell to investigate the effect of changes in the physical characteristics of the d–a interface, including the thickness and the material properties of the hybrid layer. To study the effect of the d–a interface microstructure variation we have developed the following four models: Model 1 : Graded Hybrid Layer – in which the hybrid layer is assigned a linearly decreasing elastic modulus. The hybrid layer elastic modulus is taken to be 4 GPa close to the adhesive layer and 1.75 GPa at the interface with the partially demineralized dentin; Model 2 : Uniform Hybrid Layer – in which the hybrid layer is assigned a uniform elastic modulus; Model 3 : Thin Graded Hybrid layer – in which the hybrid layer is assigned linearly decreasing properties but its thickness is taken to be 5 μm, which is half that of Model 1; Model 4 : Without Partially Demineralized Dentin – to investigate cases in which the etching process results in an absence of the partially demineralized dentin zone. A total of 8 parametric models were developed, 4 models for the stress controlled case and 4 models for the strain controlled case.
2.5
Calculation of stress concentration factors
Stress concentration factor is defined as the ratio of highest stress experienced by the individual material components divided by the global stress which is applied on the d–a interface. In the FE calculations, the highest stress can occur in elements that are in narrow locations where several material components join together. These locations typically occupy an extremely small volume of the material component (one element) and, therefore they are not considered to be representative of the stress concentration of the material. To obtain a representative stress concentration factor, the top 5% of high stress experiencing elements of the particular component were considered. Top 5% data ensured that the stress concentration factor had a narrow distribution with a coefficient of variation of less than 10%. Out of this top 5% data, a 2 σ (where σ = standard deviation) criteria was used to discard any high stress elements which could have resulted from geometrical artifacts. The remaining elements were averaged to obtain the stress concentration in the particular material component. The stress concentration factor, denoted by f c , was then obtained as:
f c = σ l c σ g
where σ l c is the average peak stress in the material component, c , and σ g is the applied global stress on the unit cell top surface. The stress concentration factors for stress and strain controlled cases are shown in Table 2 for the four FE models considered in this work.
Phase | Model 1 | Model 2 | Model 3 | Model 4 | ||||
---|---|---|---|---|---|---|---|---|
(1) | (2) | (1) | (2) | (1) | (2) | (1) | (2) | |
Adhesive | 1.50 | 0.34 | 1.16 | 0.33 | 1.17 | 0.34 | 1.50 | 0.34 |
Exposed collagen | 1.04 | 0.30 | N/A | N/A | 1.04 | 0.31 | 1.05 | 0.31 |
Partially demineralized dentin | 1.18 | 0.69 | 1.18 | 0.73 | 1.16 | 0.72 | N/A | N/A |
Dentin(intertubular and peritubular) | 1.30 | 1.04 | 1.30 | 1.04 | 1.30 | 1.06 | 1.30 | 1.42 |
2.6
S–N curves for different material components of d–a interface
The S–N (stress amplitude versus number of cycles to failure) curves for the different material components are critical for the reliability of the fatigue life prediction of the d–a interface. Generally, there is a lack of this type of data for the various material components found at the d–a interface. To demonstrate our methodology for fatigue life prediction, we have only considered the following three components: dentin, exposed collagen and adhesive. There is limited S–N data available for the components that comprise the composite/adhesive/tooth interfaces. Other components such as the hybrid layer and composite should be considered, but this requires the availability of S–N data.
The S–N curve for dentin was obtained from the literature . This data was measured at frequencies of 2, 10 and 20 Hz and a stress ratio ( R s ) of 0.1. The stress ratio ( R s ) is defined as a ratio of the minimum to the maximum stress during a cycle. Collagen S–N data were based upon experiments for type I collagen fibers from wallaby tail tendons . These experiments were performed by keeping the minimum stress constant while increasing the maximum stress to obtain the data at different stress amplitudes. Thus the stress ratio varied from 0.57 to 0.14 for small to large stress amplitudes. If the fatigue tests were performed at the constant stress ratio of 0.1 then higher fatigue life would be expected at small stress amplitudes (see for example Fig. 11 of that gives the effect of stress ratio on S–N curves for unidirectional carbon/epoxy composites). In this case, the measured curve will be primarily affected in the small stress amplitude regime, however for our proof-of-concept calculations no modification was applied to the data. The S–N data for dentin adhesive was obtained from the experiments performed at a stress ratio of R s = 0.1 and frequency of 5 Hz .
The S–N curves for the three components, i.e. dentin, exposed collagen and adhesive, are fitted with a power law given by the following formula:
σ c = A ( N f ) B
where A and B are fitting constants and superscript c refers to material components. The experimental data along with the fitted curves are shown in Fig. 4 , where for collagen A = 52 MPa, B = −0.105 and R 2 = 0.67, for dentin A = 102 MPa, B = −0.073 and R 2 = 0.71, and for adhesive A = 62 MPa, B = −0.056 and R 2 = 0.90.

2.7
Calculation of S–N curve of d–a interface
For fatigue life prediction of the dentin–adhesive interface, the stress that developed in the different material components were compared against S–N (stress-cycle) curves corresponding to each component of the d–a interface. When a global stress is applied on the computational unit cell of the d–a interface, different components of the d–a interface experience different maximum stresses as seen from Table 2 . For example, the stress concentration in the adhesive tags varied from 1.16 to 1.50 times the applied load under the stress controlled conditions. The overall fatigue life of the d–a interface is governed by the fatigue life of the component with the shortest fatigue life at the local level. Thus by using S–N curves for the different components and combining them with the stresses from the linear elastic FE models, we can estimate the overall fatigue life of the d–a interface.
To obtain the master S–N curve for the d–a interface, we first establish the strength and the endurance limit of the d–a interface as these properties determine the maximum and minimum stress amplitude over which the S–N curves need to be computed. Strength is defined as stress at which the material will last for only 1 cycle under constant amplitude stress loading. The endurance limit, on the other hand, is defined as the stress amplitude at which the material will not fail under constant amplitude cyclic stress loading for an arbitrarily large number of cycles. The number of cycles in our methodology is taken to be 10 6 . The data from Fig. 4 are used to find the local strength and endurance limits for the three material components. The local strength is then divided by the stress concentration factors from Table 2 to obtain the factored strength and endurance limit for the three material components as shown in Table 3 . The lowest values define the global strength and endurance limit of the d–a interface as tabulated in Table 3 . It is noteworthy that the strength of the d–a interface is controlled by either the adhesive or the dentin, even though the exposed collagen is the weakest component. Once the strength and endurance limits of the d–a interface are determined, the master S–N curve for the d–a interface may be computed as summarized below:
Stress controlled | Strain controlled | |||||||
---|---|---|---|---|---|---|---|---|
Model 1 | Model 2 | Model 1 | Model 2 | |||||
S | EL | S | EL | S | EL | S | EL | |
Dentin | 78 | 29 | 78 | 29 | 98 | 36 | 98 | 36 |
Adhesive | 41 | 19 | 53 | 25 | 154 | 84 | 206 | 85 |
Exposed collagen | 50 | 12 | N/A | N/A | 161 | 30 | N/A | N/A |
d–a interface | 41 | 12 | 53 | 25 | 98 | 30 | 98 | 36 |
Step 1 : A global stress is applied to the d–a interface corresponding to a stress amplitude, defined as ( σ max – σ min )/2, that would typically be applied in a fatigue life determination experiment. Using Eq. (1) and the FE computed stress concentration factors given in Table 2 , the local stress-levels in the individual material components of the d–a interface are calculated.
Step 2 : The number of cycles to failure for the individual material components are computed by inverting the S–N relationship given in Eq. (2) as:
N f c = 10 log ( A ) − log ( σ a ) B
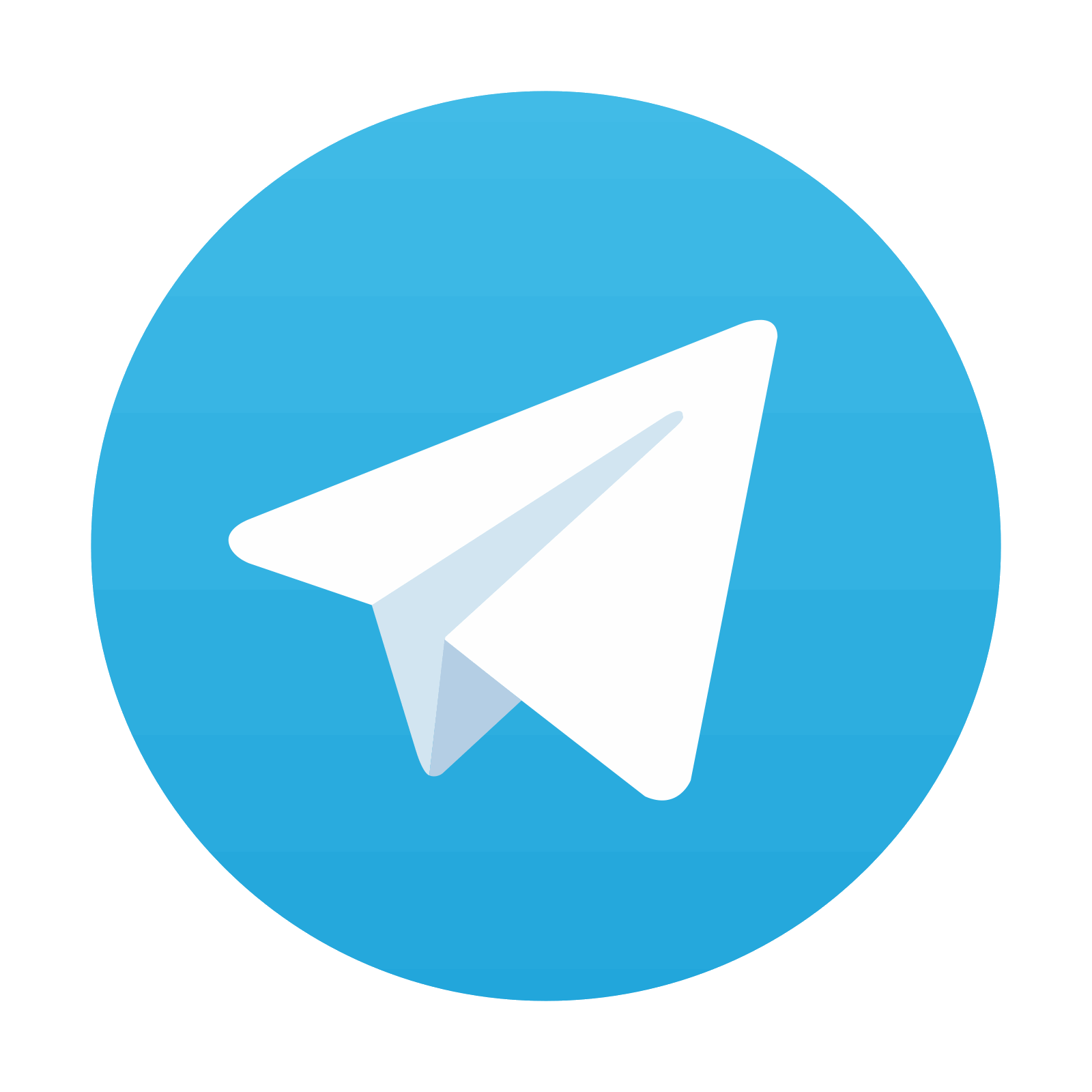
Stay updated, free dental videos. Join our Telegram channel

VIDEdental - Online dental courses
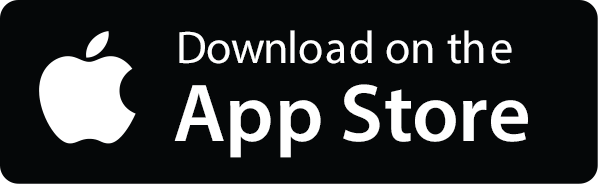
