Abstract
Objective
The effect of a novel light curing process, namely soft light energy release ( SLER ® ), on shrinkage, mechanical strength and residual stress of four dental restorative materials (DEI experience, Gradia Direct, Enamel Plus HFO and Venus) was investigated.
Methods
Composite specimens were fast cured through high level of power density and soft light energy release. Temperature, linear shrinkage and light power measurements were acquired in parallel in order to assess the effect of light modulation on temperature and shrinkage profiles during the light curing process and the following dark reaction phase. The small punch test and Raman spectroscopy were adopted to investigate the effect of SLER ® on mechanical strength and on internal stress, respectively.
Results
The soft light energy release photo-polymerization allows to reduce of about 20% the shrinkage rate and to increase the strength of fast light cured specimens. In addition, a more relaxed and homogeneous internal stress distribution was observed.
Significance
Properties of fast cured restorative materials can be improved by adopting the soft light energy release process.
1
Introduction
Composite resins are the most popular bearing materials for dental restorations . Their optical properties (i.e. translucency and color) allow attractive aesthetic restorations . These composites comprise a polymeric matrix, an inorganic reinforcement (i.e. fillers) and a coupling agent (e.g., silane). The organic matrix is mainly based on bisphenol A and glycidyl methacrylate (Bis-GMA) and/or other monomers such as triethylene glycol dimethacrylate (TEGDMA), 1,4-butanediol dimethacrylate (BDDMA) and urethane dimethacrylate (UDMA). The polymerization process takes place via a photo-activated reaction involving a photoinitiator system (e.g. camphorquinone and amine) contained in the composite resins . In clinical practice, the light curing process (LCP) is an important issue affecting the mechanical stability of a restored tooth; the clinician has not only to deal with the proper choice of materials for the specific restoration but also with the technological process involved in the place in service and setting of the specific composite.
The polymerization process forms covalent bonds between monomer, molecules which were originally subject to interaction through weaker van der Waals forces. Average intermolecular distances are therefore reduced , causing a reduction in free volume which is non-homogeneously distributed through the developing crosslinked network. These effects macroscopically translate into volumetric shrinkage.
The physical and chemical properties of the cured material are strongly dependent on the LCP, which strongly influences the degree of polymerization. An inadequate degree of cure leads to higher in vivo wear and marginal breakdown , increased cytotoxicity and lower mechanical properties (i.e. elastic modulus and strength) in vitro .
On the other hand, greater degree of cure of the polymeric matrix produces higher shrinkage and contraction stress . In clinical practice, the amount of stress building up in the composite, partially constrained by the cavity wall, depends on boundary conditions. In particular, the ratio between bonded and unbonded surfaces, the stiffness of the surrounding tissue, the photo-polymerization kinetics of the composite material in relation to its chemistry and the quality of the dentin substrate onto bond together all determine the amount of shrinkage or contraction stress developing into the material .
Free and constrained volume polymerization, investigated through shrinkage and contraction stress, respectively, represent the extremes of the infinite set of boundary conditions occurring in dental practice. Unfortunately, the variability of the physical conditions related to teeth restoration prevents to exactly define the effect of the photo-polymerization process on the mechanical stability of the involved materials (i.e. composite and tissues), however if internal stress exceeds local bond strength the resin–dentin interface and the filler–matrix interface will be jeopardized . Visco-elasticity further complicates the behavior of methyl methacrylate and dimethacrylate resins transforming, through polymerization, from a viscous phase to a highly cross-linked and vitrified network; the strain rate dependence of the mechanical properties of these resins are widely documented .
In this scenario, a variety of light curing units have been developed in order to optimise the LCP of dental restorative materials . Quartz–tungsten-halogen represents the most common light source for curing dental composites . Other fonts of light source, derived from a voltaic arch generating in mercury vapor or xenon bulbs and the argon LASER , have also been employed in dental practice. More recently, light emitting diode (LED) represents the alternative light source to traditional halogen units, the main advantage of the LED source is that its wavelength spectrum is narrow and can be precisely calibrated on camphorquinone absorption wavelength. Consequently, this source emits only light which is useful for curing the material thus providing high efficiency which in turns allows the design of a comfortable lightweight curing device .
A reciprocal relationship between light power density and exposure time on conversion of resin based composites has been observed . Accordingly, the advantage of using high power curing devices is that the time required for the polymerization process may be reduced, hence both the patient and the clinician benefit from a fast curing process. Moreover, errors related to the positioning of the light guide tip on the tooth to be restored are reduced, if compared to positioning errors occurring over a prolonged exposure time. Unfortunately, the hypothesis of reciprocity between light power density and exposure time on mechanical properties is not fully satisfied, especially when high power units are used ; mechanical properties of fast cured composites are lower than those obtained using similar energy level by means of low power density . Modulation of light intensity has been widely investigated in order to improve the performance of both light curing units and the cured dental composites. The main attempts in order to optimize the light curing process through the modulation of light intensity are based on soft start, pulsed and delay photo-polymerization . The main effect of the soft start, pulsed and delay photo-polymerization modulation is to shift in a time domain the gel point , that is the point at which the resin is cross-linked into a three dimensional network. However, the advantage of using a light delay is controversial . Increased softening after ethanol storage has been measured , but a remarkable reduction of shrinkage stress has been detected through two light step curing involving the soft pre-curing . Although the marginal gap and the stress raising at the dental tissue–composite interface may benefit from the soft start light modulation , a decrease of the degree of cure is also recognized . In the last decades a strong effort has been devoted to measure shrinkage or contraction stress developing in dental composites as a function of the light source and light modulation process . Interestingly, shrinkage and stress profiles recorded during LCP present a marked discontinuity as the light source is switched off, and this discontinuity is more pronounced as the light power is increased . It is important to point out that as the light source is switched off the polymeric matrix of the composite is already cross-linked and possibly vitrified, and it behaves as a visco-elastic solid or a composite whose matrix is in a glassy state . Therefore, the material has a low damping capability, especially if high rate of building-up stress is developed . Moreover, in clinical trials, the composite material interacts with the surrounding dental tissues , therefore high rate of stress contraction rising as the light is switched off will be directly transferred to the adhesive layer and to tissues, thus compromising the dentin–composite interface .
In order to reduce the rate of contraction stress or shrinkage developing as the light is switched off, we investigated the effect of a novel curing process based on the Soft Light Energy Release ( SLER ® ) on the composite shrinkage, strength and residual stress. Briefly, through the SLER ® process, light density is gradually reduced before the curing unit switches off ( Fig. 1 a) . This light modulation allows to control the cooling process of the composite ( Fig. 1 b). This novel approach aims to reduce the thermal effect on shrinkage ( Fig. 1 c), by slowly reducing the light energy at the end of a high power LCP. Within all the restrictions of this in vitro investigation, it will be shown that by avoiding sharp cooling effects through SLER ® , mechanical strength and stress distribution into the composite improve.

2
Materials and methods
The Mectron Starlight curing unit (Mectron Spa Genova, Italy) incorporating the SLER ® process was used ( Fig. 2 a) . The maximum power output measured by the Demetron LED radiometer (Kerr Corporation, USA) was 1400 mW/cm 2 . This curing unit allows to supply a standard or a SLER ® power curve. The standard curing conditions consists of a constant power output at the maximum intensity level, while the SLER ® power curve consists of a constant step at the maximum power followed by a soft light energy release ( Fig. 1 a). Table 1 reports light curing conditions adopted to polymerize composite materials.
LCP | Power (mW/cm 2 ) | Exposure time (s) | SLER time (s) | Energy dose (J/cm 2 ) |
---|---|---|---|---|
A | 1200 | 10 | – | 12 |
B | 1200 | 9 | 2 | 12 |
C | 1400 | 20 | – | 28 |
D | 1400 | 17.5 | 5 | 28 |
Shade A2, DEI Experience (DEI Italia, Italy), Gradia Direct (GC, Japan), Venus (Heraeus Kulzer, Germany) and Enamel Plus HFO (Micerium, Italy), composite materials were used. The polymeric matrix of Gradia Direct is UDMA, while the other composites are based on a mixture of Bis-GMA, TEGDMA, and BDDMA. Table 2 reports the polymeric matrix composition and weight amount of the investigated composites.
Material | Code | Polymeric matrix | Weight amount (%) |
---|---|---|---|
DEI Experience | DEI | BisGMA, UDMA, TEDMA | 22.5 |
Gradia Direct | GRD | UDMA | 25 |
Enamel Plus HFO | EPH | Bis-GMA, UDMA, BDDMA | 25 |
Venus | VNS | Bis-GMA, TEGDMA | 25 |
Linear shrinkage was investigated up to 400 s using composite specimens obtained from prismatic PTFE moulds of 5.0 mm × 5.0 mm × 1.5 mm ( Fig. 2 a). A Mylar strip ( Fig. 2 a) was used to handle the composite and to position this specimen between the mechanical arms ( Fig. 2 b) of a modified Instron extensometer (Instron, UK). The C-factor , that is the ratio between bonded and unbonded surfaces, was 0.2. Programs C and D ( Table 1 ) provide an energy of 28 J/cm 2 were used to polymerize composite materials. Shrinkage measurements were performed in the direction perpendicular to the light curing front (direction x of Fig. 2 b) Shrinkage, temperature and light power measurements were performed in parallel. A filtered photocell obtained from a Demetron LED radiometer (Kerr Corporation, USA) was used to monitor light power level ( Fig. 2 b). This approach has already been adopted to trigger shrinkage measurements . Disposable K-type thermocouples were used to measure temperature profiles during LCP and DRP. The mini-screws of a micromanipulator facilitated the gentle and precise positioning of the thermocouple in the side of the specimen opposite to the light tip guide ( Fig. 2 b). On line light power, linear shrinkage and temperature measurements were performed using the National Instrument DAC (National Instruments, USA) driven by Signal Express software (National Instruments, USA). Data were acquired at a speed of 50 p/s. For each composite 20 specimens were used equally divided into two sub-groups according to the LCP (i.e. standard or SLER ® process).
Mechanical properties were investigated using the small punch test set-up (ASTM F 2183) which covers the determination of mechanical behavior by small punch testing of miniature disk specimens ( Fig. 2 a) having a thickness of 0.5 mm and diameter of 6.4 mm. The diameter of these specimens is lower than the diameter of the light guide tip of the curing unit, therefore specimens have been light cured through a single step light shot. These specimens were polymerized providing a light energy of 12 J/cm 2 using programs A and B ( Table 1 ). The rationale for using an amount of energy lower than that used for shrinkage specimens is based upon on specimen thickness . Stainless steel moulds were manufactured to perform small punch tests ( Fig. 2 c) at a speed 0.5 mm/min. For each composite, 20 specimens were used equally divided into two sub-groups each of which underwent one of two different LCPs, i.e. the standard or SLER ® process.
For the DEI composite, internal stress of disc specimens ( Fig. 2 a) was detected through Raman piezo-spectrometry, the consistency of this technique relies on a linear correlation existing between Raman band broadening and stress reported for polymers such as polyethylene . Briefly, a probe volume is identified into the material through the focal point of a LASER beam ( Fig. 2 d). The observed intensity of Raman band is interpreted as an intensity distribution of scattered light around the focal point, described by the probe function. Raman band broadening is related to the frequency distribution of the light scattered by each aromatic ring, thus depending on the deformation distribution of benzene groups inside the probe volume . The T64000 Horiba/JobinYvon spectrophotometer equipped with a green argon LASER (wavelength of 514 nm) was used. Spectra were collected from the surface of each specimen down to a maximum depth of 150 μm at step of 25 μm (position accuracy of 0.1 μm). Disc specimens were polymerized in PTFE moulds ( Fig. 2 a) using programs A and B ( Table 1 ) defining the standard and the SLER ® samples, respectively. A Mylar strip was used to cover the side of the composite during the LCP in order to prevent air inhibition. 10 specimens were used equally divided in two sub-groups according to LCP (i.e. standard and SLER ® process). Control specimens were represented by relaxed specimens obtained from a sample of standard cured specimens and a sample of SLER ® cured specimens which underwent a heating step up to 100 °C and a slow cooling (relaxation step) to room temperature at 1 °C/min. The not-cured composite paste was used as reference or blank control. Data were expressed through full width at half maximum (FWHM) of the Raman band located at 1610 cm −1 associated to the in-plane stretching vibration mode of the aromatic ring.
One-way ANOVA at a significance level of 0.05 was used to assess differences in a fixed group (i.e. a specific composite of Table 2 ) cured through standard or SLER ® process. Two-way ANOVA at a significance level of 0.05, followed by the Tukey post hoc test, was used to compare properties of the investigated set of composites.
2
Materials and methods
The Mectron Starlight curing unit (Mectron Spa Genova, Italy) incorporating the SLER ® process was used ( Fig. 2 a) . The maximum power output measured by the Demetron LED radiometer (Kerr Corporation, USA) was 1400 mW/cm 2 . This curing unit allows to supply a standard or a SLER ® power curve. The standard curing conditions consists of a constant power output at the maximum intensity level, while the SLER ® power curve consists of a constant step at the maximum power followed by a soft light energy release ( Fig. 1 a). Table 1 reports light curing conditions adopted to polymerize composite materials.
LCP | Power (mW/cm 2 ) | Exposure time (s) | SLER time (s) | Energy dose (J/cm 2 ) |
---|---|---|---|---|
A | 1200 | 10 | – | 12 |
B | 1200 | 9 | 2 | 12 |
C | 1400 | 20 | – | 28 |
D | 1400 | 17.5 | 5 | 28 |
Shade A2, DEI Experience (DEI Italia, Italy), Gradia Direct (GC, Japan), Venus (Heraeus Kulzer, Germany) and Enamel Plus HFO (Micerium, Italy), composite materials were used. The polymeric matrix of Gradia Direct is UDMA, while the other composites are based on a mixture of Bis-GMA, TEGDMA, and BDDMA. Table 2 reports the polymeric matrix composition and weight amount of the investigated composites.
Material | Code | Polymeric matrix | Weight amount (%) |
---|---|---|---|
DEI Experience | DEI | BisGMA, UDMA, TEDMA | 22.5 |
Gradia Direct | GRD | UDMA | 25 |
Enamel Plus HFO | EPH | Bis-GMA, UDMA, BDDMA | 25 |
Venus | VNS | Bis-GMA, TEGDMA | 25 |
Linear shrinkage was investigated up to 400 s using composite specimens obtained from prismatic PTFE moulds of 5.0 mm × 5.0 mm × 1.5 mm ( Fig. 2 a). A Mylar strip ( Fig. 2 a) was used to handle the composite and to position this specimen between the mechanical arms ( Fig. 2 b) of a modified Instron extensometer (Instron, UK). The C-factor , that is the ratio between bonded and unbonded surfaces, was 0.2. Programs C and D ( Table 1 ) provide an energy of 28 J/cm 2 were used to polymerize composite materials. Shrinkage measurements were performed in the direction perpendicular to the light curing front (direction x of Fig. 2 b) Shrinkage, temperature and light power measurements were performed in parallel. A filtered photocell obtained from a Demetron LED radiometer (Kerr Corporation, USA) was used to monitor light power level ( Fig. 2 b). This approach has already been adopted to trigger shrinkage measurements . Disposable K-type thermocouples were used to measure temperature profiles during LCP and DRP. The mini-screws of a micromanipulator facilitated the gentle and precise positioning of the thermocouple in the side of the specimen opposite to the light tip guide ( Fig. 2 b). On line light power, linear shrinkage and temperature measurements were performed using the National Instrument DAC (National Instruments, USA) driven by Signal Express software (National Instruments, USA). Data were acquired at a speed of 50 p/s. For each composite 20 specimens were used equally divided into two sub-groups according to the LCP (i.e. standard or SLER ® process).
Mechanical properties were investigated using the small punch test set-up (ASTM F 2183) which covers the determination of mechanical behavior by small punch testing of miniature disk specimens ( Fig. 2 a) having a thickness of 0.5 mm and diameter of 6.4 mm. The diameter of these specimens is lower than the diameter of the light guide tip of the curing unit, therefore specimens have been light cured through a single step light shot. These specimens were polymerized providing a light energy of 12 J/cm 2 using programs A and B ( Table 1 ). The rationale for using an amount of energy lower than that used for shrinkage specimens is based upon on specimen thickness . Stainless steel moulds were manufactured to perform small punch tests ( Fig. 2 c) at a speed 0.5 mm/min. For each composite, 20 specimens were used equally divided into two sub-groups each of which underwent one of two different LCPs, i.e. the standard or SLER ® process.
For the DEI composite, internal stress of disc specimens ( Fig. 2 a) was detected through Raman piezo-spectrometry, the consistency of this technique relies on a linear correlation existing between Raman band broadening and stress reported for polymers such as polyethylene . Briefly, a probe volume is identified into the material through the focal point of a LASER beam ( Fig. 2 d). The observed intensity of Raman band is interpreted as an intensity distribution of scattered light around the focal point, described by the probe function. Raman band broadening is related to the frequency distribution of the light scattered by each aromatic ring, thus depending on the deformation distribution of benzene groups inside the probe volume . The T64000 Horiba/JobinYvon spectrophotometer equipped with a green argon LASER (wavelength of 514 nm) was used. Spectra were collected from the surface of each specimen down to a maximum depth of 150 μm at step of 25 μm (position accuracy of 0.1 μm). Disc specimens were polymerized in PTFE moulds ( Fig. 2 a) using programs A and B ( Table 1 ) defining the standard and the SLER ® samples, respectively. A Mylar strip was used to cover the side of the composite during the LCP in order to prevent air inhibition. 10 specimens were used equally divided in two sub-groups according to LCP (i.e. standard and SLER ® process). Control specimens were represented by relaxed specimens obtained from a sample of standard cured specimens and a sample of SLER ® cured specimens which underwent a heating step up to 100 °C and a slow cooling (relaxation step) to room temperature at 1 °C/min. The not-cured composite paste was used as reference or blank control. Data were expressed through full width at half maximum (FWHM) of the Raman band located at 1610 cm −1 associated to the in-plane stretching vibration mode of the aromatic ring.
One-way ANOVA at a significance level of 0.05 was used to assess differences in a fixed group (i.e. a specific composite of Table 2 ) cured through standard or SLER ® process. Two-way ANOVA at a significance level of 0.05, followed by the Tukey post hoc test, was used to compare properties of the investigated set of composites.
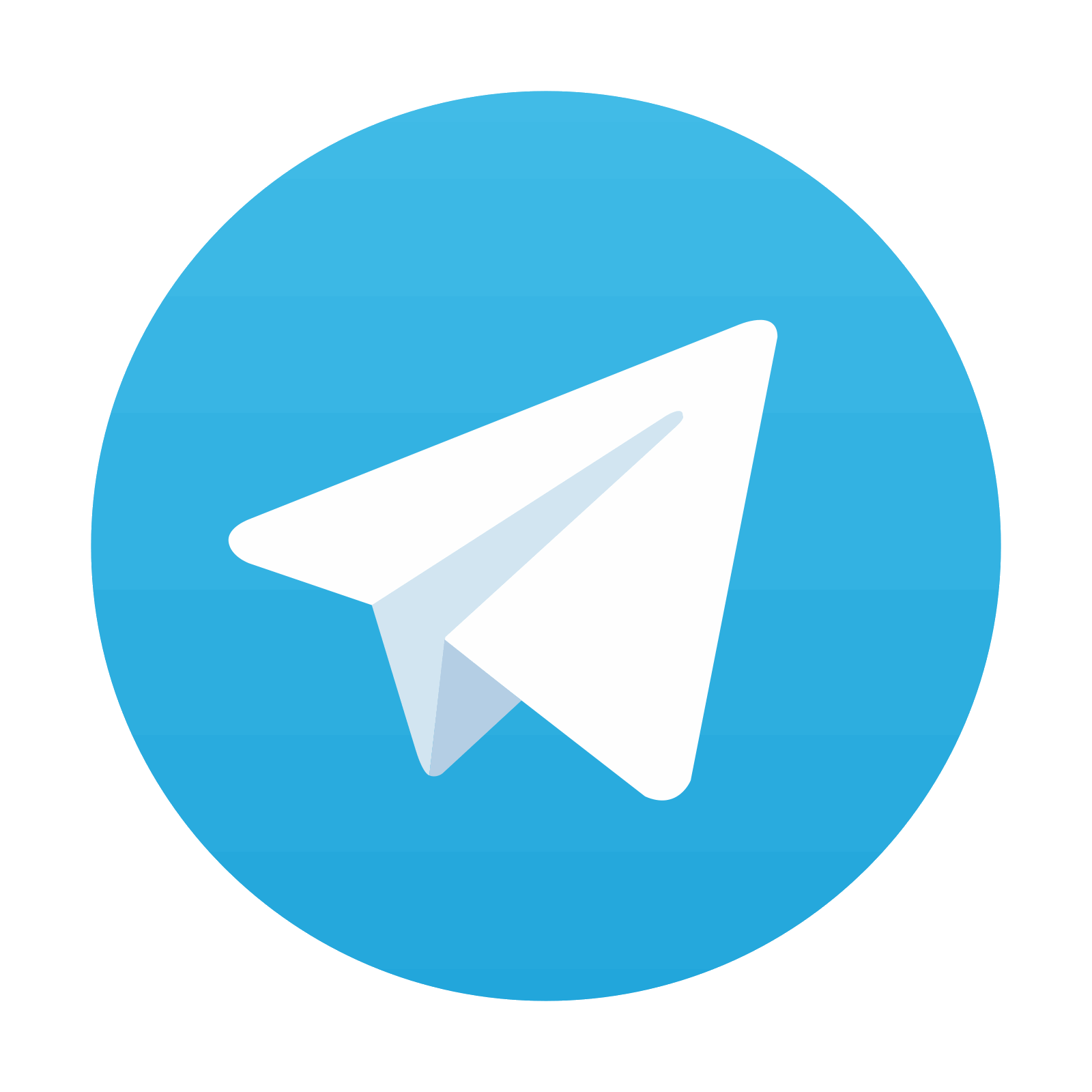
Stay updated, free dental videos. Join our Telegram channel

VIDEdental - Online dental courses
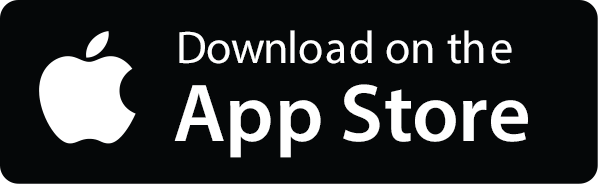
