Graphical abstract

Highlights
- •
Physical properties of a fiber-reinforced CAD/CAM resin disc (TRINIA) were examined.
- •
TRINIA demonstrated distinct anisotropy.
- •
TRINIA can be superior restorative material when specifying direction of mesh layers.
Abstract
Objectives
This study aimed to investigate physical properties of a fiber-reinforced CAD/CAM resin disc, which included woven layers of multi-directional glass fibers.
Methods
Fiber orientations of CAD/CAM specimens (TRINIA, SHOFU) were specified as longitudinal (L), longitudinal-rotated (LR), and anti-longitudinal (AL). A fiber-reinforced composite (everX posterior, GC (E)) and a conventional composite (Beauti core flow paste, SHOFU (B)) were also tested.
A three-point bending test and a tensile test with notchless prism-shaped specimens were conducted using a universal testing machine (AUTOGRAPH AG-IS, Shimadzu). A water absorption test was also carried out after the specimens were stored in water for 24 h or 1 week. Flexural strength and fracture toughness were obtained by conducting a three-point bending test.
Results
TRINIA L and LR groups showed significantly high flexural strength (254.2 ± 22.3 and 248.8 ± 16.7 MPa, respectively). Those were approximately 2.5 times higher than those in AL, E, and B groups (96.8–98.0 MPa) ( p < 0.05, ANOVA and Tukey HSD test). No significant difference was shown in flexural modulus among the experimental groups. The fracture toughness in L group (9.1 ± 0.4 MPa/m 1/2 ) was found to be significantly higher than those in other groups (1.9–3.0 MPa/m 1/2 ; p < 0.05). TRINIA group demonstrated significantly lower water absorption (4.7 ± 1.9 μg/mm 3 ) than did E (16.1 ± 3.1 μg/mm 3 ) and B (17.3 ± 3.7 μg/mm 3 ) groups ( p < 0.05).
Significance
TRINIA demonstrated distinct anisotropy. TRINIA can be used as a superior restorative material when specifying directions of its fiber mesh layers.
1
Introduction
In recent years, restorative treatments for preserving sound tooth structures with minimal intervention to the dentin have become important, based on the concept of minimal intervention dentistry (MID) . Composite resin have been widely used to achieve the MID concept. Hybrid resin developed for restoring molars has been clinically successful. These positive results have expanded the indications of composite resin in a wide range of restorations, such as fixed partial dentures and full-mouth rehabilitation . Subsequently, various attempts have been made to improve the mechanical properties of composite resin to meet this clinical demand.
In the industry, fibers have been used as reinforcement of resin, called as the fiber-reinforced plastic (FRP) . FRP is also used in dentistry. The representative examples of FRP in dentistry are hybrid resin for crown restoration, fiber post, high strength composite resin bridge, and CAD/CAM glass fiber reinforced resin. In all these materials, the fiber contained in FRP should be able to bear the tensile and bending stress and need to firmly adhere to resin matrix .
There are three patterns of fiber forms in FRP; random short fiber reinforced type (RSFRT), unidirectional continuous fiber reinforced type (UCFRT), and textile laminate reinforced type (TLRT). RSFRT is reinforced by short fibers randomly arranged in the matrix resin. UCFRT is reinforced by continuous fibers arranged unidirectionally in the matrix resin. TLRT is reinforced by tailoring fiber bundles into mesh fabrics. However, contributions of these fibers in improving the mechanical properties of FRP have not been clearly demonstrated. In particular, the effects of forms and directions of the fibers on reinforcing restoratives need to be comprehensively investigated.
Recent developments in digital technologies have significantly progressed the production of a restorative crown, especially CAD/CAM systems. A CAD/CAM crown can be made now by a simple process of milling a hybrid composite or a ceramic block without using complex technical procedures.
In this study, a glass fiber reinforced resin disc, TRINIA (SHOFU, Kyoto, Japan), was used, which was composed of 55 wt% glass fibers and 45 wt% epoxy resin matrix. A TRINIA disc, with fibers aligned as meshes and layers in a disc, seems to have good potential to produce various kinds of restorations by CAD/CAM system .
The purpose of this study was to evaluate flexural strength (FS), fracture toughness (FT), and water absorption of CAD/CAM glass fiber reinforced resin – TRINIA – by regulating the directions of fiber layers.
2
Materials and methods
2.1
Materials
Materials used in this study are presented in Table 1 . A glass fiber-reinforced resin disc (TRINIA, SHOFU, Kyoto, Japan) was composed of 45 wt% epoxy resin matrix and 55 wt% multi-directionally interlaced glass fibers, which aligned woven layers parallel to the top surface of the disc. Exposed fiber size was not disclosed. By SEM observation, the width and thickness of E-glass fibers were 1.2–1.5 mm and 0.1–0.4 mm, respectively. A fiber-reinforced composite resin (everX Posterior, GC, Tokyo, Japan) contained 8.6 wt% short E-glass fibers (approximately 200 μm) and 67.7 wt% barium glass fillers. A conventional composite resin (Beauti core flow paste, SHOFU) containing barium glass fillers was used as the control material.
TRINIA (SHOFU, Kyoto, Japan) Lot No. 037970914 |
glass fiber: 55 wt%, epoxy matrix resin: 45 wt% |
everX posterior (GC, Tokyo, Japan) Lot No. 1808201 |
Bis-GMA, TEGDMA, PMMA, beamium glass fillers: 67.7 wt%, e-glass fiber: 8.6 wt%, Silica dioxide: 5 wt% |
Beauti core flow paste (SHOFU, Kyoto, Japan) Lot No. 111611 |
Bis-GMA, TEGDMA, barium glass fillers |
2.2
Preparation of CAD/CAM fiber-reinforced resin specimens
Beam-, prism-, and disc-shaped specimens were prepared using a CAD/CAM system of a scanner (S-WAVE scanner D2000, SHOFU), a software (GO2 dental, SHOFU), and a milling machine (DWX-50, Roland, Shizuoka, Japan) for processing the resin disc in all the experiments.
Beam-shaped specimens were specified into three groups (longitudinal, longitudinal-rotated, and anti-longitudinal) according to the glass fiber orientations ( Fig. 1 B) . In longitudinal group, multi-directional glass fibers were layered longitudinally parallel to the specimen. In longitudinal-rotated group, the specimen was rotated by 90 degrees to a longitudinal one. In anti-longitudinal group, multi-directional glass fibers were layered vertical to the long axis of a specimen.

Prism-shaped specimens were specified into two groups (longitudinal and anti-longitudinal) according to the glass fiber orientations similar to the beam-shaped specimens ( Fig. 1 C).
Disc-shaped specimen used was 15 mm in diameter and 1 mm in height. The multi-directional glass fibers were layered parallel to the upper surface of the specimen.
2.3
Measurement of flexural strength
Three-point bending test was conducted according to ISO 4049 . Five specimens (2 × 2 × 25 mm) were created from each material. Each specimen was prepared according to ISO 4049 and the manufacturer’s instructions. Beam-shaped specimens of composite resin materials (everX posterior and Beauti core flow paste) were created in a half-split stainless-steel mold. As for Beauti core flow paste, the light was cured with an irradiance of 2000 mW/cm 2 for 10 s with 4.6 mm distance from curing tip. As for everX posterior, the light was cured with an irradiance of 2000 mW/cm 2 for 10 s with 4.0 mm distance from curing tip. The curing tip was placed at the center of each specimen and then moved to the section next to the center overlapping the previous section by half the diameter of the curing tip (total nine times). The other side of the center was irradiated in the same way. Polymerization of the composites was carried out using an LED light-curing unit (PenCure 2000, MORITA, Osaka, Japan). The specimens were stored at 37°C for 24 h before testing.
The specimen set is presented in Fig. 2 A (test span: 20 mm, cross-head speed: 0.75 mm/min, indenter: 2 mm diameter) and was loaded in a universal testing machine (AUTOGRAPH AG-IS, Shimadzu, Kyoto, Japan). A load-displacement curve was recorded using a software (TRAPEZIUM, Shimadzu).

Subsequently, FS ( σ ) and elastic modulus ( E ) were calculated using following formula .
σ=3PL2wt2,
σ=3PL2wt21+6SL2-3StL2,
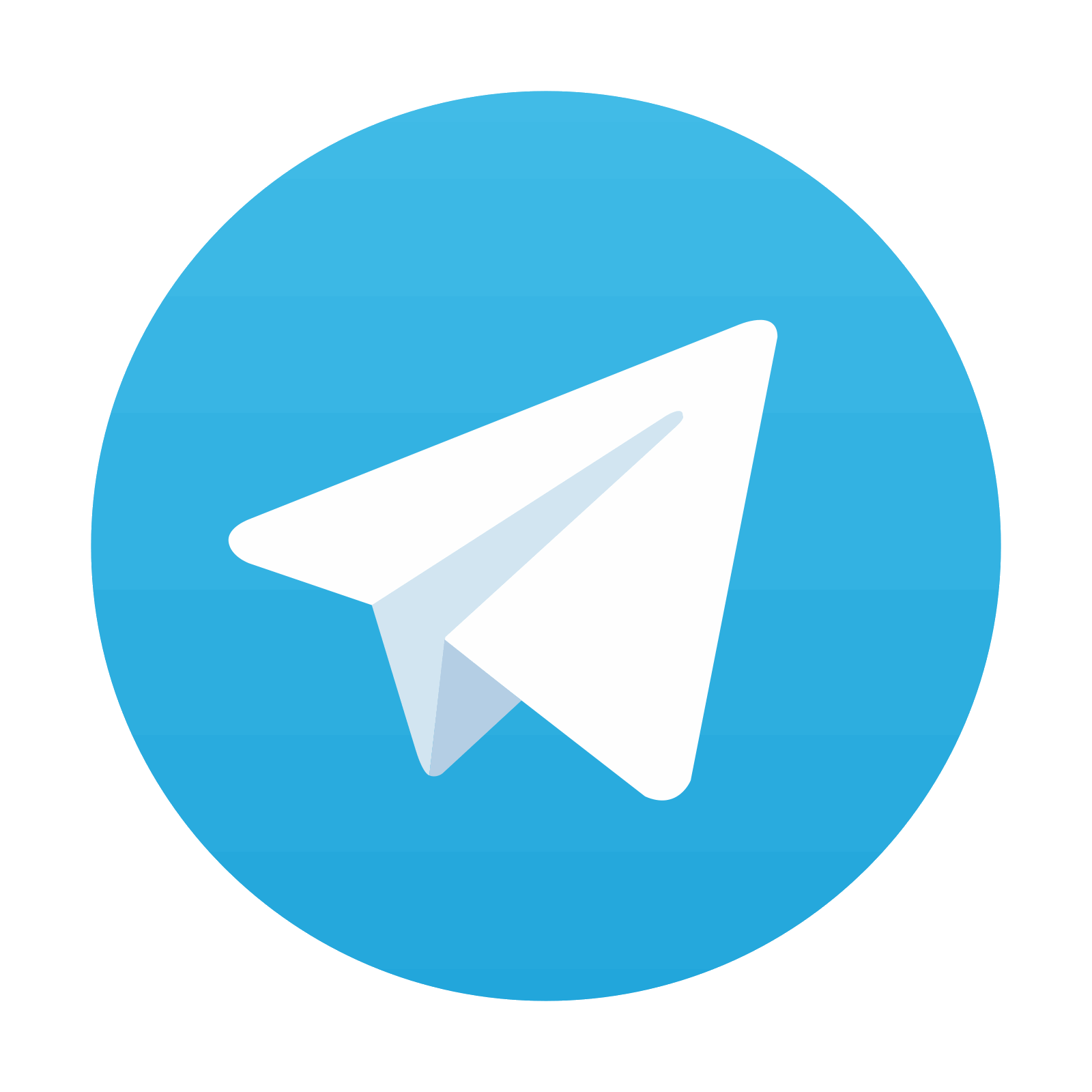
Stay updated, free dental videos. Join our Telegram channel

VIDEdental - Online dental courses
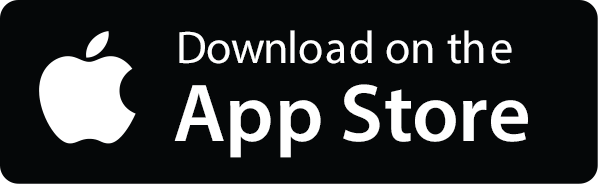

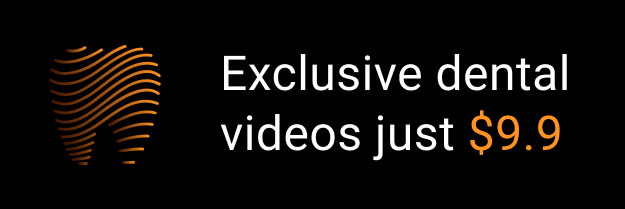