Abstract
Objectives
To produce a new veneering ceramic based on the production of a multiple phase glass–ceramic with improved performance in terms of strength and toughness.
Methods
A composition of 60% leucite, 20% diopside and 20% feldspathic glass was prepared, blended and a heat treatment schedule of 930 °C for 5 min was derived from differential thermal analysis (DTA) of the glasses. X-ray diffraction (XRD) and SEM analysis determined the crystalline phases and microstructure. Chemical solubility, biaxial flexural strength (BFS), fracture toughness, hardness, total transmittance and coefficient of thermal expansion (CTE) were all measured in comparison to a commercial veneering ceramic (VITA VM9). Thermal shock resistance of the leucite–diopside and VITA VM9 veneered onto a commercial high strength zirconia (Vita In-Ceram YZ) was also assessed. Statistical analysis was undertaken using Independent Samples t -test. Weibull analysis was employed to examine the reliability of the strength data.
Results
The mean chemical solubility was 6 μg/cm 2 for both ceramics ( P = 1.00). The mean BFS was 109 ± 8 MPa for leucite–diopside ceramic and 79 ± 11 MPa for VITA VM9 ceramic ( P = 0.01). Similarly, the leucite–diopside ceramic demonstrated a significantly higher fracture toughness and hardness. The average total transmittance was 46.3% for leucite–diopside ceramic and 39.8% for VITA VM9 ( P = 0.01). The leucite–diopside outperformed the VITA VM9 in terms of thermal shock resistance.
Significance This novel veneering ceramic exhibits significant improvements in terms of mechanical properties, yet retains a high translucency and is the most appropriate choice as a veneering ceramic for a zirconia base core material.
1
Introduction
Esthetic veneering ceramics are widely used in dentistry in conjunction with metal, glass–ceramic and high strength ceramic cores. Most commercial dental veneering ceramics are feldspathic glasses, leucite glass–ceramics or fluorapatite glass–ceramics. Many of the high strength ceramic core materials still use feldspathic glass or leucite containing glass as a veneering material to improve esthetic properties and the thermal compatibility, even though these are very weak materials . One of the most common reasons for failure of a veneering ceramic is the presence of cracks or defects within the ceramic. Due to their lack of strength and toughness, fracture or chipping of ceramic veneers readily occurs . With recent developments in high strength core ceramics, veneering ceramics are used even more frequently and the problems of chipping or fracture urgently need to be addressed and resolved.
The failure of veneering ceramics is attributed to a number of different factors. A thermal mismatch between the core and veneering ceramics can cause microcracks at the interface. As the crack propagates through the veneering ceramic, the stress concentration is maintained at the crack tip until the crack moves completely through the veneering ceramic causing failure . High strength ceramic cores must have a thermal match with the veneering ceramics in terms of the coefficient of thermal expansion (CTE) in order to minimize stresses and crack formation within the material .
A common method of veneering high strength core ceramics is by sintering. During the heating and cooling cycles, the ceramics will increase and reduce in length and volume as a function of their thermal expansion characteristics . Therefore, any differences in the CTE between core and ceramic veneer could produce transient or residual stresses. If these stresses are very high, microcracks may be produced that could propagate at a later time inducing failure. Thermal mismatch between core and veneering ceramic materials and/or technical errors in the laboratory can produce thermal shock. Thermal shock is caused by uneven or rapid heating and/or cooling of the fired crown. The exterior surface of the crown may expand or contract more quickly than the interior and, due to differential CTE values, stresses will occur. Also, thermal cracks can develop from the inner surface and break through to the outer surface .
To overcome these aforementioned problems, there is a need for the development of stronger and tougher veneering ceramics. The introduction of a multiple crystalline phase glass–ceramic, by adding a strengthening and toughening second crystallized phase, may result in a significant improvement in the mechanical properties. Diopside, an inosilicate or chain silicate, is a major crystalline phase in some glass–ceramics and is a suitable potential candidate for a second phase glass–ceramic. It is renowned for its high strength and fracture toughness due to its microstructure, a unidirectional backbone of tetrahedral silica linkages which manifests itself as rod-like crystals, providing considerable reinforcement to the glass–ceramic structure . In addition, strong cleavage or twinning provides an energy absorbing mechanism for an advancing crack . Also, diopside demonstrates excellent biocompatibility .
The aim of this research was to produce new glass–ceramic veneering materials based on a combination of feldspar, leucite (KAlSi 2 O 6 ) and diopside (MgCaSi 2 O 6 ) for a zirconia-based core material. It is hypothesized that the introduction of a second phase in addition to the leucite will result in improved performance in terms of strength and fracture toughness. This has to be achieved within the constraints of a matched CTE and appropriate esthetics. This study will assess the mechanical, physical, chemical and optical properties of the new veneering ceramic and its compatibility with a zirconia core material. This is the first time that diopside has been investigated as a possible new veneering ceramic for dental restorations and at present no such available product is commercially available.
2
Materials and methods
2.1
Glass formulation
Three glasses, a leucite, diopside and feldspar, were prepared using reagent grade raw materials and are described in Table 1 . Batches were mixed by using a vacuum mixer (DeguDent, USA) for 10 min.
Diopside glass (wt%) | Leucite glass (wt%) | Feldspathic glass (wt%) | Raw material | Source | Purity (%) | |
---|---|---|---|---|---|---|
K 2 O | 2.4 | 13 | 4 | K 2 CO 3 | Aldrich Chemical | 99+ |
MgO | 11.8 | 1 | 0.5 | MgO | Acros organics | 98 |
SiO 2 | 55.7 | 59 | 73 | SiO 2 | Riedel-deHaen | 99+ |
MgF 2 | 2 | – | – | MgF 2 | Acros organics | 98 |
Al 2 O 3 | 2 | 15 | 8 | Al 2 O 3 | Aldrich Chemical | 99 |
CaO | 16.5 | 2 | 1.5 | CaCO 3 | Acros organics | 98 |
ZrO 2 | 3 | – | – | ZrO 2 | Fisher Scientific | 100 |
Na 2 O | 1.6 | 8 | 5.5 | Na 2 CO 3 | Acros organics | 99.5 |
TiO 2 | 3 | – | – | TiO 2 | Aldrich Chemical | 99 |
B 2 O 3 | 2 | – | 7.5 | H 3 BO 3 | Aldrich Chemical | 99 |
BaO | – | 3 | – | BaCO 3 | Aldrich Chemical | 99.5 |
The diopside composition was preheated in an alumina crucible at 1000 °C overnight and melted at 1350 °C for 2 h in an electric air furnace (Vecstar furnace, UK). The leucite and feldspathic compositions were preheated in an alumina crucible at 1000 °C overnight and melted for the final 2 h at 1550 °C. The heating rate was 10 °C/min. The glass melts were rapidly cooled to form a glass frit and were dried for 1 h at 200 °C, followed by cooling at 5 °C/min to room temperature. The glass frits were ground using a planetary ball milling machine (PM 100, Retsch limited, Germany) with agate jar and balls at a grinding rate of 400 rpm for 10 min and then sieved to powder of particle size <100 μm.
2.2
DTA
Differential thermal analysis (DTA) measurements were performed on the three different glasses using a Diamond TG/DTA thermogravimetric/differential thermal analyser (Perkin Elmer Instruments, USA). Weighed powder samples (0.1 g, n = 5) were placed into platinum sample holders and an alumina standard was used as a reference material. The samples were run from 25 to 1200 °C at a rate of 10 °C/min and similarly cooled at these rates.
2
Materials and methods
2.1
Glass formulation
Three glasses, a leucite, diopside and feldspar, were prepared using reagent grade raw materials and are described in Table 1 . Batches were mixed by using a vacuum mixer (DeguDent, USA) for 10 min.
Diopside glass (wt%) | Leucite glass (wt%) | Feldspathic glass (wt%) | Raw material | Source | Purity (%) | |
---|---|---|---|---|---|---|
K 2 O | 2.4 | 13 | 4 | K 2 CO 3 | Aldrich Chemical | 99+ |
MgO | 11.8 | 1 | 0.5 | MgO | Acros organics | 98 |
SiO 2 | 55.7 | 59 | 73 | SiO 2 | Riedel-deHaen | 99+ |
MgF 2 | 2 | – | – | MgF 2 | Acros organics | 98 |
Al 2 O 3 | 2 | 15 | 8 | Al 2 O 3 | Aldrich Chemical | 99 |
CaO | 16.5 | 2 | 1.5 | CaCO 3 | Acros organics | 98 |
ZrO 2 | 3 | – | – | ZrO 2 | Fisher Scientific | 100 |
Na 2 O | 1.6 | 8 | 5.5 | Na 2 CO 3 | Acros organics | 99.5 |
TiO 2 | 3 | – | – | TiO 2 | Aldrich Chemical | 99 |
B 2 O 3 | 2 | – | 7.5 | H 3 BO 3 | Aldrich Chemical | 99 |
BaO | – | 3 | – | BaCO 3 | Aldrich Chemical | 99.5 |
The diopside composition was preheated in an alumina crucible at 1000 °C overnight and melted at 1350 °C for 2 h in an electric air furnace (Vecstar furnace, UK). The leucite and feldspathic compositions were preheated in an alumina crucible at 1000 °C overnight and melted for the final 2 h at 1550 °C. The heating rate was 10 °C/min. The glass melts were rapidly cooled to form a glass frit and were dried for 1 h at 200 °C, followed by cooling at 5 °C/min to room temperature. The glass frits were ground using a planetary ball milling machine (PM 100, Retsch limited, Germany) with agate jar and balls at a grinding rate of 400 rpm for 10 min and then sieved to powder of particle size <100 μm.
2.2
DTA
Differential thermal analysis (DTA) measurements were performed on the three different glasses using a Diamond TG/DTA thermogravimetric/differential thermal analyser (Perkin Elmer Instruments, USA). Weighed powder samples (0.1 g, n = 5) were placed into platinum sample holders and an alumina standard was used as a reference material. The samples were run from 25 to 1200 °C at a rate of 10 °C/min and similarly cooled at these rates.
3
Blending and heat treatment of the glasses
A composition of 60% leucite, 20% diopside and 20% feldspathic glass was blended using planetary ball milling at a grinding rate of 450 rpm for 5 min and sieved to a particle size of <100 μm. A heat treatment schedule was derived from the DTA data. The blended glass was prepared into pellets, placed on a refractory and fired at 930 °C for 5 min using an IPS vacuum furnace (Programat P 300, Ivoclar Vivadent AG, Liechtenstein) to allow fusion and crystallization.
3.1
XRD
To determine the crystalline phases present after heat treatment, <45 μm sieved glass–ceramic-sintered powdered specimens ( n = 5) were analysed by X-ray diffraction (XRD) using the Philips PW1050 diffractometer (Eindhoven, Netherlands) with Cu Kα radiation ( λ = 1.5406 Å) and an accelerating voltage of 50 kV between 2 θ values of 10–60°, using a step-scanning technique with a fixed step size of 0.02° and a rate of 2°/min. The diffraction patterns were analysed using STOE WinXPOW v1.1 programme (Stoe & Cie GmbH, Darmstadt, Germany) in conjunction with JCPDS.
3.2
SEM
Scanning electron microscopy (Jeol JSM-6400, Tokyo, Japan) was carried out to analyse the microstructure. Samples of 12 mm diameter were prepared by sequential grinding from 120 through 1200 grit SiC grinding papers and then by sequential polishing with 6 and 1 μm diamond paste to an optical finish. The samples were imaged in backscattered electron mode to provide contrast to the different phases.
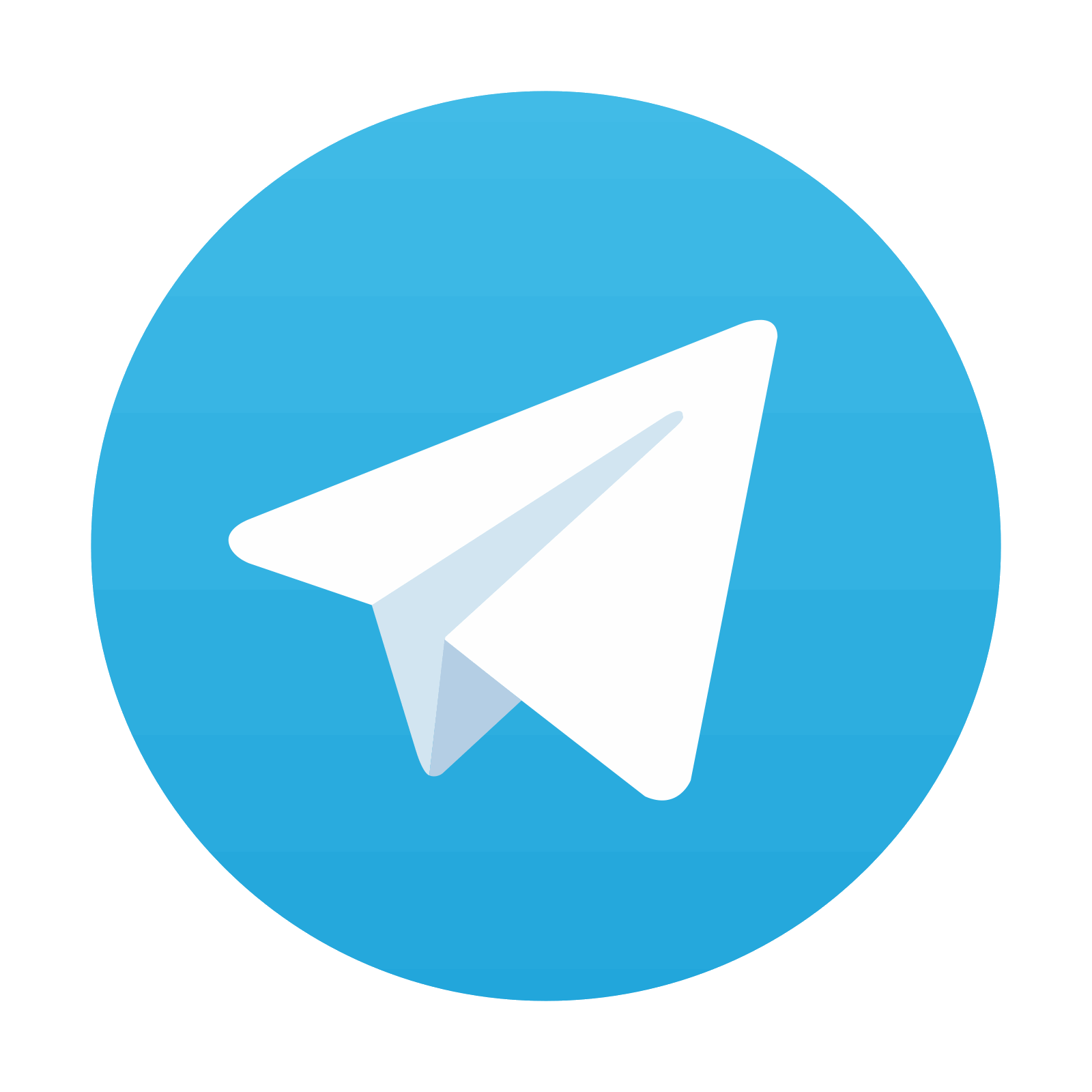
Stay updated, free dental videos. Join our Telegram channel

VIDEdental - Online dental courses
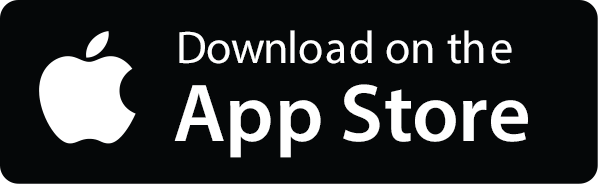
