Abstract
Objectives
To more efficiently determine the subcritical crack growth (SCG) parameters of dental ceramics, the effects of stressing rate and choice of statistical regression model on estimates of SCG parameters were assessed.
Methods
Two dental ceramic materials, a veneering material having a single critical flaw population (S) and a framework material having partially concurrent flaw populations (PC), were analyzed using constant stress-rate testing, or “dynamic fatigue”, with a variety of testing protocols. For each material, 150 rectangular beam specimens were prepared and tested in four-point flexure according to ISO6872 and ASTM1368. A full-factorial study was conducted on the following factors: material, stress rate assumed vs. calculated, number of stress rates, and statistical regression method.
Results
The proportion of specimens for which the statistical models over-estimated reliability was not significantly different based on regression method for Material S ( P = 0.96, power = 94%) and was significantly different based on regression method for Material PC ( P < 0.001). The standard method resulted in SCG parameters, n and ln B , of 35.9 and −11.1 MPa 2 s for Material S and 12.4 and 9.61 MPa 2 s for Material PC, respectively.
Significance
The method of calculation that uses only the median strength value at each stress rate provided the most robust SCG parameter estimates. Using only two stress rates resulted in fatigue parameters comparable to those estimated using four stress rates having the same range. The stress rate of each specimen can be assumed to be the target stress rate with negligible difference in SCG parameter estimates.
1
Introduction
Ceramic components, such as dental prostheses, sometimes exhibit delayed catastrophic failure due to subcritical crack growth (SCG) . This crack growth can occur through simultaneous mechanisms of stress-corrosion and cyclic fatigue . The lifetime of a component can be predicted if the stress distribution for the component and parameters characterizing the rate of SCG are known for each of the component materials in the service environment . The SCG parameters for a given material can be deduced from experiments on standard geometry specimens . When components are subject to a constant stress or are fabricated from materials that do not suffer cyclic fatigue, a static or dynamic fatigue test is sufficient to deduce the SCG parameters .
The term “static fatigue” describes the experiment in which the induced stress is constant over time and the time to failure is the dependent variable . To perform a static fatigue test for a material, measurements of failure time must be taken at several constant stress levels. In the static fatigue testing method, the time to failure for each specimen may take days or sometimes months to measure.
Constant stress-rate testing, also known as “dynamic fatigue”, is a technique to expedite determination of material SCG parameters . Constant stress-rate testing is the situation in which the induced stress is increased over time at a constant rate and the failure stress is the dependent variable. This method requires performing strength tests at several stress rates. For a material having fracture toughness ( K Ic ) and flaw geometry ( Y ) independent of flaw size ( a ), failure stress ( σ f ) decreases with decreasing stress rate, since flaws are given more time to grow before the critical stress intensity factor is reached. According to Eq. (1) , σ f must decrease with increasing a when K Ic and Y are constant .
K I c = Y σ f a
Ritter derived the equation for strength of specimens tested under constant stress rate as :
σ f n + 1 = B ( n + 1 ) S i n − 2 σ ˙
where <SPAN role=presentation tabIndex=0 id=MathJax-Element-3-Frame class=MathJax style="POSITION: relative" data-mathml='σ˙’>σ˙σ˙
σ ˙
is the stress rate, and S i is the inert (moisture free) flexural strength. By performing regression of ln σ f vs. <SPAN role=presentation tabIndex=0 id=MathJax-Element-4-Frame class=MathJax style="POSITION: relative" data-mathml='lnσ˙’>lnσ˙lnσ˙
ln σ ˙
, a linear model of best fit can be constructed and used to estimate the SCG parameters, n and B . These parameters can be used to estimate the lifetime ( t f ) under constant stress ( σ ) to be :
t f = B S i n − 2 σ − n
Eq. (3) shows that high values for both n and B represent greater resistance to stress-corrosion. However, B contains the fracture toughness; hence a high B value also represents greater fracture resistance in general :
B = 2 K I c 2 A Y 2 ( n − 2 )
v = A K I K I c n
where <SPAN role=presentation tabIndex=0 id=MathJax-Element-8-Frame class=MathJax style="POSITION: relative" data-mathml='v’>vv
v
is the velocity of subcritical crack growth, which is a function of the stress intensity factor ( K I ).
The dependence of strength on flaw distribution often leads to large variations in observed lifetime between specimens. This will cause an appreciable scatter in SCG parameter estimates. Since accurate estimates are necessary for accurate prediction of component lifetime, several authors have used Monte Carlo simulation to investigate the effects of the number of test specimens and range of stress rates employed on the accuracy and precision of estimates . Ritter et al. found that the variability in estimating the fatigue parameters increased as the number of groups tested at different stress rates increased . They also reported that if n is determined from strength measurements at two stress rates, then the statistical variability of n is quite sensitive to the stress-rate range, and the variability increased as the range of stress rates decreased . In addition, variability of estimates was dependent on the total number of specimens but not the number of specimens per group. Salem and Weaver calculated the confidence intervals of fatigue parameter estimates using both a closed form solution (propagation of error) and Monte Carlo simulation . They found that regression models using group mean values and median values were both adequate for estimating n , but because of the skewed distribution of B estimates, only median strength values were adequate for use in estimating B . Use of median strength values also provided a more conservative reliability model, since it resulted in lower values for B estimates . McCool found that estimates of B have much greater variability than estimates of n . He also reported that the number of specimens used to measure stress-corrosion has a greater influence on the variability of B estimates than does the number of specimens used to measure inert strength.
The present work is an extension of the investigations by Ritter et al., Salem and Weaver, and McCool. Contrary to the recommendations of Ritter et al., the ASTM1368 standard specifies that at least four stress rates should be used for dynamic fatigue testing . This contradiction invites further investigation. The standard also specifies that, due to variation in specimen dimensions, the actual stress rate should be calculated for each specimen individually. However, some investigators may conserve effort by assuming that all specimens in a group experienced the same stress rate, the target stress rate. This would seem to be a minor assumption, but no data are yet available regarding the effect of this assumption on test results. In addition, there are three different regression methods that are commonly used: a method that uses all failure strength values (ASTM1368), a method that uses only median failure strength values , and a method that uses the ratios of all failure stresses to those of equally ranked specimens from the inert strength group . It is unknown which of the above methods is least sensitive to irregularity in the distribution of strength data. In the present study, physical specimens made from two ceramics that are widely used in dental applications were used to:
- 1.
determine the sensitivity of SCG parameter estimates to the number and range of stress rates;
- 2.
determine whether assuming identical target stress rates for all the specimens in each group affects the accuracy of lifetime prediction; and
- 3.
determine the most robust regression method to calculate SCG parameters.
Previous authors have used indentation-crack method, constant stress-rate testing, and cyclic loading to determine the SCG parameters of a variety of dental ceramics . The ceramic materials used in this study were previously evaluated using fractographic methods to determine their critical flaw populations .
2
Materials and methods
This study was performed on two different dental ceramics that are widely used in fabricating all-ceramic dental fixed prostheses. A feldspathic porcelain (Vitadur Alpha; VITA Zahnfabrik, Bad Säckingen, Germany) was chosen to exemplify materials that are simple to characterize because a single type of critical flaw has been observed for this material (Material S) . An alumina-zirconia-glass composite (In-Ceram ® Zirconia; VITA Zahnfabrik) was chosen to exemplify materials that are difficult to characterize because its strength values were heavily skewed toward the lower end of the distribution, owing to two partially concurrent flaw populations (Material PC) . Three hundred uniaxial flexure specimens (150 of each material) were fabricated to dimensions of 25 mm × 4 mm × 1.2 mm. All specimens were processed and treated according to the manufacturer’s recommendations for fabricating an actual dental prosthesis.
Material S specimens were fabricated by mixing 0.5 g of ceramic powder (VITA Zahnfabrik) and 0.18 g of modeling liquid (VITA Zahnfabrik) to form a slurry. The slurry was poured into custom fabricated steel molds with dimensions of 25.50 mm × 4.75 mm × 2.00 mm. Then, the slurry was condensed in the molds using a mechanical vibrator (No. 1A; Buffalo Dental, Syosset, NY, USA) followed by manual vibration to allow any trapped air to escape from the slurry. A firing cycle was performed using a dental porcelain furnace (Centurion Q200; Ney, Yucaipa, CA, USA) according to the manufacturer’s instructions as follows: the specimens were dried at 600 °C for 6 min, heated to 960 °C at a rate of 60 °C/min under full vacuum, held at 960 °C for 1 min, and subsequently cooled for 1 min before removing the specimens from the furnace. After completing the firing cycle, bench-cooling to room temperature was performed for all specimens. An additional firing cycle was performed as follows: the specimens were dried at 600 °C for 6 min, heated to 950 °C at a rate of 58 °C/min under full vacuum, held at 950 °C for 1 min under 1 atm pressure, and subsequently cooled for 1 min before removing the specimens from the furnace. The second firing was used to simulate the processing step frequently used by dental technicians to make small corrections to the shape of a prosthesis. All specimens were ground to the final desired dimensions of 25 mm × 4 mm × 1.2 mm, and the tensile surfaces were polished using SiC abrasive papers with sequentially finer grit size (8” Plain Back Silicon Carbide Discs; Allied High Tech Products, Rancho Dominguez, CA, USA). The polishing procedure was concluded by using a final grit size of 400, and the last polishing direction was performed along the long axis of the specimen. All the specimens were auto-glazed as follows: each specimen was dried at 600 °C for 4 min, heated to 920 °C at a rate of 107 °C/min, and held for 1 min at 920 °C; this firing cycle was run under atmospheric pressure. Subsequently, all specimens were bench-cooled to room temperature.
A very thin (0.05 mm) adhesive tape (Scotch ® Magic™ Tape; 3 M, St. Paul, MN, USA) was placed on the compressive surface to secure the fractured segments of the specimen during the fracture test. The specimens were assigned randomly into five groups of 30 specimens each. One group of specimens was tested under an inert environment. The other specimens were tested while immersed in distilled water at 37 °C. The inert strength specimens were heated at 140 °C for 14 h to remove any moisture from the specimens, and then they were placed in 140 °C SAE 85W-140 oil (Super Tech; Wal-Mart Stores, Bentonville, AR, USA), and allowed to cool to 37 °C in a desiccator to prevent atmospheric moisture from contacting the specimens. This should have prevented moisture from assisting crack growth during fracture.
Material PC specimens were fabricated to the dimensions of 25 mm × 4 mm × 1.2 mm. This was accomplished by cutting ceramic blocks (Zirconia ZB-80; VITA Zahnfabrik) into the desired shape and dimensions using a low-speed saw with a diamond cutting blade (Isomet; Buehler, Lake Bluff, IL, USA). The ceramic block was mounted on the cutting arm, which was adjusted by an attached micrometer to set the desired cut thickness. Zirconia ZB-80 blocks are porous; to fill the porosity a glass infiltration procedure was performed. This was performed by applying a coating of glass powder-water slurry (In-Ceram ® Zirconia Glass Powder; VITA Zahnfabrik) to the ceramic specimens using a dental ceramic brush. The specimens were placed in a programmable vacuum porcelain furnace (Multimat ® Touch & Press; Dentsply, York, PA, USA) to perform the glass infiltration firing cycle according to the manufacturer’s recommendations as follows: all specimens were dried at 600 °C for 1 min, heated to 1140 °C at a rate of 20 °C/min, and held at 1140 °C for 40 min under full vacuum. After glass infiltration, the excess glass was removed using heatless coarse-grained SiC wheels (Mizzy Heatless ® Wheels; Keystone, Cherry Hill, NJ, USA). Following this step, the Material PC specimens were treated exactly as the Material S specimens, and all the firing steps that were performed on the Material S specimens were also performed on the Material PC specimens, since in the clinical situation a veneer of Material S will be built on top of a core of Material PC, and accordingly, the core material will encounter all the firing cycles that the veneer encounters.
Four-point flexure testing was performed using a servohydraulic mechanical testing machine (Minibionix 858; MTS Systems Corporation, Eden Prairie, MN, USA) with a custom semi-articulating four-point flexure fixture having an outer span of 20 mm and an inner span of 10 mm. The target stress rates were attained using the mechanical testing machine in load-controlled mode. Eq. (6) was used to determine the load rates necessary to reach the target stress rates with an assumed width and thickness.
P ˙ = 4 3 σ ˙ L w t 2
where <SPAN role=presentation tabIndex=0 id=MathJax-Element-10-Frame class=MathJax style="POSITION: relative" data-mathml='P˙’>P˙P˙
P ˙
is the load rate, <SPAN role=presentation tabIndex=0 id=MathJax-Element-11-Frame class=MathJax style="POSITION: relative" data-mathml='σ˙’>σ˙σ˙
σ ˙
is the target stress rate, L is the outer (support) span of the test fixture, <SPAN role=presentation tabIndex=0 id=MathJax-Element-12-Frame class=MathJax style="POSITION: relative" data-mathml='w’>ww
w
is the specimen width, and t is the specimen thickness. Each group of the Material S specimens was fractured using one of the four different target stress rates ranging on a logarithmic scale from 0.1 to 100 MPa/s. The fifth group was tested in inert environment (oil) with a target stress rate of 100 MPa/s. Different target stress rates, which ranged from 0.01 to 10 MPa/s, were used for the Material PC specimens, and a target stress rate of 10 MPa/s was used for the inert strength group. Slower stress rates were used for Material PC because pilot data showed a plateau in strength versus stress rate at faster stress rates. SCG parameters estimated from data on a strength plateau are not valid . The width and thickness of each specimen were measured adjacent to the fracture surface to determine the flexural strength, σ f , of each specimen according to the following equation:
σ f = 3 P L 4 w t 2
where P is the maximum load recorded during testing. The actual stress rate, <SPAN role=presentation tabIndex=0 id=MathJax-Element-14-Frame class=MathJax style="POSITION: relative" data-mathml='σ˙Actual’>σ˙Actualσ˙Actual
σ ˙ A c t u a l
, for each specimen was determined individually using the following equation:
σ ˙ A c t u a l = σ f t f
where t f is the failure time determined from the four-point flexure test for each specimen.
Subsequent data analyses were performed to estimate the fatigue parameters, n and B , at the actual stress rates using three well known methods based on logarithmic transformation followed by linear regression. These methods are as follows: a method that uses all failure stress values as in Eq. (9) ; median method, which uses only the median failure stress value from each group according to Eq. (10) ; and homologous method, which uses the ratio of failure stresses of equally ranked specimens from the water and inert strength groups as in Eq. (11) .
ln ( σ f ) vs. ln ( σ ˙ )
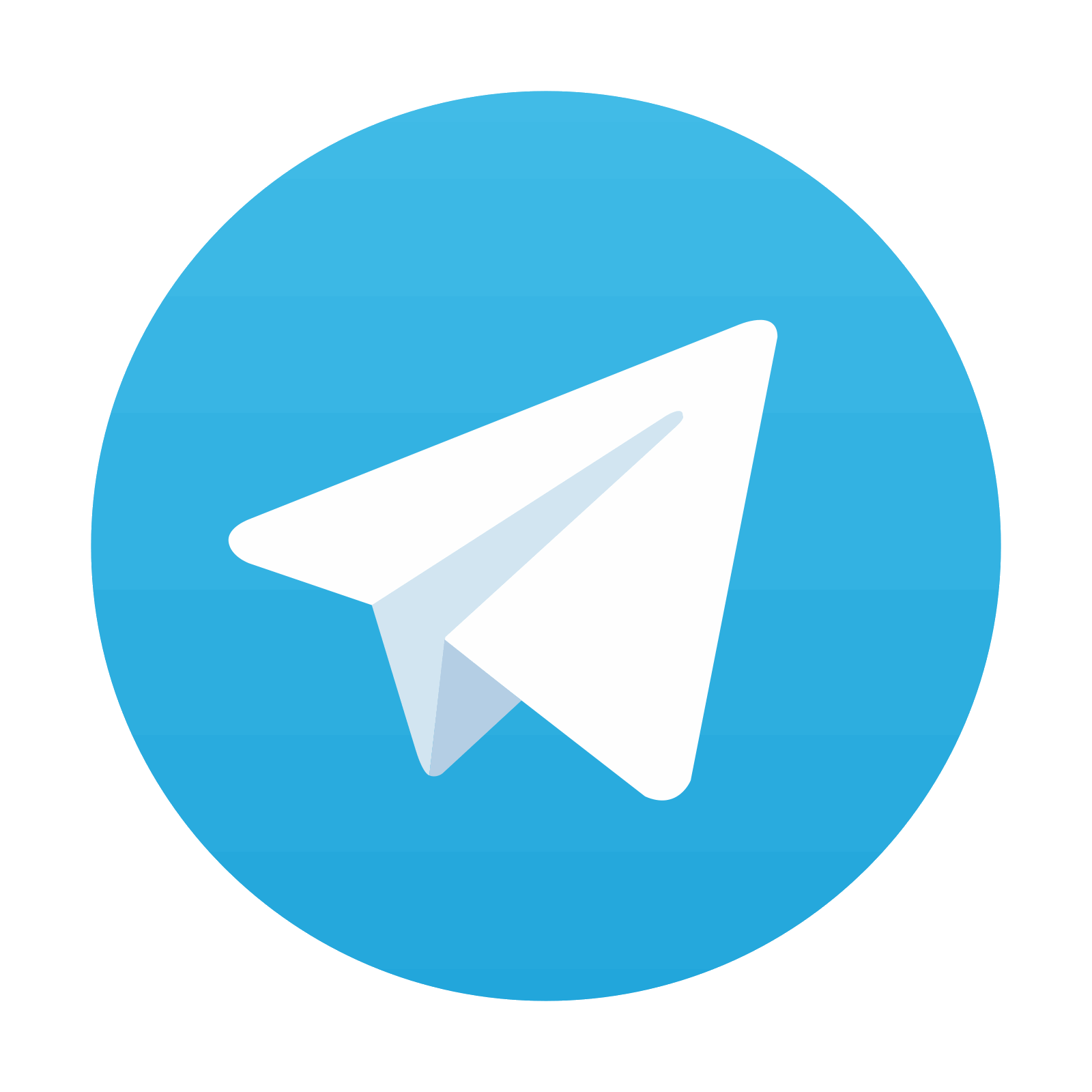
Stay updated, free dental videos. Join our Telegram channel

VIDEdental - Online dental courses
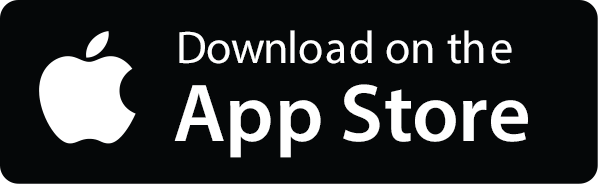
