Abstract
Objectives
The purpose of this study is to elucidate the effects of small-grit grinding on the mechanical behaviors and ageing resistance of a super-translucent dental zirconia and to investigate the necessity of glazing for the small-grit ground zirconia.
Methods
Small-grit grinding was performed using two kinds of silicon carbide abrasive papers. The control group received no grinding. The unground surfaces and the ground surfaces were glazed by an experienced dental technician. Finally, the zirconia materials were thermally aged in water at 134 °C for 5 h. After aforementioned treatments, we observed the surface topography and the microstructures, and measured the extent of monoclinic phase, the nano-hardness and nano-modulus of the possible transformed zone and the flexural strength.
Results
Small-grit grinding changed the surface topography. The zirconia microstructure did not change obviously after surface treatments and thermal ageing; however, the glaze in contact with zirconia showed cracks after thermal ageing. Small-grit grinding did not induce a phase transformation but improved the flexural strength and ageing resistance. Glazing prevented zirconia from thermal ageing but severely diminished the flexural strength. The nano-hardness and nano-modulus of the surface layer were increased by ultrafine grinding.
Conclusions
The results suggest that small-grit grinding is beneficial to the strength and ageing resistance of the super-translucent dental zirconia; however, glazing is not necessary and even impairs the strength for the super-translucent dental zirconia.
Clinical significance
This study is helpful to the researches about dental grinding tools and maybe useful for dentists to choose reasonable zirconia surface treatments.
1
Introduction
Yttria-stabilized tetragonal zirconia polycrystalline (Y-TZP) materials with high strength stand out in dentistry as distinct from various other zirconia materials when applied in fixed partial dentures and even dental implants, although its opaque appearance is not attractive . The high strength of all-ceramic restorations ensures reliable tolerance to masticatory force and lower removal volumes of natural tooth tissues . The chipping and fracture of the veneering porcelain coated on zirconia cores to adjust translucency shows that monolithic restorations made of highly translucent zirconia are a better choice .
The exposed surfaces of monolithic restorations often undergo a series of mechanical processing and adjustments and are then surrounded by oral fluids for decades . The authors of numerous studies have concluded that the mechanical behaviours of Y-TZP are affected by thermal ageing and surface treatments such as grinding and sandblasting because the transformation from the tetragonal phase to the monoclinic phase can be induced by water or stress under certain conditions. The water species penetrated the zirconia lattice and disturbed the charge conservation, as well as the stability of the tetragonal phase, compared to thermal ageing or low-temperature degradation (LTD) . According to some results, grinding with dental diamond burs reduced the LTD susceptibility of zirconia materials in spite of the increased surface roughness and the generated monoclinic zirconia. The surface roughened by grinding did not accelerate the LTD of zirconia; however, at the zone near the ground surface, a compressive stress layer was created along the grain boundary as the grains moderately expanded as a result of phase transformation. This compressive stress layer delayed the penetration of water and the subsequent propagation of microcracks . As consistently reported, the high strength was maintained after grinding and thermal ageing .
However, the effect of surface treatments on the strength of zirconia has not yet been entirely ascribed to the phase transformation . Monoclinic zirconia was truly generated by grinding with diamond burs, but it is doubtful that the mild phase transformation (3.4%-4.2% relative amounts of monoclinic phase) weakened the strength , which apparently differed from the extensive phase transformation caused by thermal ageing, which devastated the structures and impacted the mechanical behaviours of Y-TZP . There was also an evident impairment of strength and a slight phase transformation that simultaneously resulted from the same grinding protocol . The flaws induced by mechanical forces could be responsible for the lowered strength after grinding . Grinding using a large-grit diamond disc produced excessive defects within the materials that aggravated the stress concentration, leading to a characteristic strength loss, whereas strength was promoted by grinding with a small-grit diamond disc. Irrespective of whether a diamond bur or a disc was used for grinding, the use of small-grit grinding tools seemingly prevented the strength degradation . In one study, finer grinding (using a dental diamond bur with a yellow ring, 15–30 μm grit size) caused no strength damage and negligibly small chips ( <2 μm). By contrast, coarser grinding led to decreased strength and a larger chip size, suggesting that the localized defects surpassed the depth of the compressive stress layer when grinding was carried out using large-grit-size tools . Therefore, to limit defects, the use of small-grit grinding tools has been recommended . However, we still know little about how small-grit grinding tools influence the super-translucent (ST) dental zirconia material surface and whether it influences the glaze on the small-grit-ground zirconia surface, which was once performed by some dentists.
The purpose of this study is to elucidate the effects of small-grit grinding on the mechanical behaviors and ageing resistance of the ST dental zirconia and to investigate the necessity of glazing for the small-grit ground zirconia. Therefore, we applied small-grit grinding (fine grinding and ultrafine grinding) and glazing on one type of the ST dental zirconia containing 4.5-5.5 mol% yttria, which is popular in China. Autoclaving in water at 134 °C for 5 h was used to perform the thermal ageing. Finally, the surface topography and microstructure were observed and the monoclinic phase content, nano-hardness, nano-modulus and the flexural strength were tested. Both were used to analyse the effects of small-grit grinding and glazing on the mechanical behaviours and ageing resistance of the materials.
2
Materials and methods
2.1
Specimen preparation
Disc-shaped zirconia specimens (N = 180) were prepared from ST zirconia material (ST, UPCERA, China). Before sintering, ceramic blocks were shaped and ground with 2000 grit silicon carbide papers to eliminate any initial errors. Specimens (20 mm in diameter and 2.5 mm in height) were sintered at 1530 °C for 2 h in a sintering furnace (K8, Vicce, Germany). The final dimensions of the sintered specimens were measured using Vernier callipers. According to the ISO 6872-2015 standard, specimens 12 mm in diameter and 2 mm in height were selected for these experiments.
2.2
Grinding and glazing
Specimens were randomly divided into six groups and treated as specified in Table 1 . Group A and B received no grinding and were treated as the control groups. The fine grinding groups (groups C and D) and the ultrafine grinding groups (groups E and F) were respectively ground using 320 grit and 2000 grit silicon carbide waterproof abrasive papers (SUISUN, Korea) using an electric polisher-grinder machine (PG2, Jinxiang, China) with continuous irrigation. The top and bottom surfaces were ground for 1 min at 200 rpm. To obtain a uniform ground surface, the aforementioned grinding protocol was repeated four times in different directions. After grinding, groups B, D and F were glazed by an experienced dental technician. Glaze paste (IPS.e.max, Ivoclar Vivadent, Liechtenstein) covered the top and bottom surfaces and side surfaces. The firing of glaze on the zirconia surface was performed at 500 °C for 3 min plus 830 °C for 2 min as one cycle using a porcelain stove (A5 plus, Vicce, Germany).
Groups | Codes | Surface treatments |
---|---|---|
Control groups | group A | No treatments. |
group B | Glazed. | |
Fine grinding groups | group C | Ground with 320 grit silicon carbide papers. |
group D | Ground with 320 grit silicon carbide papers and glazed. | |
Ultrafine grinding groups | group E | Ground with 2000 grit silicon carbide papers. |
group F | Ground with 2000 grit silicon carbide papers and glazed. |
2.3
Thermally ageing
To simulate LTD in zirconia, specimens were thermally aged at 134 °C and at a pressure of 2 bar for 5 h using an autoclave (Xiangwei, Weihai, China), consistent with standard ISO1335-2008. The amount of phase-transformed zirconia after above treatment roughly equals to the amount of zirconia implants that has been used for 15 ~ 20 years . Groups without thermal ageing were named A0, B0, C0, D0, E0 and F0, and groups subjected to thermal ageing for 5 h were named A5, B5, C5, D5, E5 and F5.
2.4
Surface topography and roughness
The surface topography of unglazed specimens was characterized by scanning electron microscopy (SEM; Phenom Pro, Phenom World, Netherlands) and laser scanning confocal microscopy (LSCM; TEXT OLS4000, Olympus, Japan), and LSCM provided roughness data for the ground surfaces of each groups.
2.5
Phase analysis
The phase was identified by Cu Kα X-ray diffraction (XRD; Y-2000, Dandong, China). The specimens (n = 2) in each group were analysed from 25 to 35° with a step size of 0.03° and a count time of 1 s at each step. The monoclinic zirconia content was calculated using the equation proposed by Garvie and Nicholson :
where Im (-111) and Im (+111) indicate the integrated intensity of monoclinic peaks, and It (101) indicates the intensity of the tetragonal peak. The XRD profiles were analysed using the HighScore Plus software.
2.6
Microstructures and nanoindentation of surface layers
The specimens were imbedded in resin, and their cross sections were polished. The microstructure of the surface layers was characterized by SEM (Phenom Pro, Phenom World, Netherlands).
To value the hardness and the elastic modulus of the phase-transformed zone, the polished (1 μm finished) cross sections were tested using nano-indentation (Nano Indenter, G200, Agilent, USA). Ten points were equably selected on the cross sections of zirconia samples from 0 to 500 nm under the treated surfaces.
2.7
Biaxial flexure test
According to standard ISO 6872-2008, the biaxial flexure test was performed on specimens (n = 10) from each group using a universal testing machine (WDW3020, Xinke, China). Disc-shaped specimens were placed in the centre of the test mould and supported by three hardened steel balls with a diameter of 4.5 mm, positioned 120° apart on a support circle with a diameter of 10 mm. The glazed surfaces attaching the supported balls were removed and polished. The increasing load (0.52 mm/min) was applied at the centre of the specimen using a flat punch with a diameter of 1.4 mm until the specimen fractured thoroughly. Flexural strength was calculated according to ISO 6872-2008:
where σ, P and b represent the maximum tensile stress (MPa), the total load at fracture (N) and the thickness at the fracture origin (mm), respectively. In addition, v = 0.32 (for zirconia), r 1 is the radius of the support circle (5 mm), r 2 is the radius of the loaded area (0.7 mm), and r 3 is the radius of the specimen (6 mm).
2.8
Fractography examination
Specimen fragments were collected after the biaxial flexure tests. The fracture topography of fragments was examined by SEM (Phenom Pro, Phenom World, Netherlands) to observe and analyse the fracture origins and the crack propagation direction.
2.9
Data analysis
The Weibull statistic was used to analyse flexural strength according to ISO 6872-2015: Annex B. The value of parameter m and the characteristic strength σ c were determined from the plot of ln σ vs. ln[ln(1/(1 – F)]:
ln[ln(1/(1 – F)] = m ln σ c – m ln σ
The characteristic strength σ c refers to a strength at failure probability of approximately 63.2% (i.e. F = 63.2%). The Weibull modulus m is used to measure the distribution of the strength, expressing the reliability of the material.
Data statistics were conducted using IBM SPSS 22.0 software. The homogeneity of variance test (α = 0.10) was performed before other statistical analyses. One-way ANOVA or non-parametric tests (α = 0.05) were respectively applied to compare data with or without homogeneous variances.
2
Materials and methods
2.1
Specimen preparation
Disc-shaped zirconia specimens (N = 180) were prepared from ST zirconia material (ST, UPCERA, China). Before sintering, ceramic blocks were shaped and ground with 2000 grit silicon carbide papers to eliminate any initial errors. Specimens (20 mm in diameter and 2.5 mm in height) were sintered at 1530 °C for 2 h in a sintering furnace (K8, Vicce, Germany). The final dimensions of the sintered specimens were measured using Vernier callipers. According to the ISO 6872-2015 standard, specimens 12 mm in diameter and 2 mm in height were selected for these experiments.
2.2
Grinding and glazing
Specimens were randomly divided into six groups and treated as specified in Table 1 . Group A and B received no grinding and were treated as the control groups. The fine grinding groups (groups C and D) and the ultrafine grinding groups (groups E and F) were respectively ground using 320 grit and 2000 grit silicon carbide waterproof abrasive papers (SUISUN, Korea) using an electric polisher-grinder machine (PG2, Jinxiang, China) with continuous irrigation. The top and bottom surfaces were ground for 1 min at 200 rpm. To obtain a uniform ground surface, the aforementioned grinding protocol was repeated four times in different directions. After grinding, groups B, D and F were glazed by an experienced dental technician. Glaze paste (IPS.e.max, Ivoclar Vivadent, Liechtenstein) covered the top and bottom surfaces and side surfaces. The firing of glaze on the zirconia surface was performed at 500 °C for 3 min plus 830 °C for 2 min as one cycle using a porcelain stove (A5 plus, Vicce, Germany).
Groups | Codes | Surface treatments |
---|---|---|
Control groups | group A | No treatments. |
group B | Glazed. | |
Fine grinding groups | group C | Ground with 320 grit silicon carbide papers. |
group D | Ground with 320 grit silicon carbide papers and glazed. | |
Ultrafine grinding groups | group E | Ground with 2000 grit silicon carbide papers. |
group F | Ground with 2000 grit silicon carbide papers and glazed. |
2.3
Thermally ageing
To simulate LTD in zirconia, specimens were thermally aged at 134 °C and at a pressure of 2 bar for 5 h using an autoclave (Xiangwei, Weihai, China), consistent with standard ISO1335-2008. The amount of phase-transformed zirconia after above treatment roughly equals to the amount of zirconia implants that has been used for 15 ~ 20 years . Groups without thermal ageing were named A0, B0, C0, D0, E0 and F0, and groups subjected to thermal ageing for 5 h were named A5, B5, C5, D5, E5 and F5.
2.4
Surface topography and roughness
The surface topography of unglazed specimens was characterized by scanning electron microscopy (SEM; Phenom Pro, Phenom World, Netherlands) and laser scanning confocal microscopy (LSCM; TEXT OLS4000, Olympus, Japan), and LSCM provided roughness data for the ground surfaces of each groups.
2.5
Phase analysis
The phase was identified by Cu Kα X-ray diffraction (XRD; Y-2000, Dandong, China). The specimens (n = 2) in each group were analysed from 25 to 35° with a step size of 0.03° and a count time of 1 s at each step. The monoclinic zirconia content was calculated using the equation proposed by Garvie and Nicholson :
where Im (-111) and Im (+111) indicate the integrated intensity of monoclinic peaks, and It (101) indicates the intensity of the tetragonal peak. The XRD profiles were analysed using the HighScore Plus software.
2.6
Microstructures and nanoindentation of surface layers
The specimens were imbedded in resin, and their cross sections were polished. The microstructure of the surface layers was characterized by SEM (Phenom Pro, Phenom World, Netherlands).
To value the hardness and the elastic modulus of the phase-transformed zone, the polished (1 μm finished) cross sections were tested using nano-indentation (Nano Indenter, G200, Agilent, USA). Ten points were equably selected on the cross sections of zirconia samples from 0 to 500 nm under the treated surfaces.
2.7
Biaxial flexure test
According to standard ISO 6872-2008, the biaxial flexure test was performed on specimens (n = 10) from each group using a universal testing machine (WDW3020, Xinke, China). Disc-shaped specimens were placed in the centre of the test mould and supported by three hardened steel balls with a diameter of 4.5 mm, positioned 120° apart on a support circle with a diameter of 10 mm. The glazed surfaces attaching the supported balls were removed and polished. The increasing load (0.52 mm/min) was applied at the centre of the specimen using a flat punch with a diameter of 1.4 mm until the specimen fractured thoroughly. Flexural strength was calculated according to ISO 6872-2008:
where σ, P and b represent the maximum tensile stress (MPa), the total load at fracture (N) and the thickness at the fracture origin (mm), respectively. In addition, v = 0.32 (for zirconia), r 1 is the radius of the support circle (5 mm), r 2 is the radius of the loaded area (0.7 mm), and r 3 is the radius of the specimen (6 mm).
2.8
Fractography examination
Specimen fragments were collected after the biaxial flexure tests. The fracture topography of fragments was examined by SEM (Phenom Pro, Phenom World, Netherlands) to observe and analyse the fracture origins and the crack propagation direction.
2.9
Data analysis
The Weibull statistic was used to analyse flexural strength according to ISO 6872-2015: Annex B. The value of parameter m and the characteristic strength σ c were determined from the plot of ln σ vs. ln[ln(1/(1 – F)]:
ln[ln(1/(1 – F)] = m ln σ c – m ln σ
The characteristic strength σ c refers to a strength at failure probability of approximately 63.2% (i.e. F = 63.2%). The Weibull modulus m is used to measure the distribution of the strength, expressing the reliability of the material.
Data statistics were conducted using IBM SPSS 22.0 software. The homogeneity of variance test (α = 0.10) was performed before other statistical analyses. One-way ANOVA or non-parametric tests (α = 0.05) were respectively applied to compare data with or without homogeneous variances.
3
Results
3.1
Surface topography and roughness
SEM photos ( Fig. 1 ) show that fine grinding and ultrafine grinding eliminated the initial scratches caused before sintering and flattened the surfaces, but new scratches were created; the scratches on the ultrafine-ground surfaces (groups E0 and E5) were shallower than the fine-ground surfaces (groups C0 and C5). In addition, the fine-ground surfaces display more consistent scratches in one direction compared to the ultrafine-ground surfaces. Ageing did not obviously change the surface topography.
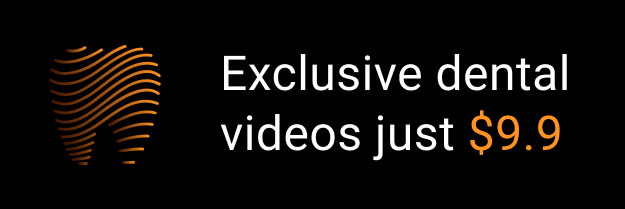