Abstract
Objectives
The effect of visible light passing through a resin composite with different particle sizes of spherical silica filler on the curing depth and Knoop hardness of the resin composite was examined. The null hypotheses tested were that the particle size of silica filler has no effect on (1) the transmitted amount of visible light passing through the resin composite, (2) the curing depth of the resin composite, and (3) the ratio of the Knoop hardness of the hardened resin composite.
Methods
A series of different experimental resin composite pastes with different particle sizes of silica filler were prepared. The amount of visible light passing through each of the experimental resin pastes during the hardening process was determined. The curing depth and Knoop hardness of the resin composites were measured. Further, to characterize the polymerization conversion, the ratio of the Knoop hardness of the bottom surface against the irradiated surface of the hardened resin composites was determined.
Results
Increases in the particle size of the silica filler resulted in decreases in the transmitted amount of visible light, curing depth, and ratio of the Knoop hardness of the resin composite. The rate of polymerization conversion of the resin composite occurring deep within the cavity was found to be less than the rate of polymerization conversion occurring at the upper surface.
Significance
To increase the rate of polymerization conversion deep within the resin composite, it is important to reduce the particle size of the silica filler.
1
Introduction
Photo-cured resin composites have been used widely for restoration of teeth because they are easy to handle and have improved esthetics and enhanced mechanical properties relative to chemical-cured composites. However, major clinical problems caused by photo-cured resin composites are related to the limited curing depth and the lower rate of polymerization conversion deep within the resin composite . This decrease in the polymerization conversion of the resin composite occurs because the photo-energy of visible light passing through the resin composite does not penetrate the resin composite sufficiently to reach the cavity floor and to activate the photo-initiator, such as Camphorquinone, CQ . This is because scattering of visible light occurs at the resin-silica interface . Previously, we examined the effects of different types of base monomers on the amount of transmitted visible light passing through the resin composite, the curing depth, and the rate of polymerization conversion . The transmitted amount of visible light was found to be strongly dependent on the magnitude of the difference between the refractive indices existing between the base resin and the silica . Specifically, this difference was found to depend upon the type of monomer used . The amount of transmitted light exhibited a strong correlation with the curing depth of the resin composite and the ratio of the Knoop hardness of the bottom surface vs. the irradiated surface of the hardened resin composite.
In this study, the effect of the particle size of the spherical silica filler on the amount of transmitted visible light passing through resin composite during the light-irradiation period was examined. The effect of the amount of transmitted visible light on the depth of curing of the resin composite and the ratio of the Knoop hardness of the bottom surface vs. the irradiated surface of the hardened resin composite are described. The null hypotheses tested were that the particle size of silica filler has no effect on (1) the amount of transmitted visible light passing through the resin composite, (2) the curing depth of the resin composite, and (3) the ratio of the Knoop hardness of the hardened resin composite.
2
Materials and methods
2.1
Materials
The mixed monomer, consisting of triethyleneglycol dimethacrylate (TEGDMA; Shin-Nakamura Chemical Co. Ltd., Nagoya, Japan) and dimethacryloyloxy ethyl 2,2,4-(or 2,4,4) trimethylhexamethylene diurethane (UDMA; Negami Chemical Industrial Co. Ltd., Ishikawa, Japan), was prepared as a base monomer for the resin composite. The molar ratio of the mixed monomer was 1/1. CQ (Aldrich Chemical Co. Inc., USA) was then dissolved into the base monomer to produce a 1% (m/m) solution.
Two equivalents of 2-dimethylaminoethyl methacrylate (Wako Pure Chemical Industry Ltd., Tokyo, Japan) (with respect to CQ) were added to this base monomer as an accelerator.
Four types of spherical silica with different particle sizes, i.e., 0.05 μm (OX 50, Nihon Aerosil, Tokyo, Japan), 0.4 μm, 0.9 μm, and 2.0 μm (Tokuyama, Tokyo, Japan) were used as fillers ( Fig. 1 ). The silica surface was treated with γ-methacryloxypropyltrimethoxysilane (Shin-Etsu Chemical Co., Tokyo, Japan). The silane weight percentages for surface treatment of the silica were 6.0% for 0.05 μm, 2.4% for 0.4 μm, and 1.0% for 0.9 μm and 2.0 μm.
The silane-treated silica was mixed with the base monomer, and resin composite pastes were prepared. The weight ratio of silica to monomer was 1:1.
2.2
Methods
2.2.1
Determination of the refractive index of the mixed monomer and its polymer
The refractive indices of the mixed monomer, consisting of UDMA and TEGDMA, and its polymer were measured at 25 °C using an Abbe refractometer (Erma Optical Works, Tokyo, Japan). The polymer was obtained from bulk polymerization at 130 °C for 15 min by addition of a mass of benzoyl peroxide equivalent to 0.5% of the mass of the mixed monomer.
Monobromonaphthalene was used to precisely fit the polymer to the refractometer.
2.2.2
Determination of the refractive index of the spherical silica filler with different particle sizes
The non-treated silica particles were dispersed into mixed solvents whose refractive indices had been previously determined. The suspension was then kept in a stationary state for 10 min. The transmittance of visible light passing through the suspension was observed at 468 nm using a spectrophotometer (U best-30; JASCO, Tokyo, Japan) at 25 °C. This observation was possible because CQ was in an excited state as a result of the absorption of visible light at 468 nm . The refractive index of the silica was determined based on the refractive index of the solvent whose suspension provided the maximum value of the transmittance.
2.2.3
Amounts of transmitted visible light passing through the resin composite
The resin composite paste was injected into a brass mold with a 5.0 mm inner diameter and a depth of 2.0 mm. Both of the resin surfaces were covered with transparent plastic matrix strips. The transmittance of visible light passing through the resin composite was measured during a light-irradiation period that ranged from 0 to 60 s by using an experimental apparatus ( Fig. 2 ). This experimental apparatus was equipped with a light sensor for detection of visible light passing through the resin composite . The Cure Master (3M, USA) was used for light-irradiation. The distance between the exit window of the external light source and the top surface of the resin composite was 3.0 mm. The transmittance via this axis, where visible light was irradiated in the absence of the resin composite, was adjusted to represent 100% transmittance. The observed transmittance of visible light passing through the resin composite was therefore represented by the ratio of the transmittance of visible light through the sample to the transmittance of visible light in the absence of the sample. The transmittance observation was performed in triplicate for each experimental resin composite.
The area where visible light passes through the resin composite was determined by calculating the area under the obtained transmittance curve during the light-irradiation period. The amount of transmitted visible light passing through the resin composite was determined by dividing the calculated area by the area under the transmittance curve obtained in the absence of the sample.
2.2.4
Curing depth of the resin composite
The resin composite paste was injected into a brass mold with a 5.0 mm inner diameter and a depth of 30 mm. After the resin surfaces were covered with transparent plastic matrix strips, visible light was irradiated on the resin composite paste for 60 s using the Cure Master. The distance between the light source and the resin surface was 3.0 mm. After being ejected from the brass mold, the irradiated sample was rinsed with ethanol to remove the uncured resin layer. The curing depth of the resin composite was then measured. Five specimens were used for each experiment.
2.2.5
The Knoop hardness of the resin composite
The resin composite paste was injected into the brass mold, which had an inner diameter of 5.0 mm and a thickness of 2.0 mm. Visible light was irradiated for 60 s. The distance between the light source and the resin surface was 3.0 mm. During light irradiation, all specimens were fully covered with transparent plastic matrix strips. The Knoop hardness of the irradiated side and the bottom side of the hardened resin composite were then measured with a Hardness Tester (HMV-2000; Shimadzu, Kyoto, Japan) equipped with a Knoop diamond. The hardness of each specimen was measured four times with a 10-g load for 30 s. The ratio of the Knoop hardness of the bottom surface against that of the irradiated surface of the hardened resin composite was derived by dividing the Knoop hardness of the bottom surface by the Knoop hardness of the irradiated surface. Five specimens were used in each experiment.
2.3
Statistical analyses
For each experimental group, the mean value and standard deviation (SD) for the amount of transmitted visible light, curing depth, and ratio of the Knoop hardness were calculated for each resin composite. The results were analyzed by one-way analysis of variances (ANOVA), as well as by a post hoc Fisher protected LSD test. The statistical significance value was set at 0.01.
2
Materials and methods
2.1
Materials
The mixed monomer, consisting of triethyleneglycol dimethacrylate (TEGDMA; Shin-Nakamura Chemical Co. Ltd., Nagoya, Japan) and dimethacryloyloxy ethyl 2,2,4-(or 2,4,4) trimethylhexamethylene diurethane (UDMA; Negami Chemical Industrial Co. Ltd., Ishikawa, Japan), was prepared as a base monomer for the resin composite. The molar ratio of the mixed monomer was 1/1. CQ (Aldrich Chemical Co. Inc., USA) was then dissolved into the base monomer to produce a 1% (m/m) solution.
Two equivalents of 2-dimethylaminoethyl methacrylate (Wako Pure Chemical Industry Ltd., Tokyo, Japan) (with respect to CQ) were added to this base monomer as an accelerator.
Four types of spherical silica with different particle sizes, i.e., 0.05 μm (OX 50, Nihon Aerosil, Tokyo, Japan), 0.4 μm, 0.9 μm, and 2.0 μm (Tokuyama, Tokyo, Japan) were used as fillers ( Fig. 1 ). The silica surface was treated with γ-methacryloxypropyltrimethoxysilane (Shin-Etsu Chemical Co., Tokyo, Japan). The silane weight percentages for surface treatment of the silica were 6.0% for 0.05 μm, 2.4% for 0.4 μm, and 1.0% for 0.9 μm and 2.0 μm.
The silane-treated silica was mixed with the base monomer, and resin composite pastes were prepared. The weight ratio of silica to monomer was 1:1.
2.2
Methods
2.2.1
Determination of the refractive index of the mixed monomer and its polymer
The refractive indices of the mixed monomer, consisting of UDMA and TEGDMA, and its polymer were measured at 25 °C using an Abbe refractometer (Erma Optical Works, Tokyo, Japan). The polymer was obtained from bulk polymerization at 130 °C for 15 min by addition of a mass of benzoyl peroxide equivalent to 0.5% of the mass of the mixed monomer.
Monobromonaphthalene was used to precisely fit the polymer to the refractometer.
2.2.2
Determination of the refractive index of the spherical silica filler with different particle sizes
The non-treated silica particles were dispersed into mixed solvents whose refractive indices had been previously determined. The suspension was then kept in a stationary state for 10 min. The transmittance of visible light passing through the suspension was observed at 468 nm using a spectrophotometer (U best-30; JASCO, Tokyo, Japan) at 25 °C. This observation was possible because CQ was in an excited state as a result of the absorption of visible light at 468 nm . The refractive index of the silica was determined based on the refractive index of the solvent whose suspension provided the maximum value of the transmittance.
2.2.3
Amounts of transmitted visible light passing through the resin composite
The resin composite paste was injected into a brass mold with a 5.0 mm inner diameter and a depth of 2.0 mm. Both of the resin surfaces were covered with transparent plastic matrix strips. The transmittance of visible light passing through the resin composite was measured during a light-irradiation period that ranged from 0 to 60 s by using an experimental apparatus ( Fig. 2 ). This experimental apparatus was equipped with a light sensor for detection of visible light passing through the resin composite . The Cure Master (3M, USA) was used for light-irradiation. The distance between the exit window of the external light source and the top surface of the resin composite was 3.0 mm. The transmittance via this axis, where visible light was irradiated in the absence of the resin composite, was adjusted to represent 100% transmittance. The observed transmittance of visible light passing through the resin composite was therefore represented by the ratio of the transmittance of visible light through the sample to the transmittance of visible light in the absence of the sample. The transmittance observation was performed in triplicate for each experimental resin composite.
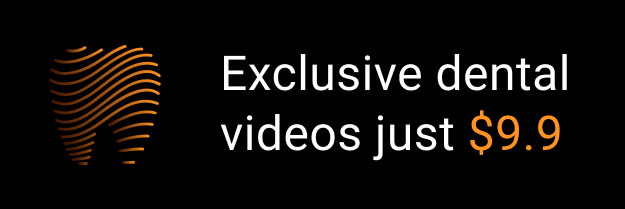