Abstract
Objectives
The objective of this study was to evaluate the effect of immersion time of restorative glass ionomer cements (GICs) and immersion duration in calcium chloride (CaCl 2 ) solution on the surface hardness.
Methods
Two high-viscosity GICs, Fuji IX GP and GlasIonomer FX-II, were selected. Forty-eight specimens were randomly divided into two groups. Sixty minutes after being mixed, half of them were immersed in a 42.7 wt% CaCl 2 solution for 10, 30, or 60 min (Group 1); the remaining specimens were immersed after an additional 1-week of storage (Group 2). The surface hardness of the specimens was measured and analyzed with two-way ANOVA and the Tukey HSD test ( α = 0.05). The surface compositions were examined using energy-dispersive X-ray spectroscopy and X-ray photoelectron spectroscopy.
Results
The surface hardness of Group 1 significantly increased as the immersion duration in CaCl 2 increased; that of Group 2 significantly increased only after 60-minute CaCl 2 immersion. After CaCl 2 immersion, the amounts of Ca increased as the immersion duration increased. The surface hardness after CaCl 2 immersion significantly correlated with the amount of Ca in Group 1, but not in Group 2. The binding energy of the Ca2p peak was similar to that of calcium polyalkenoate. These findings indicated that the Ca ions from the CaCl 2 solution created chemical bonds with the carboxylic acid groups in the cement matrix.
Significance
Immersion of GICs in CaCl 2 solution at the early stage of setting was considered to enhance the formation of the polyacid salt matrix; as a result, the surface hardness increased.
1
Introduction
Glass ionomer cements (GICs) are widely used as a dental restorative material due to their fluoride release and chemical adhesion to tooth structure without pretreatment. However, the mechanical properties of conventional GICs are insufficient for occlusal restoration . Recently, high-viscosity GICs have been developed with improved mechanical properties due to an increase in the powder/liquid ratio and the modified particle size distribution of the glass powder . Because high-viscosity GICs have greater compressive strength, surface hardness, and wear resistance compared to conventional GICs and some resin-modified GICs , high-viscosity GICs are the material of choice for the Atraumatic Restorative Treatment (ART) technique .
The setting of the GICs is caused by cross-linking of the carboxylic acid groups in the aqueous solution of polyacrylic acids with Al and Ca ions released from fluoroaluminosilicate glass powder . When the aqueous solution and the glass powder are combined, the hydrogen ions of the polyacid attack the glass particles, and then Al and Ca ions are released from the glass. These metal ions combine with the carboxylic acid groups of the polyacid to form the polyacid salts matrix, and glass surface is changed to a silica hydrogel. The initial increase in the mechanical strength of GICs is mainly caused by polycarboxylate gel formation . The mechanical properties of GICs have been reported to increase with storage time due to the continuing maturation of the acid–base reaction . However, the increase of mechanical properties of GICs occurs more slowly than do those of resin-modified GICs and composite resins . The mechanical properties of high-viscosity GICs are still insufficient at an early stage of the setting.
There are several reports describing efforts to overcome this drawback, such as using ultrasonic excitation to accelerate the initial setting reaction and the application of a surface coating with light-cured resin to protect the surface from ambient moisture during setting . The surface of the cement is directly affected by environmental conditions; therefore, the enhancement of the GIC surface at early setting stages is considered to be valuable for the stability of the GICs’ mechanical properties.
Immersion in a higher concentration of calcium chloride (CaCl 2 ) solution for 1 day and 1 week was reported to cause a greater increase in the surface hardness of high-viscosity GICs . After immersion in the CaCl 2 solution, Ca was detected in the cement matrix, suggesting that the Ca ions of the CaCl 2 solution reacted with the unreacted carboxylic acid groups remaining in the cement matrix. These reactions enhanced the reaction by forming a polyacid salts matrix. Immersing GICs in CaCl 2 solution is quite simple, and it is not necessary to change the GIC compositions and restoration procedure. If short-term immersion of GICs in CaCl 2 solution can improve their surface hardness at an early stage of setting, this method is practical in the clinical situation. However, the adequate setting stage and duration of CaCl 2 solution immersion to obtain an effective increase in the surface hardness have not been clearly elucidated.
The objective of the present study was to evaluate the effect of immersion time of restorative GICs and immersion duration in CaCl 2 solution on the surface hardness by measuring the Vickers hardness and analyzing the surface composition. The null hypothesis was that the immersion time of GICs and immersion duration in CaCl 2 solution had no influence on the surface hardness of GICs.
2
Materials and methods
2.1
Materials and storage medium
The two high-viscosity GICs evaluated in the present study are listed in Table 1 . These GICs were mixed according to each manufacturer’s instructions at 23 ± 2 °C. Calcium chloride (CaCl 2 ; Calcium Chloride, Anhydrous, JIS Special Grade, Wako Pure Chemical Industries, Osaka, Japan) was dissolved in deionized water to make a saturated concentration of 42.7 wt% Ca at 20 °C. This solution was used as the immersion media for the following experiments.
Material | Code | Manufacturer | P/L | Shade | Components | Lot No. |
---|---|---|---|---|---|---|
Fuji IX GP | FIX | GC Corp. (Tokyo, Japan) | 3.6 | A3 | P: fluoroaluminosilicate glass, polyacrylic acid L: polyacrylic acid, distilled water, polybasic carboxylic acid |
P: 1108171 L: 1108171 |
GlasIonomer FX-II | GFX | Shofu Inc. (Kyoto, Japan) | 2.6 | A2 | P: fluoroaluminosilicate glass, pigments, fluorescent material L: acrylic acid-tricarboxylic acid co-polymer, tartaric acid, distilled water |
P: 061049 L: 061034 |
2.2
Surface hardness measurement
Freshly mixed cement was placed in an acrylic cavity mold (5 mm inner diameter; 2 mm high), then slightly overfilled and compressed with a polyethylene sheet and a metal plate. The mold was stored in a 37.0 °C incubator (NIB-10, AGC Techno Glass Co., Ltd., Shizuoka, Japan) for 1 h before removal of the polyethylene sheet from the specimen surface. The forty-eight specimens were randomly divided into two groups. Half of the specimens were not stored in water (Group 1), and the remainder was used after an additional 1-week of storage in deionized water (Group 2).
The surface hardness of each specimen was measured using a micro-hardness testing machine (MVK-H2, Akashi, Kawasaki, Japan) and a Vickers indenter with a load of 50 gf and a dwell time of 15 s. The Vickers hardness of each specimen before immersion in CaCl 2 solution was determined using the average of five indentations at least 1 mm apart; these values were registered as references. Six specimens of each group were immersed in 10-mL CaCl 2 solution for 10, 30, or 60 min or in 10-mL deionized water for 60 min in a plastic container in the 37.0 °C incubator. The Vickers hardness of each specimen was then determined.
2.3
Energy-dispersive X-ray spectroscopy
Twenty-seven specimens of each GIC were prepared and stored using the above-mentioned method. Three specimens of each group were immersed in 10-mL CaCl 2 solution for 10, 30, or 60 min or in 10-mL deionized water for 60 min in a plastic container in the 37.0 °C incubator. Three specimens that were not immersed in either CaCl 2 solution or water were used as references. Subsequently, the specimens in the mold were kept in a desiccator containing silica gel for at least 1 day. The specimens were removed from the mold and mounted on aluminum stubs, then coated with carbon.
The elemental composition of the specimen surface was analyzed using a scanning electron microscope (SEM; S-4500, Hitachi High-Technologies Corp., Tokyo, Japan) and an energy-dispersive X-ray spectroscope (EDS; EMAX-7000, Horiba, Kyoto, Japan). EDS analysis was performed on each specimen at three randomly selected areas using the acceleration voltage of 15 kV for 100 s.
2.4
Fourier transform infrared (FTIR) spectroscopy
Freshly mixed cement was placed in an acrylic mold (3 mm inner diameter; 0.5 mm thick), then slightly overfilled and compressed with polyethylene sheets and glass plates. The molds were stored in a 37.0 °C incubator for 1 h, and then the specimens were removed from the mold and immersed in 10-mL CaCl 2 solution or deionized water for 60 min. The surfaces of the specimens were observed using a FTIR spectrometer (FTIR-8300, Shimadzu, Kyoto, Japan) equipped with an attenuated total reflectance accessory (DuraSampIIR, ASI Technologies, Danbury, CT, USA). A total of 64 scans ranging from 4000 to 600 cm −1 were recorded with a resolution of 4 cm −1 . A non-immersed specimen and liquid of each GIC were observed as references.
2.5
X-ray photoelectron spectroscopy
Freshly mixed cement was placed in an acrylic mold (2 mm inner diameter; 0.5 mm thick), then slightly overfilled and compressed with polyethylene sheets and glass plates. The molds were stored in a 37.0 °C incubator for 1 h, and then the specimens were removed from the mold and immersed in 10-mL CaCl 2 solution for 10, 30, or 60 min. The chemical structures of the specimen mount on a measuring holder were observed using an X-ray photoelectron spectrometer (JPC-9010MC, JEOL Ltd., Tokyo, Japan). X-ray photoelectron spectroscopy (XPS) analysis was performed under a base pressure of less than 10 −7 Pa. The Al-Kα X-ray was obtained using a 10-kV accelerating voltage and 10-mA filament current. A non-immersed specimen of each GIC and powder of CaCl 2 were observed as a reference.
2.6
Statistical analysis
The surface hardness values after immersion were analyzed by one-way analysis of variance (ANOVA) to assess the effect of the immersion condition. The Tukey HSD test was used to compare the individual data. The relationship between the Ca amount on the specimen surface and the surface hardness was evaluated using linear regression analysis. The level of significance was set at α = 0.05.
2
Materials and methods
2.1
Materials and storage medium
The two high-viscosity GICs evaluated in the present study are listed in Table 1 . These GICs were mixed according to each manufacturer’s instructions at 23 ± 2 °C. Calcium chloride (CaCl 2 ; Calcium Chloride, Anhydrous, JIS Special Grade, Wako Pure Chemical Industries, Osaka, Japan) was dissolved in deionized water to make a saturated concentration of 42.7 wt% Ca at 20 °C. This solution was used as the immersion media for the following experiments.
Material | Code | Manufacturer | P/L | Shade | Components | Lot No. |
---|---|---|---|---|---|---|
Fuji IX GP | FIX | GC Corp. (Tokyo, Japan) | 3.6 | A3 | P: fluoroaluminosilicate glass, polyacrylic acid L: polyacrylic acid, distilled water, polybasic carboxylic acid |
P: 1108171 L: 1108171 |
GlasIonomer FX-II | GFX | Shofu Inc. (Kyoto, Japan) | 2.6 | A2 | P: fluoroaluminosilicate glass, pigments, fluorescent material L: acrylic acid-tricarboxylic acid co-polymer, tartaric acid, distilled water |
P: 061049 L: 061034 |
2.2
Surface hardness measurement
Freshly mixed cement was placed in an acrylic cavity mold (5 mm inner diameter; 2 mm high), then slightly overfilled and compressed with a polyethylene sheet and a metal plate. The mold was stored in a 37.0 °C incubator (NIB-10, AGC Techno Glass Co., Ltd., Shizuoka, Japan) for 1 h before removal of the polyethylene sheet from the specimen surface. The forty-eight specimens were randomly divided into two groups. Half of the specimens were not stored in water (Group 1), and the remainder was used after an additional 1-week of storage in deionized water (Group 2).
The surface hardness of each specimen was measured using a micro-hardness testing machine (MVK-H2, Akashi, Kawasaki, Japan) and a Vickers indenter with a load of 50 gf and a dwell time of 15 s. The Vickers hardness of each specimen before immersion in CaCl 2 solution was determined using the average of five indentations at least 1 mm apart; these values were registered as references. Six specimens of each group were immersed in 10-mL CaCl 2 solution for 10, 30, or 60 min or in 10-mL deionized water for 60 min in a plastic container in the 37.0 °C incubator. The Vickers hardness of each specimen was then determined.
2.3
Energy-dispersive X-ray spectroscopy
Twenty-seven specimens of each GIC were prepared and stored using the above-mentioned method. Three specimens of each group were immersed in 10-mL CaCl 2 solution for 10, 30, or 60 min or in 10-mL deionized water for 60 min in a plastic container in the 37.0 °C incubator. Three specimens that were not immersed in either CaCl 2 solution or water were used as references. Subsequently, the specimens in the mold were kept in a desiccator containing silica gel for at least 1 day. The specimens were removed from the mold and mounted on aluminum stubs, then coated with carbon.
The elemental composition of the specimen surface was analyzed using a scanning electron microscope (SEM; S-4500, Hitachi High-Technologies Corp., Tokyo, Japan) and an energy-dispersive X-ray spectroscope (EDS; EMAX-7000, Horiba, Kyoto, Japan). EDS analysis was performed on each specimen at three randomly selected areas using the acceleration voltage of 15 kV for 100 s.
2.4
Fourier transform infrared (FTIR) spectroscopy
Freshly mixed cement was placed in an acrylic mold (3 mm inner diameter; 0.5 mm thick), then slightly overfilled and compressed with polyethylene sheets and glass plates. The molds were stored in a 37.0 °C incubator for 1 h, and then the specimens were removed from the mold and immersed in 10-mL CaCl 2 solution or deionized water for 60 min. The surfaces of the specimens were observed using a FTIR spectrometer (FTIR-8300, Shimadzu, Kyoto, Japan) equipped with an attenuated total reflectance accessory (DuraSampIIR, ASI Technologies, Danbury, CT, USA). A total of 64 scans ranging from 4000 to 600 cm −1 were recorded with a resolution of 4 cm −1 . A non-immersed specimen and liquid of each GIC were observed as references.
2.5
X-ray photoelectron spectroscopy
Freshly mixed cement was placed in an acrylic mold (2 mm inner diameter; 0.5 mm thick), then slightly overfilled and compressed with polyethylene sheets and glass plates. The molds were stored in a 37.0 °C incubator for 1 h, and then the specimens were removed from the mold and immersed in 10-mL CaCl 2 solution for 10, 30, or 60 min. The chemical structures of the specimen mount on a measuring holder were observed using an X-ray photoelectron spectrometer (JPC-9010MC, JEOL Ltd., Tokyo, Japan). X-ray photoelectron spectroscopy (XPS) analysis was performed under a base pressure of less than 10 −7 Pa. The Al-Kα X-ray was obtained using a 10-kV accelerating voltage and 10-mA filament current. A non-immersed specimen of each GIC and powder of CaCl 2 were observed as a reference.
2.6
Statistical analysis
The surface hardness values after immersion were analyzed by one-way analysis of variance (ANOVA) to assess the effect of the immersion condition. The Tukey HSD test was used to compare the individual data. The relationship between the Ca amount on the specimen surface and the surface hardness was evaluated using linear regression analysis. The level of significance was set at α = 0.05.
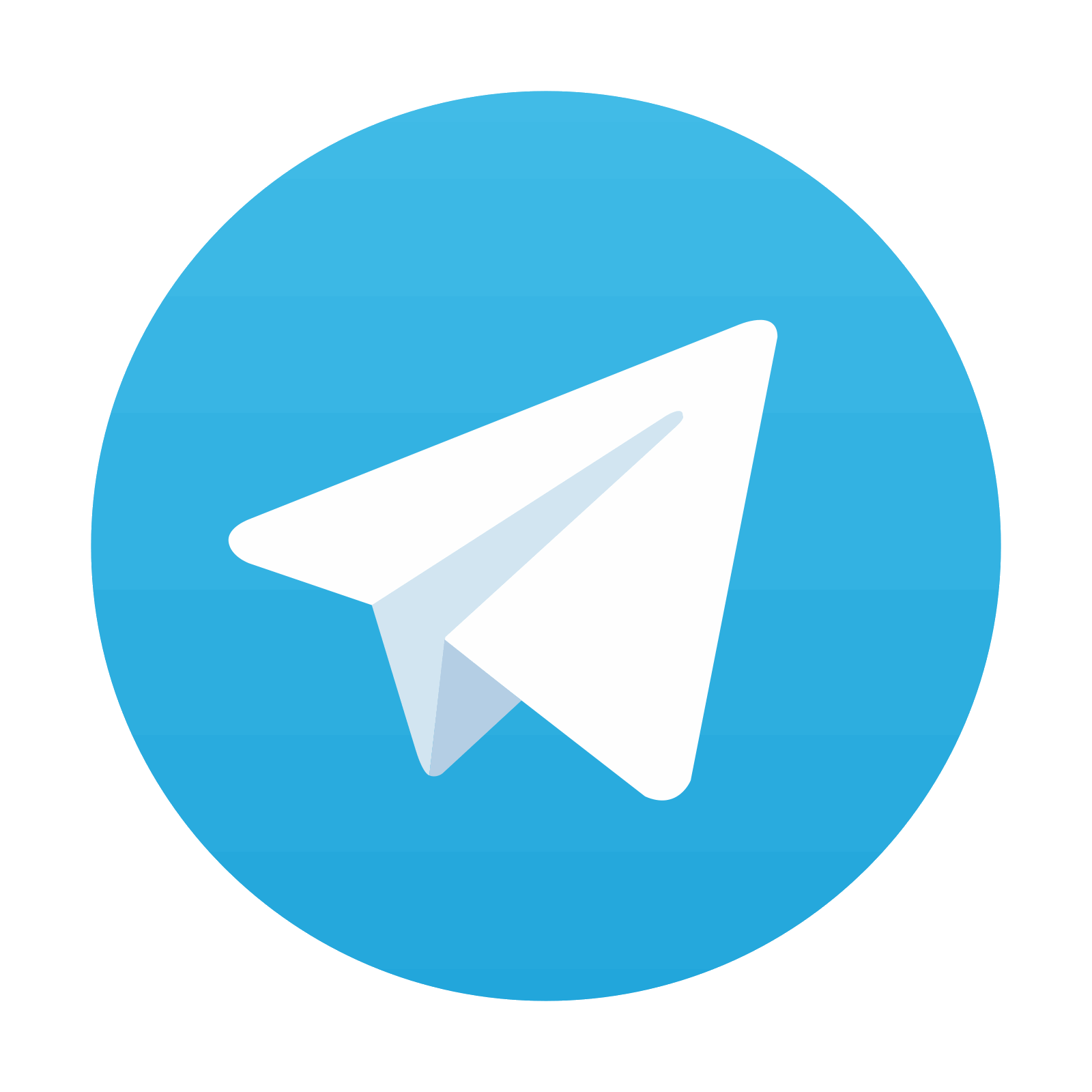
Stay updated, free dental videos. Join our Telegram channel

VIDEdental - Online dental courses
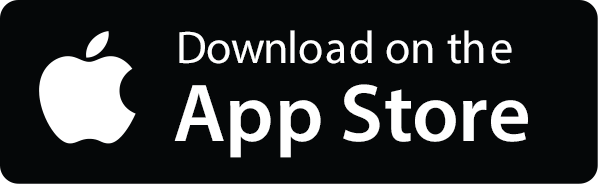
