Abstract
Objectives
Bioactive calcium phosphate cement (CPC) has been used widely to repair bone defects because of its excellent biocompatibility and bioactivity. However, the poor handling properties, low initial mechanical strength, and long setting time of CPC limit its application in vital pulp therapy (VPT). The aim of this study was to synthesize biphasic calcium phosphate/sulfate cements and evaluate the feasibility of applying these cements in VPT.
Methods
The physical, chemical, and mechanical properties of CPC were improved by mixing the cement with various amounts of α-calcium sulfate hemihydrate (CSH). The hydration products and crystalline phases of the materials were characterized using scanning electron microscopy and X-ray diffraction analysis. In addition, the physical properties, such as the setting time, compressive strength, viscosity, and pH were determined. Water-soluble tetrazolium salt-1 and lactase dehydrogenase were used to evaluate cell viability and cytotoxicity.
Results
The developed CPC (CPC/CSH cement), which contains 50 wt% CSH cement, exhibited no obvious temperature increase or pH change during setting when it was used as a paste. The initial setting time of the CPC/CSH biphasic cement was substantially shorter than that of CPC, and the initial mechanical strength was 23.7 ± 5.6 MPa. The CPC/CSH cement exhibited higher viscosity than CPC and, thus, featured acceptable handling properties. X-ray diffraction analysis revealed that the relative peak intensity for hydroxyapatite increased, and the intensity for calcium sulfate dehydrate decreased as the amount of CPC was increased. The cell viability and cytotoxicity test results indicated that the CPC/CSH cement did not harm dental pulp cells.
Significance
The developed CPC/CSH biphasic cement exhibits substantial potential for application in VPT.
1
Introduction
Vital pulp therapy (VPT), including direct and indirect pulp capping and partial pulpotomy, in which material is placed directly over exposed pulp tissue, can be administered to maintain the vitality of exposed pulp and to promote pulp healing and generate reparative dentin . A study suggested using numerous materials in VPT . Calcium hydroxide has been considered the standard direct pulp capping material for several decades . However, calcium hydroxide is highly soluble and is subject to dissolution over time . In addition, calcium hydroxide has no inherent adhesive qualities and provides poor sealing; thus, it cannot prevent long-term microleakage . Mineral trioxide aggregate (MTA) has recently been used as a VPT material. MTA has exhibited excellent biocompatibility, sealing ability, antibacterial properties, mechanical strength, and radiopacity, and can induce the release of bioactive dentin matrix proteins . In addition, MTA promotes the formation of a dentin bridge barrier and causes little or no inflammation at the pulp exposure site . However, the long setting time (approximately 165 min), sandy consistency, and low viscosity limit the application of MTA in VPT .
An ideal material for VPT features high biocompatibility, nontoxicity to pulp tissue, antibacterial properties, acceptable sealing ability, relative stability in the oral cavity, adequate mechanical strength, a short setting time, and excellent handling properties . Although numerous materials have been developed, none of them have fulfilled these clinical demands.
Although MTA have been widely used for root canal therapy, its inconvenient handling properties due to prolong self-hardening time evoke the needs of other material to be developed. Calcium phosphate cement (CPC) has been widely used as a bone substitute in orthopedics, reconstructive surgery and dentistry since it can stimulate osteogenesis . Final product of CPC after setting is hydroxyapatite (HAp), which is the primary mineral component in dentin and facilitates earlier formation of the dentin bridge barrier after it is placed on the exposure site . Furthermore, CPC exhibits high biocompatibility and a self-hardening characteristic; thus, it owns potential properties in develop as an endodontic filling material or sealer and to treat periodontal bone defects . So far, some properties, such as initial mechanical weakness, and long setting time (over 60 mins), which can cause a severe inflammatory response, limit its application in vital pulp therapy (VPT) . The aim of this study was to synthesize biphasic calcium phosphate/sulfate cements and evaluate the feasibility of applying these cements in VPT. We would like to develop a new CPC which own a promising applications in dentistry not only its biocompatibility, a mineralizing ability equivalent to that of MTA but also its good handling property.
Since CPC has now been widely used in orthopedics and dentistry for decades, usually sets rapidly , in order to shorten the setting time and improve the handling properties of CPC, we try to mix CPC with various weight ratios of α-calcium sulfate hemihydrate (CSH; CaSO 4 ·1/2H 2 O). The major components of CPC been used in this study were tetracalcium phosphate (TTCP, Ca 4 (PO 4 ) 2 O) and dicalcium phosphate anhydrous (DCPA, CaHPO 4 ). These materials can be solidified through an in situ reaction with water to form HAp . After the biphasic calcium phosphate/sulfate cement is mixed with water, it becomes a paste before it sets completely; thus, it features favorable handling properties.
In this study, we determined that varying the weight ratios of CSH in biphasic calcium phosphate/sulfate cements significantly affected the physical and mechanical properties of the cement, and an in vitro study was conducted using human dental pulp cells (HDPCs) as a cell source to evaluate the cell viability and cytotoxicity of the developed biphasic cements.
2
Materials and methods
2.1
Preparation of calcium phosphate/sulphate cements
All reagents used in this study were purchased from Sigma–Aldrich Co. (St. Louis, MO, USA). TTCP (Ca 4 [PO 4 ] 2 O) powder was prepared through a solid-state reaction in which 1 mol of calcium pyrophosphate (Ca 2 P 2 O 7 , 401552) and 2 mol of calcium carbonate (CaCO 3 , C6763) were heated to 1400 °C for 3 h. The product was quenched to room temperature, ground in a mortar, and sieved to obtain TTCP powder, which was mixed with a DCPA (CaHPO 4 , C7263) powder in a molar concentration equal to that of the CPC.
Five cements were prepared by mixing CPC and CSH (CaSO 4 ·1/2H 2 O, 12090) at weight ratios of 0%, 25%, 50%, 75%, and 100% (CPC, 3CPC/CSH, CPC/CSH, CPC/3CSH, and CSH). Deionized (DI) water was added to obtain CPC-CSH biphasic cement. The liquid-to-powder ratio (L/P) for all cements was 0.35 mL/g. The mixture was turned into paste, placed into a stainless steel mold with a diameter of 12 mm and a height of 6 mm, and dried in air for 10 min. The specimens were removed from the mold and stored in a sealed container with 100% relative humidity at 37 °C to facilitate further solidification and hydration.
2.2
Setting time and compressive strength measurement
The Gillmore needle test was used to measure the initial setting time and final setting time of the cements. This test was conducted according to ASTM International C266-99 . The CPC-CSH cement paste was placed in a mold as defined in the standards. The mold containing the CPC-CSH cement paste was incubated in a container at 37 °C in > 90% humidity and a normal laboratory atmosphere (25−28 °C). A Gilmore needle with a tip 2.12 mm in diameter was initially fixed on a 113-g moveable rod and moved vertically. The initial setting time was defined as the time at which the needle did not leave a perceptible indentation on the surface of the paste. The final setting time was determined using a needle tip (1.06 mm in diameter) loaded on a 453.6-g moveable rod, which no longer penetrated or indented the surface of the paste. Five specimens in each cement group were measured, and the values are expressed as the mean ± standard deviation (mean ± SD).
The compressive strength on specimens in molds with a diameter of 6 mm and a height of 12 mm was measured according to ASTM International 451-08 . The mold was filled with CPC-CSH cement paste and stored in a sealed container in 100% relative humidity at 37 °C for 14 days. The specimens were removed from the molds and tested using a universal testing machine (Instron 5566, Canton, MA, USA) at a cross-head speed of 1 mm/min. The maximum load required to fracture each specimen was measured and the compressive strength was calculated according to the formula defined in ASTM 451-08:
C = 4 P π D 2
where P is the maximum load applied in newtons, and D is the mean diameter of the specimen in millimeters. Six specimens in each group were tested. The results are expressed as the mean ± SD and were analyzed using a one-way ANOVA. Differences for which P < 0.05 were considered significant.
2.3
pH measurement and temperature difference
The pH values of the tested cement specimens were measured using the temperature-compensated electrode of a digital pH meter (Eutech Alpha pH 500, Singapore). Prior to pH measurement, the apparatus was calibrated with standard pH solutions. Six specimens in each group were measured under the same testing condition. Tubes containing 1 g of cement and 10 mL of a phosphate-buffered saline (PBS) solution were sealed in a container. The pH values of the PBS solutions in the tubes were measured using a pH meter at 37 °C for 1, 2, 4, 8, 12, and 24 h.
The thermal behavior of the CPC-CSH biphasic cement during hardening was examined to determine the temperature variation. The CPC-CSH cement paste was prepared and placed in a polytetrafluoroethylene (Teflon) mold (12 mm in diameter and 6 mm in height). The specimen was stored in a moist atmosphere with 100% humidity at 37 °C. The temperature during cement setting was recorded using a thermocouple. Data were collected every minute for 60 min.
2.4
Hydration product analysis and characterization of microstructures
The hydration products of the cements were analyzed using a Rigaku X-ray powder diffractometer (XRD, Rigaku Geigerflex DMX-2200, Japan) with CuK α radiation ( λ = 1.54 Å) and a Ni filter. The potential was 30 kV and the current was 20 mA. The specimens were scanned in a range from 10° to 70° at a speed of 3°/min. The patterns were analyzed using a model automatched to the Joint Committee on Powder Diffraction Standards (JCPDS) database by using Jade 6.0 software. The tested specimens were filled in XRD sample packing holders (20 mm in length, 15 mm in width, and 0.5 mm in height) and immersed in simulated body fluid (SBF), which is often evaluated by examining the bioactivity of bone cements . After being immersed in SBF for various time intervals (20 min and 1, 3, 7, 14 and 28 days), the holder was soaked immediately in anhydrous ethanol for 1 h to stop the hydration reaction and dried specimens for XRD analysis.
The fractured surfaces of the hydrated cements were observed using scanning electron microscopy (SEM) (JAX-840A, Japan) to examine the morphology of the hydrated crystals and the interlocking between the crystals. The fractured surfaces of the hydrated cements were coated with a gold film approximately 200 Å thick by performing sputtering physical vapor deposition and were examined using SEM.
2.5
Viscosity measurement
The rheological properties of the CPC-CSH cement paste were measured using a cone-and-plate rheometer (TA Instruments, AR 1000) at 25 °C. The L/P ratio of all tested cements was 2 mL/g because the viscosity of the cement was high. The shear rate was used to measure the steady-state flow with cone and plate geometry. The shear rate range was increased from 150/s to 250/s to measure the viscosity of the tested cements.
2.6
Culture of human dental pulp cells
The use of primary HDPCs in this study was approved by the National Taiwan University Hospital Research Ethics Committee, and all patients provided written informed consent. Dental pulp tissues were obtained from freshly extracted premolars and third molars without caries or pulpal diseases. A tissue explant technique was used to cultivate the HDPCs as described previously . Briefly, pulp tissues were minced into small pieces (approximately 1 mm 3 ) and then digested with 3 mg/mL of collagenase type I (Sigma, St. Louis, MO, USA) and 4 mg/mL of dispase (Sigma, St. Louis, MO, USA) for 1 h at 37 °C. Single-cell suspensions were obtained by passing the cells through a 70-mm strainer (Falcon; BD Biosciences, San Jose, CA). The HDPCs were cultured in Dulbecco’s modified Eagle’s medium (DMEM), which contained 4 mM L -glutamine, 4500 mg/L of glucose, and 1 mM sodium pyruvate. The culture medium was supplemented with 10% fetal bovine serum, and the HDPCs were incubated in a humidified atmosphere of 5% CO 2 at 37 °C. When the HDPCs proliferated to 90% confluence in DMEM, the confluent cultures were detached using 0.25% Trypsin-EDTA and subcultured in a flask of DMEM to enable expansion. Cultured HDPCs in Passages 3−10 were used in subsequent experiments.
2.7
Cytotoxicity and cell viability assay
The cytotoxicity of CPC-CSH biphasic cements was measured using a commercial lactate dehydrogenase (LDH) assay kit (CytoTox 96 ® Assay; Promega, San Luis Obispo, CA, USA). When cells are damaged or dead, a large amount of LDH is released from the cell membrane. The cytotoxicity of the CPC-CSH biphasic cement was tested according to ISO 10993-5. Briefly, 0.2 g of CPC-CSH biphasic cement was soaked in 1 mL of DMEM and incubated at 37 °C for 72 h. The HDPCs were seeded in a 96-well plate at a cell density of 5 × 10 3 cells per well for 1 day. At Day 1, a solution containing CPC-CSH biphasic cements in various concentrations was added to a culture plate containing HDPCs. The plates were incubated for 1 day and 3 days. Subsequently, 100 μL of the medium was collected from each well, and the LDH release was measured using an enzyme-linked immunosorbent assay (ELISA) at an optical density of 490 nm.
The cell viability of the CPC-CSH biphasic cement was assessed using a water soluble tetrazolium salt-1 (WST-1) cell proliferation assay kit (Roche Diagnostics, Mannheim, Germany). A colorimetric measurement was performed using the ELISA reader at an absorbance of 440 nm. All in vitro assay data are expressed as the mean ± standard deviation (SD). Statistically significant differences with the control group were determined using an ANOVA. Differences for which P < 0.05 were considered significant.
2
Materials and methods
2.1
Preparation of calcium phosphate/sulphate cements
All reagents used in this study were purchased from Sigma–Aldrich Co. (St. Louis, MO, USA). TTCP (Ca 4 [PO 4 ] 2 O) powder was prepared through a solid-state reaction in which 1 mol of calcium pyrophosphate (Ca 2 P 2 O 7 , 401552) and 2 mol of calcium carbonate (CaCO 3 , C6763) were heated to 1400 °C for 3 h. The product was quenched to room temperature, ground in a mortar, and sieved to obtain TTCP powder, which was mixed with a DCPA (CaHPO 4 , C7263) powder in a molar concentration equal to that of the CPC.
Five cements were prepared by mixing CPC and CSH (CaSO 4 ·1/2H 2 O, 12090) at weight ratios of 0%, 25%, 50%, 75%, and 100% (CPC, 3CPC/CSH, CPC/CSH, CPC/3CSH, and CSH). Deionized (DI) water was added to obtain CPC-CSH biphasic cement. The liquid-to-powder ratio (L/P) for all cements was 0.35 mL/g. The mixture was turned into paste, placed into a stainless steel mold with a diameter of 12 mm and a height of 6 mm, and dried in air for 10 min. The specimens were removed from the mold and stored in a sealed container with 100% relative humidity at 37 °C to facilitate further solidification and hydration.
2.2
Setting time and compressive strength measurement
The Gillmore needle test was used to measure the initial setting time and final setting time of the cements. This test was conducted according to ASTM International C266-99 . The CPC-CSH cement paste was placed in a mold as defined in the standards. The mold containing the CPC-CSH cement paste was incubated in a container at 37 °C in > 90% humidity and a normal laboratory atmosphere (25−28 °C). A Gilmore needle with a tip 2.12 mm in diameter was initially fixed on a 113-g moveable rod and moved vertically. The initial setting time was defined as the time at which the needle did not leave a perceptible indentation on the surface of the paste. The final setting time was determined using a needle tip (1.06 mm in diameter) loaded on a 453.6-g moveable rod, which no longer penetrated or indented the surface of the paste. Five specimens in each cement group were measured, and the values are expressed as the mean ± standard deviation (mean ± SD).
The compressive strength on specimens in molds with a diameter of 6 mm and a height of 12 mm was measured according to ASTM International 451-08 . The mold was filled with CPC-CSH cement paste and stored in a sealed container in 100% relative humidity at 37 °C for 14 days. The specimens were removed from the molds and tested using a universal testing machine (Instron 5566, Canton, MA, USA) at a cross-head speed of 1 mm/min. The maximum load required to fracture each specimen was measured and the compressive strength was calculated according to the formula defined in ASTM 451-08:
C = 4 P π D 2
where P is the maximum load applied in newtons, and D is the mean diameter of the specimen in millimeters. Six specimens in each group were tested. The results are expressed as the mean ± SD and were analyzed using a one-way ANOVA. Differences for which P < 0.05 were considered significant.
2.3
pH measurement and temperature difference
The pH values of the tested cement specimens were measured using the temperature-compensated electrode of a digital pH meter (Eutech Alpha pH 500, Singapore). Prior to pH measurement, the apparatus was calibrated with standard pH solutions. Six specimens in each group were measured under the same testing condition. Tubes containing 1 g of cement and 10 mL of a phosphate-buffered saline (PBS) solution were sealed in a container. The pH values of the PBS solutions in the tubes were measured using a pH meter at 37 °C for 1, 2, 4, 8, 12, and 24 h.
The thermal behavior of the CPC-CSH biphasic cement during hardening was examined to determine the temperature variation. The CPC-CSH cement paste was prepared and placed in a polytetrafluoroethylene (Teflon) mold (12 mm in diameter and 6 mm in height). The specimen was stored in a moist atmosphere with 100% humidity at 37 °C. The temperature during cement setting was recorded using a thermocouple. Data were collected every minute for 60 min.
2.4
Hydration product analysis and characterization of microstructures
The hydration products of the cements were analyzed using a Rigaku X-ray powder diffractometer (XRD, Rigaku Geigerflex DMX-2200, Japan) with CuK α radiation ( λ = 1.54 Å) and a Ni filter. The potential was 30 kV and the current was 20 mA. The specimens were scanned in a range from 10° to 70° at a speed of 3°/min. The patterns were analyzed using a model automatched to the Joint Committee on Powder Diffraction Standards (JCPDS) database by using Jade 6.0 software. The tested specimens were filled in XRD sample packing holders (20 mm in length, 15 mm in width, and 0.5 mm in height) and immersed in simulated body fluid (SBF), which is often evaluated by examining the bioactivity of bone cements . After being immersed in SBF for various time intervals (20 min and 1, 3, 7, 14 and 28 days), the holder was soaked immediately in anhydrous ethanol for 1 h to stop the hydration reaction and dried specimens for XRD analysis.
The fractured surfaces of the hydrated cements were observed using scanning electron microscopy (SEM) (JAX-840A, Japan) to examine the morphology of the hydrated crystals and the interlocking between the crystals. The fractured surfaces of the hydrated cements were coated with a gold film approximately 200 Å thick by performing sputtering physical vapor deposition and were examined using SEM.
2.5
Viscosity measurement
The rheological properties of the CPC-CSH cement paste were measured using a cone-and-plate rheometer (TA Instruments, AR 1000) at 25 °C. The L/P ratio of all tested cements was 2 mL/g because the viscosity of the cement was high. The shear rate was used to measure the steady-state flow with cone and plate geometry. The shear rate range was increased from 150/s to 250/s to measure the viscosity of the tested cements.
2.6
Culture of human dental pulp cells
The use of primary HDPCs in this study was approved by the National Taiwan University Hospital Research Ethics Committee, and all patients provided written informed consent. Dental pulp tissues were obtained from freshly extracted premolars and third molars without caries or pulpal diseases. A tissue explant technique was used to cultivate the HDPCs as described previously . Briefly, pulp tissues were minced into small pieces (approximately 1 mm 3 ) and then digested with 3 mg/mL of collagenase type I (Sigma, St. Louis, MO, USA) and 4 mg/mL of dispase (Sigma, St. Louis, MO, USA) for 1 h at 37 °C. Single-cell suspensions were obtained by passing the cells through a 70-mm strainer (Falcon; BD Biosciences, San Jose, CA). The HDPCs were cultured in Dulbecco’s modified Eagle’s medium (DMEM), which contained 4 mM L -glutamine, 4500 mg/L of glucose, and 1 mM sodium pyruvate. The culture medium was supplemented with 10% fetal bovine serum, and the HDPCs were incubated in a humidified atmosphere of 5% CO 2 at 37 °C. When the HDPCs proliferated to 90% confluence in DMEM, the confluent cultures were detached using 0.25% Trypsin-EDTA and subcultured in a flask of DMEM to enable expansion. Cultured HDPCs in Passages 3−10 were used in subsequent experiments.
2.7
Cytotoxicity and cell viability assay
The cytotoxicity of CPC-CSH biphasic cements was measured using a commercial lactate dehydrogenase (LDH) assay kit (CytoTox 96 ® Assay; Promega, San Luis Obispo, CA, USA). When cells are damaged or dead, a large amount of LDH is released from the cell membrane. The cytotoxicity of the CPC-CSH biphasic cement was tested according to ISO 10993-5. Briefly, 0.2 g of CPC-CSH biphasic cement was soaked in 1 mL of DMEM and incubated at 37 °C for 72 h. The HDPCs were seeded in a 96-well plate at a cell density of 5 × 10 3 cells per well for 1 day. At Day 1, a solution containing CPC-CSH biphasic cements in various concentrations was added to a culture plate containing HDPCs. The plates were incubated for 1 day and 3 days. Subsequently, 100 μL of the medium was collected from each well, and the LDH release was measured using an enzyme-linked immunosorbent assay (ELISA) at an optical density of 490 nm.
The cell viability of the CPC-CSH biphasic cement was assessed using a water soluble tetrazolium salt-1 (WST-1) cell proliferation assay kit (Roche Diagnostics, Mannheim, Germany). A colorimetric measurement was performed using the ELISA reader at an absorbance of 440 nm. All in vitro assay data are expressed as the mean ± standard deviation (SD). Statistically significant differences with the control group were determined using an ANOVA. Differences for which P < 0.05 were considered significant.
3
Results
3.1
Physical properties of the materials
Fig. 1 a shows the initial and final setting times of all tested cements. A clear difference existed between the initial and final setting times of the CPC and CSH cements. The initial and final setting times of the CSH cement were 5 and 10 min, respectively, which are approximately 10 times shorter than those of CPC (60 and 90 min). When the ratio of the 2 cements was 1:1, both the initial and final setting times decreased markedly; these results were consistent with those of the tested CPC/3CSH and CSH cements. The initial and final setting times of the CPC/CSH cement were approximately 7 min and 13 min, respectively. Fig. 1 b shows the compressive strength of all tested cements. The compressive strength decreased as CSH was added and was strongly correlated with the weight ratio of CSH. The highest compressive strength was that of CPC (40.4 MPa), and the lowest compressive strength was that of the CSH cement (15.3 MPa). No significant differences between 3CPC/CSH and CPC/CSH cements or between CPC/3CSH and CSH cements were observed. Fig. 2 a shows the pH values of all tested cements during setting. The pH values of all tested cements immersed in PBS decreased slightly during the setting process and reached a steady value after 12 h of hydration. The pH values of the CPC-CSH cement decreased, whereas the CSH weight percentage increased. Between 1 and 24 h, the pH value of CSH cement ranged from 6.3 to 5.9 and that of CPC ranged from 7.4 to 6.9; the pH value of CSH cement was slightly lower than that of CPC. The variation in the pH value of CPC/CSH cement was smooth and stable, changing from 6.8 at 1 h to 6.6 after 24 h of hydration. Fig. 2 b shows that the thermal changes in CPC and the 3CPC/CSH and CPC/CSH cements were relatively steady compared with those of the CPC/3CSH and CSH cements. However, all cements reached their temperature peak at 30–40 min. The temperature of CPC/CSH cement was higher than that of 3CPC/CSH cement, but the increase was not substantial to the extent that it affected setting and the results. The thermal changes of the CPC and 3CPC/CSH cements were less than 1 °C, and that of the CPC/CSH cement was approximately 2.5 °C. However, the temperatures of the CPC/3CSH and CSH cements increased 4.5 °C and 7.8 °C, respectively.
3.2
Fractographic analysis
Fig. 3 shows the microstructures of the CPC/CSH and CPC/3CSH cements hydrated in SBF for 28 days. The size of calcium sulfate dihydrate (CSD) crystals increased when various ratios of CSH were added. Fig. 3 a and b shows the hydration product of CPC with 50 wt% CSH (CPC/CSH). Fine HAp crystals (1–2 μm) covering most of the fractured surface as well as a few CSD crystals were observed. Fig. 3 c and d indicates that, when CPC contained 75 wt% CSH (CPC/3CSH) and was hydrated in SBF for 28 days, both HAp and CSD crystals appeared on the fractured surface. The hydration product of CPC/3CSH indicated that most of the CSH was transformed into CSD, yielding HAp crystals. Mesh-like HAp and bulk-like CSD crystals (10–25 μm) were observed in the matrix. Mesh-like HAp crystals were observed embedding the pillared CSD crystal matrix ( Fig. 3 d).
3.3
X-ray diffraction analysis
Fig. 4 shows XRD patterns of CPC with 25 wt% CSH (3CPC/CSH), 50 wt% CSH (CPC/CSH), and 75 wt% CSH (CPC/3CSH) recorded 20 min and 1, 3, 7, 14, and 28 days after hydration in SBF. Index peaks for the CSD, CSH, TTCP, DCPA, and HAp structures were identified using JCPDS No. 06-0046, No. 41-0224, No. 25-1137, No. 09-0080, and No. 09-0432, respectively. The peaks at 29.2° and 29.8° corresponded to TTCP structures, those at 26.4° and 30.1° corresponded to DCPA structures, those at 25.9°, 31.7°, 32.1°, and 32.9° corresponded to HAp structures, and those at 11.6°, 20.7°, and 29.1° corresponded to CSD structures.
The XRD pattern of the 3CPC/CSH cement was observed after hydration for 20 min and 1, 3, 7, 14, and 28 days. At 20 min of hydration, the characteristic peaks corresponding to CSH could not be identified, but CSH transformed into CSD crystals, and the HAp crystals could not be identified. The intensities of characteristic peaks corresponding to TTCP and DCPA gradually decreased with the hydration time, whereas the intensities of the major peaks corresponding to HAp increased ( Fig. 4 a). In addition, we analyzed the relative intensities of the CSD and HAp components in the CPC/CSH cements after 14 days of hydration in the SBF solution. CSD formed within 20 min; however, CSD decreased over time. Consequently, no CSD was observed after 28 days ( Fig. 4 b). In the CPC/3CSH cement, most of the CSH transformed into CSD after 28 days of hydration in the SBF solution ( Fig. 4 c). After 28 days, the HAp and CSD crystalline phases coexisted in the matrix, indicating that CSD formation depends on the amount of CSH, and increases in TTCP are associated with decreased transformation of CSH into CSD after 28 days.
3.4
Rheological properties of the materials
Rheological measurement was performed to evaluate the viscosity of the tested cements. Fig. 5 shows the rheometer viscosity values of all tested cements. The viscosity changed according to changes in the shear rate. At a high shear rate (ranging from 150/s to 250/s), CSH cement exhibited the highest viscosity, whereas CPC exhibited the lowest viscosity.
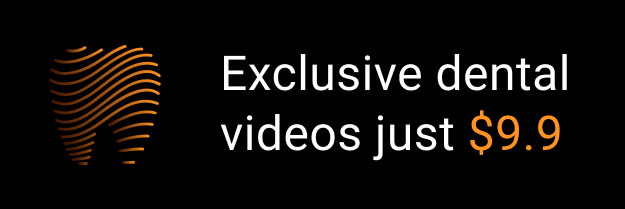