Highlights
- •
The LTD also significantly increased the fracture resistance of zirconia.
- •
The fracture resistance was significantly lower in all groups that were glazed.
- •
The groups were treated with rubber polishers alone presented the highest resistance.
- •
Phase transformations in ultra-translucent zirconia were not observed.
- •
Finishing and polishing induced phase transformation.
Abstract
Objective
To investigate the effect of different surface finishing and polishing regimes and low temperature degradation on flexural strength, phase transformation and surface topography of ultra-translucent ZrO 2 ceramic.
Methods
300 (n = 15/group) of conventional zirconia (Z: Ice Zirkon Transluzent) and ultra-translucent zirconia (UT: Prettau Anterior) bar-specimens were made and divided according to the “Finishing/Polishing” – (C — Control, B — diamond rubber polishers, P — adjusting with burs, PB — adjusting with burs + diamond polishers, PG — adjusting with burs + glaze), “Low temperature Degradation (LTD)” (with or without a treatment at 127 °C, 1.7 bar/24 h). Then, a 3-point mini flexural test was performed in a universal testing machine (1 mm/min, 500 kgf load cell). SEM, EDS, XDR, AFM, optical profilometry and Weibull analysis were performed. Data were analyzed by 3-way ANOVA and Tukey’s post-test (5%).
Results
Groups ZPB D (1670 ± 253 MPa), ZB D (1664 ± 217 MPa), and ZB (1655 ± 3678 MPa) showed significantly higher flexural strength than the UTPG group (372 ± 56 MPa). The Weibull modulus was significantly higher for the ZP D group compared to the UB, UC D , UP D and UPB D , while UTB, UTC D and UTP D had the lowest value . Monoclinic phases were observed only in the conventional zirconia groups and were more evident after LTD. Diamond rubber polishers presented less roughness for both zirconias.
Significance
The use of diamond rubber polishers is the most suitable finishing/polishing method for zirconia ceramic restorations and that final glazing reduces the fracture resistance of these materials.
1
Introduction
Yttria partially stabilized zirconia (Y-PSZ) is one of the most versatileceramic materials used in dentistry because of their excellent mechanical and physical properties [ ]. In recent years, this material has undergone microstructure and composition modifications to improve translucency without losing mechanical properties [ , ]. The first generation monolithic zirconia (3Y-TZP, 3 mol% yttria-stabilized zirconia polycrystals) had high opacity due to the amount and size of the Al 2 O 3 (aluminum oxide) particles. In addition, the material had low structural stability and fracture resistance at high temperatures, and was thus discontinued for dental rehabilitation [ ]. In 2012, a second generation of zirconia with reduced grain size and the amount of aluminum oxide sintering aids and higher translucency was introduced [ ]. But its translucency was still incomparable to glass ceramics used for esthetic restorations.
Further structural modifications, such as reduction in aluminum oxide, increase of yttrium oxide (4–5%), and a cubic-to-tetragonal weight ratio of up to 25–75 [ , ] resulted in the third generation of zirconia, with high translucency and lower fracture resistance compared to previous generations, but better mechanical properties than glass ceramics. These characteristics allowed the ultra-translucent zirconia to be widely used in front teeth restorations such as crowns, veneers, and dental “laminate veneers” [ ] made by CAD/CAM (computer-aided design/ computer-aided manufacturing).
Despite the accuracy of monolithic zirconia restorations made by CAD/CAM technology, small adjustments might often be necessary prior to the cementation for adequate interproximal and occlusal contacts, and overall contour improvement [ , ]. Due to the hardness of zirconia, adjustments are usually made with diamond burs, which affect the glaze layer and original smoothness of the surface [ ]. A rough surface also may cause greater wear of the antagonist tooth, favors biofilm accumulation and affects the surface characteristics make it irregular [ ].
These changes lead to greater stress on the ceramic surface and indirectly increase the degradation of the material and decrease its esthetic and longevity [ ]. In order to reestablish the smoothness and shine of monolithic zirconia surfaces, several techniques have been proposed, such as glazing [ ], polishing with diamond rubber polishers [ ] and the use of fine diamond burs [ ]. Despite the benefits of a polished surface, some finishing and polishing methods can lead to the development of cracks that can propagate under traction forces [ ], weakening the structure.
Among the methods described, application of glaze after adjustment has been questioned. Numerous studies have demonstrated a reduction in the fracture toughness of these ceramics [ , ] after their application and also an increase of the roughness. On the other hand, diamond rubber polishers have been one of the most used methods that produce restorations with better surface morphological characteristics as well as resistance to fracture [ ].
The heating of the zirconia surface during adjustments can promote tetragonal-to-monoclinic phase transformation and affect the resistance to fracture of the material. However, this mechanism is still unclear [ ]. In addition, the fracture resistance of the material can decrease when subjected to hydrothermal degradation and where the phase transformation zone has spread deep into zirconia. There is a formation of small surface defects that tend to propagate throughout the zirconia, affecting the mechanical properties [ ].
Currently, there is no established finishing and polishing protocol for monolithic ultra-translucent zirconia, and the effects on strength and surface characteristics of the available regimes are unknown. Thus, the objective of this study was to evaluate the effect of different finishing and polishing regimes and low temperature degradation on flexural strength, surface topography, and phase transformation of ultra-translucent zirconia. The hypotheses are: h1-hydrothermal degradation can reduce the flexural strength of zirconia, and h2- the adjustments can reduce the flexural strength of the ceramics.
2
Materials and methods
The materials (the trade name, manufacturers, chemical composition and batch number) used in this study are presented in Table 1 .
Material | Trade name | Manufacturer | Composition | Batch number |
---|---|---|---|---|
Polycrystalline tetragonal zirconia (opaque conventional) | Ice Zirkon transluzent | Zirkonzahn, Gais, Itália. | ZrO 2 > 85% Y 2 O 3 – 4–6% Al 2 O 3 < 1% SiO 2 max. 0.02% Fe 2 O 3 max. 0.01% Na 2 O max. 0.04% |
ZB4224A ZB4222E ZB5302G |
Polycrystalline tetragonal zirconia full stabilized by yttria (ultratransluzent) | Prettau Anterior | Zirkonzahn, Gais, Italy. | ZrO 2 > 85% Y 2 O 3 <12% Al 2 O 3 < 1% SiO 2 max. 0.02% Fe 2 O 3 max. 0.02% |
ZB4235E ZB5121B ZB7052D ZB5134A ZB4235C ZB4172F |
Glaze | Ivocolor flúor | Ivoclar, Schaan, Liechtenstein | Glass of aluminum silicate of sodium solvents |
V35797 |
Cylindrical Diamond burs #4135 | KG Sorensen | KG Sorensen, Cotia, Brazil. | Diamond particles | 039910 |
Diamond Rubber for zirconia finishing and polishing | premium compact kit | Dhpro, Paraná, Brazil. | Polyurethane rubber impregnated with diamond particles | OP166 |
2.1
Preparation of samples
The flowchart of the study design is shown in Fig. 1 . Disks (95 mm diameter and 18 mm height) of conventional zirconia (Z) (Ice Zirkon Translucent, Zirkonzahn, Gais, Italy) and ultra-translucent zirconia (UT) (Prettau Anterior, Zirkonzahn, Gais, Italy) were sectioned with double-sided diamond discs (22 × 0.15 mm, Dhpro, Paraná, Brazil) to obtain 300 zirconia bars of 10 × 2.5 mm, with 30 bars having a 1.3 mm height for the control group, and 30 bars having from 1.7 to 2.1 mm for each experimental group. The bars were regularized with 800, 1000, and 1200-grit sand papers.

Prior to sintering, the samples were cleaned in an ultrasonic bath in distilled water for 5 min. With the 25% contraction from sintering (Zirkonofen 600 oven, Zirkonzahn, Gais, Italy) [ ], the final dimensions of the bars were 8 × 2 × 1 mm (± 0.2 mm) for the control groups and 8 × 2 × 1.7–1.3 mm for the treatment groups [ ]. After treatments, all the specimens had the same thickness of 1 mm. The samples were then divided into 20 groups according to the “Ceramics” factor (2 levels), “Finishing and polishing” factor (5 levels), and “Low temperature Degradation — LTD” factor (2 levels).
2.1.1
Finishing and polishing
The samples were adapted to a silicone matrix (Elite, Zhermack, Badia Polinese, Italy) for stabilization and divided into 5 groups:
C: no treatment;
P: smoothing with cylindrical ultra-fine diamond bur (#4135-FG, 90−120 μm, KG Sorensen, Cotia, Brazil) using a high-speed dental micro motor with water cooling and standard movements, until reaching a thickness of 1 mm. Burs were replaced after 10 samples.
B: polishing with abrasive rubber polishers of extra-hard (100 Shore A) diamond-impregnated polyurethane (Premium Compact, Dhpro, Paraná, Brazil). The disks were used according to the manufacturer’s instruction (HZ1DL for wear, HZ2DL for pre-polishing, and HC3DL for high gloss) at 12,000 rpm (20 s per disk) and standard movements, until the surface was smooth and shiny.
PB: combination of burs and rubber polishers as described above.
PG: After burs, application of a single layer of glaze (Ivocolor fluor, Ivoclar, Schaan, Liechtenstein) using a brush followed by sintering.
2.1.2
Low-temperature degradation (LTD)
After the different finishing and polishing regimes, half of the samples of both zirconia groups ( n = 150) were subjected to autoclave hydrothermal degradation (Cristófoli, Paraná, Brazil) for 24 h at 127 °C and 1.7 bar [ ].
2.2
Mini flexure resistance test
The zirconia samples were subjected to the three-point mini flexure resistance test in a universal testing machine (INSTRON, Norwood, Massachusetts, USA). An adjustable metal bending test device was used. The sample was supported by two rolls 6 mm apart with the treated side facing downwards [ ]. Load was applied in the center with a loading rate of 1.0 mm/min and a load cell of 500 kgf [ ]. The flexural strength in MPa was calculated at the time of failure, according to the equation:
where l is the distance (mm) between the support rolls, F is the load (N) applied at the moment of failure, H is the height (mm) of the specimen, and W is the width of the specimen.
2.3
Atomic force microscopy
Forty blocks ( n = 2) of each type of zirconia (4 × 4 × 1 mm) were made to perform the complementary analyzes. For the analysis of surface topography, the silicon tip of the probe was coated with gold (40 μm, 0.01–0.025 Ω cm) and used in intermittent contact mode to obtain the 3D images. The scans were performed in an area of 5 × 5 μm (PPP-NCL probes nanosensors) with constant force of 48 N/m, and the images were processed with the Gwyddion™ software (v 2.33, GNU, Free Software Foundation, Boston, MA, USA).
2.4
X-rays diffraction
X-ray diffraction analysis was performed to evaluate the presence of the monoclinic ( M ) and tetragonal ( T ) phases (Equation A), determine the percentage of zirconia t → m transformations (Equation B) and the depth of the transformation zone (Equation C). The samples used in the atomic force microscopy (N = 40; n = 2) were analyzed in the diffractometer (D2Phaser, Bruker) using copper radiation (CuKα, λ = 1,54 Å). The scans were performed with 10 mA current, 30 kV, using a Lynxeye detector, 0.02 °/step, and acquisition time of 0.1 s. The graphs were generated with Origin 8. Subsequently, the phase percentages were determined, where (−111) M , 2θ = 28 o ; (111) M , 2θ = 31.2°; (101) T . The equations used were:
2.5
Optical profilometry
Eight samples of each group used for the flexural test (8 × 2 × 1 mm) had their surfaces evaluated in a 3D optical profilometer (Taylor Hobson-AMETEK, Leicester, England). An area of 300 × 300 μm was scanned and the mean of three readings was used for the roughness value (Ra) of each group (μm). 2D and 3D images of the surfaces were obtained.
2.6
Scanning Electron microscopy/X-ray dispersive energy spectrometry
Samples were gold-sputtered (BAL-TEC SCD 005) for 130 s at 15 mA to obtain a 80 Å layer. An area of 6 μm with 5000× magnification was evaluated and the percentages of the main chemical elements were obtained. In addition, micrographs were obtained with the scanning electron microscope (SEM) (Hitachi, Tokyo, Japan) to verify the surface modifications promoted by the different treatments.
2.7
Statistical analysis
The power of the study was calculated using the OpenEpi website, considering a 95% confidence interval. Statistical assumptions were evaluated before statistical analysis. The results indicated that the residuals were normally distributed and, by plotting against predicted values, the uniformity was checked, then none of the ANOVA assumptions were violated ( Fig. 2 ). Levene’s test was performed and there was no statistically significant difference amongst the standard deviations (p = 0.647). These results relate that the data follow a normal distribution. Three-way analysis of variance (ANOVA) and Tukey’s test (5%) were performed to compare flexural strength and roughness between groups. The computer program STATISTIX (Analytical Software Inc., version 8.0, 2003) was used for analyses.

Weibull analysis was performed to evaluate the reliability of the flexural strength test, using the Weibull parameter ( m ) and the characteristic strength (σ o ), with a confidence interval of 95%, being determined in a lnσc-ln [ln 1/(1- F (σ c )] diagram (according to ENV 843-5):
The characteristic strength is the strength at a probability of approximately 63.3%, and the Weibull modulus is used as a measure of strength distribution, which expresses the structural homogeneity of the material. Statistical analysis was performed using the Minitab software (version 17, 2013, Minitab, State College, PA). The level of significance was 5%.
3
Results
3.1
Mini flexural strength
The factors “LTD” (p = 0.01), “Finishing/Polishing” (p < 0.001), and “Zirconia” (p < 0.001) independently influenced the values of flexural strength. The interaction of “Polishing x Zirconia” (p = 0.0000) and “Polishing x Zirconia x LTD” (p = 0.02) were also statistically significant. ( Table 2 ).
Source | gl | SQ | QM | F | P |
---|---|---|---|---|---|
Degradation | 1 | 584677 | 584677 | 15,95 | 0,0001 ** |
Finishing and Polishing | 4 | 1.077E+07 | 2694233 | 73,48 | 0,0000 ** |
Zirconia | 1 | 5.680E+07 | 5.680E+07 | 1548.93 | 0,0000 ** |
Degradation x Finishing and Polishing | 4 | 109371 | 27342.7 | 0,75 | 0,5616 |
Degradation x zirconia | 1 | 3589.68 | 3589.68 | 0,10 | 0,7546 |
Finishing and Polishing x Zirconia | 4 | 2808281 | 702070 | 19,15 | 0,0000 ** |
Degradation x Finishing and Polishing x Zirconia | 4 | 432872 | 108218 | 2,95 | 0,0206 ** |
Error | 280 | 1.026E+07 | 36668.0 | ||
Total | 299 | 8.178E + 07 |
Conventional zirconia (1398 MPa) had higher flexural strength than ultra-translucent zirconia (528 MPa). LTD significantly increased the resistance of zirconia (1007 MPa) compared to samples not subjected to LTD (919 MPa). Regarding the “Finishing/Polishing” factor, the use of rubber polishers promoted a higher flexural strength (1183.4 MPa) than the groups treated with Bur + rubber Polisher (1066.4 MPa), Control (1012 MPa), Bur (933 MPa), and Bur + Glaze (621 MPa) — Tukey test.
The comparison between all the experimental groups ( Table 3 ) showed that the ZPB D (1670 ± 253), ZB D (1664 ± 217) and ZB (1655 ± 3678) groups had the highest flexural strength, and were different from the other groups except ZP D (1499 ± 134), ZPB (1497), ZC D (1464 ± 258), and ZC (1456 ± 222). The ultra-translucent zirconia (UT) groups presented lower flexural strength. The UTB (624 ± 186), UTB D (792 ± 169CD), UTC D (679 ± 225) and UTPB D (602 ± 164) groups had significantly higher flexural strength values compared to the other groups, and UPG (372 ± 56) had the lowest value, which was significantly different from the other groups, especially when compared to the groups treated with rubber polishers.
Finishing/polishing | Conventional (Z) | Ultratransluzent (UT) | ||
---|---|---|---|---|
without | with | without | with | |
Control (C) | 1456.1 ± 220.5 AB | 1463.9 ± 258.2 AB | 450.8 ± 79.5 EFG | 678.7 ± 225.4 CDE |
Burs (P) | 1343.1 ± 169.7 B | 1499.3 ± 133.9 AB | 460.3 ± 72.8 EFG | 429.9 ± 182.3 FG |
Diamond rubber polishers (B) | 1654.7 ± 367.7 A | 1663.5 ± 216.8 A | 623.5 ± 185.9 DEF | 791.8 ± 169.4 CD |
Burs + Diamond Rubber polishers | 1497.1 ± 196.0 AB | 1670.2 ± 252.7 A | 496.0 ± 103.6 EFG | 602.3 ± 163.9 DEFG |
Burs + Glaze | 837.3 ± 189.8 CD | 898.2 ± 212.4 C | 372.1 ± 56.2 G | 376.0 ± 75.6 FG |
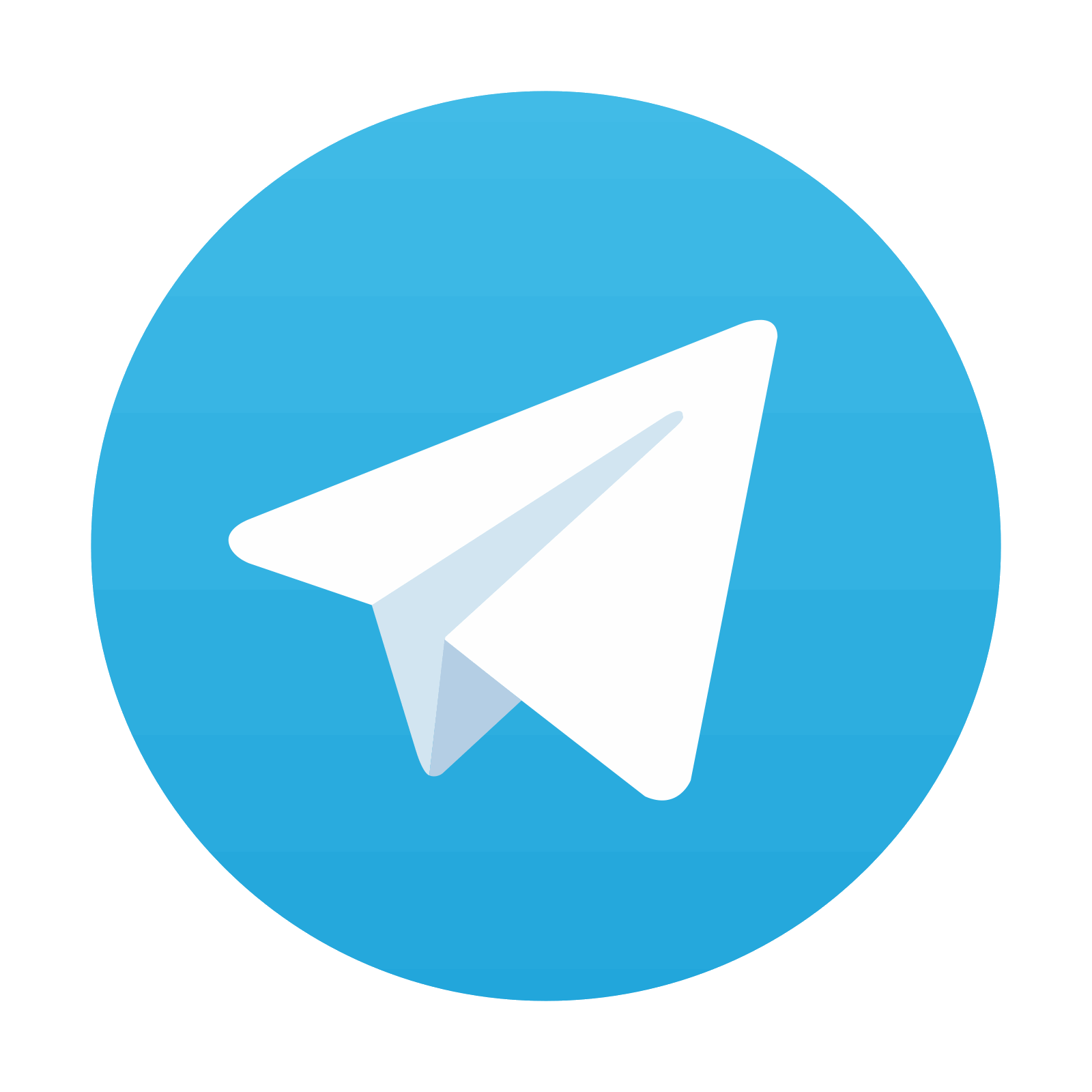
Stay updated, free dental videos. Join our Telegram channel

VIDEdental - Online dental courses
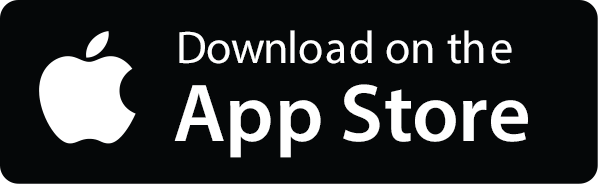

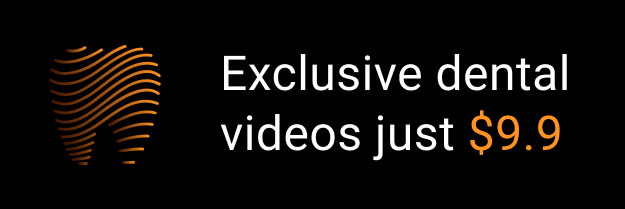