Abstract
Objectives
Casein phosphopeptide–amorphous calcium phosphate (CPP–ACP) is a milk derivative which holds nanoclusters of calcium and phosphate ions. The presence of CPP–ACP has been found to reduce demineralization and enhance remineralization in subsurface enamel and in dentin. Incorporation of CPP–ACP into luting cements has not been investigated. The aim of this study was to determine the effect on the physical properties of two commercially available zinc oxide non-eugenol temporary luting cements with incorporation of up to 8% (w/w) CPP–ACP.
Methods
Setting time, compressive strength, diametral tensile strength, film thickness and solubility tests were investigated for 0, 0.5, 1.0, 2.0, 3.0, 4.0 and 8.0% (w/w) CPP–ACP incorporated into Freegenol™ and Temp-Bond ® NE. Tests were carried out based on ISO 3107 requirements.
Results
Compressive and diametral tensile strengths progressively decreased with increasing concentrations of up to 8.0% (w/w) CPP–ACP incorporated into both Freegenol™ and Temp-Bond ® NE. Setting time was delayed beyond ISO requirements. Film thickness was not adversely affected. Increased solubility of Temp-Bond ® NE with 8.0% (w/w) CPP–ACP incorporation suggested an effect of the CPP–ACP on this property for this cement.
Significance
The incorporation of up to 8.0% (w/w) CPP–ACP into two zinc oxide non-eugenol luting cements has no adverse effects on the film thickness, compressive strength and diametral tensile strength of the cements investigated. Solubility investigations suggest that CPP–ACP leaches out of the zinc oxide non-eugenol luting cements into an aqueous environment.
1
Introduction
Casein phosphopeptide–amorphous calcium phosphate (CPP–ACP) complexes are produced by tryptic digestion of the milk protein casein by aggregation with calcium and phosphate ions and purification by ultrafiltration . Casein phosphopeptides contain the sequence Ser(P)–Ser(P)–Ser(P)–Glu–Glu. Through their multiple phosphoseryl residues, the casein phosphopeptide (CPP) binds to clusters of amorphous calcium phosphate (ACP), preventing their growth to the critical size required for nucleation and precipitation. The proposed mechanism for anticariogenicity of CPP–ACP is the localization of ACP in dental plaque thus buffering free calcium and phosphate ion activities. This provides a state of supersaturation of these ions with respect to tooth enamel, inhibiting demineralization and enhancing remineralization.
It has been shown that the incorporation of CPP–ACP into a glass-ionomer cement restorative material provided enhanced protection of the adjacent dentin during acid challenge in a laboratory study . This is due to the ability of CPP–ACP to localize amorphous calcium phosphate at the tooth surface, thereby helping to maintain a state of supersaturation with respect to tooth mineral. The CPP–ACP complexes have been shown to prevent demineralization and promote remineralization of enamel subsurface lesions in laboratory , animal and in situ caries models . More recently, a laboratory study has also shown a similar effect in dentin following a 5-min application of Tooth Mousse™ (GC Int. Corp., Tokyo, Japan) .
Thus far, CPP–ACP has been incorporated into glass-ionomer restorative materials or applied directly as a paste onto tooth surfaces to remineralize early caries lesions in enamel. The physical properties and ion release of a glass ionomer cement restorative material were investigated using 0.78, 1.56 and 3.91% (w/v) of CPP–ACP .
Dentin hypersensitivity following crown preparation is common problem in dentistry. The pain is speculated to be due to fluid movement within the dentin tubules based on Brännström’s hydrodynamic theory. The incorporation of CPP–ACP into temporary luting agents is hoped to facilitate the ingress of CPP–ACP molecules onto the surface of dentin tubules and ultimately into the dentinal tubules. The ingress of CPP–ACP may result from forces during crown cementation from pulpward cementation pressures . Mechanical occlusion of surface dentin could potentially reduce the incidence of dentin hypersensitivity and pulpal inflammation following crown preparation. It has been shown that glass-ionomer luting cements exhibited a lower setting pH than zinc phosphate and zinc polycarboxylate luting cements, remaining at pH values less than 4.0 for 30 min after mixing . The presence of a temporary luting cement containing basic CPP–ACP particles may increase the buffering capacity of the dentin surface in returning the pH back to neutral. The most common cause of failure in crowned teeth is caries . Leakage at the marginal areas of provisional crowns which is to an extent unavoidable may be amenable to dissolution of the temporary luting agents releasing CPP–ACP complexes containing saturated levels of calcium and phosphate ions. This dissolution of ions may provide an additional inhibition of demineralization, particularly during extended periods of provisional full coverage restorations. No previous studies have been carried out to determine the possibility of incorporating CPP–ACP powder into the base or accelerator pastes of commercially available zinc oxide non-eugenol temporary luting cements. It is therefore necessary to determine if the incorporation of CPP–ACP can be carried out without adversely affecting the setting reaction and usability of these temporary luting cements.
The aim of this study was to determine whether incorporation of CPP–ACP powder into two commercially available zinc oxide non-eugenol temporary cements would alter the physical characteristics, based on ISO recommendations.
2
Materials and methods
2.1
Setting time
The base and accelerator pastes of Freegenol™ (GC Int. Corp., Tokyo, Japan, batch no: 0405061) and Temp-Bond ® NE (Kerr, Romulus, MI, USA, batch no: 7-1008) were weighed to an accuracy of 0.1 mg using a weighing machine (E. Mettler, Zurich, Switzerland) on a fresh sheet of mixing paper. For Freegenol™, the base and accelerator were weighed to a proportion of 4:1, respectively. This ratio was chosen after a pilot study revealed that it closely approximated equal volumetric amounts of paste, as recommended by the manufacturer. With Temp-Bond ® NE, a w/w ratio of 5:2 for the base to accelerator was used based on manufacturer’s recommendations. Following this, the amount of CPP–ACP powder (Recaldent™, CASRN691364-49-5, batch DE/SS/NC, manufactured 09/06/2000) was determined weight per weight according to the percentage required ( Table 1 ).
Produce name | Type | Manufacturer | Composition | Batch | Base:accelerator | |
---|---|---|---|---|---|---|
Freegenol™ | Zinc oxide non-eugenol temporary luting agent | GC Corp., Tokyo, Japan | Base | Zinc oxide | 0405061 | 4:1 |
Olive oil | ||||||
Vaseline | ||||||
Pigment | ||||||
Accelerator | Polymerized fatty acids | |||||
Ester gum | ||||||
Beeswax | ||||||
Olein acid | ||||||
Temp-Bond ® NE | Zinc oxide non-eugenol temporary luting agent | Kerr, Manufacturing Co., Romulus, MI | Base | Zinc oxide | 7-1008 | 5:2 |
Mineral oil | ||||||
Corn starch | ||||||
Accelerator | Resin | |||||
Ortho-ethoxybenzoic acid | ||||||
Carnauba wax | ||||||
Octanoic acid |
Mixing of each specimen was carried at an ambient room temperature of 23 °C and 60 ± 5% relative humidity. All pre-measured pastes and CPP–ACP powder were mixed together manually using a stainless steel mixing spatula within the recommended mixing time of 20–30 s. The mixture was then placed in a circular stainless steel mold and allowed to set in an incubator maintained of 37 ± 2 °C with a relative humidity of 90 ± 5%. A weighted metal indenter of mass 400 ± 2 g with a flat ended cylindrical tip 1.0 ± 0.1 mm in diameter was lowered vertically onto the surface of the cement every 15 s. Setting time was the time period from the start of mixing to the time the indenter failed to completely penetrate the depth of the cement.
The control was the base and accelerator of Freegenol™ mixed without addition of CPP–ACP. The test groups involved 0.5%, 1.0%, 2.0%, 3.0%, 4.0% and 8.0% CPP–ACP added to the cement. A sample size of five specimens in each test group was used. The five specimens were measured at 15-s intervals.
2.2
Compressive strength
Cylindrical specimens (6 mm × 4 mm) of both cements with incorporated CPP–ACP were made using lubricated brass molds. One hour following mixing, the specimens were lapped in their molds with 1200-grit silicon-carbide paper and de-ionized water to produce a cylinder of 4.0 ± 0.1 mm (diameter) × 6.0 ± 0.1 mm in length. All specimens were maintained in distilled water at 37 ± 2 °C until the time of testing. Testing was then performed 24 h after specimen production on a universal testing machine (Model 5544, Instron ® , Massachusetts, USA) at a cross-head speed of 1.0 mm/min. Compressive strength values are reported as a mean of five specimens.
2.3
Diametral tensile strength
Specimens were prepared in the same manner as the compressive strength specimens. However, vertical loading was applied across the diameter of the specimens which were placed length-wise on the platens of the universal testing machine. The cross-head speed was identical at 1.0 mm/min. Five specimens were fabricated for each test group, and mean tensile strengths calculated.
2.4
Film thickness
Two flat square glass plates of uniform thickness and an area of 2 cm 2 were used. Thickness measurements were carried out using a digital micrometer (Bocchi, Pontoglio, Italy) accurate to 1 μm. Two minutes after the start of mixing, a vertical load of 15 kg was applied on the top plate. Ten minutes after the start of mixing, the thickness of the two glass plates with the interposing cement was measured once again with the micrometer. Film thickness for each specimen is the difference in thickness of the two glass plates with and without cement. There were seven test groups, which contained 0% (control), 0.5%, 1.0%, 2.0%, 3.0%, 4.0% and 8.0% of CPP–ACP with the two cements. Each group had a sample size of five, from which mean thicknesses were calculated.
2.5
Solubility/disintegration
Solubility investigations of Freegenol™ and Temp-Bond ® NE were carried out with two test groups. Based on the concentrations used previously in this study, a median and high concentration of 3.0 and 8.0% (w/w) of CPP–ACP, respectively, were chosen. The base and accelerator pastes of the temporary luting agents were weighed to an accuracy of 0.1 mg, to the recommended ratio of 4:1 and 5:2 for Freegenol™ and Temp-Bond ® NE, respectively. Manual mixing was carried out on a mixing pad using a stainless steel spatula in ambient conditions (23 ± 2 °C, relative humidity 60 ± 5%). A mixing time of 1 min was utilized to achieve an even mix of CPP–ACP powder into the pastes.
A length of waxed dental floss approximately 10 cm in length was cut and weighed to an accuracy of 0.1 mg on a weighing machine (E. Mettler, Zurich, Switzerland). Stainless steel washers of 20 mm internal diameter and 1.5 mm thickness were used as molds to prepare the specimens. A thin layer of vaseline coated the washers to facilitate removal of specimens. One end of the floss was threaded through the center of the washer, and left to extend approximately 1–2 cm past the washers on a flat glass surface. The mix of the luting cement incorporated with CPP–ACP was loaded carefully into the washer tilted at a slight angle in order to avoid formation of voids in the specimen. A glass slide was placed on top and pressed firmly against the metal washer in order to remove excess material. The mold assembly was then placed in an incubator at 37 ± 2 °C and 90 ± 5% relative humidity for 1 h. Following this, excess cement was carefully removed with a sharp metal instrument around the edge of the mold. The specimen disc with attached floss was briefly rinsed with distilled water and blotted dry. Two specimens were suspended in a screw-top container containing 50 mL of distilled water ensuring they were not in contact with each other or the wall of the container. The container was then placed in a humidified incubator at 37 ± 2 °C and 90 ± 5% relative humidity for 24 h. At one day following soaking of the specimens, cement discs were rinsed briefly with de-ionized water, gently blotted dry, weighed to an accuracy of ±0.1 mg, then placed in a desiccator with silica gel and weighed daily. This procedure was repeated until the weight change from one measurement to the next was less than 0.001 g. The percentage weight loss or solubility was calculated as:
M 1 = weight of disc 1 h after the start of mixing
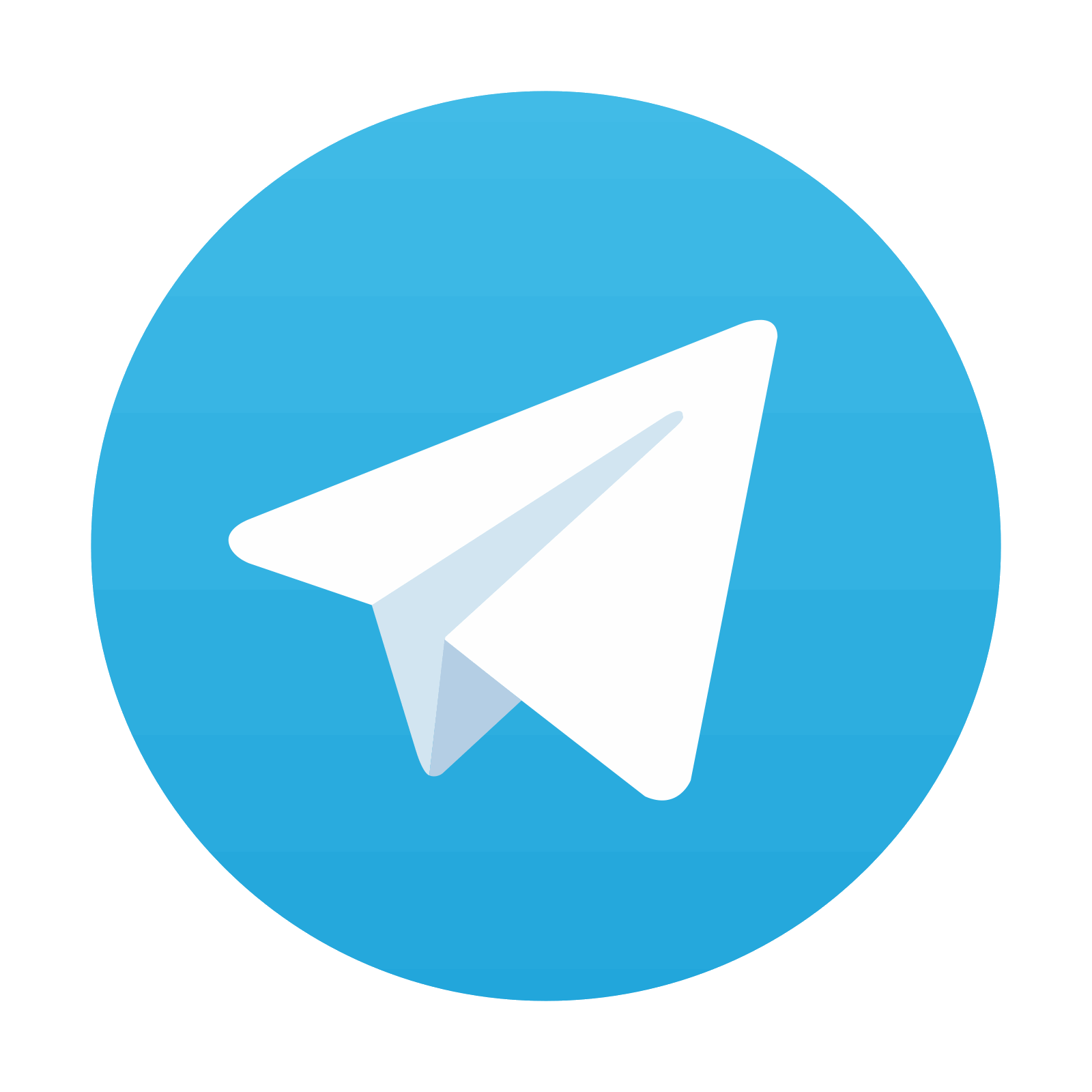
Stay updated, free dental videos. Join our Telegram channel

VIDEdental - Online dental courses
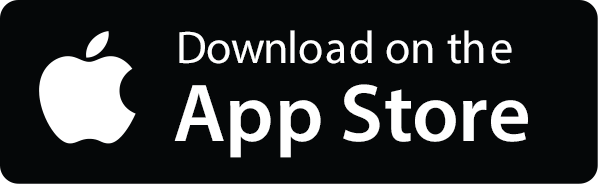
