Abstract
Objective
To investigate the effect of autoclave induced low-temperature degradation on the adhesion energy between yttria-stabilized zirconia veneered with porcelain.
Methods
The strain energy release rate using a four-point bending stable fracture test was evaluated for two different porcelains [leucite containing (VM9) and glass (Zirox) porcelain] veneered to zirconia. Prior to veneering the zirconia had been subjected to 0 (control), 1, 5, 10 and 20 autoclave cycles. The specimens were manufactured to a total bi-layer dimension of 30 mm × 8 mm × 3 mm. Subsequent scanning electron microscopy/energy dispersive spectrometry, electron backscatter diffraction and X-ray diffraction analysis were performed to identify the phase transformation and fracture behavior.
Results
The strain energy release rate for debonding of the VM9 specimens were significantly higher ( p < 0.05) compared to the Zirox specimens across all test groups. Increasing autoclave cycles lowered the strain energy release rate significantly ( p < 0.05) from 18.67 J/m 2 (control) to the lowest of 12.79 J/m 2 (cycle 10) for only the VM9 specimens. SEM analyses showed predominant cohesive fracture within the porcelain for all cycle groups. XRD analysis of the substrate prior to veneering confirmed a tetragonal to monoclinic phase transformation with increasing the number of autoclave cycles between 5 and 20. The monoclinic phase reverted back to tetragonal phase after undergoing conventional porcelain firing cycles. EBSD data showed significant changes of the grain size distribution between the control and autoclaved specimen (cycle 20).
Significance
Increasing autoclave cycles only significantly decreased the adhesion of the VM9 layered specimens. In addition, a conventional porcelain firing schedule completely reverted the monoclinic phase back to tetragonal.
1
Introduction
In recent years, the rising price of gold and increasing esthetic demands has led to increased interest in the development of alternative substructures for dental restorations. In particular, yttria-stabilized zirconia has received considerable attention due to its superior mechanical properties compared to other ceramic systems. Previous in vitro studies have identified flexural strength of up to 900–1200 MPa and fracture toughness in the range of 5.9–10 MPa m 1/2 . Short and medium-term clinical studies have also reported that yttria stabilized tetragonal zirconia polycrystal (Y-TZP) frameworks exhibit high stability and fracture resistance . However, a common issue associated with zirconia is the unknown effects of low-temperature degradation (LTD) . LTD is a process where a spontaneous tetragonal to monoclinic (t to m) phase transformation occurs as a result of prolonged moist low-temperature conditions and not as a result of applied local stress such as at the tip of an advancing crack . Previous applications of Y-TZP in orthopedics have demonstrated catastrophic failures as a result of LTD . However, the use of Y-TZP in dentistry, up till now, has shown no evidence that indicates LTD having a significant effect on the reliability of the restoration . Nonetheless, a recent study by Tholey et al. did observe that the moisture induced LTD accompanied with glass induced dissolution from porcelain sintering at the Y-TZP interface resulted in severe surface faceting to occur. These surface facets have been shown by atomic force microscopy techniques to be monoclinic (martensitic) self-accommodating variants which are induced through LTD. In addition, the bonding mechanism between Y-TZP and the veneering porcelain is still not thoroughly understood . Ban proposed that the main bonding mechanism was micromechanical interaction. Fischer et al. on the other hand found that an adequate bond was produced even with a highly polished zirconia surface. Furthermore, Choi et al. suggested that zirconia and glass ceramic established a thermodynamically stable equilibrium by dissolution of the zirconia ions into the veneering material. Therefore, at this stage, the bonding characteristics between Y-TZP and the veneering material appear to involve both chemical and mechanical interaction.
One of the key reasons of this study was to investigate the effects of possible routine procedures such as high pressure steam cleaning, fine adjustments with diamond burs and sandblasting of the Y-TZP interface. These practices may all induce unintended t to m transformation at the surface which accompanied with moisture induced LTD addressed above, may have a significant influence on the adhesion of the Y-TZP–porcelain interface. A known method to accelerate in a controlled manner the t to m transformation is by autoclave treatment . This technique allows us to critically observe the effect on the veneering adhesion as the amount of monoclinic zirconia at the surface is increased.
Therefore, the aim of this research was to investigate and quantify the extent to which monoclinic zirconia induced by autoclaving prior to veneering with porcelain had on the adhesion between zirconia and porcelain. The adhesion energy was quantified using a four-point bending stable fracture test.
2
Materials and methods
The bi-layered specimens were fabricated using a Y-TZP substrate (In-Ceram YZ, Vita, Bad Säckingen, Germany) veneered with two porcelains: a glass based (Zirox, Wieland Pforzheim, Germany) and a leucite based porcelain (VM9, Vita, Bad Säckingen, Germany). There were 10 groups; each with 15 specimens which came to a total sample size of 150. A summary of the specifications for the veneering porcelain and substrate material are listed in Table 1 .
Material | Processing method | Product/manufacturer | Product | CTE (ppm/K) | LOT |
---|---|---|---|---|---|
Glass-based leucite-free porcelain | Layering technique | Wieland Dental, forzheim, Germany | Zirox | 9.3 | 5/08–6/09 |
Fine structure feldspar veneering porcelain | Layering technique | Vident, VITA Zahnfabrik, Bad Säckingen, Germany | VITA VM9 | 8.8–9.2 | 10681–26540 |
5 wt% yttria-stabilized zirconia | CAD/CAM sintered | Vident, VITA Zahnfabrik, Bad Säckingen, Germany | VITA In-Ceram YZ | 10.5 | 11750–16270 |
2.1
Preparation of the substrate material
Rectangular pre-sintered zirconia blocks were sectioned under water lubrication to the desired oversized dimension of 37.5 mm × 10 mm × 1.875 mm using the Accutom-50 (Struers, Denmark), precision cut-off machine. The oversize dimension was required in order to compensate for the approximate 20% shrinkage of the zirconia after sintering. The specimens were subsequently ultrasonically cleaned in water for 5 min, air dried and sintered at 1530 °C as recommended (Vita ZYrcomat, Vita, Bad Säckingen, Germany), resulting in a final substrate dimension of 30 mm × 8 mm × 1.5 mm. The dimensions in each stage of production were measured with a digital caliper accurate to 0.01 mm. Prior to the veneering of the specimens, high pressure steam autoclaving was performed (134 °C for ∼4 min per cycle) for 0 (control), 1, 5, 10 and 20 autoclave cycles. The control (0 autoclave cycles) was selected as the basis of comparison to all other autoclaved groups. Subsequent autoclave cycles of 1, 5, 10 and 20 were performed to observe the influence of induced LTD on the adhesion between the zirconia and porcelain.
2.2
Preparation of the veneering porcelain
Veneering of the porcelain on the zirconia substrate was performed with the traditional layering technique with assistance from a metal template. A total of four firings excluding the final glaze firing, (wash bake, 1st dentin and two 2nd dentin firings) were required to produce the layer of veneering porcelain. In addition, an extended drying time of 12 min with the 1st and 2nd dentin firings were used to compensate for the large volume of porcelain. This procedure is not usually performed because typical restorations are smaller and are sufficiently dried with the normal drying time. The other firing procedures as recommended by the manufacturer remained unchanged. After the specimens were layered with veneering porcelain, the top of the porcelain surfaces were wet-ground using 320–1200 grit-size silicon carbide abrasive paper (Struers) to obtain a flat surface and consistent dimensions of 30 mm × 8 mm × 1.5 mm before final glaze firing. One lateral surface of each specimen was polished to a 5 μm finish and coated with a ∼10 nm carbon layer for SEM analysis.
2.3
X-ray diffraction
X-ray diffraction (XRD) analyses were conducted to determine the relative amount of monoclinic phase present in the as-sintered (control), autoclave treated specimens (autoclave cycles 1–20) and autoclave treated then sintered specimens (autoclave cycle 20 sinter treated). XRD analyses were performed at two different angles: glancing at fixed incidence angle of 5° and standard angle, which were scanned between 3° and 80° 2 θ for 20 min (0.05° step size Cu radiation) (Philips, PANalytical X’Pert Pro MPD system). A simple method proposed by Garvie and Nicholson was used to estimate the volume percentage of monoclinic content present while the monoclinic transformation depth was calculated by the formula proposed by Kosmać et al. .
2.4
Interfacial strain energy release rate test
The adhesion energy between the porcelain and Y-TZP interface was measured using the approach proposed by Charalambides et al. . This approach measured the strain energy release rate of a stable crack extension along the bi-layer interface. Following Suansuwan and Swain , the porcelain layer of the specimen was notched close to the bi-layer interface using a water-cooled diamond impregnated saw and a small pre-crack (<2 mm) was initiated. The total bi-layer dimension of the specimens were 30 mm × 8 mm × 3 mm and were stored in kerosene immediately after pre-cracking to minimize the influence of water vapor on crack growth .
Testing of the bi-layer specimens were performed on a Universal Testing Machine (Instron 3369) using a four point bending jig ( Fig. 1 ) with a 500 N load cell at a crosshead speed of 0.05 mm/min and data recorded with BlueHill 2 (Version 2.03.0359) software. Specimens exhibited stable crack propagation as indicated by a plateau on the force–displacement curve as shown in Fig. 2 . The mean value of the plateau load was used to calculate the strain energy release rate ( G ) using the formula :
G = η ( p 2 l 2 ) ( l − v z 2 ) E z b 2 h 3
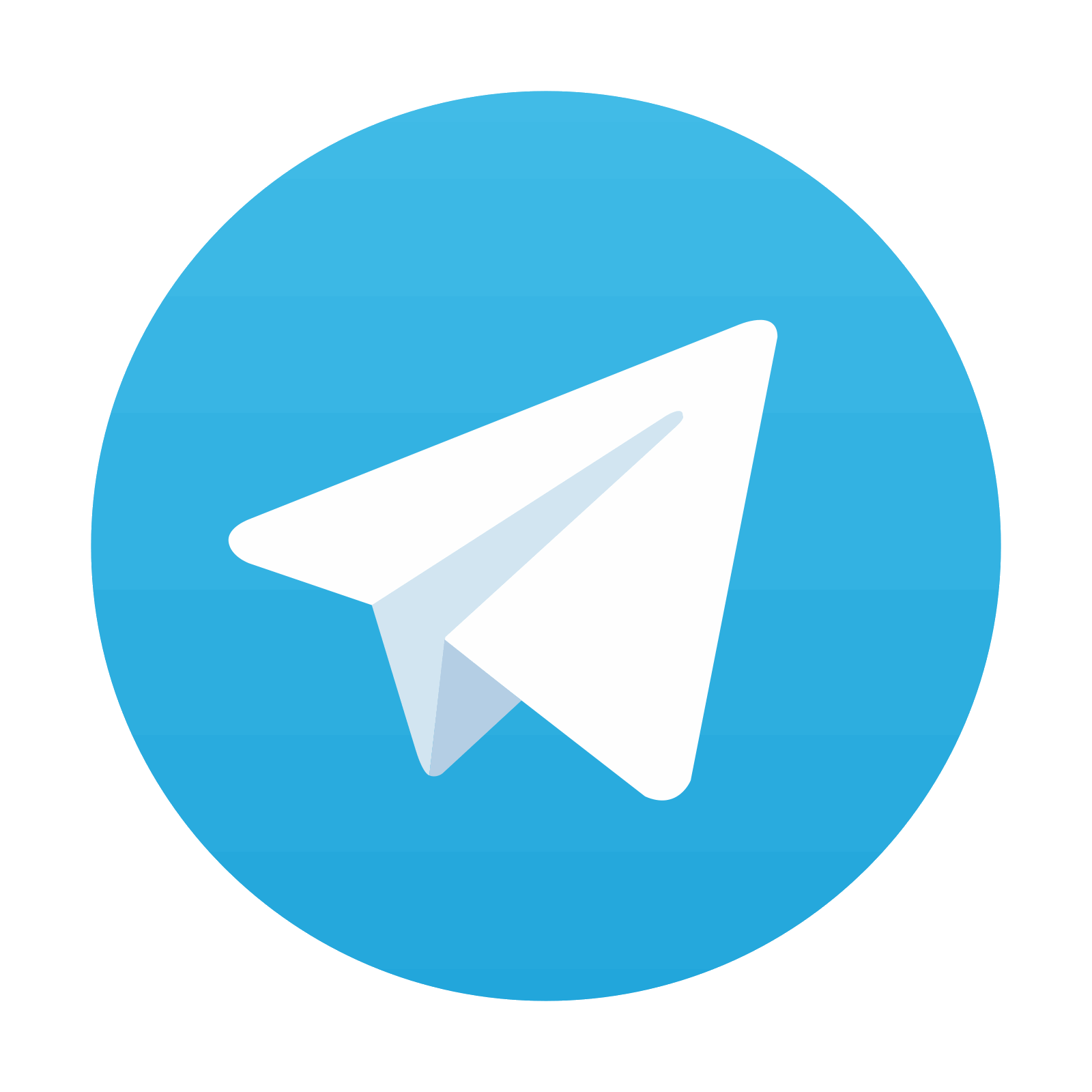
Stay updated, free dental videos. Join our Telegram channel

VIDEdental - Online dental courses
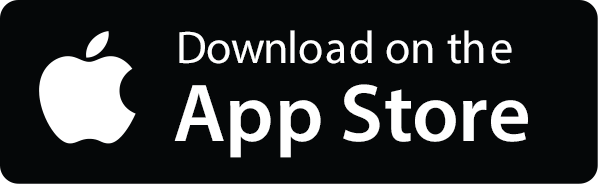
