Dental Waxes, Casting Investments, and Casting Procedures
Composition of Dental Waxes
Most dental waxes contain 40% to 60% paraffin by weight, which is derived from high-boiling fractions of petroleum. They are composed mainly of a complex mixture of hydrocarbons of the methane series together with minor amounts of amorphous and microcrystalline phases. The wax can be obtained in a wide range of melting or softening temperatures depending on the molecular weight and distribution of the constituents. The melting range can be determined by a temperature versus-time cooling curve, as shown in Figure 10-1, for a paraffin-based inlay wax. The temperature-time relationship during cooling indicates the successive solidification of progressively lower-molecular-weight fractions. This condition promotes moldability of the wax below its melting temperature. Paraffin that is used for type I waxes has a higher melting point than the paraffin used for type II waxes. Paraffin wax is likely to flake when it is trimmed, and it does not produce a smooth, glossy surface, which is a desirable requisite for an inlay wax. Thus, other waxes and natural resins must be added as modifying agents.
Desirable Properties of Wax
1. The wax should be uniform when softened. It should be compounded with ingredients that blend with each other so that there are no granules on the surface and no hard spots within the surface when the wax is softened.
2. The color should contrast with die materials or prepared teeth. Since it is necessary to carve the wax margins against the die surface, the wax must exhibit a definite contrast in color and sufficient opacity in thin layers to facilitate proper finishing of the margins.
3. The wax should not fragment into flakes or similar surface particles when it is molded after softening. Such flakiness is likely to be present in paraffin wax, so modifiers must be added to minimize this effect.
4. Once the wax pattern has solidified, it is necessary to carve the original tooth anatomy and the margins so that the pattern conforms precisely to the surface of the die. The latter procedure sometimes requires that the wax be carved to a very thin layer. The wax must not be pulled away by the carving instrument or chip as it is carved or such precision cannot be achieved.
5. For lost-wax casting of metals, an investment mold is formed around a wax pattern. After the mold containing the wax pattern has been formed, the wax must be eliminated from the mold. Elimination of the sprued wax pattern is usually accomplished by heating the mold to melt and ignite the wax. If the wax leaves a residue or an impervious coating on the walls of the mold, the cast metal inlay may be adversely affected. Consequently, the wax should burn out completely by oxidizing residual carbon to volatile gases. Ideally, when wax melts and is vaporized at 500 °C, it should not leave a solid residue that amounts to more than 0.10% of the original weight of the specimen.
Flow of Dental Wax
One of the desirable properties of type I inlay wax is that it should exhibit a marked plasticity or flow at a temperature slightly above that of the mouth. The temperatures at which the wax is plastic are indicated by the time-temperature cooling curve for a typical type I wax, as shown in Figure 10-1. The wax begins to harden slowly below 65 °C and becomes solid below approximately 48 °C; below which it cools rapidly at a constant rate.
Requirements for the flow properties of inlay waxes at specific temperatures are summarized in Table 10-1. The flow is measured by subjecting cylindrical specimens to a designated load at the stated temperature and measuring the percentage of reduction in length. The maximum flow permitted for type I waxes at 37 °C is 1%. Their low flow at this temperature permits carving and removal of the pattern from the prepared cavity at oral temperature without distortion. In addition, both type I and type II waxes at 45 °C must have a minimal flow of 70% and a maximum flow of 90%. At this temperature, the wax is inserted into the prepared cavity. If the wax does not have sufficient plasticity, it will not flow into all of the areas in the preparation and reproduce the details that were established by the invested wax pattern.
TABLE 10-1
Requirements for Inlay Wax Flow (%)
Type of Wax | T = 30 °C Maximum |
T = 37 °C Maximum |
T = 40 °C Minimum |
T = 40 °C Maximum |
T = 45 °C Minimum |
T = 45 °C Maximum |
I | — | 1 | — | 20 | 70 | 90 |
II | 1 | — | 50 | — | 70 | 90 |
Thermal Properties of Dental Waxes
Another thermal characteristic of inlay waxes is their high coefficient of thermal expansion. As shown in Figure 10-2, the wax may expand as much as 0.7% with an increase in temperature of 20 °C or contract as much as 0.35% when it is cooled from 37 °C to 25 °C. The average linear thermal expansion coefficient over this temperature range is 350 × 10−6/K, with values ranging from 217 to 512 × 10−6/K.
The thermal dimensional change may be affected by the previous treatment of the wax. Curve A in Figure 10-2 represents the thermal expansion of inlay wax as a function of temperature. The expansion rate increases abruptly above approximately 35 °C. The temperature at which a change in rate occurs is known as the glass transition temperature. Some constituents of the wax probably change in their crystalline form at this temperature, and the wax is more plastic at higher temperatures. Not all waxes exhibit transition temperatures. The transition point shown in Figure 10-2 appears to be characteristic of an inlay wax with a high paraffin wax content. If the wax is allowed to cool without being placed under pressure, the transition temperature region is not as pronounced when it is reheated, nor is there much change in the thermal expansion coefficient, as shown in curve B of Figure 10-2.
Manipulation of Inlay Wax
To fabricate indirect patterns, the die should be lubricated, preferably with a lubricant containing a wetting agent. Any excess must be avoided because it will prevent intimate adaptation to the die. The melted wax may be added in layers with a spatula or a waxing instrument. The prepared cavity should be overfilled, and the wax then carved to the proper contour. When the margins are being carved, care should be taken to avoid abrading any surface of the stone die. A silk or other fine cloth may be used for a final polishing of the pattern, rubbing toward the margins. Theoretically, applying pressure is undesirable, as shown by change in shape of the the stick of wax in Figure 10-3. However, some clinicians prefer to apply finger pressure as the wax is cooling to help fill the cavity and prevent distortion during cooling. The fingers also accelerate the cooling rate. Although temperature changes should be avoided, some technicians prefer to repeatedly remelt small areas along the margins and examine them under a low-power microscope. Regardless of the method chosen, the most practical method for avoiding any possible delayed distortion is to invest the pattern immediately after removal from the mouth or die, as noted earlier. Once the investment hardens (sets), no distortion of the pattern will occur.
Wax Distortion
Like other thermoplastics, waxes tend to return partially to their original shape after manipulation. This is known as elastic memory. To demonstrate this effect, a stick of inlay wax can be softened over a Bunsen burner, bent into a horseshoe shape, and chilled in this position. If it is then floated in room-temperature water for a number of hours, the horseshoe will open, as shown in Figure 10-3, A and B. This is more critical for inlay waxes than for other impression materials because the metal or hot-pressed ceramic restorations made from the wax must fit onto unyielding hard tooth tissue.
The elastic memory of waxes is further illustrated during measurement of the thermal expansion of a wax held under pressure during cooling. The expansion increases above the glass transition temperature more than when it is cooled without pressure, as shown in curve B of Figure 10-2. Again, this illustrates the tendency of wax to return to its normal undisturbed state. In recalling Figure 10-3, A, when the wax is bent into a horseshoe, the inner molecules are under compression and the outer ones are in tension. Once the stresses are gradually relieved at room temperature, the wax tends to recover its elastic strain.
The components of a casting ring with a wax pattern surrounded by casting investment are shown in Figure 10-4. A sprued wax pattern is shown in the center of the investment ring. Examples of properly sprued wax patterns for a single crown and for a three-unit bridge are shown in Figure 10-5. Note the spherical reservoir that is attached to the single crown pattern. The purpose of the reservoir is to maintain a molten pool of metal to ensure complete filling of the crown area of the mold cavity. For the bridge pattern on the right side of Figure 10-5, a runner bar is used as a reservoir. Additional details are presented later in this chapter.
Specialty Waxes
A pattern made of hard wax is less sensitive to temperature conditions than one made of soft wax. The exothermic heat generated during the setting of an investment affects the pattern selectively. A soft wax pattern may result in a slightly larger and relatively rougher casting than a hard wax pattern. This tendency of softer inlay waxes to expand during setting in a hygroscopic bath at 37.8 °C (100 °F) may contribute to the phenomenon of hygroscopic expansion, described further in Chapter 9.
Gypsum-Bonded Investment
The mold cavity is produced by eliminating a wax or resin pattern by heating the mold to a specific temperature and for a specific time. This is called the burnout process. To provide a pathway to the mold cavity for molten metal, the wax or resin pattern must have one or more cylindrical wax segments attached at the desired point(s) of metal entry; this arrangement is termed a sprued wax pattern. A sprue is the channel in a refractory investment mold through which molten metal flows. After the wax pattern has been made, either directly on a prepared tooth or on a replica die of the tooth, a sprue former base is attached to the sprued wax pattern, an investment ring is pressed into the sprue former base, and an investment slurry is vibrated into the ring to embed the wax pattern in the investment. Examples of sprued wax patterns on a sprue former base are shown in Figure 10-5. The investment material is mixed in the same manner as plaster or dental stone, poured around the pattern, and allowed to set. After the investment hardens, the sprue-former base is removed. The molten metal is then forced through the sprue or ingate created by the sprue former base into the mold cavity left by the wax.
The remainder of this chapter deals with refractory investments and casting methods used for the fabrication of small dental crown and bridge prostheses either by casting metal or by hot-pressing ceramic. Generally two types of investments—gypsum-bonded and phosphate-bonded—are employed, depending on the melting range of the alloy to be cast. The gypsum-based materials represent the type traditionally used for conventional casting of gold alloy inlays, onlays, crowns, and larger fixed dental prostheses (FDPs). Phosphate-based investments are designed primarily for alloys used to produce copings or frameworks for metal-ceramic prostheses (Chapter 18) and some base metal alloys. It can also be used for pressable ceramics. A third type is the ethyl silicate–bonded investment, which is used principally for the casting of removable partial dentures made from base metals (cobalt-based and nickel-based alloys). Commercially pure titanium and titanium alloys require a special investment as well as a controlled atmosphere to achieve satisfactory castings.
Gypsum-Bonded Investments
The thermal expansion curves for the three common forms of gypsum products are shown in Figure 10-6. All forms shrink considerably after dehydration between 200 °C and 400 °C. A slight expansion takes place between 400 °C and approximately 700 °C, and a large contraction then occurs. This latter shrinkage is most likely caused by decomposition and the release of sulfur dioxide. This decomposition not only causes shrinkage but also contaminates the castings with the sulfides of the nonnoble alloying elements, such as silver and copper. Thus, it is imperative that gypsum investments not be heated above 700 °C. However, for gypsum products containing carbon, the maximum temperature is 650 °C. In this way proper fit and uncontaminated alloys are obtained.
Silica
The wax pattern is usually eliminated from the mold by heat. During heating, the investment is expected to expand thermally to compensate partially or totally for the casting shrinkage of the solidifying alloy. As shown in Figure 10-5, gypsum shrinks considerably when it is heated. If the proper forms of silica are employed in the investment, this contraction during heating can be eliminated and changed to an expansion. Silica exists in at least four allotropic forms: quartz, tridymite, cristobalite, and fused quartz. Quartz and cristobalite forms are of particular dental interest.
The density decreases as the α form changes to the β form, with a resulting increase in volume that occurs by a rapid increase in the linear expansion as indicated in Figure 10-7. Consequently, the shrinkage of gypsum shown in Figure 10-6 can be counterbalanced by the inclusion of one or more of the crystalline silicas. Fused quartz is amorphous and glasslike in character, and it exhibits no inversion at any temperature below its fusion point. It has an extremely low linear coefficient of thermal expansion and is of little use in dental investments. Quartz, cristobalite, or a combination of the two forms may be used in a dental investment. Both are available in the pure form. Tridymite is no longer an expected impurity in cristobalite. On the basis of the type of silica principally employed, dental investments are often classified as quartz or cristobalite investments.
Modifiers
Unlike the dental stones, a setting expansion is usually desirable to assist in compensating for the contraction of the alloy. Some of the added modifiers—such as alkali-earth and transition-metal chlorides, boric acid, and sodium chloride—not only regulate the setting expansion and the setting time but also prevent most of the shrinkage of gypsum when it is heated above 300 °C. In some instances, the modifiers are needed to regulate the setting time and setting expansion, as described for the dental stones. The microstructure of a set gypsum-bonded investment can be seen in Figure 10-8.
Hygroscopic Setting Expansion
Hygroscopic setting expansion was first discovered in connection with an investigation of the dimensional changes of a dental investment during setting. As illustrated in Figure 10-9, the hygroscopic setting expansion may be six or more times greater than the normal setting expansion of a dental investment. In fact, it may be as high as 5 linear percent. The hygroscopic setting expansion is one of the methods for expanding the casting mold to compensate for the casting shrinkage of gold alloys.
Variables That Affect Hygroscopic Expansion
The effects of some of the factors previously discussed (W/P ratio, mixing, and shelf life) on the maximal hygroscopic setting expansion are illustrated in Figure 10-9 relative to the amount of water added. As shown in Figure 10-9, the magnitude of the hygroscopic setting expansion below the maximal expansion value is dependent only on the amount of water added and independent of the W/P ratio, the amount of mixing, and the age or shelf life of the investment. This finding is the basis for the mold expansion technique.
Thermal Expansion of Gypsum-Bonded Investments
To achieve sufficient expansion of gypsum-bonded investment, the silica must be increased to counterbalance the contraction of the gypsum during heating. However, when the quartz content of the investment is increased to 60%, with the balance being the calcium sulfate hemihydrate binder, the initial contraction of the gypsum is not eliminated. The contraction of the gypsum is entirely balanced when the quartz content is increased to 75% (Figure 10-10). If a sufficient amount of setting expansion had been present, a casting made at 700 °C would probably have fit the die reasonably well. The thermal expansion curves of quartz investments are influenced by the particle size of the quartz, the type of gypsum binder, and the resultant W/P ratio necessary to provide a workable mix.
The effect of cristobalite compared with that of quartz is demonstrated in Figure 10-11. Because of the much greater expansion that occurs during the inversion of cristobalite, the normal contraction of the gypsum during heating is readily eliminated. Furthermore, the expansion occurs at a lower temperature because of the lower inversion temperature of the cristobalite in comparison with that of quartz. A reasonably good fit of the castings is obtained when a gold alloy is cast into the mold at temperatures of 500 °C and higher. The thermal expansion curves of an investment provide some idea of the form of the silica that is present. As can be seen from Figures 10-11 and 10-12, the investments containing cristobalite expand earlier and to a greater extent than those containing quartz. Some of the modern investments are likely to contain both quartz and cristobalite.
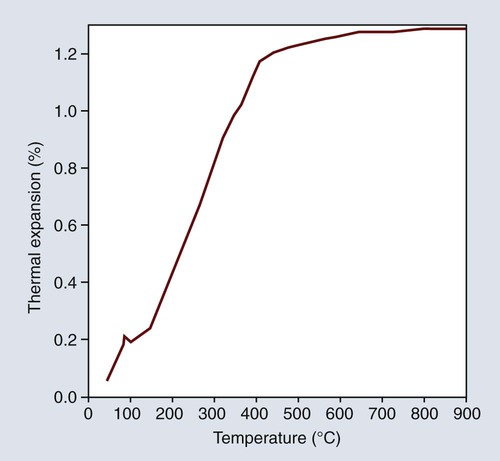
The magnitude of thermal expansion is related to the amount of solids present. Therefore, it is apparent that the more water used in mixing the investment, the less is the thermal expansion that is produced during subsequent heating. This effect is demonstrated by the curves shown in Figure 10-13. Although the variations in the W/P ratios shown are rather extreme, the curves indicate that it is imperative to measure the water and powder accurately if the proper compensation is to be achieved.
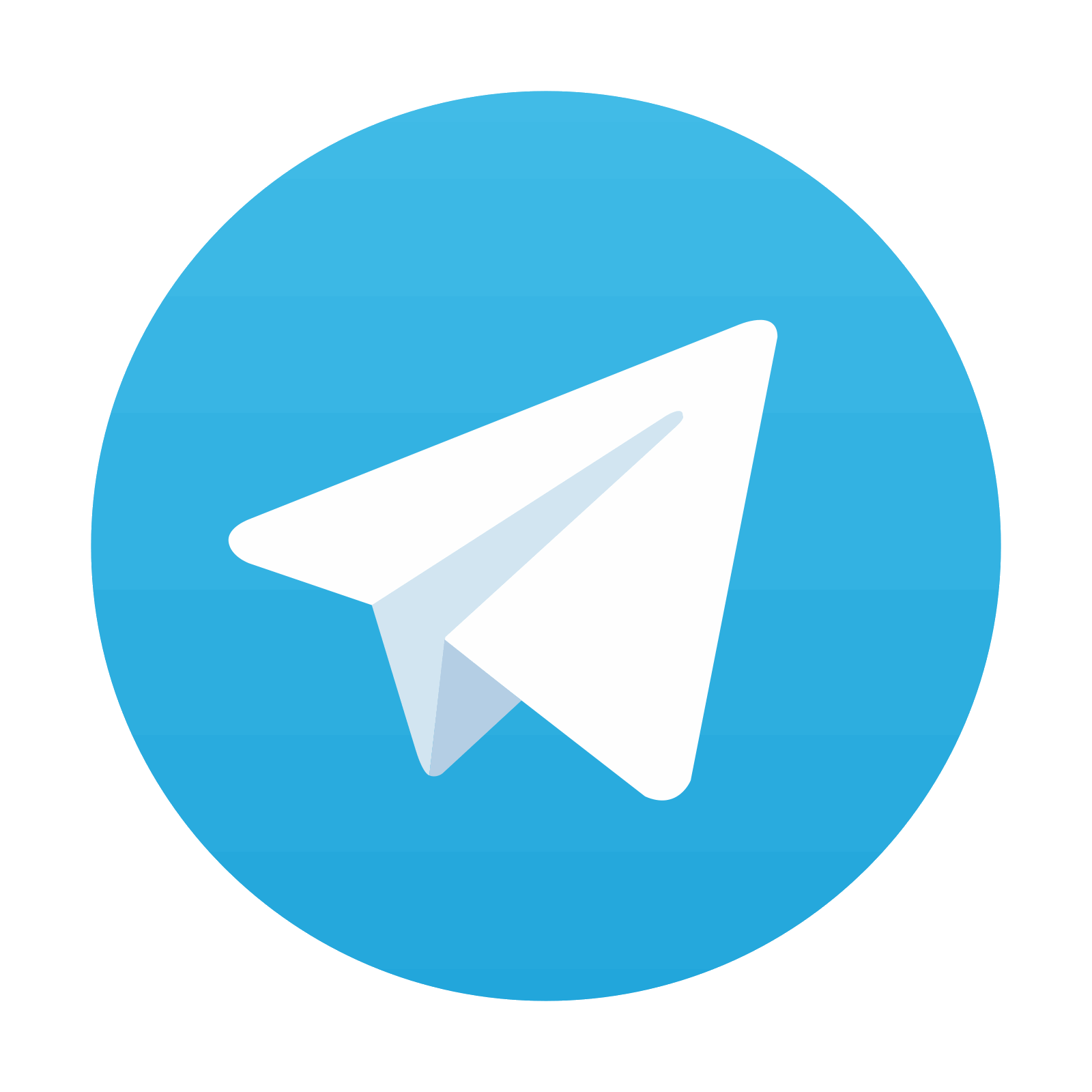
Stay updated, free dental videos. Join our Telegram channel

VIDEdental - Online dental courses
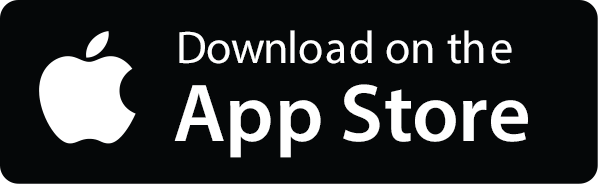
