Dental Polymers
Key Terms
Backbone—The main chain of a polymer.
Block copolymer—Polymer made of two or more monomer species and identical monomer units (“mers”) occurring in relatively long sequences along the main polymer chain. See also random copolymer and graft or branched copolymer.
Chain transfer—Stage of polymerization in which the free radical on the growing end of one polymer chain is transferred to either a monomer or a second polymer chain. This terminates chain growth in the first chain and initiates chain growth in the monomer or second polymer chain (see also Figures 6-10 and 6-11).
Curing—Chemical reaction in which low-molecular-weight monomers (or small polymers) are converted into higher-molecular-weight materials to attain desired properties (see also the closely related terms polymerization and setting).
Crosslink—A difunctional or multifunctional monomer that forms a link between two polymer chains. Crosslinked polymers have many such crosslinks between neighboring chains such that a three-dimensional interconnected polymer network results. See Figures 6-2 and 6-3.
Denture base—The part of the denture that rests on the soft tissues overlying the maxillary and mandibular jawbone and that anchors the artificial teeth.
Elastic recovery—Reduction or elimination of elastic strain (deformation per unit length) when an applied force is removed; elastic solids recover elastic strain immediately on removal of the applied force, whereas viscoelastic materials recover elastic strain over time. The greater the viscous nature of an elastomer, the more incomplete the recovery.
Final set—Stage at which the curing process is complete.
Free radical—An atom or group of atoms (R) with an unpaired electron (•). R•-producing reactions that initiate and propagate polymerization and eventually lead to a final set.
Glass transition temperature (Tg)—The temperature at which macromolecule molecular motion begins to force the polymer chains apart. Thus, polymeric materials soften when heated above this temperature.
Graft or branched copolymer—Polymer in which a sequence of one type of mer unit is attached as a graft (branched) onto the backbone of a second type of mer unit.
Initial set (of a polymer)—The stage of polymerization during which the polymer retains its shape.
Induction—Activation of free radicals, which in turn initiates growing polymer chains.
Macromolecule—A large high-molecular-weight compound usually consisting of repeating units in a chainlike configuration (see also polymer).
Mer—The term used to designate the repeating unit or units in a polymer chain; thus, mers are the “links” in the chain.
Methacrylate polymers—Type of macromolecule derived from monomers with the chemical structure CH2C(CH3)
COOR.
Monomer—Chemical compound that is capable of reacting to form a polymer.
Plastic flow (of a polymer)—Irreversible deformation that occurs when polymer chains slide over one another and become relocated within the material.
Polymer—Chemical compound consisting of a large organic molecule (“macromolecule”) formed by the union of many smaller repeating units (mers).
Polymerization—Chemical reaction in which monomers of a low molecular weight are converted into chains of polymers with a high molecular weight.
< ?xml:namespace prefix = "mml" />

PMMA and MMA—Poly(methylmethacrylate), a commonly used acrylic thermoplastic dental material derived by polymerization of the monomer, methylmethacrylate (MMA).
Propagation—Stage of polymerization during which polymer chains continue to grow to high molecular weights.
Random copolymer—Polymer made of two or more monomer species but with no sequential order between the mer units along the polymer chain. See also block copolymer and graft or branched copolymer.
Resin or synthetic resin—Blend of monomers and/or macromolecules with other components, which form a material with a set of useful properties.
Resin-based composite—A highly crosslinked resin reinforced by a dispersion of amorphous silica, glass, crystalline, or organic resin filler particles and/or fibers bonded to the polymer matrix by a coupling agent.
Setting (of a polymer)—Extent to which polymerization has progressed.
Thermoplastic polymer—Macromolecule material made of linear and/or branched chains that softens when heated above the glass-transition temperature (Tg), at which molecular motion begins to force the chains apart and soften the polymer. Thermoplastics can be heated above the Tg, molded to a new shape, and then cooled below the Tg to retain the new configuration.
Thermosetting polymer—Polymeric material that becomes permanently hard when heated above the temperature at which polymerization occurs and that does not soften again on reheating to the same temperature.
Termination—Stage of polymerization during which polymer chains no longer grow.
Viscoelastic—Term describing a polymer that combines the spring-like behavior of an elastic solid (such as a rubber band) with that of the puttylike behavior of a viscous, flowable fluid (such as honey).
History of Dental Polymeric Materials
The modern era’s use of dental polymers began with natural rubber for dentures. Vulcanized rubber, a plant-derived latex crosslinked with sulfur, was introduced as a denture base material in 1853. At about the same time, celluloid, a nitrocellulose material used to make billiard balls and detachable shirt collars, was adapted as a denture base material. Both materials offered advantages over the wood, bone, ivory, and ceramics used at the time, but each also had substantial drawbacks. An early advance was a combination of the two materials as a “composite” structure (see Chapter 13) in order to gain a better balance among the advantages and drawbacks of each material. Vulcanized rubber was used as the denture base and celluloid formed the gingival area around porcelain teeth. This denture was flexible, allowed easy fabrication of denture bases, and simulated the look of gingival tissue. Unfortunately the celluloid portion absorbed stains, gradually became grossly discolored, developed odors, and was flammable. Thus, substantial improvements in both appearance and functional durability were still needed.
During the 1890s, gutta-percha, a plant exudate containing trans-polyisoprene, came into use for temporary crowns and cavity fillings, permanent restorations, and root canal (endodontic) filling materials. Interestingly, gutta-percha, which is closely related to natural latex rubber (cis-polyisoprene), remains in wide use as an endodontic material to this day. Gutta-percha is a thermoplastic polymer. Vulcanized latex is an elastomeric polymer, which is now used in dentistry in examination gloves and rubber dams. During the 20th century a wide variety of synthetic elastomers—polysulfides, silicone rubber, polyethers, and polyvinylsiloxanes—were developed, some of which were adapted for use as dental impression materials (Chapter 8). At about the same time, during the 1930s and 1940s, phenol-formaldehyde, polystyrene, polyvinylchloride (PVC), vinyl acetate, and other synthetic polymers were developed. Many were evaluated as denture materials but with limited success until the introduction in 1936 of polymethylmethacrylate (PMMA), as a heat-processed thermosetting material. By 1940, PMMA was also being used to make inlays, crowns, and fixed dental prostheses. Beginning in the mid 1940s, room-temperature polymerizing methacrylates became available that were quickly adapted for dentistry as self-curing prosthetic and restorative resins (also known as cold- and chemical-curing resins). Low-temperature curing has made possible directly placed esthetic restorative materials. Sevriton (LD Caulk Inc., Milford, DE), introduced in the 1950s, was the first such tooth-colored resin for anterior teeth. It was composed of methylmethacrylate (MMA) monomer blended with powdered PMMA.
Methylmethacrylate/PMMA resins were soon replaced by the more durable difunctional methacrylate monomers based on either bis-GMA (bisphenol-A glycidylmethacrylate, see Figure 6-16) or urethane dimethacrylate (see Figure 6-17). These innovations were pioneered by Dr. Ray Bowen of the ADA Research Foundation, who introduced self-curing dimethacrylates reinforced by a dispersed phase ceramic particle “filler” in the late 1950s. Such resin-based “composites” form a highly crosslinked, durable, and esthetically pleasing polymer network (Chapter 13).
Self-curable resins were later replaced by ultraviolet photocured materials, which were in turn replaced by blue-light photo-polymerizable resins. These latter “light-curable” resin materials remain in use today, although they have evolved through many innovations in the initiator, reinforcing filler, and monomer components. In the past few years, new resins have been introduced that utilize highly esthetic nanometer-sized reinforcing particles. Most recently, a new monomer system based on a ring-opening polymerization mechanism has been introduced to reduce the problems associated with curing shrinkage (Chapter 13).
The dimethacrylate resins have had an enormous impact on dentistry; they are now used to seal fissures against cariogenic bacteria, as adhesives for both enamel and dentin bonding (Chapter 12), as luting and adhesive cements (Chapter 14), as veneering materials, and as direct and indirect restoratives (Chapter 13). Because the field is dynamic, and new types of polymeric materials are continually being developed, a dentist’s knowledge must include basic concepts of polymer materials science to critically evaluate new developments in the field and to make informed choices on the uses of new dental products. This chapter provides a brief review of the fundamentals of polymer materials for this purpose.
Dental Uses of Polymeric Materials and Resins
• Prosthodontics: denture bases and teeth, soft liners, custom trays, impression materials, core buildup materials, temporary restoratives, cementing/luting materials, and maxillofacial prostheses
• Operative Dentistry: dentin bonding agents, cavity fillings, resin and glass-ionomer cements, pit and fissure sealants, splinting materials, and veneers
• Orthodontics: brackets, bracket bonding resins and cements, and spacers
• Endodontics: gutta-percha points, root canal sealants, and rubber dams
• Equipment: mixing bowls and spatulas, mouth guards (sports equipment), and protective eyewear
Components and Composition
Fundamental Nature of Polymers
The two most significant features of polymers are that they consist of very large macromolecules and that their chainlike molecular structure is capable of virtually limitless configurations and conformations. Chain length, the extent of chain branching and crosslinking, and the organization of the chains among themselves, determine the properties of polymers as illustrated in Figures 6-1 and 6-2 and as explained below. Polymerization is a repetitive intermolecular chain growth reaction that can proceed almost indefinitely, sometimes reaching molecular weights as high as 50 million.
Chain Length and Molecular Weight
The longer the polymer chain, the greater are the numbers of entanglements (temporary connections) that can form along it. Therefore, the longer the chain, the more difficult it is to distort the polymeric material; thus, such properties as rigidity, strength, and melting temperature increase with increasing chain length (Figure 6-1). Consider the analogy between the behavior of a group of polymer molecular chains and a plate of spaghetti. The longer the strands or chains, the more difficult it is to separate (disentangle) them. Cutting them up—that is, reducing the chain length—makes them easier to separate.
Chain Branching and Crosslinking
In addition to linear macromolecules, polymer chains are often connected together to form a nonlinear, branched, or crosslinked polymer (Figures 6-1 and 6-2). Branching is analogous to extra arms growing out of a polymer chain; thus, the probability of entangled, physical connections among chains increases. Various consequences of chain branching are discussed later in this chapter (e.g., in the section below on internal plasticizers). While the entangled interchain connections formed by chain branches are temporary in the sense that they can be disentangled with relatively low-energy, crosslinks that are chemical bond connections between chains and require a relatively high energy to break. Because of interlinking a large number of chain backbones, a highly crosslinked polymeric material can consist of just a few giant molecules or even a single giant molecule.
In crosslinked polymers, some of the structural units must have at least two sites where reactions can occur. For example, as described in Chapter 8, during curing of polysulfide impression material, linear polymers are joined, or bridged, through reactive side chains to form crosslinked molecular networks (see Figure 8-3 which shows crosslinking of poly(methylmethacrylate) by ethylene glycol dimethacrylate during copolymerization).
Crosslinking forms bridges between chains and dramatically increases molecular weight. Consequently, physical and mechanical properties vary with the composition and extent of crosslinking for a given polymer system. The three-dimensional network of crosslinked polymers increases rigidity and resistance to solvents. Crosslinking of a low-molecular-weight polymer increases the softening temperature, known as the glass-transition temperature (Tg), compared with that of a high-molecular-weight polymer (see Figure 6-1). On the other hand, crosslinking has only a modest influence on strength.
Copolymer Structures
• Random copolymer—No sequential order exists among the two or more mer units along the polymer chain.

• Block copolymer—Identical monomer units occur in relatively long sequences (blocks) along the main polymer chain.

• Graft or branched copolymer—Sequences of one type of mer unit (B) are “grafted” onto a backbone chain of a second (A) type of mer unit to form a branched configuration (see Figure 6-2).
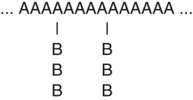
Molecular Organization
In some polymers the chains are randomly coiled and entangled in a very disordered or random pattern known as an amorphous structure (Figure 6-4, left side). In others, the chains align themselves to form a highly ordered, or crystalline, structure (Figure 6-4, right side). Most polymeric materials combine these two forms of organization in greater or lesser proportions. Characteristically, the linear dental polymers are predominantly amorphous with little or no crystallinity. The polymer chains form a tangled mass, comparable with cooked spaghetti, in which each string is a mile or so long. Such polymer segments have little chance to migrate and are immobile in the solid state. As in the case of glass, a short-range order results.
However, many polymers have regions of long-range ordering that produce a degree of crystallinity depending on the secondary bonds that can be formed, the structure of the polymer chain, the degree of ordering, and the molecular weight (Figure 6-4). Polymer crystallinity usually increases strength, rigidity, hardness, and melting temperature, but at the price of reduced ductility—that is, increased brittleness.
Factors that reduce or prevent crystallinity include the following:
• Copolymer formation, which inhibits polymer chain alignment
• Polymer-chain branching, which also interferes with chain alignment
• Random arrangement of substituent groups, particularly large side groups that keep polymer chains separated
• Plasticizers, which tend to separate the chains (see Solvation Properties, below)
Performance Criteria for Dental Resins
Biological Compatibility
Polymers and resins should be tasteless, odorless, nontoxic, nonirritating, and otherwise not harmful to the oral tissues. To fulfill these requirements, a resin should be completely insoluble in saliva or in any other fluids taken into the mouth, Tg and it should be impermeable to oral fluids to the extent that the resin does not become unsanitary or disagreeable in taste or odor. If the resin is used as a filling or cementing material, it should set fairly rapidly and bond to tooth structure to prevent microbial ingrowth along the tooth-restoration interface. A more comprehensive overview of the biocompatibility of dental materials is presented in Chapter 7.
Mechanical and Physical Properties of Polymers
As illustrated in Figure 6-1, the combination of polymer composition, chain length, branching, crosslinking, and molecular orientation can produce a variety of properties. To meet the needs of various dental applications, these features are manipulated to produce a balance that approaches the ideal performance properties as closely as practical. These properties can be grouped into four interrelated categories: mechanical, rheological (flow), dissolution, and thermal.
Mechanical Properties—Deformation and Recovery
• Plastic strain is irreversible deformation that cannot be recovered and results in a new, permanent shape as the result of slippage (flow) among polymer chains.
• Elastic strain is reversible deformation and will be quickly and completely recovered when the stress is eliminated, as the result of polymer chains uncoiling and then recoiling.
• Viscoelastic strain is a combination of both elastic and plastic deformation, but only the elastic portion is recovered when the stress is reduced, as described in Chapter 3. Also, recovery is not instantaneous and occurs over time because the elastic recovery process is impeded by the viscous flow resistance among chains. The amount of deformation that is not recovered at the moment the stress is eliminated is known as plastic deformation.
In the absence of crosslinking, only relatively weak inter-polymer-chain bonds (van der Waals and hydrogen bonds) are available to hold the polymer chains together in a solid state. Chain slippage decreases as chain length increases because the bonds between chains, together with chain entanglements, resist dislodgment of the individual chains. At a certain chain length the resistance provided by interchain bonds and entanglements becomes strong enough to exceed the covalent bond strength of the carbon-carbon bonds along the backbone chains. At this critical chain length, an applied force can rupture chains rather than dislodge them and cause one chain to slide past another. This balance between the strength of the interchain bonds and the covalent bonds along the backbone chains explains why the physical and mechanical properties of polymers increase with increased molecular weight up to a certain point. Subsequently, increased molecular weight becomes less important, as shown in Figure 6-1.
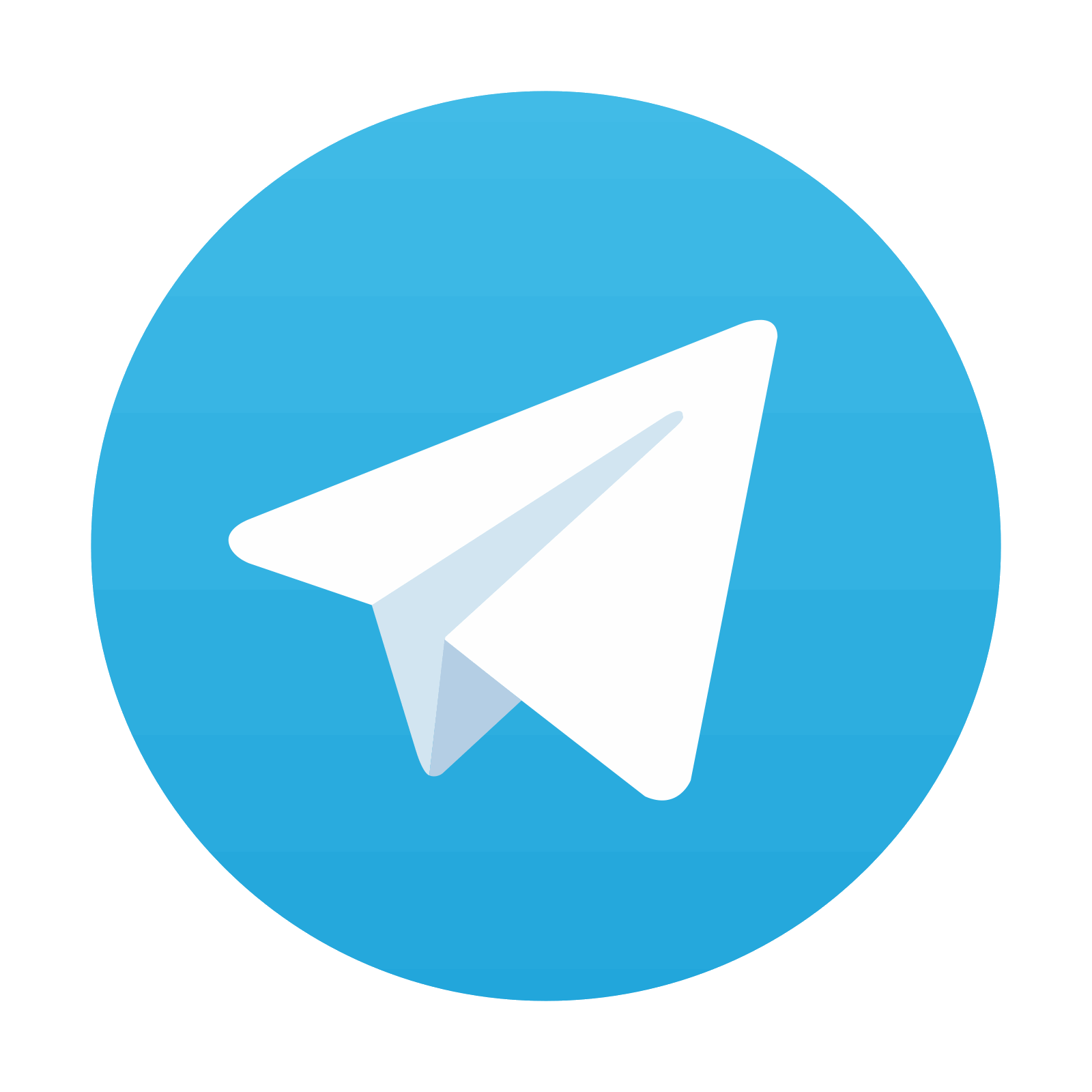
Stay updated, free dental videos. Join our Telegram channel

VIDEdental - Online dental courses
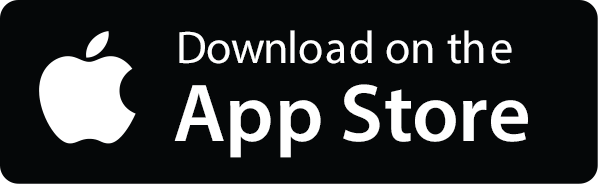
