Introduction
The aim of this research was to compare the load systems produced by rectangular loops and continuous arches for the correction of extruded second molars with a mesial inclination (inconsistent system) and a distal inclination (consistent system).
Methods
The maxillary first molar of an acrylic model of a patient, with passive brackets and tubes bonded, was connected to a 3-dimensional load cell of an orthodontic force tester, and the second molar was replaced by its respective tube bonded to a second load cell. The second molar tube was moved 2.5 mm occlusally and tipped 20° mesially and distally, creating an inconsistent force system and a consistent force system. For each situation, ten 0.017 × 0.025-in beta-titanium, 8 × 10-mm rectangular loops were compared with 10 0.014-in nickel-titanium continuous arches. The vertical forces—F(z)—and tipping moments—M(x)—were compared using 4 t tests, at 5%.
Results
In the inconsistent group, the rectangular loop produced a larger M(x) in both molars: 2.11 N.mm in the second molar compared with the −0.15 N.mm of the continuous arches. On the first molar, the rectangular loops produced −5.58 N.mm against −2.08 N.mm produced by the continuous arches. The F(z) values produced at the second molar with each system were similar, whereas on the first molar they were different; the rectangular loops produced 0.41N, and continuous arches produced 0.53N. In the consistent group, the rectangular loops produced smaller M(x) values at the second molar (−3.06 N.mm) than did the continuous arch (−4.25 N.mm) ( P = 0.01), as well as a smaller F(z) value (−0.52 vs −0.92 N, respectively). At the first molar, the rectangular loops produced smaller M(x) values (−2.32 N.mm) than did the continuous arch (−4.18 N.mm), as well as a smaller F(z) value (0.59 vs 1.10 N).
Conclusions
In the inconsistent group, only the rectangular loop produced a system of force that could correct the second molar. In the consistent system, both group mechanics produced a system of force compatible with the correction of the second molar, but the continuous wire produced larger moments. Both groups showed a tendency for mesial crown tipping of the first molar.
Highlights
- •
A rectangular loop can successfully correct an extruded and crown-mesial tipped second molar.
- •
The load system from a 0.014-in nickel-titanium wire will not correct an extruded and crown-mesial tipped second molar.
- •
Both mechanics can be used to correct an extruded and crown-distal tipped second molar.
Maxillary permanent second molars frequently extrude when their antagonist teeth are lost or damaged, and their correction with continuous arch mechanics may not be adequate depending on the position of the brackets and tubes. When the force system (or load system) produced by a continuous arch is incompatible with the direction of the force or moment required for tooth correction, it is called an inconsistent load system, and a different strategy from the conventional continuous arch is required. Rectangular loops, temporary anchorage devices, or surgery may prove useful for correcting these orthodontic problems when the load system is inconsistent. However, there are situations when the direction of forces and moments produced by a straight wire match the ones desired for correction and are said to produce consistent load systems. In those situations, the correct bonding of the appliance and any leveling wire should be enough to correct the orthodontic problem, at least in theory.
When maxillary permanent second molars extrude, they may tip either crown mesially or crown distally due to their eruption pattern or dental migration. Depending on their position, the load system produced by a continuous arch may be estimated as consistent or inconsistent ( Fig 1 ) according to a well-known orthodontic rationale. Therefore, the most appropriate solution for these 2 problems of mesial or distal tipping with extrusion might not be the same. When a second molar is extruded and tipped crown mesially, a rectangular loop is thought to be a more suitable solution than a continuous arch, which may not be able to produce the load system required for the correction. On the other hand, when an extruded second molar is tipped crown distally and the load system is consistent, a continuous arch may correct the second molar in a simpler manner.

However, these 2 strategies have never been objectively compared to determine whether one would be better than the other for consistent or inconsistent load systems in a specific clinical situation. A reliable way to compare the system of forces required for a clinical situation is with an orthodontic force tester, which is an orthodontic force measurement system composed of 2 three-dimensional load cells that can be adapted to any patient model to investigate different mechanics for the solution of a clinical problem.
Therefore, the aim of this study was to compare the 3-dimensional load system produced by a rectangular loop and a continuous arch in 2 situations of an extruded maxillary permanent second molar, one with mesial-crown tipping and one with distal-crown tipping (inconsistent and consistent systems of forces, respectively), to determine which approach would be the most appropriate for each orthodontic problem.
Material and methods
A maxillary model of a patient was poured in acrylic resin and had 0.018-in MBT prescription brackets and tubes (Opal Orthodontics, Sandy, Utah) passively bonded with epoxy glue (JB Weld, Sulfur Springs, Tex), from second molar to second molar, using a 0.017 × 0.025-in stainless steel wire guide.
The model was secured to an orthodontic force tester custom-made table. One load cell (Multi-axis force/torque Nano17; ATI Industrial Automation, Apex, NC) was attached to the left first molar (later released from the model), and the other one was connected to an articulated device that replaced the left second molar. The articulated device had a second molar tube bonded to it and was placed in the same position as the left second molar, after it was removed from the model ( Fig 2 , A ). The distance between both molar tubes was 7 mm, the same intertube distance before the removal of the second molar ( Fig 2 , B ).

The second molar tube was moved 2.5 mm occlusally from its passive position using a precision rod and a digital dial (Mitutoyo, Aurora, Ill) adapted to the orthodontic force tester. The articulated device allowed the tube to be tipped 20° in mesial and distal directions, enabling data from these 2 angulations to be obtained. Before the data were collected from each situation, tube angulations were assessed by Screen Protractor software (Iconico, New York, NY) using a digital image of the setup. The orthodontic force tester custom software (Department of Mechanical Engineering, Perdue University, Indianapolis, Ind) allowed calibration of the load cells, which transferred the origins of the measurements from the center of the load cell to the center of each tube, regardless of the rotation or position of the load cells. The orientation of the reference grid for measurements was perpendicular (x- and z-axes) and parallel (y-axis) to the tubes.
The extruded second molar tube with a 20° mesial-crown angulation was evaluated first, and the rectangular loop and the continuous arch mechanisms were compared. The load system was considered inconsistent in this group. A scaled digital image allowed the design of a template in the Loop Software (dHAL Orthodontic Software, Athens, Greece) for the bending of ten 8 × 10-mm rectangular passive loops from 0.017 × 0.025-in beta-titanium wires (TMA; Ormco, Glendora, Calif). The loop was designed with its box centralized to the tube of the second molar ( Fig 3 , A ). The passivity of the loops was verified in the physical model using the measurements of forces and moments from the orthodontic force tester software. A second template for the preactivation of the loops was also made in the Loop software as follows. First, the second molar bracket was repositioned virtually in the Loop software to its desired final position: ie, intruded and with its tipping corrected (a 2° overcorrection was needed to ensure a parallel orientation of the wire angle of entry to the first molar tube). The loop was then activated, and the resulting active shape was frozen by an option of the Loop software ( Fig 3 , B ), saved, and printed in real size.

The passive loops were preactivated by bends and were stress relieved by trial activation as many times as needed, until the new preactivated shape matched the printed preactivation template. The center of the box of the loop was marked with a felt-tip pen to allow its position to be centralized with the second molar tube. The loops were inserted into the auxiliary tube of the first molar and into the second molar tube ( Fig 4 ). Each loop was tested only once, and the orthodontic force tester software recorded the vertical forces (Fz) and tipping moments (Mx) of the second and first molars. Also, ten 0.014-in superelastic nickel-titanium wires (Highland Metals, Franklin, Ind) were tied to all brackets and tubes of the model with elastic ligatures (GAC International, Islandia, NY). ( Fig 5 , A and B ) to register the load system produced by continuous arch mechanics. The entire system was inserted into a box made of expanded rigid polystyrene plastic with an external hot-air source controlled by a digital thermometer maintaining the temperature at 37°C ± 1°C.


A second clinical setup was used to compare the same mechanics by altering the 20° of mesial-crown tipping to distal-crown tipping, maintaining the vertical position of the tube. This second situation was assumed to produce a consistent load system. Ten passive rectangular loops in this new tube position were hand-bent with the same protocol as in the inconsistent situation ( Fig 5 , C ) that included the design of 2 new individualized templates (for passive shape and preactivation). The same 10 nickel-titanium wires from the same batch used in the inconsistent situation were side-flipped and similarly tied to all brackets and tubes of the model to collect the F(z) and M(x) values produced by the continuous arch ( Fig 5 , D )
The data collected from the 2 groups were normally distributed and were compared using 4 independent t tests, with a significance level of 5%, to detect differences between the F(z) and M(x) produced by the rectangular loops and continuous arch mechanics for the first and second molars in each situation, inconsistent and consistent.
Results
In the inconsistent simulation, the M(x) values produced were different ( P <0.001). In the second molar tube, the loops produced an M(x) value of 2.11 N.mm, whereas the continuous arch produced −0.15 N.mm ( Table I ). In the first molar tube, the loops produced –5.58 N.mm, and the continuous arch produced −2.08 N.mm. No differences were found for the F(z) produced in the second molars ( P = 0.118), but they were different for the first molars ( P <0.001), where the loops produced 0.41 N against 0.53 N produced by the continuous arch ( Table I ).
Group | Mx (N.mm) | Fz (N) | |
---|---|---|---|
Second molar | Rectangular loop | 2.11 (0.45) | −0.41 (0.11) |
0.014-in nickel-titanium wire | −0.15 (0.06) | −0.35 (0.02) | |
Significance | P <0.001 | P = 0.118 | |
First molar | Rectangular loop | −5.58 (1.34) | 0.41 (0.11) |
0.014-in nickel-titanium wire | −2.08 (0.55) | 0.53 (0.01) | |
Significance | P <0.001 | P = 0.007 |
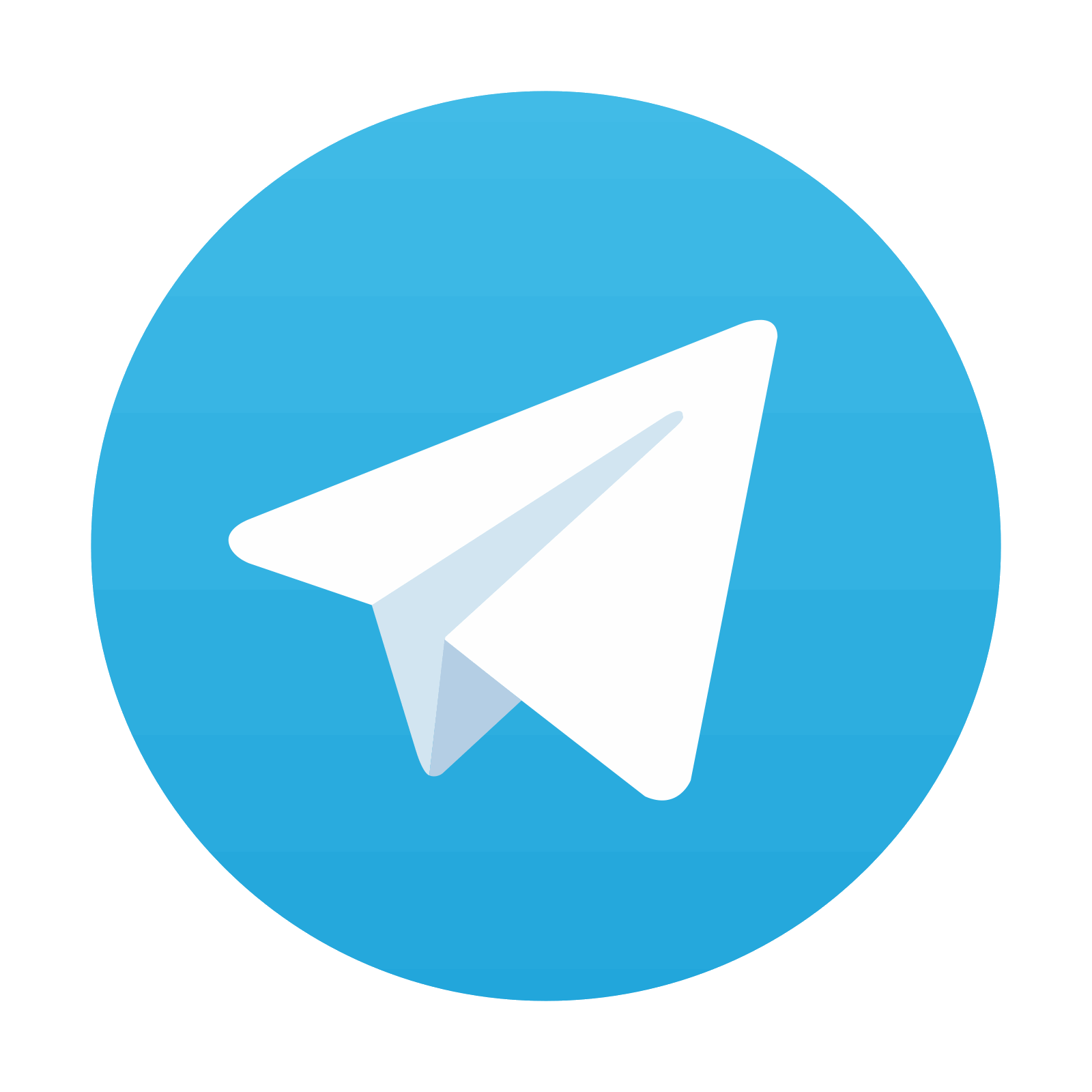
Stay updated, free dental videos. Join our Telegram channel

VIDEdental - Online dental courses
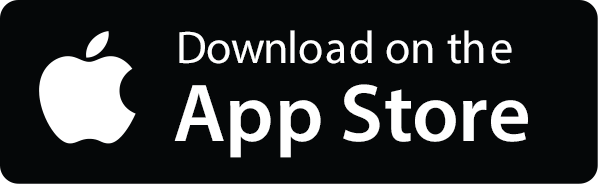

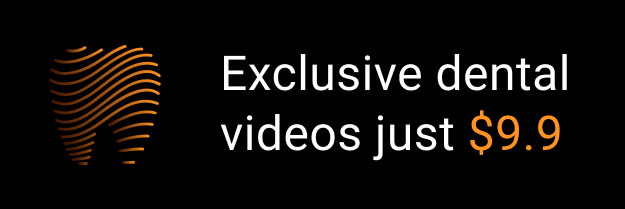