Highlights
- •
Co–Cr alloys were produced from cast, CAD/CAM and powder metallurgy techniques.
- •
Microstructure, crystal structure and chemical composition were analyzed.
- •
Fcc phase stability was dramatically higher for alloys with finer grain sizes.
- •
Cr content at the alloy surface was higher for finer grained alloys.
- •
Phase transformation mechanisms were different between the bulk and interface.
Abstract
Objective
The objective of this study was to identify the different microstructures produced by CC, PM and as-cast techniques for Co–Cr alloys and their phase stability following porcelain firings.
Methods
Three bi-layer porcelain veneered Co–Cr specimens and one monolithic Co–Cr specimen of each alloy group [cast, powder metallurgy (PM), CAD/CAM (CC)] were manufactured and analyzed using electron backscatter diffraction (EBSD), energy dispersive spectrometry (EDS) and X-ray diffraction (XRD). Specimens were treated to incremental numbers of porcelain firings (control 0, 5, 15) with crystallographic data, grain size and chemical composition subsequently obtained and analyzed.
Results
EBSD datasets of the cast alloy indicated large grains >200 μm whereas PM and CC alloy consisted of mean arithmetic grain sizes of 29.6 μm and 19.2 μm respectively. XRD and EBSD results both indicated the highest increase in hcp content (>13 vol%) for cast Co–Cr alloy after treatment with porcelain firing while PM and CC indicated <2 vol% hcp content. A fine grain interfacial layer developed on all surfaces of the alloy after porcelain firing. The depth of this layer increased with porcelain firings for as-cast and PM but no significant increase ( p > .05) was observed in CC. EDS line scans indicated an increase in Cr content at the alloy surface after porcelain firing treatment for all three alloys.
Significance
PM and CC produced alloy had superior fcc phase stability after porcelain firings compared to a traditional cast alloy. It is recommended that PM and CC alloys be used for porcelain-fused-to-metal restorations.
1
Introduction
Cobalt–chromium (Co–Cr) alloys used for fixed dental prosthesis are well established and have shown substantial clinical success over the past few decades. The increasing acceptance of this alloy is justified by its excellent mechanical properties and low production cost compared to high noble alloy predecessors. Continual advancements in technology have also expanded the range of methods by which these restorations can be manufactured. Processing techniques such as computer aided manufacturing (CAM) and powder metallurgy (PM) are just some of the various alternatives that are gaining momentum in dentistry as computer aided designs (CAD) have become more efficient. From a metallurgical properties perspective, one of the major advantages that these new techniques permit over traditional casting methods is the ability to refine the microstructure of the Co–Cr alloy. Although as-cast Co–Cr alloys exhibit exceptional corrosion and wear resistance, they still lack strength and ductility due to their coarse microstructure and solidification defects . Therefore, the ability to produce refined and controlled microstructures allows further enhancement of their mechanical properties.
In terms of chemical composition, there is little difference between Co–Cr alloys used for different manufacturing techniques. Typical Co–Cr alloys contain between 55–63 wt% cobalt and 25–28 wt% chromium with a melting point of >1490 °C . The equilibrium phase diagram for these compositions indicates that >900 °C the anticipated structure is face centered cubic (fcc) and <900 °C it is hexagonal close packed (hcp) . The cast microstructure of Co–Cr alloys is known from previous studies to contain large grains with dendritic-like structures. The dendritic and interdendritic regions form into two phases : fcc and hcp respectively. Although the equilibrium state at room temperature, as given by binary Co–Cr phase diagrams lies within the hcp stable region, under normal cooling conditions, the fcc–hcp transformation is relatively sluggish . Therefore, a majority of the fcc structure is retained in the as-cast state. In addition, the stability of the phases is also dependent on the minor elements included in the alloy. Elements such as Ni, Fe and N are known to increase the stability of the fcc structure while Cr, Mo, and W tend to stabilize the hcp structure. The alternative methods of production on the other hand, do not share the same dendritic structures of cast Co–Cr alloy due to controlled grain refinement. Powder metallurgical (PM) techniques for example are known to produce much finer grain sizes than as-cast materials whereas Co–Cr alloy produced for CAD/CAM (CC) allows further grain refinement through processes such as cold rolling and annealing treatments. These treatments are also known to introduce sigma 3 (1 1 1)〈60°〉 twin boundaries which are common in fcc metals and can act to inhibit slip systems , which affects the overall properties of the alloy. Such refined microstructures have unknown effects especially in regards to the phase stability of the alloy after porcelain firing. The ability to retain the fcc phase allows for enhanced ductility of the alloy which is beneficial to the manipulation of the alloy by practitioners as well as the overall strength of the restoration. Previous investigations on the effect of porcelain firings have mostly focused on the role of oxidation on the bonding between the alloy and porcelain . Other studies have also explored the changes in properties such as hardness, corrosion and wear resistance after porcelain firing treatment. However, to date, the complexities of the phase equilibrium in typical dental base metal alloys such as Co–Cr have not been discussed.
The objective of the present study was to identify and compare the different microstructures produced by CC, PM and as-cast techniques for Co–Cr alloys and their phase stability after conventional porcelain firings. This was investigated using electron backscatter diffraction (EBSD) technique to quantify the individual grain crystallographic structure of large areas. Unfortunately, commercially available dental Co–Cr alloys often have minor composition variations especially when utilizing different processing techniques. Therefore, exact equivalence of the compositions of the alloys for the three processing techniques was not possible. The three alloys investigated were reasonably equivalent with <5 wt% difference in their primary compositions, making them almost ideal for this comparison. The slight difference in minor composition, namely the ∼10 wt% W found in CC and ∼5–6 wt% Mo found in cast and PM, because of their density differences, have proportional influences on the phase stability of the alloy since both elements are hcp stabilizers .
The hypothesis of this research is that the microstructure of the alloy influences the phase stability of the Co–Cr alloy.
2
Materials and method
Bi-layered specimens of cast (LOT:20111115, DentaNEM, Wieland Pforzheim, Germany), powder metallurgy (LOT:1301001, Sintron, Amanngirrbach, Germany) and CAD/CAM (LOT:408699, Remanium Star MD I, Dentaurum, Germany) Co–Cr alloys were produced following manufacturers’ instructions. These specimens were then evaluated using energy dispersive spectrometry (EDS) and EBSD analysis. A leucite-based porcelain (Vita VMK Master, Vita, Germany) was used for the veneering porcelain layer. Specimens for XRD analysis underwent the same sintering process but without porcelain layering.
2.1
Preparation of the substrate material
Rectangular plates (4) 20 mm × 8.0 mm × 1 mm of each Co–Cr alloy were fabricated using different techniques. The cast alloy was manufactured by first embedding pre-cut thermoforming discs (Erkodent, Germany) with a phosphate-bonded investment. The investment was subsequently pre-heated to 950 °C for 1 h and cast using an induction casting machine (Fornax, BEGO, USA) at temperatures above the melting point of this alloy of ∼1490 °C. The investment and cast alloy was then left to air cool to room temperature before subsequent removal. The PM produced alloy was dry sectioned to the required dimension using a low-speed precision cutting machine (DTQ-5, Weiyi, China) in its pre-sintered state and sintered at ∼1300 °C with argon supply (Argotherm, Amanngirrbach, Germany). The CC alloy was cut to dimension using an electrical discharge machine. All specimens were ground with 320 grit SiC (SiC paper, Struers, Denmark) paper to achieve exact dimensions and flat surface finish and in the case of the CC alloy, removed any surface contamination from the electrical discharge cutting process. Finally, the surfaces were impacted with airborne particle abrasion using 110 μm Al 2 O 3 particles at 2 bar pressure. According to the properties provided by the manufacturer, all three Co–Cr alloys have an elastic modulus within the range of 200–230 GPa and a hardness range of ∼2.7–3.2 GPa.
2.2
Preparation of the veneering porcelain
The layering of the veneering porcelain was in accordance to the manufacturers’ recommendation with conventional firing procedures. Specimens were treated to 5 and 15 porcelain-firing cycles in accordance to their specimen group. A detailed summary of the firing and specimen group specifications is listed in Table 1 . The veneering porcelain was layered to a thickness of 1.5 mm with the assistance of prefabricated templates.
Firing Programs | Sintering temperature (°C) | Heating rate (°C/min) | Hold time (min) | Cast, PM, CC Co–Cr alloy | ||
---|---|---|---|---|---|---|
Control | OD5 | OD15 | ||||
Wash Opaque 1 | 960 | 80 | 1 | – | 1 | 1 |
Opaque 2 | 950 | 80 | 1 | – | 1 | 1 |
Dentin 1 | 930 | 55 | 1 | – | 1 | 1 |
Dentin 2 | 920 | 55 | 1 | – | 2 | 12 |
Total firings | – | – | – | 0 | 5 | 15 |
2.3
X-ray diffraction
One specimen of each alloy group was analyzed using XRD to determine the relative amount of hcp phase present in the as-sintered (control) alloys (cast, PM, CC) and after 5 porcelain firings (OD5). No porcelain layering was used on the XRD specimens. Oxides at the alloy surfaces were also evaluated to determine the oxidation potential of the Co–Cr alloys. XRD analyses were scanned between 20° and 80° 2 θ (0.05° step size Cu radiation) (Philips, PANalytical X’Pert Pro MPD system).
2.4
Electron backscatter diffraction and energy dispersive spectrometry
EBSD was used to measure and identify the grain size and crystal structure while EDS was used to determine the chemical composition of the alloy. In the present study, both techniques were used to analyze the Co–Cr core substructure before (control) and after an increasing number of porcelain veneering firings (OD5 and OD15). The plates as described above were sectioned perpendicular to the porcelain surface and sequentially polished to a <0.05 μm colloidal silica finish to eliminate as much surface damage as possible: an essential process for acquiring high quality electron backscatter diffraction patterns. EBSD patterns were collected using an Oxford Instruments AZtec (@25 kV, ∼50.4 nA) in a fixed grid of 450 μm × 220 μm at 0.2–0.5 μm step size. EBSD data were post-processed (HKL CHANNEL 5 software) using methods outlined in Prior et al. and grains were defined as cells surrounded by boundaries with misorientations of 10° or more . Subsequent texture orientation, grain size analysis and phase maps were also produced under the boundary conditions outlined above. A figure marking the areas analyzed is shown in Fig. 1 . Energy dispersive spectrometry (EDS) was also performed (@15 kV ∼300 pA) across the bulk and metal porcelain interface to identify the elemental composition.
2.5
Statistical analysis
Two-tailed t -test with Bonferroni correction was used to verify the statistical significance ( p < .05) between the grain size and depth measurements of the interfacial layer at the alloy surface.
2
Materials and method
Bi-layered specimens of cast (LOT:20111115, DentaNEM, Wieland Pforzheim, Germany), powder metallurgy (LOT:1301001, Sintron, Amanngirrbach, Germany) and CAD/CAM (LOT:408699, Remanium Star MD I, Dentaurum, Germany) Co–Cr alloys were produced following manufacturers’ instructions. These specimens were then evaluated using energy dispersive spectrometry (EDS) and EBSD analysis. A leucite-based porcelain (Vita VMK Master, Vita, Germany) was used for the veneering porcelain layer. Specimens for XRD analysis underwent the same sintering process but without porcelain layering.
2.1
Preparation of the substrate material
Rectangular plates (4) 20 mm × 8.0 mm × 1 mm of each Co–Cr alloy were fabricated using different techniques. The cast alloy was manufactured by first embedding pre-cut thermoforming discs (Erkodent, Germany) with a phosphate-bonded investment. The investment was subsequently pre-heated to 950 °C for 1 h and cast using an induction casting machine (Fornax, BEGO, USA) at temperatures above the melting point of this alloy of ∼1490 °C. The investment and cast alloy was then left to air cool to room temperature before subsequent removal. The PM produced alloy was dry sectioned to the required dimension using a low-speed precision cutting machine (DTQ-5, Weiyi, China) in its pre-sintered state and sintered at ∼1300 °C with argon supply (Argotherm, Amanngirrbach, Germany). The CC alloy was cut to dimension using an electrical discharge machine. All specimens were ground with 320 grit SiC (SiC paper, Struers, Denmark) paper to achieve exact dimensions and flat surface finish and in the case of the CC alloy, removed any surface contamination from the electrical discharge cutting process. Finally, the surfaces were impacted with airborne particle abrasion using 110 μm Al 2 O 3 particles at 2 bar pressure. According to the properties provided by the manufacturer, all three Co–Cr alloys have an elastic modulus within the range of 200–230 GPa and a hardness range of ∼2.7–3.2 GPa.
2.2
Preparation of the veneering porcelain
The layering of the veneering porcelain was in accordance to the manufacturers’ recommendation with conventional firing procedures. Specimens were treated to 5 and 15 porcelain-firing cycles in accordance to their specimen group. A detailed summary of the firing and specimen group specifications is listed in Table 1 . The veneering porcelain was layered to a thickness of 1.5 mm with the assistance of prefabricated templates.
Firing Programs | Sintering temperature (°C) | Heating rate (°C/min) | Hold time (min) | Cast, PM, CC Co–Cr alloy | ||
---|---|---|---|---|---|---|
Control | OD5 | OD15 | ||||
Wash Opaque 1 | 960 | 80 | 1 | – | 1 | 1 |
Opaque 2 | 950 | 80 | 1 | – | 1 | 1 |
Dentin 1 | 930 | 55 | 1 | – | 1 | 1 |
Dentin 2 | 920 | 55 | 1 | – | 2 | 12 |
Total firings | – | – | – | 0 | 5 | 15 |
2.3
X-ray diffraction
One specimen of each alloy group was analyzed using XRD to determine the relative amount of hcp phase present in the as-sintered (control) alloys (cast, PM, CC) and after 5 porcelain firings (OD5). No porcelain layering was used on the XRD specimens. Oxides at the alloy surfaces were also evaluated to determine the oxidation potential of the Co–Cr alloys. XRD analyses were scanned between 20° and 80° 2 θ (0.05° step size Cu radiation) (Philips, PANalytical X’Pert Pro MPD system).
2.4
Electron backscatter diffraction and energy dispersive spectrometry
EBSD was used to measure and identify the grain size and crystal structure while EDS was used to determine the chemical composition of the alloy. In the present study, both techniques were used to analyze the Co–Cr core substructure before (control) and after an increasing number of porcelain veneering firings (OD5 and OD15). The plates as described above were sectioned perpendicular to the porcelain surface and sequentially polished to a <0.05 μm colloidal silica finish to eliminate as much surface damage as possible: an essential process for acquiring high quality electron backscatter diffraction patterns. EBSD patterns were collected using an Oxford Instruments AZtec (@25 kV, ∼50.4 nA) in a fixed grid of 450 μm × 220 μm at 0.2–0.5 μm step size. EBSD data were post-processed (HKL CHANNEL 5 software) using methods outlined in Prior et al. and grains were defined as cells surrounded by boundaries with misorientations of 10° or more . Subsequent texture orientation, grain size analysis and phase maps were also produced under the boundary conditions outlined above. A figure marking the areas analyzed is shown in Fig. 1 . Energy dispersive spectrometry (EDS) was also performed (@15 kV ∼300 pA) across the bulk and metal porcelain interface to identify the elemental composition.
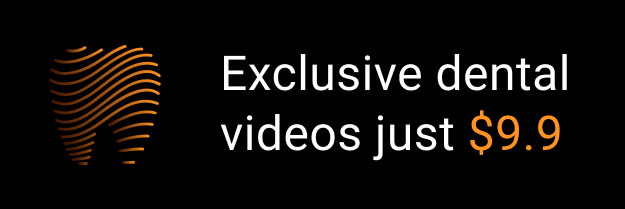