Introduction
Titanium nitride (TiN) plating is a method to prevent metal corrosion and can increase the surface smoothness. The purpose of this study was to evaluate the friction forces between the orthodontic bracket, with or without TiN plating, and stainless steel wire after it was corroded in fluoride-containing solution.
Methods
In total, 540 metal brackets were divided into a control group and a TiN-coated experimental group. The electrochemical corrosion was performed in artificial saliva with 1.23% acidulated phosphate fluoride (APF) as the electrolytes. Static and kinetic friction were measured by an EZ-test machine (Shimadazu, Tokyo, Japan) with a crosshead speed of 10 mm per minute over a 5-mm stretch of stainless steel archwire. The data were analyzed by using unpaired t test and analysis of variance (ANOVA).
Results
Both the control and TiN-coated groups’ corrosion potential was higher with 1.23% APF solution than with artificial solution ( P <0.05). In brackets without corrosion, both the static and kinetic friction force between the control and TiN-coated brackets groups showed a statistically significant difference ( P <0.05). In brackets with corrosion, the control group showed no statistical difference on kinetic or static friction. The TiN-coated brackets showed a statistical difference ( P <0.05) on kinetic and static friction in different solutions.
Conclusion
TiN-coated metal brackets, with corrosion or without corrosion, cannot reduce the frictional force.
Orthodontic tooth movement followed the alveolar bone remodeling theory. Orthodontists are concerned with the friction characteristics of orthodontic brackets. Most orthodontic metal brackets are made of stainless steel. In an oral environment, orthodontic brackets are exposed to potentially damaging physical and chemical agents. These conditions may affect the amount of metal corrosion. The outcome of the corrosion is that metallic ions are released and the metal bracket surface becomes rough.
Physical vapor deposition (PVD)-type ion plating is a surface modification technique capable of coating substrates with various thin-layer films. This procedure is currently being successfully applied to the coating of dental instruments with titanium nitride (TiN), resulting in improved properties for rotary and endodontic cutting instruments. The TiN film demonstrates favorable characteristics with regard to corrosion resistance, wear resistance, and increased hardness. Except anticorrosion effects of TiN plating, the friction effects between the TiN plating bracket and the orthodontic wire is important in orthodontic treatment.
Friction is a function of the dynamic relationship among the archwire, bracket, and ligation type in the oral environment. In vitro studies on bracket and wire friction were affected by the following factors: type of archwire and bracket materials ; their size and shape ; the width and slot dimensions ; the ligature materials ; the type of ligation ; the surface composition, roughness, and cleanliness of the contacting surfaces ; the bracket-to-archwire positioning in a 3-dimensional space ; the interbracket distances ; and saliva or solution, plaque, and the acquired pellicle. There were significant differences in friction noticed between dry and wet test conditions. When human saliva and dry testing were compared, the human saliva sometimes behaved as an adhesive on steel-on-steel couples, but at other times it behaved as a lubricant on nickel titanium archwires on stainless steel brackets.
To prevent tooth decay in orthodontic treatment, fluoride is usually applied. The fluoride level in the oral cavity varies according to the prophylactic treatment. Fluoride is used at concentrations of up to 1% in toothpastes and mouthwashes and about 2% when the aim is to eliminate enamel stains. These substances have a pH range of about 3.5 to 7.0. In fluoride-containing solutions, the friction of orthodontic metal brackets can be affected. Our previous study showed that friction forces in fluoride-containing solutions is higher than that in pH 6.5 artificial solutions.
The TiN-plated metal surface has anticorrosion effects. The purpose of the present study was to evaluate the friction forces between the orthodontic bracket, with or without TiN plating, and stainless steel wire after it was corroded in fluoride-containing solution.
Material and methods
Sample preparation
In total, 540 bracket samples were used in the present study. Each test condition contained 30 brackets ( Fig 1 ). The metal brackets were selected from Tomy OPAK system bracket with a 0.022-in × 0.028-in slot (Tomy Co., L, Tokyo, Japan). The 0.019-in × 0.025-in stainless steel wire (3M Unitek, Monrovia, Calif) was used for the friction test. The ligation between the bracket and the wire was a clear AlastiK module (Quik-Stick Clear, A-1 AlastiK, 3M Unitek [Monrovia, Calif). The bracket and archwire were cleaned with alcohol wipes before the test.
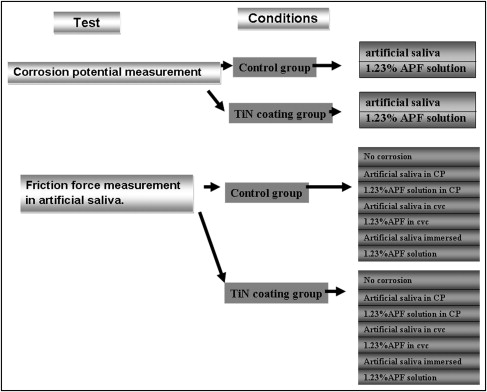
The testing solutions used in the present study were distilled water, artificial saliva (Sinphar Pharmaceutical Co., Ltd, Taipei, Taiwan) ( Table I ), and 1.23% acidified phosphate fluoride (APF) (0.2 mass % NaF + 0.17 mass % H 3 PO 4 , pH 3.5) solution.
Content | Amount (mg) |
---|---|
Sodium chloride | 0.844 |
Potassium chloride | 1.2 |
Calcium chloride anhydrous | 0.146 |
Magnesium chloride 6 H 2 O | 0.052 |
Potassium phosphate dibasic | 0.34 |
Sorbitol solution (70%) | 60 |
Methylparaben | 2 |
Hydroxyethyl cellulose | 3.5 |
Titanium nitride (TiN) ion plating
The TiN plating employed is according to the method previously referred to by Hai et al. The metal brackets were ultrasonically cleaned in both acetone and ethanol baths. Specimens were first placed for 10 minutes in an ion-plating apparatus and were exposed to argon gas plasma created under 400-W radiofrequency (rf) power, 67-megapascal (mPa) argon gas pressure, and –400-V bias voltage. After this and prior to TiN ion coating, a 100-nm primary layer of titanium undercoating was applied to improve the bonding between the substrate and the subsequent TiN film. TiN ion plating was then performed under conditions of 400-W rf power, 13-mPa argon gas pressure, 53-mPa nitrogen gas pressure, and –1-kV bias voltage. The substrate temperature was maintained at approximately 200°C by means of an infrared heat source. The thickness of the TiN film was controlled by changing the ion plating time with the use of a quartz crystal microbalance.
Electrochemical corrosion
The method followed here was that first described by Kuphasuk et al. A mixture of epoxy glue and silver paste was used to attach the back surface of each specimen to a copper wire, which provided electrical contact to the electrochemical corrosion-testing apparatus. Artificial saliva and 1.23% APF solution were chosen for corrosion testing. Electrochemical corrosion studies were conducted at 37°C ± 1°C, and the test system incorporated an atmosphere composed of nitrogen gas in order to simulate the intraoral environment and reduce any potential fluctuation in the oxygen concentration of the electrolyte. The g/AgCl reference electrode, platinum plate as counter electrode, and platinum wire for bracket ligation as the working electrode were prepared. The 3-electrode assembly was connected to CH Instrument Model 600C Series Potentiostat/Galvanostat (CH Instruments, Inc., Austin, Tex). The data was controlled and recorded by computer. Corrosion potential (Ecorr) was measured over a 100-minute period. Voltammetry was performed at a scanning rate of 0.25 mV per second in the anodic direction, with a range of –1000 to 500 mV/saturated calomel electrode.
Friction test
After the corrosion potential was calculated, using the data on the Jiehan 5000 Electrochemical Workstation (Jiehan Co, Taipei, Taiwan) the new sample was allowed to corrode for 23 hours. After sample corrosion, the bracket and wire friction were measured in a wet solution that contained artificial saliva ( Fig 2 ).
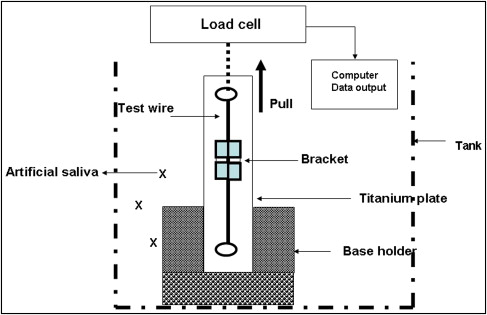
The test procedure was modified from our previous design. Testing was performed on an EZ-test machine (Shimadazu, Tokyo, Japan) with a crosshead speed of 10 mm per minute over a 5-mm stretch of archwire. A plumb line was hung to ensure that the bracket mount was parallel with the vertical line scribed on the steel bar base of the bracket mount assembly. The 5-N load cell was calibrated to between 0 and 5 N, and the archwire was drawn through the bracket as the crosshead moved inferiorly at 10 mm per minute. This crosshead speed was selected because a previous study found no significant difference with crosshead speeds of 0.5 to 50 mm per minute. Care was taken to align the archwire so that the sample was parallel with the vertical framework of the machine. The bracket was pulled vertically by a loop of 0.018-in stainless steel wire, and the force required to initiate and maintain movement of the bracket over the 5-mm test distance was measured. The program was set to highlight the maximum frictional force at initial movement, which was taken to represent the peak static frictional resistance.
Data acquisition and statistical analysis
The load cell registered the force levels needed to move the wire through the bracket, and these values were stored on a computer hard disk. The data were then analyzed using a statistical package (Primer, McGraw Hill, New York, NY,). The corrosion potential was static by an unpaired t test. A completely randomized design (2-way) analysis of variance (ANOVA) was used to test for significant differences among the solutions. The Student-Newman-Keuls multiple comparison of means procedure at P <0.05 was used to determine differences between the groups. An unpaired t test was used to detect the frictional difference between the TiN-coated groups and control groups with P <0.05 accepted as showing a significant statistical difference.
Results
Corrosion potential measurement
The control group and TiN group corrosion potential showed a statistical difference in artificial saliva (–0.05 ± 0.01 vs –0.03 ± 0.01, t = 4.47, P <0.05) and a nonstatistical difference in 1.23% APF solution (–0.25 ± 0.05 vs –0.26 ± 0.08, t = –0.355, P >0.05). Both the control and TiN-coated groups’ corrosion potential was higher with 1.23% APF solution than with artificial solution ( P <0.05) ( Fig 3 ).

Friction force measurement
Bracket without corrosion
The friction force was measured in artificial saliva by a universal testing machine. The static friction force between the control group and the TiN-coated brackets group showed a statistically significant difference ( t = –3.6, P = 0.002 <0.05) ( Fig 4 ) The kinetic friction force between the control and TiN-coated brackets groups showed a statistically significant difference ( t = –3.042, P = 0.007 <0.05) ( Fig 4 ) Both control and TiN-coated groups’ static friction was higher than kinetic friction.
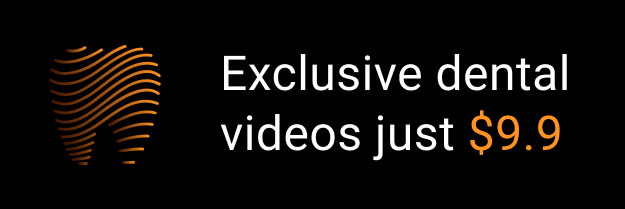