Abstract
The edge chipping resistances of six CAD/CAM dental restoration materials are analyzed and correlated to other mechanical properties. A new quadratic relationship that is based on a phenomenological model is presented.
Objective
The purpose of this study was to further analyze the edge chipping resistance of the brittle materials evaluated in Part 1. One objective was to determine why some force-distance trends were linear and others were nonlinear. A second objective was to account for differences in chipping resistance with indenter type.
Methods
Edge chipping experiments were conducted with different indenters, including some custom-made sharp conical indenters. A new force – distance quadratic expression was correlated to the data and compared to the linear and power law trends.
Results
The new quadratic function was an excellent fit in every instance. It can account for why some materials can be fit by a linear trend, while others can be fit by the power law trend. The effects of indenter type are accounted for variations in crack initiation and by the wedging stresses once an indentation hole is created.
Significance
The new quadratic force – edge distance function can be used with edge chipping data for all brittle materials, not just those evaluated in this study. The data trends vary from linear to nonlinear depending upon the material’s hardness, fracture toughness, and elastic modulus.
1
Introduction
Part 1 showed how the edge chipping test may be used to evaluate CAD/CAM dental restoration materials . The traditional linear analysis that relates the force to create a chip ( F ) to the distance from the edge ( d ) is:
The constant T e is the “edge toughness” which is the slope of a line on a force versus distance plot. Edge toughness varies with indenter type and quantitative values could vary by as little as 10% or as much as a factor of two with indenter for a given material . The edge chipping methodology and Eq. (1) were recently applied to brittle denture tooth materials . Fig. 1 shows contrasts in the chips and indentations in a hard dental ceramic and a soft denture tooth material.

Part 1 showed that a power law relationship often was a better fit to the data:
where A and n are constants. Thouless et al. derived a model based on buckling of an edge flake that predicted n = 3, but their loading geometry was somewhat different than the usual edge chipping procedures with pointed indenters. (The forces in their model and experiments were applied in a distributed fashion parallel to the edge and at a location between the crack and the side surface.) They obtained:
where λ is a constant, E is the elastic modulus, c f is the critical crack length at instability. An indentation fracture mechanics model for edge chipping by Chai and Lawn for edge chip resistance supports the power law Eq. (2) , but only for the case of n = 1.5. Although some of our data in Part 1 and earlier work matched the power law with n = 1.5, much of the data did not. Our exponents ranged from as small as 1 to as large as 2.
As discussed in Part 1, the nonlinearity and the dependence of results on indenter type stem from the multistep chipping process: (a) formation of a small indentation; (b), formation of short stable radial cracks; (c), propagation of some of the radial cracks downward and parallel to the side surface; and (d), unstable crack propagation toward the side surface of one or a pair of cracks causing the chip to pop off. In some of the experiments described in Part 1 , the experiments were interrupted and the specimens examined prior to chip pop-off. There were significant differences in steps (a) and (b) depending upon indenter type. At small forces the relatively blunt Rockwell C indenter created shallow depressions with no cracking. Radial or cone cracks initiated only at larger forces. Vickers or 120° sharp conical indenters initiated cracks at small forces. Thus it is not surprising that the force-distance trends are different and that much greater force was needed to form chips with the Rockwell C indenter. Different amounts of deformation and fracture occur during a test sequence and nonlinear effects should be expected.
Although Part 1 showed that much of the data could be matched by the power law Eq. (2) , problems remained with the interpretation of the exponent n and the constant A . Is n a fundamental material parameter indicative of a material’s chipping behavior? Can it be related to other material properties such as fracture toughness?
Similar questions have arisen in the past about interpretations of power law fits of hardness data for brittle materials. As will be shown below, a simple relationship that has found widespread utility for interpreting hardness data may have an analog for edge chipping. There are some parallels in hardness and edge chip testing. Both involve deformation and fracture. Fracture around an indentation can alter the hardness response of brittle materials and can dramatically change the “indentation size effect (ISE)” whereby hardness varies with force or indentation size.
The hardness, H , of a material is determined by the ratio of an applied load to the contact (or projected) area of an indentation:
where F is the applied load, l is a measure of the indentation size (typically, the diagonal size) and the constant depends on indenter geometry. Hardness usually varies with indentation force. The hardness of ceramics is very high at small indentation forces. Hardness decreases with increasing force and gradually approaches a constant value at large force. Data are sometimes fitted to the Meyer law:
where C is a constant and n is the Meyer or logarithmic index denoting the degree of curvature for the hardness-load relationship. (This n is not the same as the one in Eq. (1) .) If n = 2, hardness is constant and independent of the force. For most ceramics, n < 2, and hardness decreases with increasing force. There is no theoretical basis for applying the Meyer law to brittle materials. Although some (e.g., Sargent and Page ) have designated group of ceramics with comparable values, the exponents ultimately did not provide much insight as to material behavior.
The inadequacy of the Meyer analysis for brittle materials and metals alike led to alternative curve fits to hardness-force or hardness-indentation size data. Bernhardt proposed a function in 1941:
where F is the load, l is the indentation diagonal size, and a 1 and a 2 are constants. Mitsche in 1948 and Bückle in 1954 discussed a similar power series expansion:
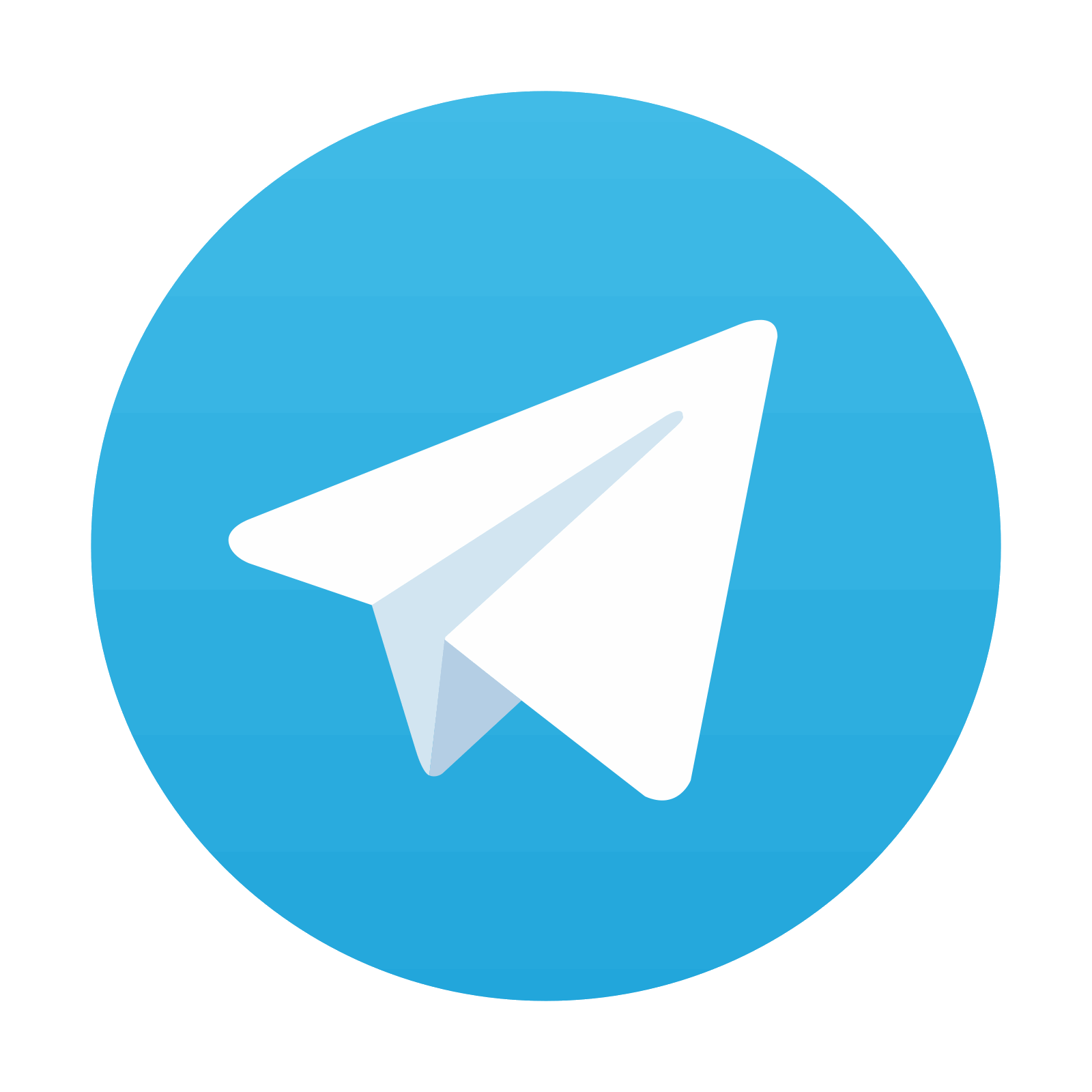
Stay updated, free dental videos. Join our Telegram channel

VIDEdental - Online dental courses
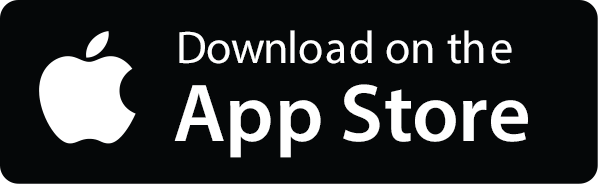
