Abstract
Objectives
The aim of this study was the interfacial characterization and the determination of bond strength of commercially available low fusing dental porcelain for Ti.
Methods
Eight materials were included in this study: Duceratin, Duceratin Plus, Initial Ti, Ti-22, TiKrom, TitanKeramik, Triceram (powder) and Triceram (paste). Eight ISO 9693 bond characterization specimens from each porcelain were prepared according to manufacturers’ instructions. One specimen from each group was embedded in acrylic resin and after metallographic preparation was studied under an SEM. Interfacial characterization was carried out with Backscattered Electron Imaging and X-ray EDS analysis operating in line scan mode. Metal–ceramic specimens were tested in three point bending at a crosshead speed of 1.5 mm/min according to ISO 9693 requirements. Additionally the fracture mode (adhesive–cohesive) of all specimens was evaluated employing SEM/EDS analysis. The results of bond strength and adhesive percentage were statistically analysed with one-way ANOVA and SNK multiple comparison test ( a = 0.05). Additionally the possible correlation between the bond strength and fracture mode was also tested using Pearson test.
Results
Interfacial characterization showed the mutual diffusion of Ti, Si, O and La along the Ti–ceramic interface. Only in Tricerap (paste) Zr showed an increased concentration at the interface. The results of bond strength classified the materials in the following decreasing order: TiKrom > Duceratin > Initial Ti > Duceratin Plus > Ti-22 > Triceram(paste) > Triceram(powder) >TitanKeramik. No correlation ( r = 0.132) between the fracture mode and bond strength of the selected material denoting that the fracture mode is irrelevant with the bond strength of Ti–ceramic joint and thus the former should not be applied for comparison among different materials.
Significance
According to the results of this study the materials tested provided great difference in interfacial analysis and bond strength with metallic Ti.
1
Introduction
During recent decades, commercially pure titanium (cp Ti) has been used in dentistry for metal–ceramic restorations because of its excellent biocompatibility, good corrosion resistance, and adequate mechanical properties .
Strong bonding of porcelain to cp Ti is critical for the longevity of metal–ceramic restorations . Contrary to conventional alloys, Ti is rapidly oxidized during porcelain firing at temperatures above 800 °C providing a thick and non-adherent layer of Ti oxide , that compromises the metal–ceramic bond strength compared to conventional dental alloys increasing the risk of failure . Various surface treatments have been introduced to overcome this limitation such as surface roughening , preoxidation , etching , and the application of bonding coatings . However, only the roughening of metallic surface prior to porcelain application has been adopted as a standard operating procedure .
Although extensive research has been done for the evaluation of metal–ceramic bond strength of low fusing porcelains to cp Ti in most cases the results are not directly comparable due to the great differences in the research protocols employed. In the relevant literature more than fifteen different metal–ceramic bond strength tests have been used and the results have been reported in three different ways including debonding load (Nt) , bond strength in MPa and fracture mode as percentage of cohesive and adhesive failures. The most recent specification on assessment of metal–ceramic bonding of the International Standardization Organization ISO 9693 provides a sound method for the standardized evaluation of bond strength of metal–ceramic systems and meets the criteria for a comparative evaluation of metal–ceramic bond strength, independently from the mechanical properties of alloys tested.
The aim of the present study was to evaluate the compliance of eight commercially available dental porcelains for veneering cp Ti with ISO 9693:1999 specification and to characterize the morphology and elemental composition of the metal–ceramic interfaces.
2
Materials and methods
2.1
Specimens preparation
Seventy rectangular wax (Anutex; Kemdent Dental Products Ltd, Wiltshire, United Kingdom) pattern (30 mm × 3.5 mm × 1 mm) were invested with magnesia based investment material (Titavest CB, Morita, Kyoto, Japan) and casting were performed with grade II cp Ti (J. Morita Co., Kyoto, Japan) in a two chamber inert-gas vacuum pressure casting machine (Cyclarc II, Morita, Kyoto Japan). Castings were sandblasted with 110 μm alumina oxide particles (Al 2 O 3 ) for the removal of the investment material. The porosity of all specimens was examined radiographically. A dental radiographic unit (Gendex 756 DC; Dentsply, Milano, Italy) was used under the following conditions: 65 kV accelerating voltage 7 mA beam current, 13 cm distance from the source to charged couple device sensor and 0.8 s exposure time. The specimens with internal pores were excluded from the study. The selected specimens were ground on all sides with 600 grit SiC paper under continuous water cooling in a grinding/polishing machine (Ecomt III, Buehler Bluff Lake, Ill). All specimens were ground up to final dimensions of 25 mm × 3 mm × 0.45–0.55 mm. Then one side of each specimen was ground up to 2000 grit and polished with 6 μm, diamond paste (DP Paste, Struers, Copenhagen, Denmark). Before the porcelain application final cleaning was performed with hot distilled water in ultrasonic cleaner for 10 min. Fifty six specimens were randomly divided in eight groups and the specimens of each group were covered with the porcelains shown in Table 1 according to their manufacturers’ instructions. Metallic surface preparation (sandblasting with Al 2 O 3 particles) and successive porcelain layers (bonding agent, opaque, dentin and glaze) were applied at the center of each specimen over an 8 mm length and 1 mm thickness. One specimen from each group to be used for interfacial analysis was covered with porcelain without prior sandblasting contrary to manufacturers’ instructions. To minimize the effect of handling variations, all the metal–ceramic specimens were prepared by one dental technician (the second author).
Brand names | Material type | Manufacturers | Firing temp. (°C) | CTE (×10 −6 K −1 ) |
---|---|---|---|---|
Duceratin | Powder | Degussa Dental, Hanau, Germany | 830 | N/A a |
Duceratin plus | Powder | Degussa Dental, Hanau, Germany | 780 | 12.5 (25–500 °C) |
Initial Ti | Powder | GC Corporation, Tokyo, Japan. | 810 | N/A b |
Ti-22 | Powder | Noritake, Nagoya, Japan | 800 | 9.7∼10.7 (25–500 °C) |
TiKrom | Powder | Orotig, Verona, Italy | 810 | N/A a |
Titankeramik | Paste | Vita, Bad Sackingen, Germany | 800 | N/A a |
Triceram | Powder | Esprident-Dentaurum, Ispringen, Germany | 795 | 9.4∼9.5 b |
Triceram | Paste | Esprident-Dentaurum, Ispringen, Germany | 795 | 9.2 (25–400 °C) |
2.2
Interfacial characterization
One specimen from each group was embedded in an acrylic resin (Durofix-2, Struers). After 24 h storage in room temperature the specimens were ground with silicon carbide papers (220–2000 grit size) under continuous water cooling. Final polishing was performed with 0.25 μm diamond paste (DP Paste, Struers) in the grinding/polishing machine (Ecomet III, Buehler, Lake Bluff, IL, USA). The specimens were ultrasonically cleaned for 10 min in a water bath and sputter-coated with carbon in a sputter-coating unit (SCD 004 Sputter-Coater with OCD 30 attachment, Bal-Tec, Vaduz, Liechtenstein). The metal–ceramic interface was examined in a scanning electron microscope (Quanta 200, FEI, Hillsboro, Or, USA) equipped with a super ultra-thin Be window X-ray EDS detector (Sapphire CDU, Edax Int, Mahwaw, NJ, USA). Interfaces were imaged with Backscattered Electron Imaging (BEI) employing a solid state backscattered detector under 30 kV acceleration voltage, 110 μA beam current and 1500× nominal magnification. Additionally, the elemental distribution across the metal–ceramic interface was determined by using line scan EDS analysis. The interface was imaged in 30,000× magnification and the data were collected across a 8.36 μm line each side the metal–ceramic interface employing 14 point of analysis per micron. The results were smoothened employing the Genesis 5.1 software (Edax Int, Mahwaw, NJ, USA).
2.3
Evaluation of bond strength
Three cast specimens without porcelain were subjected to a three point bending test to determine the modulus of elasticity of cp Ti castings, using a universal testing machine (Tensometer10, Monsanto, Swindon, UK). The specimens were loaded at the center with a crosshead speed of 1.5 mm/min, and the deflection and load were continuously recorded. The elastic modulus of Ti in bending was determined according to the following formula:
E = L 3 Δ P 4 b h 3 Δ d
where E is the elastic modulus in bending, L is the span between supporting rods (20 mm), b is the specimen width (3 mm), h is the specimen thickness (0.5 mm), and Δ P and Δ d are the load and deflection increment, respectively, between two specific points in the elastic portion of the curve. The remaining six metal–ceramic specimens of each group were loaded in the three point bending device at the same crosshead speed of 1.5 mm/min ( Fig. 1 ). Porcelain debonding was determined by a sudden decrease in the load–deflection graphs. The debonding load was recorded, and the metal–ceramic bond strength in units of MPa was calculated according to the following formula provided by ISO 9693 :
Bond strength = F × k
where F is the debonding load (N t), and k is a coefficient calculated from the ISO specification that is dependent on the modulus of elasticity of the alloy and height of each specimen.
2.4
Fracture mode analysis
The metallic fractured surfaces of all specimens were sputter-coated with carbon in a sputter-coating unit (SCD 004 Sputter-Coater with OCD 30 attachment, Bal-Tec, Vaduz, Liechtenstein). The fractured surfaces were examined in SEM employing secondary electron images (SEI) under 25 kV accelerating voltage 110 μA beam current and 100× nominal magnification. One EDS spectrum was obtained from the central region of each specimen under 30 kV accelerating voltage 100 μA beam current and 1.28 mm × 1.28 mm sampling window. Quantitative analysis was performed in standardless mode using the Genesis (5.1 version) software. (Edax Int). The area fraction of the adherent bonding agent residues (AFBA) on each specimen after porcelain debonding was calculated by the following equation :
% porcelain adherence = 100 × S i f − S i t S i p − S i t
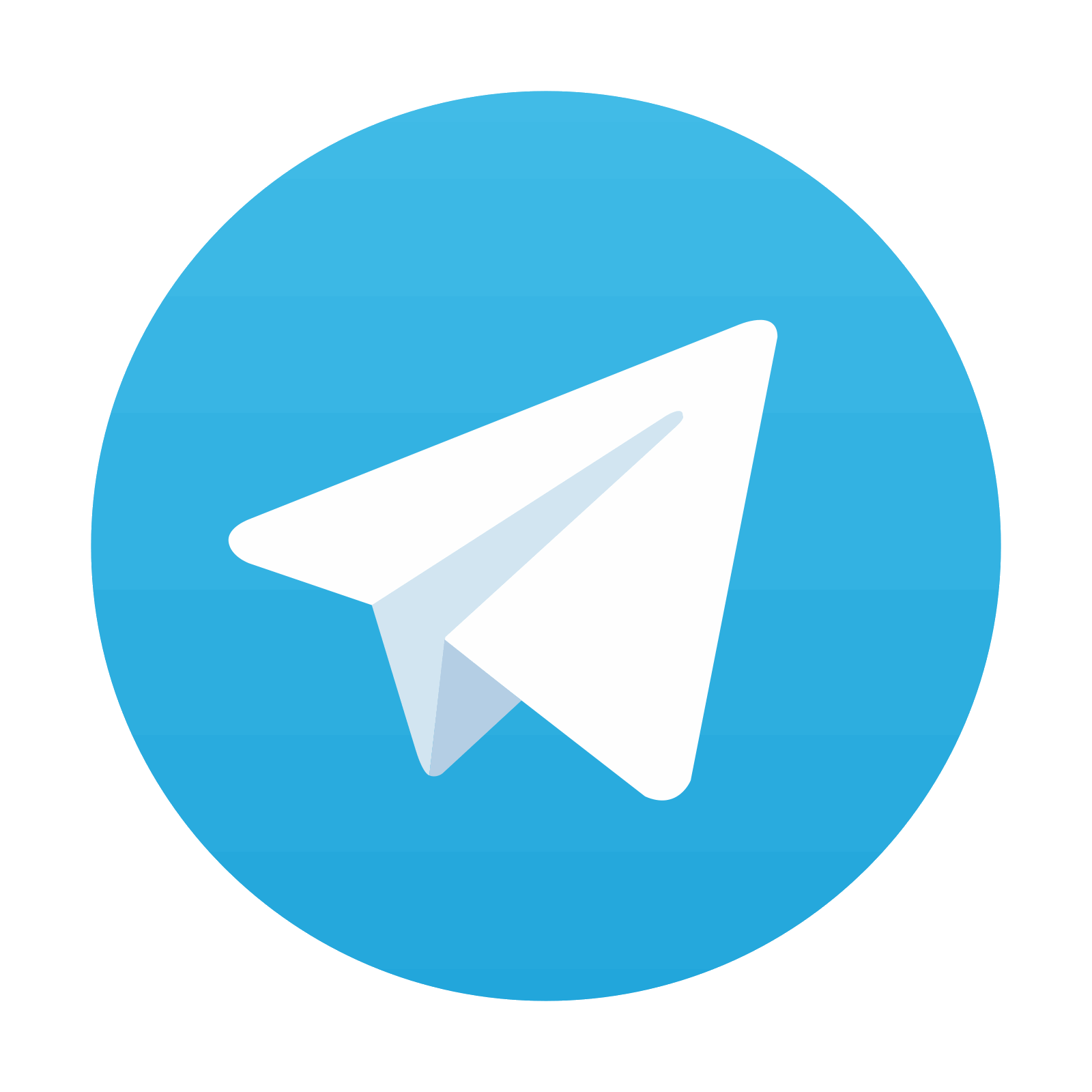
Stay updated, free dental videos. Join our Telegram channel

VIDEdental - Online dental courses
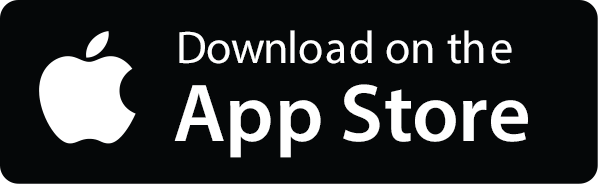
