Highlights
- •
There are large differences in the flexural strength results of dental zirconia although the same ISO standard is used.
- •
The surface treatment method used played an important role and was highly dependent on the operator.
- •
Moreover, even the required mean value of 500 MPa could not be achieved within one group.
Abstract
Objective
The aim of this interlaboratory round robin test was to prove the robustness of the DIN EN ISO 6872:2019 and to identify the influence of processing and testing variations.
Methods
Each of the 12 laboratories participated (A–L) received 60 (n = 720) assigned zirconia specimens. All participants seperated the specimens from the blanks, sintered them, polished half of all specimens and performed the biaxial flexural test (DIN EN ISO 6872:2019). The surface roughness was determined by using tactile measuring device. Fractographic examination was performed under scanning-electron-microscopy (SEM). Data was analysed using Kolmogorov–Smirnov-, Kruskal–Wallis-, Mann–Whitney-U-test and two-parametric Weibull statistic (p < 0.05).
Results
The results for both preparation methods (as-fired and polished) showed significant differences for some participants. The values for as-fired groups ranged between 513 (I) and 659 (E) MPa. H showed higher Weibull modulus than C, E and I. Within polished groups flexural strengths values from 465 (L) to 1212 (E) MPa were observed, with a tendency to clustered groups A, I, J, L (465–689 MPa) and remaining groups (877–1212 MPa). E presented the highest and H the lowest Weibull modulus. Within A and J, no impact of the preparation method on flexural strength values was observed. Within L, as-fired specimens showed higher flexural strength than polished ones. The flexural strength increase did only associate to a certain extent with measured surface roughness. Fractography showed defect populations depending on polishing techniques, associated to the strength level, especially for polished groups. Reduced strength is related to machining defects, regardless of the surface state.
Significance
DIN EN ISO 6872:2019 can be seen as guidance to biaxial flexural strength testing but additional effort is necessary to ensure interlaboratory comparability. Calibrated furnaces and reliable sintering conditions are mandatory requirements together with detailed specifications on finishing or polishing procedures. Biaxial flexural testing is really a matter of understanding specimen preparation, alignment and mechanical testing by itself.
DIN EN ISO 6872:2019 should further recommend reporting of mean surface roughness along with any biaxial flexural strength data. Fractography is a mandatory tool in interpretation and understanding of strength data.
1
Introduction
Mechanical properties of dental ceramics like zirconia are a crucial factor for determining clinical indications. These properties are often measured using standardized experimental procedures and test setups in order to obtain reproducible and reliable data that are valid and easy to compare. The comparison of characteristic material properties does not only matter for benchmark testing of products but is even more relevant for internationally standardized comparability among manufacturers and independent research facilities. The International Organization for Standardization (ISO) has therefore published a wealth of standards describing specific procedures and techniques. These standards do not claim to present the most exact and precise way of measuring a property, but at least ensure common standard procedures worldwide. Regarding the property of biaxial flexural strength of ceramics, the ISO has released several standards in the technical field, but only one being specific on dental ceramics. The Technical Subcommittee TC106/SC2 is responsible for drafting and updating the DIN EN ISO 6872 standard (Dentistry – Ceramic Materials) [ ] with the latest update in 2019. Therein, dental ceramics are classified and relevant specimen preparation and testing environments are defined.
The dental market today offers different types of dental zirconia materials ranging from yttria stabilized tetragonal zirconia polycrystals (3Y-TZP) with varying content of alumina (either 0.25 wt% or 0.05 wt%) to partially stabilized zirconia polycrystals with consistent content of alumina (0.05 wt%) but varying amounts of yttria (4Y-PSZ and 5Y-PSZ). The adjustment in chemical composition affects the crystal structure of zirconia resulting in improved light transmittance (translucency) and a decrease in mechanical properties among the different types. The adjustment of the chemical composition affects the crystal structure of zirconia, resulting in improved light transmission (translucency) and a reduction in mechanical properties between the different types. The reduced alumina content leads, for example, to an increase in the cubic phase in the microstructure – which exhibits isotropic optical behaviour – and this in turn does not lead to birefringence at the lattice structure as is the case with the tetragonal phase, and thus reduces scattering loss [ ]. Furthermore, the high proportion of cubic phase also influences the fracture toughness. The well-known transformation stabilization (tetragonal to monoclinic) as known from the 1st generation zirconia is not given here [ ].
One key property characterizing the long-term performance in certain clinical indications is the flexural strength of a dental restorative material. Regarding flexural strength testing, DIN EN ISO 6872:2019 [ ] defines three different experimental procedures including the 3-point, 4-point and biaxial flexural strength testing. It is known from literature, that the results of these different test setups can vary considerably [ , ] due to factors like the flaw distribution and the effective volume under maximum stress. However, even if one test procedure is standardized and conducted strictly according to ISO requirements, it is questionable whether the outline by DIN EN ISO 6872:2019 accounts for sufficient reproducibility between different, independent test laboratories. Doubt is cast by scientific data showing that the manufacturing process itself has an impact on mechanical [ ], microstructural [ ] or optical properties [ ] of zirconia. Furthermore, it is known that the grain size and the flexural strength depend on the sintering temperature [ ]. Speaking of that, no specification about the sintering furnace is mentioned in the DIN EN ISO 6872:2019 [ ].
In addition, the quality of surface finishing also has a significant influence on flexural strength of ceramic materials [ , ]. One would expect different outcome when testing as-fired specimens versus smoothly polished specimens. Unfortunately, both variants are allowed in the ISO standard, whereas grinding is done with “diamond-embedded media, having a nominal grit size of 30 μm–40 μm, and final polish on media having 15 μm–20 μm diamond grit” [ ].
Furthermore, it is often difficult to test CAD/CAM materials in accordance with this standard, as the geometries of the blanks available on the market often do not permit the production of test specimens from them [ ].
A Web of Science search revealed 195 publications (10.01.2020) dealing with: TITLE: (biaxial flexural strength) AND TOPIC: (ceramic) AND TOPIC: (dental). This result depicts the worldwide interest towards biaxial flexural strength testing in dental research groups.
After a preliminary literature screening, only three investigations were found including interlaboratory comparisons in the field of dental materials. All papers were published by Heintze et al. [ ] with the main focus on wear behavior of dental restorative materials and denture teeth. In the field of technical ceramics, a VAMAS (Versailles Project on Advanced Materials and Standards; http://www.vamas.org/ ) based round robin test on biaxial flexural strength was conducted in the mid 1980s [ ]. A successful and consistent interlaboratory study involved seven test centers and was conducted with detailed distinction between material inherent, processing, experimental, systematic, and statistical errors. The leading expert, George Quinn, has further addressed the issue of standardization to the dental community during an invited talk at the 2014 Academy of Dental Materials conference in Bologna, Italy [ ]. Therein, he highlighted the importance of round robin tests on the precision, reliability, and interlaboratory reproducibility. A further technical investigation dealt with flexural strength data comparison in an interlaboratory study (4-point flexural strength on alumina). They demonstrated that the humidity could produce a problem in the reproducibility of their strength data, and it was recommended to test the specimens coated with oil to protect them from contact with the environmental moisture [ ].
On this background, the authors of the current investigation identified the need for a closer investigation on biaxial flexural strength of dental ceramic materials as described in DIN EN ISO 6872:2019 [ ] and initiated an interlaboratory round robin test. The study involves the influence of surface finish and sintering furnace on the biaxial flexural strength and surface roughness of zirconia considering the impact of varying approaches, devices and test setups used in experienced research institutes. The null hypothesis was that there are no differences between the results of different laboratories when strictly testing within the frame of the DIN EN ISO 6872:2019 [ ].
2
Materials and methods
Twelve dental research laboratories, experienced in mechanical testing, participated in this investigation (A–L). Every test laboratory made sure to refer to the latest version of DIN EN ISO 6872:2019. One translucent zirconia 5Y-PSZ (Ceramill ZOLID FX, Amann Girrbach, Koblach, Austria, LOT 1512008) was used. The manufacturer provided n = 60 specimens for each participant (total 720). Specimens were milled (Ceramill Motion 2, ArmannGirrbach, Koblach, Austria). Nine specimens per zirconia blank were milled, whereby all specimens remained connected to the blank by small support webs. To avoid a batch-dependent influence, material from one batch was used. All blanks were packed and sent to the participants of each coordinating laboratory. All participants then separated the specimens from the blanks, sintered the specimens, polished half of all specimens and performed the biaxial flexural test. All test conditions of each participating laboratory are summarized in Supplement. Beyond DIN EN ISO 6872:2019 specifications, each test laboratory employed individually established lab procedures, such as specimen preparation, sintering procedures and testing fixtures. All practical details are summarized in Supplements 1 and 2.
2.1
Biaxial flexural test
The biaxial flexural test was performed according to DIN EN ISO 6872:2019 [ ]. The disk-shaped specimens (12 mm diameter, 1.2 ± 0.2 mm thickness) were placed on three balls arranged in a circle (positions shifted by an angle of 120°). Each participant divided the specimens into two groups after the sintering process. Half of the specimens (n = 30) were tested as-fired and half of the specimens (n = 30) were polished before the flexural test (details: see Supplement). The polished side was placed under tension and a force was applied using a centered piston at a crosshead speed of 1 mm/min. The radius and the thickness of the disc-shaped specimens, the radius of the circle defined by the three balls and the radius of the loaded area are summarized in Supplement 2. The biaxial flexural strength σ was calculated according to Eq. (1) :
where P is the maximum force measured during the test, b is the thickness of the specimens at the origin of fracture, r 1 is the radius of the circle defined by the three balls, r 2 is the radius of the loaded area, r 3 is the radius of the specimen, and ν is the Poisson’s ratio defined to ν = 0.31.
2.2
Surface roughness measurement
A tactile profilometer was used for roughness analysis (Perthometer S6P, Mahr, Göttingen, Germany). For each participant, n = 3 specimens per surface condition were analysed (n = 6/participant) in one coordinating laboratory. On a measuring surface of 3 mm × 3 mm, n = 121 single profiles per specimens were measured.
The samples were examined before the measurement, and where conspicuous scratches could be seen, the stylus was positioned perpendicular to the defect direction for the measurement. Of course this could not be applied to the samples where no surface defects were visible.
The arithmetic mean roughness value (Ra) was determined by using software (MountainsMap 7.3, Digital Surf, Besançon, France). The Gaussian filter was set to 0.6 mm.
2.3
Microstructure
The microstructure of the 5Y-PSZ material under investigation was analyzed. Images were taken from group F, after thermal etching at 1400 °C for 30 min and gold sputtering in a Field Emission Scanning Electron Microscope (FESEM) (Ultra 55 plus, Carl Zeiss, Oberkochen, Germany).
2.4
Fractographic examination
Fractured specimens from all research participants and from as-fired and polished groups were fractographically examined with regard to surface polishing quality, morphology, subsurface defects, and reasons for failure, i.e. failure origins. All specimens were cleaned in 90 vol% ethanol solutions in an ultrasonic bath (Easyclean, Renfert, Hilzingen, Germany) to remove organic debris and contaminants. Photographs and stereomicroscopic images (Discovery V8, Carl Zeiss) were taken to register the visual appearance of the fragments before processing for SEM. Specimens were then sputter-coated with gold and analyzed under an Auriga SEM equipped with a Gemini gun (Carl Zeiss) for surface morphology and fracture patterns that would allow the determination of crack trajectories and fracture origins.
2.5
Statistical analysis
Descriptive statistics were computed. The presumption of normal distribution was tested using the Kolmogorov–Smirnov test. To determine significant differences between the various participant groups and specimen preparation methods (as-fired or polished) the non-parametric Kruskal–Wallis- and Mann–Whitney-U tests were used at a significance level of α = 0.05. All p-values below 0.05 were construed as statistically significant. The software SPSS statistics version 25 (IBM, Armonk, NY, USA) was used for the analysis. Two-parameter Weibull modulus and characteristic flexural strength were computed with calculations based on the method of least squares [ ].
3
Results
The specimen thickness is shown in Fig. 1 . Across all participants (A–L), the thickness of as-fired specimens was in the same range (1.371 mm–1.391 mm). Within polished specimens, differences in the thickness were determined (1.007 mm–1.387 mm) ( Fig. 1 ).

The roughness for as-fired and polished specimens is shown in Fig. 2 .

The surface condition of as-fired specimens was identical across all participants (A–L), while the surface quality in the polished state showed differences. Specimens tested as-fired showed significantly higher surface roughness than polished specimens (p < 0.001). Within as-fired specimens no impact of participants was observed (p < 0.001). However, within polished specimens, participants A and I showed higher roughness values than the remaining participants (p = 0,067).
The Weibull results (m and σ 0 ) are summarized in Tables 1 and 2 . Within as-fired groups, participant H showed significantly higher Weibull modulus than participants C, E and I. Within polished groups, participant E presented significantly higher Weibull modulus than participants C, D, F, G, H, J, K, and L. Participant H showed significantly lower Weibull modulus than participants D and E. The remaining groups were in same range of values. The coefficient of variation (Weibull modulus) for polished group was 29.20%, and 16.90% in as fired group.
Participant | Normal distribution | Weibull distribution | ||
---|---|---|---|---|
Biaxial flexural strength | SD | Characteristic flexural strength (95% CI) | Weibull modulus (95% CI) | |
A | 650 bc | 83 | 684 (655;713) | 9.4 (6.4;13.7) |
B | 631 bc | 89 | 665 (637;694) | 8.9 (6.1;12.8) |
C | 575 abc | 88 | 608 (580;638) | 8.2 (5.5;12.1) |
D | 593 abc | 80 | 623 (597;650) | 9.3 (6.3;13.6) |
E | 659 c | 91 | 698 (665;732) | 8.0 (5.4;11.6) |
F | 581* abc | 57 | 605 (584;625) | 12.2 (8.2;17.8) |
G | 653 bc | 70 | 682 (657;706) | 11.3 (7.6;16.5) |
H | 600 abc | 59 | 625 (604;646) | 12.3 (8.3;17.9) |
I | 513 a | 81 | 547 (517;578) | 7.1 (4.7;10.4) |
J | 610 bc | 70 | 640 (614;665) | 10.1 (6.8;14.7) |
K | 566 ab | 64 | 592 (570;613) | 11.1 (7.5;16.2) |
L | 606 bc | 74 | 636 (610;662) | 10.0 (6.7;14.6) |
Participant | Normal distribution | Weibull distribution | ||
---|---|---|---|---|
Biaxial flexural strength | SD | Characteristic flexural strength (95% CI) | Weibull modulus (95% CI) | |
A | 658 b | 78 | 690 (663;717) | 10.0 (6.8;14.4) |
B | 1047* def | 162 | 1109 (1049;1172) | 7.2 (4.8;10.6) |
C | 908 d | 205 | 987 (913;1065) | 5.0 (3.3;7.3) |
D | 1124* ef | 161 | 1194 (1134;1255) | 7.7 (5.2;11.3) |
E | 1212 f | 144 | 1271 (1223;1321) | 10.1 (6.8;14.7) |
F | 1034 def | 187 | 1107 (1042;1174) | 6.6 (4.4;9.6) |
G | 989 de | 201 | 1070 (997;1148) | 5.5 (3.6;8.0) |
H | 952 de | 205 | 1037 (957;1122) | 4.9 (3.2;7.2) |
I | 618 ab | 98 | 659 (624;696) | 7.2 (4.8;10.4) |
J | 689 bc | 185 | 750 (688;816) | 4.6 (3.0;6.8) |
K | 877 cd | 190 | 950 (882;1023) | 5.3 (3.5;7.7) |
L | 465 a | 122 | 503 (465;544) | 5.0 (3.3;7.4) |
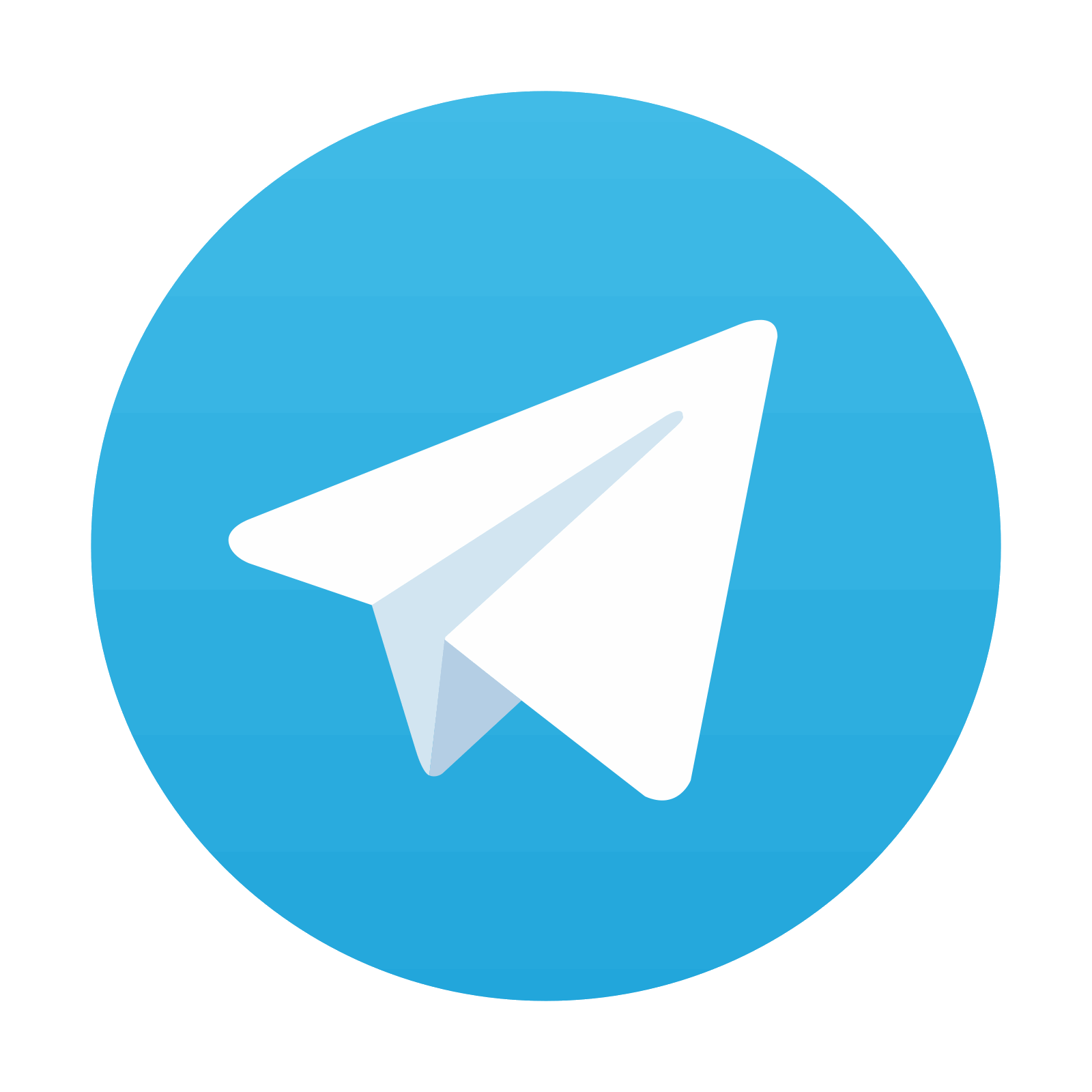
Stay updated, free dental videos. Join our Telegram channel

VIDEdental - Online dental courses
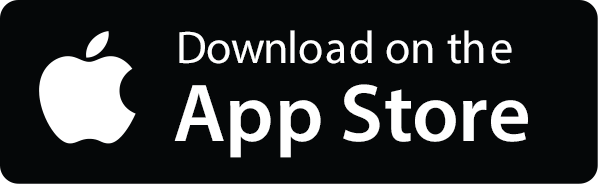

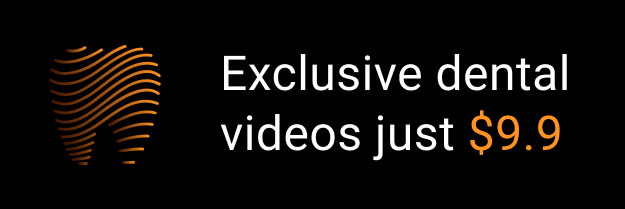