Abstract
Objectives
The purpose of this study was to evaluate polymerization shrinkage of resin composites using a coordinate measuring machine, optical coherence tomography and a more widely known method, such as Archimedes Principle. Two null hypothesis were tested: (1) there are no differences between the materials tested; (2) there are no differences between the methods used for polymerization shrinkage measurements.
Methods
Polymerization shrinkage of seven resin-based dental composites (Filtek Z250™, Filtek Z350™, Filtek P90™/3M ESPE, Esthet-X™, TPH Spectrum™/Dentsply 4 Seasons™, Tetric Ceram™/Ivoclar-Vivadent) was measured. For coordinate measuring machine measurements, composites were applied to a cylindrical Teflon mold (7 mm × 2 mm), polymerized and removed from the mold. The difference between the volume of the mold and the volume of the specimen was calculated as a percentage. Optical coherence tomography was also used for linear shrinkage evaluations. The thickness of the specimens was measured before and after photoactivation. Polymerization shrinkage was also measured using Archimedes Principle of buoyancy ( n = 5). Statistical analysis of the data was performed with ANOVA and the Games–Howell test.
Results
The results show that polymerization shrinkage values vary with the method used. Despite numerical differences the ranking of the resins was very similar with Filtek P90 presenting the lowest shrinkage values.
Significance
Because of the variations in the results, reported values could only be used to compare materials within the same method. However, it is possible rank composites for polymerization shrinkage and to relate these data from different test methods. Independently of the method used, reduced polymerization shrinkage was found for silorane resin-based composite.
1
Introduction
Despite the major developments in new restorative materials, all resin-based composites present a certain degree of volume reduction due to the polymerization reaction. Assuming that these materials are bonded to prepared dental cavities, this volume contraction will lead to internal stress generation, which in turn, compromises the mechanical and chemical stability of the restoration and may lead to the loss of marginal integrity . As a consequence, marginal leakage of saliva and its components will occur resulting in post-operative sensitivity, discolored margins, recurrent caries and fractures of the restoration margins . These clinical consequences are the main reasons for restoration substitution, and explain why polymerization shrinkage is recognized as the main limitation of these materials .
Many studies have been conducted to evaluate polymerization shrinkage of resin composites. The results indicate that the volume contraction is dependent on the filler concentration, polymerization characteristics, volume and cavity design, restorative procedure and light intensity used for photoactivation . In addition, polymerization shrinkage has a strong influence on stress generation and most of these tensions are developed in the first few seconds after irradiance . The characterization of the shrinkage behavior and the polymerization reaction itself are an important aspect in the development of new restorative materials .
To reduce shrinkage, the main approaches adopted so far are modifications in the filler amount, shape or surface treatment. Versatile methods to modify the monomer matrix have been developed, starting with typical dimethacrylates with a reduced reactive group. Other approaches include the development of liquid crystal monomers or ring-opening systems to produce non-shrinking or minimally shrinking dental composites that contain spiroorthocarbonates as additives to dimethacrylate or epoxy resins. A new resin system, called siloranes, claims to have combined the two key advantages of the individual components: low polymerization shrinkage due to the ring-opening oxirane monomer and increased hydrophobicity due to the presence of the siloxane species .
However, the magnitude of the shrinkage is dependent on the methodology used to measure it. The results obtained for any of the methods recently published also varies between operators. Therefore, comparisons between published results are quite difficult with research being carried out in different laboratories with different equipment and operators .
Many methods have been described to measure polymerization shrinkage: bonded disk method , mercury dilatometer , optical method , gas pycnometer , the use of a strain gage , linear displacement , free linear shrinkage, wall-to-wall shrinkage , among others. However, each method for polymerization shrinkage evaluation depends on one physical principle for measurement.
It is in this context that new polymerization shrinkage evaluation methods appear, not only to determine volume variations but mainly to enable comparisons between the results obtained for each method. This is of greater importance to assure the reproducibility and veracity of the results.
Coordinate measuring systems were developed at the end of the 20th century to fulfill the industrial sector’s need for easy and quick inspections of fabricated pieces using automated manufacturing systems. The primary goal of coordinate measuring machines (CMMs) is to obtain the Cartesian coordinates of points on a solid surface .
A CMM is composed of four interconnected rigid parts, three mobile and one fixed base. A CMM with a fixed working table and a mobile bridge is the most common type. In this type of CMM, the object to be measured is placed on the fixed granite table and the operator dislocates each of the three mobile parts along the three axes using a joystick in the following sequence: the bridge (along the OX axes), the car (along the OY axes) and the probe column (along the OZ axes). Finally, a ruby probe touches a specific point on the object. Each part of the machine has a built-in guide rail, so that the relationship between the axes allows a point to be located in all three planes with one check. The resulting data are mathematically processed in a computerized system to provide dimensional and geometrical measurements of any kind of object with high precision .
Optical coherence tomography (OCT) is a non-invasive medical diagnostic imaging modality with high resolution that can give near-histologic images. The basic principle of OCT is analogous to computerized tomography (which uses X-rays), magnetic resonance imaging (which uses spin resonance), and B-scan ultrasound (which uses sound waves). Nevertheless OCT uses only light to derive its image in a non-contact, non-invasive system .
OCT is based on a Michelson interferometer with a low coherence, broadband light source. The light generated in an OCT system is divided in two: one part follows a sample arm containing the item of interest, and the other follows the reference arm, which is usually a mirror. Reflected light is then recombined. When the path length of light from the reference mirror is the same as the tissue or sample, an interference fringe is detected. Because the reference mirror is moved by known increments, the position of the reflected light within the sample can be determined by the optical scattering properties of tissues. These interference patterns generate a reflectivity profile, called an A-scan. A two-dimensional tomographic image can be created by combining a series of A-scans .
Archimedes Principle (buoyancy of a material in fluid) is a well-established test method that can be used to measure volumetric dimensional changes by measuring density variations. This principle states that a body immersed in a fluid is buoyed up by a force equal to the weight of the dispersed fluid. Whether a given body will float, sink, or remain static in a given fluid is dependent on both the weight and volume of that material. The relative density – the weight per unit volume of the body compared to that of the fluid – determines the buoyant force .
The determination of dimensional changes in resin composites, shrinkage or expansion, through density measurements using this principle is a relatively simple and low-cost method. It basically consists of weighing the material under study several times in two distinct environments of known density; air is conventionally used as one of environment. Several liquids such as mercury, distilled water and silicone oil can be used as the second surrounding medium.
The purpose of this study was to evaluate shrinkage of resin composite polymerization using CMM, OCT, and a more widely known method, such as Archimedes Principle. Two null hypotheses were tested: (1) there are no differences between the materials tested; (2) there are no differences between the methods used for polymerization shrinkage measurements.
2
Materials and methods
The materials, manufacturers, composition and batch numbers for this study are listed in Table 1 .
Composite | Matrix a | Filler content; filler size; % by weight/volume | Manufacturer b ; batch no. |
---|---|---|---|
Filtek Z250™ | BisGMA, UDMA and BisEMA BisGMA | Zirconia/silica; microhybrid; 82/60 | |
3M/ESPE; 9EM | |||
Filtek Z350™ | UDMA, TEGDMA and BisEMA | Zirconia/silica and silica; nanoparticle; 78.5/59.5 | 3M/ESPE; 8UU |
Filtek P90™ | Silorane | Quartz and yttrium fluoride; microhybrid; 76/55 | 3M/ESPE; 9CH |
4 Seasons™ | BisGMA, UDMA and TEDMA | Barium glass, ytterbium trifluoride, Ba–Al-fluorosilicate glass, highly dispersed silicon dioxide and spheroid mixed oxide; nanohybrid; 75–77/55–58 | Ivoclar Vivadent; 12979 |
Tetric Ceram™ | BisGMA, UDMA and TEDMA | Barium glass, ytterbium trifluoride, Ba–Al-fluorosilicate glass, highly dispersed silicon dioxide and spheroid mixed oxide; microhybrid; 79/60 | Ivoclar Vivadent; 08516 |
Esthet-X™ | U-BisGMA, BisEMA and EGDMA | Borosilicate/aluminum/barium glass and silica; nanohybrid; 77/– | Dentsply Caulk; 0709132 |
TPH Spectrum™ | U-BisGMA | Borosilicate/aluminum, barium and silica; microhybrid; 77/57.1 | Dentsply Brazil; 135676B |
a BisGMA, bisphenol-glycidyl methacrylate; UDMA, urethanethyl dimethacrylate; TEGDMA, triethylene glycol dimethacrylate; BisEMA, bisphenol-polyethylene glycol dimethacrylate; U-BisGMA, urethane-modified bisphenol-glycidyl methacrylate.
b 3M ESPE, St. Paul, MN, USA; Ivoclar Vivadent, Schaan, Liechtenstein; Dentsply Caulk, Milford, DE, USA; Dentsply Indústria e Comércio ltda, Petropólis, RJ, Brazil.
All photoactivation procedures were done using a halogen light output (Optilight Plus™, Gnatus, São Paulo, Brazil) with a 10 mm diameter light conductor. Just before each specimen preparation, light intensity was measured with an external radiometer (Gnatus, São Paulo, Brazil), always within the range of 550–600 mW/cm 2 . The composites were photoactivated for 40 s in continuous mode, which ensures a radiant exposure between 22 and 24 J/cm 2 and, therefore, adequate polymerization .
2.1
Coordinate measuring system
A predefined quantity (0.135 ± 0.010 g) of each test material was placed in bulk in a cylindrical Teflon mold (7 mm × 2 mm). Composites were then covered with a mylar strip and pressed with a microscope glass slide to ensure adequate adaptation into the mold. Photoactivation was performed using the established protocol, and the specimens were then carefully removed from the mold and stored in a dark environment for 15 min ( n = 5) ( Fig. 1 ).

A CMM (Crysta 574/Mitutoyo, Japan) with measurement uncertainty of 2.0 μm was used. To proceed with the measurements, specimens were fixed on a flat glass plate with caulking putty. Measurements were done according to the following protocol:
- (1)
Teflon mold geometry determination:
- a.
5 points on the top surface;
- b.
2 points at the bottom surface;
- c.
4 points at the diameter.
- a.
- (2)
Specimens geometry determination:
- a.
Determination of the origin at the glass plate;
- b.
4 points at the diameter;
- c.
2 points at the top surface.
- a.
The dimensions of the Teflon mold and the specimens (diameter and height) were then used to determine their volumes according to the following equation:
V = π r 2 h
where V is the final volume, π is a mathematical constant equal to 3.14, r is the radius, and h is the height of the cylinder.
Polymerization shrinkage (Δ V ) in % was calculated according to the differences between the volume of the Teflon mold and the specimen, using the following equation:
Δ V = Vol mold − Vol specimen Vol mold × 100 %
where Δ V is the volume variation as a percentage (%), Vol mold , is the volume of the Teflon mold, and Vol specimen is the volume of the specimen.
2.2
Optical coherence tomography
In this experiment, a commercially available OCT system was used (Spectral Radar SR-OCT: OCP930SR/Thorlabs, New Jersey, USA). The superluminescent diode (SLD) light source operates at a central wavelength of 930 nm. This system consists of three main parts: a handheld scanning probe, a base unit, and a personal computer (PC) ( Fig. 2 ). The base unit contains the SLD light source. A fiber optic coupler is used to direct the light from a broadband SLD source to the Michelson interferometer, which is located inside the handheld probe. Both probe and reference light travel back through the same fiber to the spectrometer and imaging sensor located in the base unit. The base unit is connected to the PC, which is equipped with two high-performance data acquisition cards. All required data acquisition and processing is performed via the integrated software package, which contains a complete set of functions for controlling data measurement, collection and processing, and for displaying and managing OCT image files. The maximum image depth is 1.6 mm and transverse scanning is 6.0 mm with an axial resolution of 6.2 μm.

A cylindrical Teflon mold (7 mm diameter ± 0.5 mm height) was used to assess linear polymerization shrinkage. To execute the scans, insert and photoactivate the composites, the mold was fixed onto a sliding rail. A micrometric x , y , and z translator was attached to the scanning probe in order to dislocate it precisely. This was necessary to ensure OCT scanning of the entire mold. Because of the smaller size of the scan length (6.0 mm) compared with the diameter of the Teflon mold (7.0 mm), each scan was done at two distinct predetermined points.
At the beginning of each specimen preparation, the empty mold was scanned to ensure its accurate height. Resin composites were inserted into the mold it and then covered with a very thin microscope glass slab (0.13–0.16 mm thick). A thicker microscope glass slab (1.03 mm) was placed over the whole assembly and manually pressed against the mold to ensure adequate resin accommodation inside the cavity and then it was removed. In a dark room, a second scan was performed to register the exact amount of uncured resin.
Photoactivation was performed using the established protocol, and the very thin microscope glass slab was then carefully removed from the upper side of the specimens. Fifteen minutes later, another scan was performed ( n = 5).
To measure the thickness of the composites, images were analyzed using the ImageJ program (Image Processing and Analysis in Java) . Linear shrinkage was then calculated using the formula:
linear shrinkage = R C 0 min − R C 15 min R C 0 min × 100 %
where RC 0 min is the mean resin thickness between points 1 and 2 when it is still unpolymerized, and RC 15 min is the polymerized mean resin thickness between points 1 and 2.
The refractive index of all the test materials was also calculated using the previously obtained images. The refractive index was determined by applying the formula: refractive index = optical distance/real distance. The optical distance was obtained from the OCT images and the real distance refers to the real thickness of the samples, which was measured from the height of the Teflon molds confirmed by a digital caliper (0.01 mm). Two images (points 1 and 2) were generated for each sample and the refractive index was calculated for each point, which resulted in 10 measurements for each group. Mean values were calculated to obtain the refractive index of the material.
2.3
Archimedes principle
Volumetric shrinkage was determined by density measurements according to Archimedes Principle. Measurements were carried out using a digital analytical balance with a density determination kit (Marte AL 500, Minas Gerais, Brazil). To obtain stabilized readings the measurements were done in a temperature-controlled room ( T = 25 ± 1 °C) and protected from air drafts and electrostatic influences .
The specimens were weighed in air and in water and the density in g/cm was calculated according to the equation:
ρ = m water m air − m water ( ρ water − ρ air ) + ρ air
where ρ is the density of the material, m water is the weight in grams (g) of the specimen in water, m air is the weight in grams (g) of the specimen in air, ρ water is the density of water at the exactly measured temperature in °C according to the density table for distilled water, and ρ air is the density of air (0.0012 g/cm).
Five uncured sphere-shaped specimens each weighing 0.10 ± 0.02 g, were carefully hand made in such a way that trapped air bubbles were avoided. Since the uncured materials were rather sticky, a small mylar strip was used to handle the uncured material. The weight in air and water was previously determined. The weight of the whole assembly (resin + mylar strip) was then determined, first in air and then in water. Slight deformations of the material during the test were of no importance because they do not influence the density. Furthermore, the weighing process was very fast, so there was not much time for the material to flow. The mass of each material was calculated by subtracting the mass of the mylar strip from the mass of the whole assembly. Then, the density of the uncured material ( ρ unpol ) was computed.
To measure the density of the polymerized resin, five cylindrical specimens were made in a Teflon mold (7 mm × 2 mm) and the upper side was covered with a mylar strip to avoid an oxygen inhibition layer . Photoactivation was carried out using the established protocol. Specimens were weighed after 15 min of dry and dark storage. The percentage change in volume change (Δ V ) after polymerization was calculated from the densities according to the equation:
Δ V = 1 ρ 15 min − 1 ρ unpol 1 ρ unpol 100 %
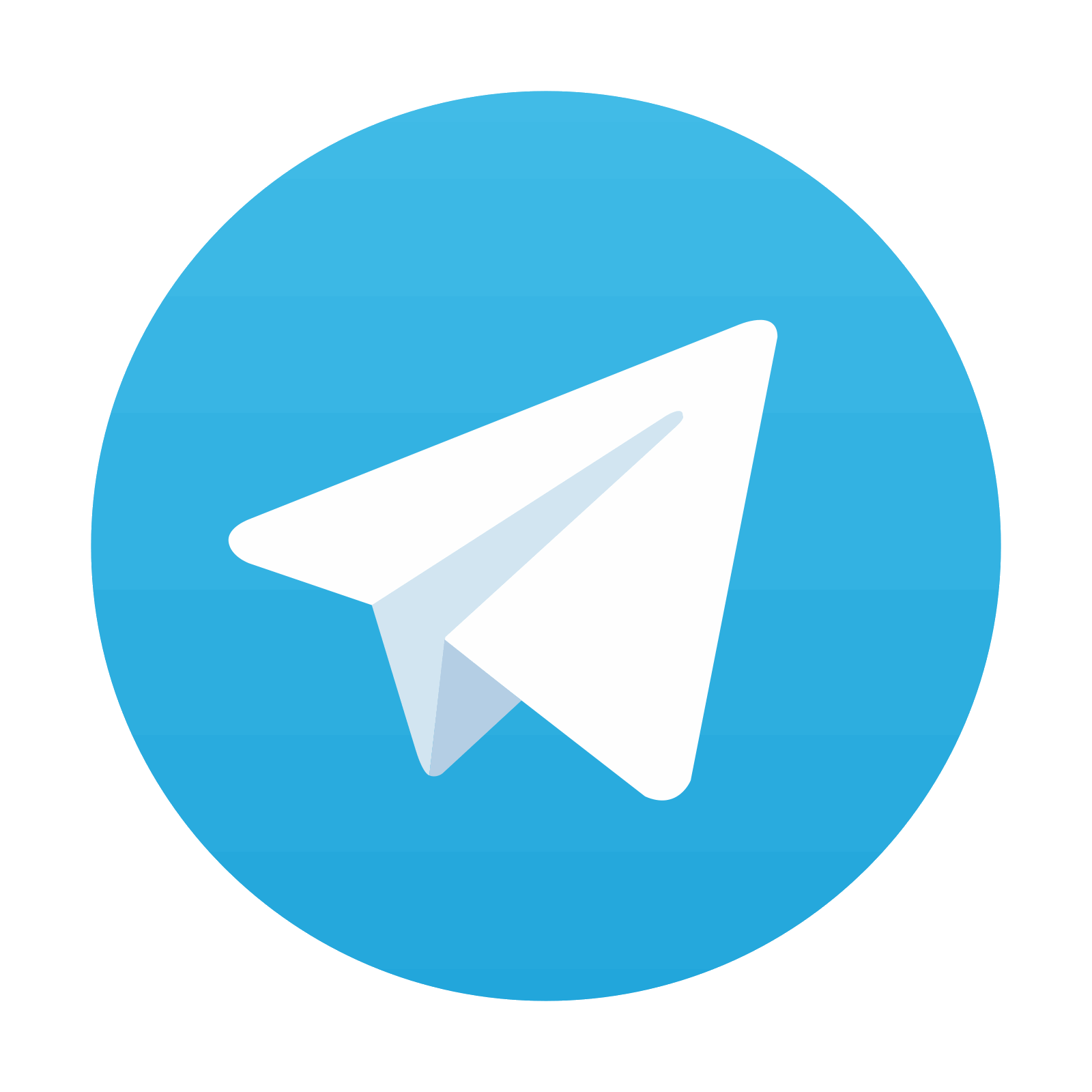
Stay updated, free dental videos. Join our Telegram channel

VIDEdental - Online dental courses
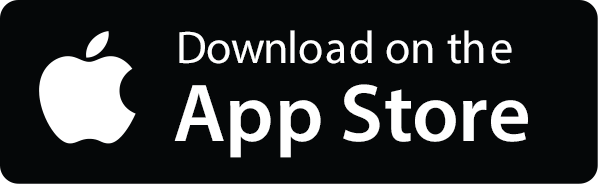
