Abstract
Objectives
Investigation and characterization of the replacement of the Portland cement component in mineral trioxide aggregate (MTA) with tricalcium silicate cement which is manufactured using the sol-gel method from pure raw materials.
Methods
Tricalcium silicate and Portland cement were characterized by viewing under the scanning electron microscope (SEM) and surface imaging and elemental analysis with X-ray energy dispersive analysis (EDX), and by X-ray diffraction analysis with Rietveld refinement. In addition the hydration products of the material after 28 days of curing were evaluated by plotting atomic ratio plots from the EDX data. The cement leachate was evaluated for pH and chemical composition by inductively coupled plasma.
Results
Portland cement was composed of 68% tricalcium silicate. The tricalcium silicate cement was 99% pure. On hydration both cements produced calcium silicate hydrate and calcium hydroxide. The calcium hydroxide was leached in solution with higher leaching in HBSS. The leaching of calcium hydroxide in solution resulted in an alkaline pH. The reaction of calcium with the phosphorus present in HBSS resulting in the deposition of calcium phosphate on the cement surface.
Significance
Tricalcium silicate could prospectively replace the Portland cement component in MTA.
1
Introduction
Portland cement which is used in industry as a binder for concrete was introduced as a root-end filling material in dentistry due to its hydraulic nature as it sets and develops its properties in a humid environment. A radiopacifier namely bismuth oxide was added to the cement in 1:4 proportions in order to allow the material to be identified on a radiograph post-operatively. The formulation of 80% Portland cement and 20% bismuth oxide was patented and received acceptance by the US Federal Drug Administration and became commercially available as ProRoot MTA™ (Dentsply Tulsa Dental, Johnson City, TN, USA) and MTA Angelus™ (Angelus Soluções Odontológicas, Londrina, Brazil). Mineral trioxide aggregate is composed of 53.1% tricalcium silicate, 22.5% dicalcium silicate, 21.6% bismuth oxide and traces of calcium sulfate . The tricalcium and dicalcium silicates are the main components of Portland cement. The similarity of Portland cement to ProRoot MTA™ and MTA Angelus™ has been reported in various studies.
The Portland cement component in MTA may contain some heavy metal contamination. Usually these trace metals are present in amounts ranging from 5 to 100 parts per million (ppm) . These heavy metals include arsenic, chromium and lead which are incorporated in the cement during its production. The heavy metals originate from the use of waste materials as inorganic raw material or from secondary fuels used to fire the kiln during cement manufacture. These wastes are used to minimize the cost of cement production. Trace elements found in wastes which are utilized in cement production may either be transferred to the cement, or emitted with exhaust gasses into the environment .
It is claimed that ProRoot MTA™ is manufactured specifically for Dentsply under clean and segregated conditions to ensure freedom from contamination . The ingredients used to form this dental cement are certified for their purity and the absence of heavy metal contamination. Each batch of MTA is tested using inductively coupled plasma (ICP) . The industrial Portland cements include higher levels of heavy metals than the dental cements . Gray Portland cement and gray MTA exhibited higher acid extractable and leachable arsenic than the white versions of the material. ProRoot MTA and MTA Angelus have similar levels of chromium, arsenic and lead as white Portland cement . ISO 9917-1; 2007 does not specify chromium levels in dental materials. However the level of arsenic detected in MTA was higher than levels specified in ISO 9917. Conversely other researchers reported levels of arsenic below the limit set by ISO 9917 with As III being the species mostly present in the cements .
The main constituent of MTA is tricalcium silicate. Tricalcium silicate has been used on its own or with additives as bone cement , as a die material for the plastic-forming process by extrusion when admixed with cellulose based polymers , as a posterior restorative material and as a root filling material in dentistry. The tricalcium silicate exhibited adequate physical properties and induced cell growth and differentiation and also the deposition of hydroxyapatite on its surface . Tricalcium silicate can be manufactured by the sol–gel method using pure raw materials unlike the raw materials used in the manufacture of Portland cement . Calcium oxide and silicon oxide are used as raw materials to avoid aluminum which has been linked to Parkinson’s and Alzheimer’s disease . The sol–gels are transformed into ceramics by heating at relatively low temperatures . The tricalcium silicate has been postulated to be able to replace the cement component in MTA due to similar composition and bioactivity of the material .
The aim of this research was to characterise tricalcium silicate and investigate the hydration characteristics and leaching of this novel material.
2
Materials and methods
Materials used in this study included Portland cement (PC; CEM 1, 52.5 N; LaFarge Cement, Birmingham, UK), and tricalcium silicate (TCS; Mineral Research Processing, Meyzieu, France). The cements were mixed at water to powder ratio of 0.35.
2.1
Microscopy and elemental analysis of powders and hydrated cements
The morphology and elemental analysis of both un-reacted powders and hydrated cements was evaluated using the scanning electron microscope (SEM) with backscattering detectors and X-ray energy dispersive analysis (EDX). The powders were sprinkled on carbon double-sided tape over an aluminum stub. Diskettes 10 ± 1 mm and a thickness of 1 ± 0.1 mm were prepared for each cement type and were allowed to cure for 28 days at 37 ± 1 °C in either water or Hanks balanced salt solution (HBSS; H6648, Sigma Aldrich, St. Louis, MO, USA). The composition of the HBSS was (g/L) 0.4 KCl, 0.06 KH 2 PO 4 anhydrous, 0.35 NaHCO 3 , 8.0 NaCl, 0.05 Na 2 HPO 4 anhydrous and 1.0 d -glucose. They were then mounted on aluminum stubs with carbon double-sided tape. All the specimens were then carbon coated and SEM/EDX analysis was used to analyze the microstructure and the elemental constitution of each sample.
2.2
Assessment of hydration characteristics
Portland cement and tricalcium silicate cement mixed with water at a water to cement ratio of 0.35 were analyzed. The pastes were compacted in a circular mold 30 mm in diameter using a stainless steel plugger. The materials were cured in sealed plastic (polythene) containers at 37 °C for 28 days using a thermostatically controlled water bath (MGW Lauda M 20, Leica Microsystemes SA, Rueil-Malmaison, France) after which they were immersed in acetone for four days to remove any remaining water, and then dried in a vacuum desiccator for 8 h. The dried paste pieces were set in epoxy resin using vacuum impregnation. The hardened resin block was sawn (Labcut 1010, Agar scientific, Stansted, UK) and ground under copious water irrigation using progressively finer grits of abrasive paper to produce a flat surface. A thin conductive coating of evaporated carbon was applied to the sections prior to examination in the scanning electron microscope. The scanning electron microscope used was an ISI SS40 (ISI, Tokyo, Japan), with an energy-dispersive X-ray system (SAMx Numerix, Levens, France) and a standard beryllium window X-ray detector. The beryllium window was used to absorb X-rays emitted from light elements. Quantitative analyses were carried out using X-ray standards obtained from minerals for each element. Oxygen was calculated by stoichiometry . The examination procedure consisted of collecting backscattered electron images to show the general microstructure, and a series of X-ray spectra. For each specimen, between 50 and 60 spectra were collected. The X-ray spectra were quantified using suitable mineral standards and the data plotted in a standard format showing atomic ratios of Si/Ca vs Al/Ca and Al/Ca vs S/Ca. These atomic ratio plots are used in SEM/EDX studies of cementitious materials and enable the principal hydration products to be differentiated.
2.3
Rietveld X-ray diffraction analysis
Both powders and hydrated cements ground to fine powders after 28 days of hydration in water were analyzed quantitatively using X-ray diffraction analysis (XRD) with Rietveld correction. Five percent corundum (Al 2 O 3 ) relative to the weight of cement was blended with the cement powder to serve as an internal standard thus allowing the calculation of the quantities of the amorphous fraction. This material was chosen because it does not react with water and has no influence on the hydration reaction. X-ray diffraction patterns were first obtained with sufficient resolution for Rietveld analysis. The detector was rotated at 0.017° 2 per 20 s.
2.4
Evaluation of pH of leachate
Diskettes 10 ± 1 mm and a thickness of 1 ± 0.1 mm were prepared of each cement type. After storage in an incubator at 37 ± 1°C for 24 h and removal from the molds, the materials were immersed upright in either 10 ml water or Hanks balanced salt solution. The pH readings of the storage solution were taken using a pH meter (Hanna HI 9811, Hanna Instruments, Woonsocket, RI, USA) prior to immersion and after 28 days.
2.5
Chemical analysis of leachate
The chemical analysis of the cement products released in water and HBSS was performed using inductively coupled plasma atomic absorption spectroscopy (Varian Medical Systems, Palo Alto, CA, USA). The Portland cement and tricalcium silicate cement were mixed in a similar way as the previous experiments producing diskettes 10 mm in diameter and 1 mm high. The specimens were cured for 24 h at 37 °C and 100% humidity after which they were weighed to the accuracy of 0.0001 g and immersed in either 5 ml water or HBSS in closed sterile containers (Labplex, Birmingham, UK). The specimens were removed after 28 days. Containers filled with water and HBSS were used as controls. The leachates were analyzed for aluminum, calcium, silicon, and phosphorus. The amount of leachate was calculated in μg/g using the following formula:
Amount of leachate per weight of cement = amount of leachate per litre × 0.005 × 1000 weight of cement pellet
2
Materials and methods
Materials used in this study included Portland cement (PC; CEM 1, 52.5 N; LaFarge Cement, Birmingham, UK), and tricalcium silicate (TCS; Mineral Research Processing, Meyzieu, France). The cements were mixed at water to powder ratio of 0.35.
2.1
Microscopy and elemental analysis of powders and hydrated cements
The morphology and elemental analysis of both un-reacted powders and hydrated cements was evaluated using the scanning electron microscope (SEM) with backscattering detectors and X-ray energy dispersive analysis (EDX). The powders were sprinkled on carbon double-sided tape over an aluminum stub. Diskettes 10 ± 1 mm and a thickness of 1 ± 0.1 mm were prepared for each cement type and were allowed to cure for 28 days at 37 ± 1 °C in either water or Hanks balanced salt solution (HBSS; H6648, Sigma Aldrich, St. Louis, MO, USA). The composition of the HBSS was (g/L) 0.4 KCl, 0.06 KH 2 PO 4 anhydrous, 0.35 NaHCO 3 , 8.0 NaCl, 0.05 Na 2 HPO 4 anhydrous and 1.0 d -glucose. They were then mounted on aluminum stubs with carbon double-sided tape. All the specimens were then carbon coated and SEM/EDX analysis was used to analyze the microstructure and the elemental constitution of each sample.
2.2
Assessment of hydration characteristics
Portland cement and tricalcium silicate cement mixed with water at a water to cement ratio of 0.35 were analyzed. The pastes were compacted in a circular mold 30 mm in diameter using a stainless steel plugger. The materials were cured in sealed plastic (polythene) containers at 37 °C for 28 days using a thermostatically controlled water bath (MGW Lauda M 20, Leica Microsystemes SA, Rueil-Malmaison, France) after which they were immersed in acetone for four days to remove any remaining water, and then dried in a vacuum desiccator for 8 h. The dried paste pieces were set in epoxy resin using vacuum impregnation. The hardened resin block was sawn (Labcut 1010, Agar scientific, Stansted, UK) and ground under copious water irrigation using progressively finer grits of abrasive paper to produce a flat surface. A thin conductive coating of evaporated carbon was applied to the sections prior to examination in the scanning electron microscope. The scanning electron microscope used was an ISI SS40 (ISI, Tokyo, Japan), with an energy-dispersive X-ray system (SAMx Numerix, Levens, France) and a standard beryllium window X-ray detector. The beryllium window was used to absorb X-rays emitted from light elements. Quantitative analyses were carried out using X-ray standards obtained from minerals for each element. Oxygen was calculated by stoichiometry . The examination procedure consisted of collecting backscattered electron images to show the general microstructure, and a series of X-ray spectra. For each specimen, between 50 and 60 spectra were collected. The X-ray spectra were quantified using suitable mineral standards and the data plotted in a standard format showing atomic ratios of Si/Ca vs Al/Ca and Al/Ca vs S/Ca. These atomic ratio plots are used in SEM/EDX studies of cementitious materials and enable the principal hydration products to be differentiated.
2.3
Rietveld X-ray diffraction analysis
Both powders and hydrated cements ground to fine powders after 28 days of hydration in water were analyzed quantitatively using X-ray diffraction analysis (XRD) with Rietveld correction. Five percent corundum (Al 2 O 3 ) relative to the weight of cement was blended with the cement powder to serve as an internal standard thus allowing the calculation of the quantities of the amorphous fraction. This material was chosen because it does not react with water and has no influence on the hydration reaction. X-ray diffraction patterns were first obtained with sufficient resolution for Rietveld analysis. The detector was rotated at 0.017° 2 per 20 s.
2.4
Evaluation of pH of leachate
Diskettes 10 ± 1 mm and a thickness of 1 ± 0.1 mm were prepared of each cement type. After storage in an incubator at 37 ± 1°C for 24 h and removal from the molds, the materials were immersed upright in either 10 ml water or Hanks balanced salt solution. The pH readings of the storage solution were taken using a pH meter (Hanna HI 9811, Hanna Instruments, Woonsocket, RI, USA) prior to immersion and after 28 days.
2.5
Chemical analysis of leachate
The chemical analysis of the cement products released in water and HBSS was performed using inductively coupled plasma atomic absorption spectroscopy (Varian Medical Systems, Palo Alto, CA, USA). The Portland cement and tricalcium silicate cement were mixed in a similar way as the previous experiments producing diskettes 10 mm in diameter and 1 mm high. The specimens were cured for 24 h at 37 °C and 100% humidity after which they were weighed to the accuracy of 0.0001 g and immersed in either 5 ml water or HBSS in closed sterile containers (Labplex, Birmingham, UK). The specimens were removed after 28 days. Containers filled with water and HBSS were used as controls. The leachates were analyzed for aluminum, calcium, silicon, and phosphorus. The amount of leachate was calculated in μg/g using the following formula:
Amount of leachate per weight of cement = amount of leachate per litre × 0.005 × 1000 weight of cement pellet
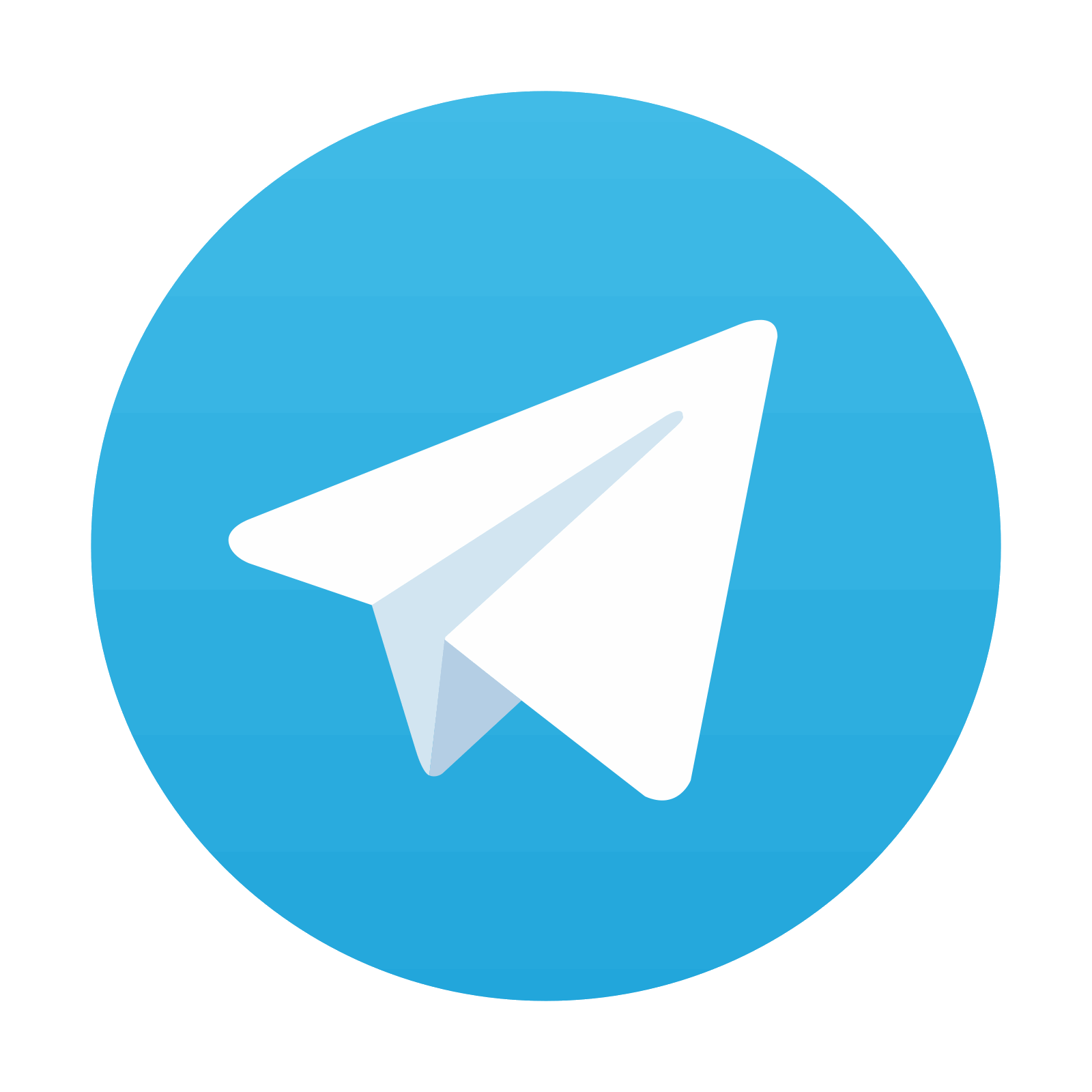
Stay updated, free dental videos. Join our Telegram channel

VIDEdental - Online dental courses
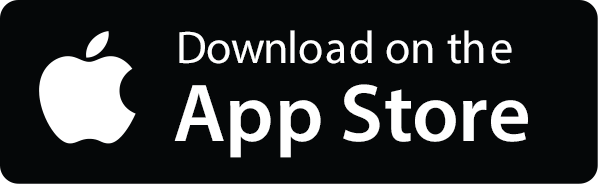
