Abstract
Objectives
To test the accuracy of measurements of tooth wear using a non-contacting laser profilometer (NCLP) and surface matching software.
Methods
The accuracy and repeatability of the NCLP and software in measuring length was assessed by repeatedly scanning a calibrated 25 mm engineering steel gage block. Volumetric measurements were assessed after scanning commercially pure titanium frustums of varying volume. The accuracy and repeatability of the systems in measuring step height and volume after surface matching were assessed using a custom built model with cemented engineering slip gages and cemented onlays of super-plastically formed titanium. The overall effect on the uncertainty of measurement of repeated superimpositions of the same cast, repeated impressions of the same patient and using step-over distances smaller than the laser spot size were also quantified.
Results
The accuracy and repeatability were 1.3 μm and 1.6 μm in measuring length. The system was accurate for volumetric measurement with coefficients of variation <5%. Measurements using the model with cemented engineering slip gages and cemented super-plastically formed titanium onlays varied slightly (23.07 μm and 1.6 mm 3 ). Scanning and superimposing the same model introduced mean error of 2.7 μm (SD = 0.7). Scanning and superimposing separate casts from repeated impressions of a patient introduced mean error of 14.8 μm (SD = 2.8). Decreasing step-over distances reduced measurement error ( p < 0.05).
Significance
The methodologies described here served to assess sources of error in tribology studies using surface mapping and surface matching technologies. The results optimized data interpretation. Study supported by Guy’s and St. Thomas’ Charity and the Royal College of Surgeons of England.
1
Introduction
Surface mapping systems have become an invaluable tool in tribology studies as they allow accurate measurement of samples subjected to wear. In dental research they have been successfully used to measure tooth wear in vitro , in situ , in vivo and have also been used to measure wear of restorations . These systems, also termed profilometers or for simplicity, scanners, record a surface profile as coordinates on the X , Y and Z axes at multiple individual data points from a sample and join them together to form a mesh. Tooth wear can be measured by analyzing and processing the sequential digital files using surface metrology or surface matching software, with reported accuracy in the order of 1–15 μm depending on the system used. The scans can be recorded directly from impressions of teeth scanning casts poured in gypsum or epoxy resin with or without the use of electro-conductive coatings . Direct in vivo measurements are currently not possible but remain the ideal or gold standard. Therefore, inherent errors will be created at each stage when reproducing the tooth shape from an impression to a cast to a digital file. To what extent each step contributes to the overall measurement error remains unquantified.
Once the tooth surface has been scanned, tooth wear is measured using surface metrology software as changes in step heights from an unchanged reference area or using surface matching software which superimposes sequential scans of teeth without the need for artificial reference points . Surface matching software utilizes common areas between sequential scans comparing them to changed areas to measure wear .
Due to the relatively new and increased availability of scanners in dental research, the literature shows there is no consensus on how to assess the accuracy and repeatability of the scanning systems and the surface matching software. Therefore, there is a need to develop evaluation standards applicable to clinical tooth wear measurements where surface matching is required. The aim of this paper was to describe an evaluation protocol to assess the uncertainty of measurement of a system comprising a non-contacting laser profilometer (Xyris 2000TL – Taicaan ® , Southampton, UK) (NCLP) in conjunction with surface matching software (Geomagic ® Qualify 11 – Geomagic ® Incorporated, North Carolina, USA), for measuring simulated tooth wear applicable to in vivo tooth wear measurement studies. This included firstly, the use of dimensional reference standards to evaluate the system, secondly, the manufacture of a standard relevant to a clinical scenario and finally, the quantification of measurement error of superimposition.
2
Materials and methods
2.1
Measurements of length and volume
2.1.1
Length
A Mitutoyo ® steel gage block (Part No: 611635-131, Mitutoyo ® Corporation – Japan, Japanese Industrial Standard number B7506 [1997]) measuring 25 mm × 35 mm × 9 mm was used as a ‘gold standard’. The block was scanned five times on the NCLP using a step-over distance of 50 μm. Each time the standard was removed, replaced and re-scanned in approximately the same position. The NCLP had a 785 nm wavelength laser triangulation sensor with a spot diameter of 30 μm, an axis and sensor resolution of 0.1 μm and an angular tolerance of 89.7°. The scanner recorded the coordinates of multiple individual points and joined them to form a mesh. The scans were analyzed using Geomagic ® Qualify 11 surface metrology software (Geomagic ® Incorporated, North Carolina, USA). Each scan was opened and 20 repeated measurements of the length of the gage block were recorded and their mean compared to those from the gold standard. Finally, to assess the level of ‘noise’ present in the system due to fluctuations in environmental conditions, the block was set below the laser spot on the NCLP (without the table moving) and targeted for 5 s. The range of readings received by the sensor, were recorded to assess the Delta P – T (maximum peak to trough distance). The procedure was carried for 30 s to obtain a standard deviation (SD) of all readings obtained in that time period.
2.1.2
Volume
A volumetric standard was built with four custom made frustums ( Fig. 1 ) of increasing volume with a convergence angle of 75° which were turned on a lathe from a cylinder of commercially pure titanium. The frustums were individually weighed on a set of laboratory scales (Mettler Toledo AT250, Mettler Toledo, Leicester, UK. Resolution = 0.01 mg, accuracy = 0.1 mg, repeatability = 0.3 mg) and the volume for each frustum was calculated using the formula Volume = Mass/Density (density of commercially pure titanium is 4.51 g/cm 3 ); these measurements were called ‘calculated true volume’. The frustums were coated with a 50 nm carbon coating to ensure the same reflectivity before scanning on the NCLP. This was done under conventional protocols for scanning electron microscopy and required two 50 nm coatings to ensure uniformity of the coating. The four frustums were scanned five times on the NCLP using a 50 μm step-over distance, and were removed and replaced in approximately the same position between scans. Each scan was opened in Geomagic ® Qualify 11 and volume was measured above a plane from the top of the base. The measurements using the software were compared to those from the calculated real volume. All testing and storage were performed in a dry environment at 20 °C (±1 °C).
2.2
Measuring changes in step height and volume from teeth
A customized maxillary phantom head teaching model was fabricated having detachable morphology to permit the simulation of dental wear. These comprised (a) engineering slip gages of known height and (b) titanium occlusal onlays and palatal veneers of known volume. When in place, they represented the before wear state and when removed, the after wear state. Firstly, flat inclines were prepared on cuspal inclines of selected teeth of the model (UR3, UR7 and UL3). The model was then reproduced using laboratory silicone (Chaperlin and Jacobs Ltd. Surrey – UK) and was cast in Moonstone ® type IV dental stone (Bracon Ltd. Etchingham, UK) and was also cast in a refractory material (Croform ® , Schottlander, Letchworth, UK). Metal onlays were precision pressed onto the refractory cast by super-plastically forming (SPF) a sheet of Titanium-64 alloy 0.5 mm in thickness onto the occlusal/palatal surfaces of selected teeth (UR5, UR6, UL2 and UL5). The process took approximately two and a half hours under a maximum pressure of 540 psi of argon gas at 900 °C. The resulting pressed sheet was cut into onlays to fit on the occlusal surface of the UR5, UR6, and UL5 and the palatal surface of the UL2 on the Moonstone ® cast. The surfaces of the onlays, except the fitting surface were sandblasted with 25–50 μm silicon oxide to give a matte finish. The onlays were individually weighed on a set of laboratory scales and by using the formula Volume = Mass/Density the volume was calculated (density of Titanium-64 alloy was 4.428 mg/mm 3 ). Finally, sections of engineering slip gages were cut with a guillotine and cemented to the previously created flat inclines on the UR3, UR7 and UL3. The slip gages used were 50 μm, 150 μm, 250 μm and 500 μm. The onlays and slip gages were fitted to the model with cyanoacrylate glue.
Another Moonstone ® cast (without SPF onlays or slip gages) was produced from the same laboratory silicone mold. Both casts, with and without onlays/slip gages were carbon coated using the same protocols as described above. The casts, before carbon coating, are shown in Fig. 2 .
Both casts were scanned on the NCLP using a step-over distance of 50 μm. Scans were superimposed using Geomagic ® Qualify 11 by transforming them into a CAD format, with neighboring 3D data points joined to form a polygon mesh. Differences between scans were obtained by translating the scans into the same coordinate system by using a best fit algorithm which searched for regions of matching and difference between the casts. The software randomly selected 300 data points and continued to align them until it found regions of best fit and the process was repeated using an additional 1000 points until the differences in the Z axis between scans were minimized. The maximum number of iterations to achieve surface matching was pre-set at 1000. The two scans were superimposed and differences between them recorded as changes in step height and volume. Each step height was measured between the top of the cemented slip gage to the surrounding flat area and the volume was calculated by subtracting the volume of teeth with and without the onlays. There were no failed superimpositions. Fig. 3 shows a screen capture of a superimposition of the scan of the cast with onlays against a scan of the cast without onlays; blue indicates wear and thus the position of the onlays and the slip gages; green areas indicates no change (a measurement error of 14.8 μm, see following methodology) and yellow indicates gain of material, due to slight imperfections on the cast with no onlays of frustums.
To quantify the cement space between the onlay and the cast the fitting surface of the onlays and the occlusal/palatal surfaces of the cast were scanned on a Cyclone ® contacting scanner (Renishaw ® PLC, Wotton-under-edge – UK) and superimposed using Geomagic ® Qualify 11 using similar procedures to those described above and using basic geometric formulae previously described by .
2.3
Accuracy of superimposition
Five repeated maxillary impressions from one of the authors (RSA) were taken using Aquasil ® putty and light bodied putty-wash technique. The impressions were disinfected by 10 min immersion in Perform ID (Schülke & Mayr UK Ltd. Sheffield, UK) and left to rest undisturbed for 24 h before being poured in Moonstone ® . In order to assess the repeatability of the superimpositional procedure, one randomly selected cast was scanned five separate times on the NCLP and the resulting scans superimposed and compared measuring root mean square differences in the Z axis. To assess the repeatability of the impression technique, scans were made from each of the five casts, superimposed, and compared measuring root mean differences in the Z axis.
The laser spot moves over a surface and captures images or profiles at defined intervals. The software patches these images together to form a line and eventually the whole surface is replicated digitally. In metrology, oversampling is the process of measuring profiles at a step-over distance (between individual laser spot points) which is less than the diameter of the stylus or diameter of the laser spot. Theoretically, using a step-over distance less than the width of the spot size results in more accurate representation of the surface. The effect of using varying step-over distances in the accuracy of measurement has not been addressed in the literature, so to analyze possible effects of this, the UR2, UR3 and UR4 from one of the casts mentioned above were scanned on the NCLP at varying step-over distances. Each tooth was scanned twice; at 15 μm, 30 μm, 50 μm, 75 μm or 100 μm step-over distances. The resulting scans from each step-over distance were aligned and superimposed using Geomagic ® Qualify 11 using similar protocols as described above. Root mean differences in the Z axis per tooth and per superimposition were then measured.
2.4
Statistical analysis
Coefficients of variation (CoVar = (SD/mean) × 100) were used to assess repeatability of measurements of length and volumetric measurements using the gage block and volumetric standard. Bland and Altman plots were used to assess agreement between calculated true volume and measured volume from the volumetric standard using Geomagic ® Qualify 11. Differences in measurements due to varying step-over distances were assessed using analysis of variance (ANOVA) and post-ANOVA Scheffe tests. Statistical significance was inferred where p < 0.05. Data were not normally distributed so required logarithmic transformations prior to analysis.
2
Materials and methods
2.1
Measurements of length and volume
2.1.1
Length
A Mitutoyo ® steel gage block (Part No: 611635-131, Mitutoyo ® Corporation – Japan, Japanese Industrial Standard number B7506 [1997]) measuring 25 mm × 35 mm × 9 mm was used as a ‘gold standard’. The block was scanned five times on the NCLP using a step-over distance of 50 μm. Each time the standard was removed, replaced and re-scanned in approximately the same position. The NCLP had a 785 nm wavelength laser triangulation sensor with a spot diameter of 30 μm, an axis and sensor resolution of 0.1 μm and an angular tolerance of 89.7°. The scanner recorded the coordinates of multiple individual points and joined them to form a mesh. The scans were analyzed using Geomagic ® Qualify 11 surface metrology software (Geomagic ® Incorporated, North Carolina, USA). Each scan was opened and 20 repeated measurements of the length of the gage block were recorded and their mean compared to those from the gold standard. Finally, to assess the level of ‘noise’ present in the system due to fluctuations in environmental conditions, the block was set below the laser spot on the NCLP (without the table moving) and targeted for 5 s. The range of readings received by the sensor, were recorded to assess the Delta P – T (maximum peak to trough distance). The procedure was carried for 30 s to obtain a standard deviation (SD) of all readings obtained in that time period.
2.1.2
Volume
A volumetric standard was built with four custom made frustums ( Fig. 1 ) of increasing volume with a convergence angle of 75° which were turned on a lathe from a cylinder of commercially pure titanium. The frustums were individually weighed on a set of laboratory scales (Mettler Toledo AT250, Mettler Toledo, Leicester, UK. Resolution = 0.01 mg, accuracy = 0.1 mg, repeatability = 0.3 mg) and the volume for each frustum was calculated using the formula Volume = Mass/Density (density of commercially pure titanium is 4.51 g/cm 3 ); these measurements were called ‘calculated true volume’. The frustums were coated with a 50 nm carbon coating to ensure the same reflectivity before scanning on the NCLP. This was done under conventional protocols for scanning electron microscopy and required two 50 nm coatings to ensure uniformity of the coating. The four frustums were scanned five times on the NCLP using a 50 μm step-over distance, and were removed and replaced in approximately the same position between scans. Each scan was opened in Geomagic ® Qualify 11 and volume was measured above a plane from the top of the base. The measurements using the software were compared to those from the calculated real volume. All testing and storage were performed in a dry environment at 20 °C (±1 °C).
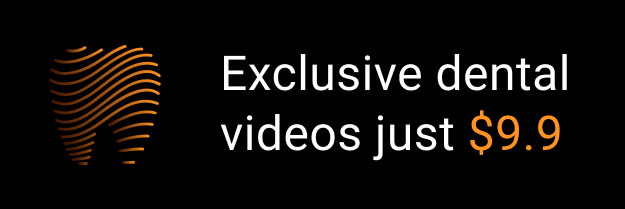