Abstract
Objective
To investigate the effect of the substrate: coating elastic modulus ratio on the failure behaviour of glass ionomer cement (GIC) under Hertzian indentation.
Methods
GIC (Amalgomer CR, Advanced Healthcare, Tonbridge, Kent, UK) discs, 2 mm thick and 10 mm diameter, were randomly divided into 11 groups, 10–22 specimens for each group, and stored at 37 °C in artificial saliva for 7 days. Discs were tested resting freely on 11 substrate materials at 23 °C in air by loading centrally through a 20 mm diameter hard steel ball at a crosshead speed of 0.2 mm/min. The elastic moduli of the substrates ( E s ) and the coating GIC ( E c ) were first measured with a method similar to that of the Hertzian indentation, except for the three harder materials: amalgam, Al6061 and stainless steel 304. The failure load at the first crack was recorded with the aid of acoustic emission detection. Fracture surfaces were observed by SEM.
Results
E s values ranged from 0.09 to 210 GPa; E c was 7.7 GPa. Failure load generally increased with E s at first and then became relatively stable; the turning point occurred for E s / E c = 1. Bottom surface-initiated radial cracking was the principal failure mode on softer substrates ( E s / E c < 1), while top surface conical cracking usually occurred on harder substrates ( E s / E c ≥ 1).
Conclusion
The elastic modulus ratio, substrate: coating, is a controlling factor for both the failure mode and load for the coating material under Hertzian indentation.
1
Introduction
Many functional systems in dentistry are effectively laminated structures, for example, the hard tissue of natural tooth consists of enamel (or cementum in the root) and dentin. Similarly, dental restorations are usually constructed with several layers of material on top of the dentin: liner, base and the outer restorative material, while ceramic crowns may be made up of outer veneer and inner core ceramics or metals. In such systems, the various properties of each layer are intended to allow the whole structure to function better than their constituent components would on their own. However, the differences in the mechanical properties of each material also affect the failure behaviour of the laminated structure because elastic modulus mismatch between the layer components can produce new stresses at, and either side of, the interface , most obviously because of the bending which occurs on a softer substrate . The failure mode of such laminated structures as hard ceramics or glasses on soft substrates under Hertzian indentation have been demonstrated extensively by Lawn, his collaborators and other researchers . It has, for example, been shown that the failure mode of a veneering ceramic is greatly affected by the substrate, a higher elastic modulus improving the load-bearing capacity of the coating. However, the types of substrate materials chosen in these studies were not very diverse so that the overall failure behaviour of the coating material was not demonstrated. In addition, all studies of this behaviour have been ceramic-related; no other dental restorative materials being considered. At present, most of the substrate materials used for mimicking dental laminated structures have been arbitrary: some with resin, some with metal, and some with dentin . This might cause difficulty in the explanation of results.
Accordingly, the purpose of this study was to investigate the effect of the elastic modulus ( E ) ratio of substrate: coating on the failure load and failure mode of a commonly used brittle dental restorative material, glass ionomer cement (GIC), under Hertzian indentation, to obtain a general pattern for the behaviour variation under change of substrate elastic modulus.
2
Materials and methods
Glass ionomer cement (GIC) (Amalgomer CR, Batch No. 302007; Advanced Healthcare, Tonbridge, Kent, UK) discs of 2.0 mm thickness and 10.0 mm diameter were prepared in poly(tetrafluoroethylene) (PTFE) moulds at 23 ± 1 °C, 50 ± 10% relative humidity. The GIC was hand-mixed strictly according to the manufacturers’ instructions: 1 scoop powder: 1 drop of water, mixed for 2 min. Excess mixed paste was packed into the mould on a glass slab, avoiding bubbles, covered with a polyethylene separating sheet (Dentsply, Dentsply Detrey, Konstanz, Germany) and placed under a 5 kg load in a levelling press (Leitz, Wetzlar, Germany) for 5 min to make the surface level After complete setting (7 min, according to the manufacturer’s instruction), the GIC disc was demoulded and stored at 37 ± 1 °C in artificial saliva (AS) at pH ∼6 (formula of Leung and Darvell, without CO 2 ) for 7 days to avoid dehydration. Both sides were ground flat on a pregrinder (Lunn-Major, Struers, Copenhagen, Denmark) to 1200 grit under running water on day 2 and returned to AS storage. The thickness was controlled by a vernier caliper (1143 M, Moore & Wright, Sheffield, England) to within 0.02 mm of the target value (2.00 mm). Eleven types of material with various values of elastic modulus were used as substrate ( Table 1 ). Most substrate materials were prefabricated. Rod- or sheet-form materials were cut into discs of appropriate size, both the upper and bottom surfaces were ground to 1200 grit. For bovine cortical bone and glass, because of the difficulty of processing, a larger-sized rectangle was adopted to ensure that the coating discs were fully supported. Three types of substrate were custom-made in the laboratory with moulds of 10 mm diameter and 5 mm thickness: silicone rubber, GIC ( i.e. the same as the coating material), and dental silver amalgam. The silicone rubber was prepared and stored at 23 ± 1 °C, 50 ± 10% relative humidity, in air, 30 min before testing. Equal amounts of the two components were hand-mixed to uniform colour before filling the mould and levelling with a glass plate. After setting (7 min after mixing), the material was removed from the mould and stored (as above) 30 min before use. The preparation and storage of GIC substrate discs were as above. Dental amalgam (pre-dosed capsules) were machine-mixed for 6 s (Silamat, Vivadent, Amherst, NY, USA) according to the manufacture’s instruction, hand-packed and condensed into a mould on a glass slab. The upper surface was covered with a polyethylene separating sheet (Dentsply) and levelled under 5 kg load in a levelling press (Leitz). After setting (10 min after mixing), the substrates were demoulded and stored 7 days prior to use. All preparation and storage for the amalgam was at 23 ± 1 °C, 50 ± 10% RH, in air. Between 10 and 22 coating and substrate specimens were prepared for each test group.
Material | Manufacturer | Batch no. | Size (mm) |
---|---|---|---|
Coating | |||
Ceramic-reinforced glass ionomer (GIC) | Amalgomer, Advance Healthcare, UK | 302007 | t : 2 r : 5 |
Substrate | |||
Addition-cured silicone rubber (SR) | Elite HD+ putty, Zhermack, Italy | 34648 | t : 5 r : 5 |
Polyacrylonitril-butadiene-styrene (ABS) | Goodfellow Cambridge, England | AB 307910/1 | t : 5 r : 5 |
Polycarbonate (PC) | t : 4.3 r : 5 |
||
20% glass fibre-reinforced polycarbonate (RPC) | Goodfellow Cambridge, England | CT 327920 | t : 5 r 10 |
30% glass fibre-reinforced polyamide-nylon (RPN) | Goodfellow Cambridge, England | AM 367910/2 | t : 5 r : 5 |
Bovine cortical bone (BCB) | t : 5 l : 12 w : 10 |
||
Ceramic-reinforced glass ionomer (GIC) | Amalgomer, Advance Healthcare, UK | 302007 | t: 5 r : 5 |
Window glass | – | t : 5.8 l : 18 w : 15 |
|
Dental silver amalgam (pre-dosed capsules) | Logic+, SDI, Australia | 30826202 | t : 5 r : 5 |
Aluminium alloy, Al 6061 | – | t : 5 r : 5 |
|
Stainless steel 304 | – | t : 5 r : 5 |
The main experimental setup is illustrated in Fig. 1 . Test conditions and the general test method were similar to those described before . “Coating” GIC discs were tested resting freely on a substrate piece, with the load applied through a hard steel bearing ball of 20 mm diameter. To detect the acoustic energy (AE) signals released from the cracking of the GIC, two aluminium probes with piezoelectric sensors (15 mm × 1.5 mm × 0.6 mm) (BM15015–06HC, Quantelec, Witney, UK) bonded on the front part, were set to rest lightly on the top surface of the specimen on opposite sides. AE signals were recorded using a digital oscilloscope (COM7101, Kikusui Electronics, Kawasaki, Japan), with 0.5 ms timebase and 5 mV/division scale. The load on the ball was applied through a universal testing machine (UTM) (1185, Instron, High Wycombe, England) at a crosshead speed of 0.1 mm/min until either a sudden drop appeared in the load chart or a burst of AE signal was observed on the oscilloscope. The load at the first crack was recorded. For a few uncertain specimens, graphite powder was lightly smeared on the surfaces of the specimens to increase the visual contrast and facilitate confirmation of cracks after unloading to confirm the validity of the recorded value. Scanning electronic microscope (SEM) (XL30CP, Philips Electron Optics, Eindhoven, Netherlands) observations were made to identify the failure mode, if necessary. Some 3–5 specimens of each group were gold-sputtered in a vacuum evaporator (JFC-1100, JEOL, Tokyo, Japan) and examined on top, bottom and fracture surfaces at 10–80× magnification.
To determine the elastic modulus of both the GIC coating ( E c ) and the softer substrate materials ( E s ), measurement was by using the UTM under similar loading conditions as they were in the Hertzian indentation test itself. A stainless steel disc, 25 mm diameter and 5 mm thickness, was put on top of the substrate material to spread the load evenly, with the pair aligned on the load axis with the aid of a centralization jig. Load was applied through a 20 mm diameter ball as above. For the soft silicone rubber impression material, a mould was put around the specimen to limit its lateral expansion during loading as in the actual test of the coating. Test conditions were crosshead speed: 0.1 mm/min; chart speed: 100 mm/min; load cell: 5 kN full scale load range at 10–100% of full scale according to the stiffness of the material. Test loading was repeated: the first time as a preparation for the second, load was applied to the maximum scale in order to ensure a good contact between the surfaces by causing the collapse of any asperities; on the second loading, the load–strain response was closer to linear and this load–deflection curve was used for calculation.
The recorded deflection comprised two components: one for the test substrate and the other due to the compliance of the test system, primarily the load string. The overall deflection rate of the system was determined from the slope of the load–deflection curve up to 5 kN on a tool steel disc, through a flat anvil of the same material, at 0.1 mm/min crosshead speed and 20 mm/min chart speed, to be 0.040 μm/N. This value was used as a correction constant ( k ) for the calculation of E using:
E = t s A Δ y Δ P − k − 1
where Δ y /Δ P is slope of the steepest linear part of the load–deflection curve, t s is the thickness of the substrate, and A the effective area under compression. The mean of five values was taken as the working value for each material. For the stiffer materials (amalgam, aluminium 6061, stainless steel 304), this method was inapplicable as the machine deflection dominated; literature values were therefore used.
Some 1/3 to 1/2 of the specimens of each group were randomly chosen for SEM observation.
2
Materials and methods
Glass ionomer cement (GIC) (Amalgomer CR, Batch No. 302007; Advanced Healthcare, Tonbridge, Kent, UK) discs of 2.0 mm thickness and 10.0 mm diameter were prepared in poly(tetrafluoroethylene) (PTFE) moulds at 23 ± 1 °C, 50 ± 10% relative humidity. The GIC was hand-mixed strictly according to the manufacturers’ instructions: 1 scoop powder: 1 drop of water, mixed for 2 min. Excess mixed paste was packed into the mould on a glass slab, avoiding bubbles, covered with a polyethylene separating sheet (Dentsply, Dentsply Detrey, Konstanz, Germany) and placed under a 5 kg load in a levelling press (Leitz, Wetzlar, Germany) for 5 min to make the surface level After complete setting (7 min, according to the manufacturer’s instruction), the GIC disc was demoulded and stored at 37 ± 1 °C in artificial saliva (AS) at pH ∼6 (formula of Leung and Darvell, without CO 2 ) for 7 days to avoid dehydration. Both sides were ground flat on a pregrinder (Lunn-Major, Struers, Copenhagen, Denmark) to 1200 grit under running water on day 2 and returned to AS storage. The thickness was controlled by a vernier caliper (1143 M, Moore & Wright, Sheffield, England) to within 0.02 mm of the target value (2.00 mm). Eleven types of material with various values of elastic modulus were used as substrate ( Table 1 ). Most substrate materials were prefabricated. Rod- or sheet-form materials were cut into discs of appropriate size, both the upper and bottom surfaces were ground to 1200 grit. For bovine cortical bone and glass, because of the difficulty of processing, a larger-sized rectangle was adopted to ensure that the coating discs were fully supported. Three types of substrate were custom-made in the laboratory with moulds of 10 mm diameter and 5 mm thickness: silicone rubber, GIC ( i.e. the same as the coating material), and dental silver amalgam. The silicone rubber was prepared and stored at 23 ± 1 °C, 50 ± 10% relative humidity, in air, 30 min before testing. Equal amounts of the two components were hand-mixed to uniform colour before filling the mould and levelling with a glass plate. After setting (7 min after mixing), the material was removed from the mould and stored (as above) 30 min before use. The preparation and storage of GIC substrate discs were as above. Dental amalgam (pre-dosed capsules) were machine-mixed for 6 s (Silamat, Vivadent, Amherst, NY, USA) according to the manufacture’s instruction, hand-packed and condensed into a mould on a glass slab. The upper surface was covered with a polyethylene separating sheet (Dentsply) and levelled under 5 kg load in a levelling press (Leitz). After setting (10 min after mixing), the substrates were demoulded and stored 7 days prior to use. All preparation and storage for the amalgam was at 23 ± 1 °C, 50 ± 10% RH, in air. Between 10 and 22 coating and substrate specimens were prepared for each test group.
Material | Manufacturer | Batch no. | Size (mm) |
---|---|---|---|
Coating | |||
Ceramic-reinforced glass ionomer (GIC) | Amalgomer, Advance Healthcare, UK | 302007 | t : 2 r : 5 |
Substrate | |||
Addition-cured silicone rubber (SR) | Elite HD+ putty, Zhermack, Italy | 34648 | t : 5 r : 5 |
Polyacrylonitril-butadiene-styrene (ABS) | Goodfellow Cambridge, England | AB 307910/1 | t : 5 r : 5 |
Polycarbonate (PC) | t : 4.3 r : 5 |
||
20% glass fibre-reinforced polycarbonate (RPC) | Goodfellow Cambridge, England | CT 327920 | t : 5 r 10 |
30% glass fibre-reinforced polyamide-nylon (RPN) | Goodfellow Cambridge, England | AM 367910/2 | t : 5 r : 5 |
Bovine cortical bone (BCB) | t : 5 l : 12 w : 10 |
||
Ceramic-reinforced glass ionomer (GIC) | Amalgomer, Advance Healthcare, UK | 302007 | t: 5 r : 5 |
Window glass | – | t : 5.8 l : 18 w : 15 |
|
Dental silver amalgam (pre-dosed capsules) | Logic+, SDI, Australia | 30826202 | t : 5 r : 5 |
Aluminium alloy, Al 6061 | – | t : 5 r : 5 |
|
Stainless steel 304 | – | t : 5 r : 5 |
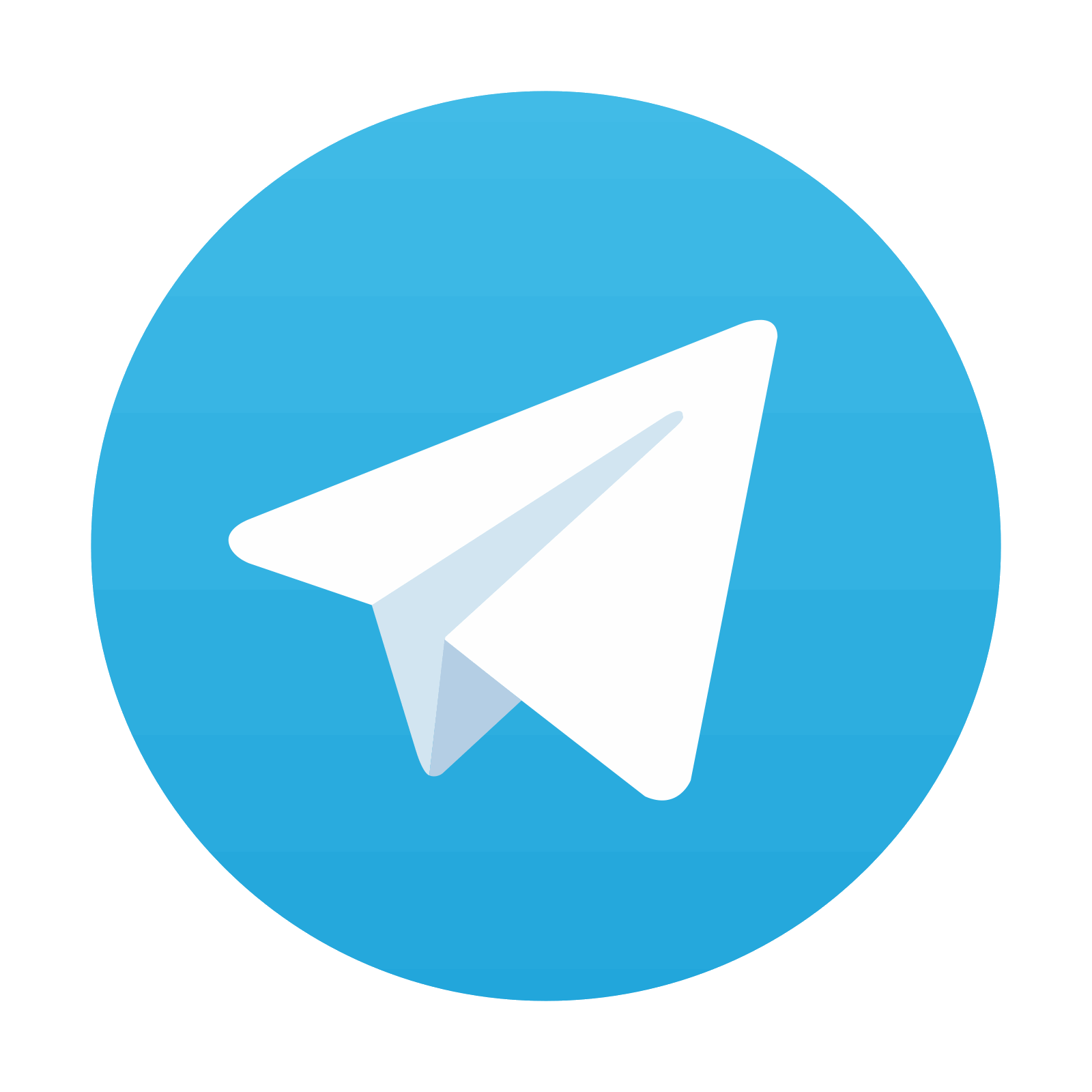
Stay updated, free dental videos. Join our Telegram channel

VIDEdental - Online dental courses
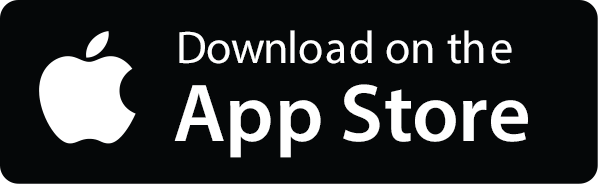

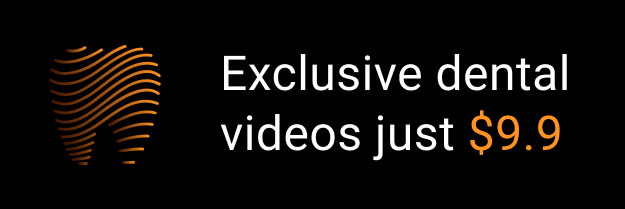